Paul Birch
Chief Operating Officer at MVP Group International, Inc- Claim this Profile
Click to upgrade to our gold package
for the full feature experience.
Topline Score
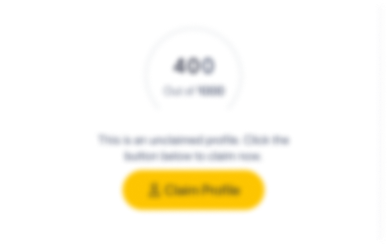
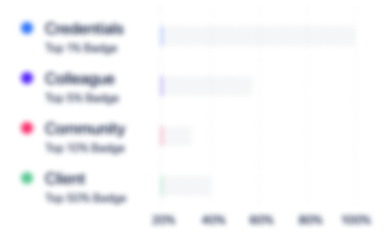
Bio

Lindsey Padilla
Paul was an excellent boss and mentor for me at PartyLite. His open door policy and overall support of my position and projects were vital to the success of all the projects that were run through R, D & E. Even with working in separate facilities in different time zones, Paul always made time to understand and work through projects and issues with me. His support was the main driving force for numerous cost savings and innovation initiatives in the company. Paul has a ‘do things the right way’ attitude that was greatly appreciated among the team members. I personally am grateful for having had the opportunity to work with Paul and I can accredit many of my professional lessons learned to working with him.

Anne Butler
Paul is a smart, hardworking supply chain professional who loves to take on a challenge, and will stretch himself and his team to meet company goals. When PartyLite purchased a proprietary manufacturing process from another company, Paul led the effort to improve the process to convert it from a boutique process to mass production, with added quality controls and lower costs, all while meeting the required timing for launch. Paul can be counted on to focus on the important things, and get them done.

Lindsey Padilla
Paul was an excellent boss and mentor for me at PartyLite. His open door policy and overall support of my position and projects were vital to the success of all the projects that were run through R, D & E. Even with working in separate facilities in different time zones, Paul always made time to understand and work through projects and issues with me. His support was the main driving force for numerous cost savings and innovation initiatives in the company. Paul has a ‘do things the right way’ attitude that was greatly appreciated among the team members. I personally am grateful for having had the opportunity to work with Paul and I can accredit many of my professional lessons learned to working with him.

Anne Butler
Paul is a smart, hardworking supply chain professional who loves to take on a challenge, and will stretch himself and his team to meet company goals. When PartyLite purchased a proprietary manufacturing process from another company, Paul led the effort to improve the process to convert it from a boutique process to mass production, with added quality controls and lower costs, all while meeting the required timing for launch. Paul can be counted on to focus on the important things, and get them done.

Lindsey Padilla
Paul was an excellent boss and mentor for me at PartyLite. His open door policy and overall support of my position and projects were vital to the success of all the projects that were run through R, D & E. Even with working in separate facilities in different time zones, Paul always made time to understand and work through projects and issues with me. His support was the main driving force for numerous cost savings and innovation initiatives in the company. Paul has a ‘do things the right way’ attitude that was greatly appreciated among the team members. I personally am grateful for having had the opportunity to work with Paul and I can accredit many of my professional lessons learned to working with him.

Anne Butler
Paul is a smart, hardworking supply chain professional who loves to take on a challenge, and will stretch himself and his team to meet company goals. When PartyLite purchased a proprietary manufacturing process from another company, Paul led the effort to improve the process to convert it from a boutique process to mass production, with added quality controls and lower costs, all while meeting the required timing for launch. Paul can be counted on to focus on the important things, and get them done.

Lindsey Padilla
Paul was an excellent boss and mentor for me at PartyLite. His open door policy and overall support of my position and projects were vital to the success of all the projects that were run through R, D & E. Even with working in separate facilities in different time zones, Paul always made time to understand and work through projects and issues with me. His support was the main driving force for numerous cost savings and innovation initiatives in the company. Paul has a ‘do things the right way’ attitude that was greatly appreciated among the team members. I personally am grateful for having had the opportunity to work with Paul and I can accredit many of my professional lessons learned to working with him.

Anne Butler
Paul is a smart, hardworking supply chain professional who loves to take on a challenge, and will stretch himself and his team to meet company goals. When PartyLite purchased a proprietary manufacturing process from another company, Paul led the effort to improve the process to convert it from a boutique process to mass production, with added quality controls and lower costs, all while meeting the required timing for launch. Paul can be counted on to focus on the important things, and get them done.

Experience
-
MVP Group International, Inc
-
United States
-
Manufacturing
-
1 - 100 Employee
-
Chief Operating Officer
-
Mar 2019 - Present
Responsible for all MVP Operations, overseeing all manufacturing, distribution, sourcing, demand planning and logistics. Providing operational support to other division's international facilities in Asia. Brought on in 2019 to help restructure the business and restore profitability. In 2020 the team tripled gross margin through significant business rationalization and process changes. Currently focused on developing plans for future acquisitions and integrations. Responsible for all MVP Operations, overseeing all manufacturing, distribution, sourcing, demand planning and logistics. Providing operational support to other division's international facilities in Asia. Brought on in 2019 to help restructure the business and restore profitability. In 2020 the team tripled gross margin through significant business rationalization and process changes. Currently focused on developing plans for future acquisitions and integrations.
-
-
-
PartyLite (A Division of Blyth)
-
Plymouth, Massachusetts
-
Vice President, North American Operations
-
2010 - 2014
Responsible for manufacturing, distribution, demand planning and continuous improvement activities for PartyLite. Actively pursuing Supply Chain integration and transparency improvement projects to promote a more responsive and effective supply chain for PartyLite's markets and customers. Demonstrated strong operational, leadership, financial management, execution and change management skills. • Developed and implemented Cost of Supply Chain Inefficiency measure. The metric led the… Show more Responsible for manufacturing, distribution, demand planning and continuous improvement activities for PartyLite. Actively pursuing Supply Chain integration and transparency improvement projects to promote a more responsive and effective supply chain for PartyLite's markets and customers. Demonstrated strong operational, leadership, financial management, execution and change management skills. • Developed and implemented Cost of Supply Chain Inefficiency measure. The metric led the Ops team to execute projects reducing costs by more than $8mm from 2012-2013. • Reduced customer complaint rate by 33% through focused pick accuracy projects and package and product design development activities saving in excess of $1.5mm/year. • Redesigned NA Distribution cubing, cartonization and dunnage system saving $700k+/year. • Focused NA manufacturing execution reducing manufactured product back order rate by 66%, improved customer order fill rate by over 6% saves in excess of $700k/year. • Supported the North American market by changing shipping mode to individual orders from aggregate orders improving time to customer by five days. • Integrated North American Operations, relocating Distribution into the Manufacturing facility. Project saved in excess of $4.6mm/year while supporting improved service and execution. • Selected and implemented Logility Voyager demand planning and inventory management system. Leveraging system has increased service levels while more than doubling inventory turns, and dropped E&O product and expediting costs by more than 50%. • Introduced forecast consensus (alignment) meeting with the markets, improved timing and accuracy of catalog pre-sale, promotional planning and “normal forecast" to improve product availability. • Initiated and championed multi-site Lean/Continuous improvement program – focused on training, project management and lean tools. Qualified 33 project managers and eight Green belts across five sites. Show less Responsible for manufacturing, distribution, demand planning and continuous improvement activities for PartyLite. Actively pursuing Supply Chain integration and transparency improvement projects to promote a more responsive and effective supply chain for PartyLite's markets and customers. Demonstrated strong operational, leadership, financial management, execution and change management skills. • Developed and implemented Cost of Supply Chain Inefficiency measure. The metric led the… Show more Responsible for manufacturing, distribution, demand planning and continuous improvement activities for PartyLite. Actively pursuing Supply Chain integration and transparency improvement projects to promote a more responsive and effective supply chain for PartyLite's markets and customers. Demonstrated strong operational, leadership, financial management, execution and change management skills. • Developed and implemented Cost of Supply Chain Inefficiency measure. The metric led the Ops team to execute projects reducing costs by more than $8mm from 2012-2013. • Reduced customer complaint rate by 33% through focused pick accuracy projects and package and product design development activities saving in excess of $1.5mm/year. • Redesigned NA Distribution cubing, cartonization and dunnage system saving $700k+/year. • Focused NA manufacturing execution reducing manufactured product back order rate by 66%, improved customer order fill rate by over 6% saves in excess of $700k/year. • Supported the North American market by changing shipping mode to individual orders from aggregate orders improving time to customer by five days. • Integrated North American Operations, relocating Distribution into the Manufacturing facility. Project saved in excess of $4.6mm/year while supporting improved service and execution. • Selected and implemented Logility Voyager demand planning and inventory management system. Leveraging system has increased service levels while more than doubling inventory turns, and dropped E&O product and expediting costs by more than 50%. • Introduced forecast consensus (alignment) meeting with the markets, improved timing and accuracy of catalog pre-sale, promotional planning and “normal forecast" to improve product availability. • Initiated and championed multi-site Lean/Continuous improvement program – focused on training, project management and lean tools. Qualified 33 project managers and eight Green belts across five sites. Show less
-
-
-
PartyLite
-
United States
-
Manufacturing
-
700 & Above Employee
-
Vice President of Manufacturing and R&D
-
Jun 2005 - Dec 2009
Responsible for two Manufacturing facilities, Batavia, IL and Cumbria, UK supporting sales in excess of $250 million. Factories design, develop and commercialize candles and other home fragrance products. R&D Group in Batavia develops Candle and Air Care products and innovations. • Supported tight cost management, reducing North American overhead by 30% over three years, holding European overhead flat while increasing throughput by 33% • Developed and coordinated cost and strategic… Show more Responsible for two Manufacturing facilities, Batavia, IL and Cumbria, UK supporting sales in excess of $250 million. Factories design, develop and commercialize candles and other home fragrance products. R&D Group in Batavia develops Candle and Air Care products and innovations. • Supported tight cost management, reducing North American overhead by 30% over three years, holding European overhead flat while increasing throughput by 33% • Developed and coordinated cost and strategic business models that supported balancing production at both facilities to manage volume and profitability. Process helped improve European profitability by $2mm per year. • Led Research, Development and Engineering activity – worked with marketing to implement streamlined process focused on product performance specifications. Commercialized in excess of 400 new products per year. Averaging 20 fragrances and 12 product families/concepts per year. • Implemented safety and housekeeping programs that reduced workers compensation costs by 90% over the course of three years and established culture that allowed plant to go 1.5mm hours without lost time from 2008-2011. • Championed first ever Corporate wide safety conference in 2008. • Coordinated multi-site continuous improvement plan at the facilities regularly delivering in excess of 5% improvements per year. • Implemented Microsoft Dynamics AX ERP system for both manufacturing sites (2006-2007.) Cut ERP support costs for the facilities by 65% and set foundation for corporate system. • Developed plan and implemented liquid filling operations at the US factory starting up $30mm sales product line on time and under budget. • Implemented alternate fuels program (2005) that supported continuity of operations through hurricane Rita aftermath when key raw material refineries were shut down for six months. Show less Responsible for two Manufacturing facilities, Batavia, IL and Cumbria, UK supporting sales in excess of $250 million. Factories design, develop and commercialize candles and other home fragrance products. R&D Group in Batavia develops Candle and Air Care products and innovations. • Supported tight cost management, reducing North American overhead by 30% over three years, holding European overhead flat while increasing throughput by 33% • Developed and coordinated cost and strategic… Show more Responsible for two Manufacturing facilities, Batavia, IL and Cumbria, UK supporting sales in excess of $250 million. Factories design, develop and commercialize candles and other home fragrance products. R&D Group in Batavia develops Candle and Air Care products and innovations. • Supported tight cost management, reducing North American overhead by 30% over three years, holding European overhead flat while increasing throughput by 33% • Developed and coordinated cost and strategic business models that supported balancing production at both facilities to manage volume and profitability. Process helped improve European profitability by $2mm per year. • Led Research, Development and Engineering activity – worked with marketing to implement streamlined process focused on product performance specifications. Commercialized in excess of 400 new products per year. Averaging 20 fragrances and 12 product families/concepts per year. • Implemented safety and housekeeping programs that reduced workers compensation costs by 90% over the course of three years and established culture that allowed plant to go 1.5mm hours without lost time from 2008-2011. • Championed first ever Corporate wide safety conference in 2008. • Coordinated multi-site continuous improvement plan at the facilities regularly delivering in excess of 5% improvements per year. • Implemented Microsoft Dynamics AX ERP system for both manufacturing sites (2006-2007.) Cut ERP support costs for the facilities by 65% and set foundation for corporate system. • Developed plan and implemented liquid filling operations at the US factory starting up $30mm sales product line on time and under budget. • Implemented alternate fuels program (2005) that supported continuity of operations through hurricane Rita aftermath when key raw material refineries were shut down for six months. Show less
-
-
-
Blyth Inc.
-
United States
-
Consumer Goods
-
1 - 100 Employee
-
Director of Manufacturing, Blyth Homescents Intl
-
Jan 1999 - Jun 2005
Significantly improved safety, quality, service, cost, production floor leadership and cross functional communication at company’s largest candle facility while upgrading the facility. The factory served a wide variety of wholesale customers and markets, including Colonial and Carolina Designs Brands and WalMart private label. Facility supported four divisions and 17 brands and sales in excess of $100 million. • Safety - reportable and lost time accident rates reduced 56% & 80%… Show more Significantly improved safety, quality, service, cost, production floor leadership and cross functional communication at company’s largest candle facility while upgrading the facility. The factory served a wide variety of wholesale customers and markets, including Colonial and Carolina Designs Brands and WalMart private label. Facility supported four divisions and 17 brands and sales in excess of $100 million. • Safety - reportable and lost time accident rates reduced 56% & 80% respectively (1999 to 2001.) • Quality - strengthened product development process by formalizing development testing and pre-production processes. Implemented in-process quality checks and manufacturing process checklists. Improved site level of knowledge of candle chemistry and packaging development. • Service - improved production planning and inventory control functions. Supported production of over 3700 sku’s a year. Reduced manufacturing lot sizes by 75% from 1999-2002. Improved on time delivery service to over 40 key mass channel retailers with diverse requirements. • Cost - restructured and streamlined operation, reducing overhead from $22.4 million in 1999 budget to $12.7 million in 2002. Met 2002 expense budget while running 111% of budgeted production. Reduced premium channel inventory by 45% while maintaining fill rates above 98%. • Production floor leadership - implemented supervisory training for front line supervisors. Cross-trained key supervisors and managers. Shifted culture from “the boss says” to effective decision making at hourly supervisory level. • Cross functional communication - strengthened relationships with other corporate functions and sites. • Facility upgrade - led mass markets areas during ~$20MM capacity expansion, including installation of nine production lines that generated 43% of 2002 production volume. (Capital work 1999-2001) Show less Significantly improved safety, quality, service, cost, production floor leadership and cross functional communication at company’s largest candle facility while upgrading the facility. The factory served a wide variety of wholesale customers and markets, including Colonial and Carolina Designs Brands and WalMart private label. Facility supported four divisions and 17 brands and sales in excess of $100 million. • Safety - reportable and lost time accident rates reduced 56% & 80%… Show more Significantly improved safety, quality, service, cost, production floor leadership and cross functional communication at company’s largest candle facility while upgrading the facility. The factory served a wide variety of wholesale customers and markets, including Colonial and Carolina Designs Brands and WalMart private label. Facility supported four divisions and 17 brands and sales in excess of $100 million. • Safety - reportable and lost time accident rates reduced 56% & 80% respectively (1999 to 2001.) • Quality - strengthened product development process by formalizing development testing and pre-production processes. Implemented in-process quality checks and manufacturing process checklists. Improved site level of knowledge of candle chemistry and packaging development. • Service - improved production planning and inventory control functions. Supported production of over 3700 sku’s a year. Reduced manufacturing lot sizes by 75% from 1999-2002. Improved on time delivery service to over 40 key mass channel retailers with diverse requirements. • Cost - restructured and streamlined operation, reducing overhead from $22.4 million in 1999 budget to $12.7 million in 2002. Met 2002 expense budget while running 111% of budgeted production. Reduced premium channel inventory by 45% while maintaining fill rates above 98%. • Production floor leadership - implemented supervisory training for front line supervisors. Cross-trained key supervisors and managers. Shifted culture from “the boss says” to effective decision making at hourly supervisory level. • Cross functional communication - strengthened relationships with other corporate functions and sites. • Facility upgrade - led mass markets areas during ~$20MM capacity expansion, including installation of nine production lines that generated 43% of 2002 production volume. (Capital work 1999-2001) Show less
-
-
-
Ecolab
-
United States
-
Chemical Manufacturing
-
700 & Above Employee
-
Plant Manager Ecolab Engineering Center
-
Sep 1993 - Mar 1998
Process Engineer promoted to Plant Manager for the Engineering Center. Activities included product design, development and scale up, initial production, launch support and technology transfer of new products from the R&D center to the regional manufacturing sites. • Managed all aspects of development and production operations, $7 million expense budget, annual budgeting process, capital project management and production of 6000 batches generating in excess of $70 million in sales. •… Show more Process Engineer promoted to Plant Manager for the Engineering Center. Activities included product design, development and scale up, initial production, launch support and technology transfer of new products from the R&D center to the regional manufacturing sites. • Managed all aspects of development and production operations, $7 million expense budget, annual budgeting process, capital project management and production of 6000 batches generating in excess of $70 million in sales. • Staffed two additional production lines and shifts and completed training to support line construction, process scale-up and initial launch of Ecolab’s most significant product line introduction in the last 15 years. • Integrated test kit production operations into Eagan location, including 225 manufactured items and 800 raw materials. Generated $200,000 annual cost savings from a $1 million operation. • Personally led in excess of 100 plant tours for customers and in-house training sessions. Customer tour responsibility included all levels of clients from $40 million corporate accounts to regional dairy/restaurant cooperatives. Closure rate on toured customers exceeded 90 percent. • Functioned as site safety and emergency response director. Team director for eight incidents over three years. Wausau rated facility safety and housekeeping programs as the best in corporation from ’95-’98. • Developed ISO-9002 production plant certification program. • Reduced out-of -specification (non-conforming) product by over 90% from ’95-’97. • Supervised application developer/LAN manager while acting as site IT manager. Directed site network, software and anti-virus strategies. Wrote 1998 capital projects for server, cabling and OS replacement. • Was member of Ecolab’s IT Steering Committee, a four-member committee determining and directing information systems priorities for the R,D&E community. Show less Process Engineer promoted to Plant Manager for the Engineering Center. Activities included product design, development and scale up, initial production, launch support and technology transfer of new products from the R&D center to the regional manufacturing sites. • Managed all aspects of development and production operations, $7 million expense budget, annual budgeting process, capital project management and production of 6000 batches generating in excess of $70 million in sales. •… Show more Process Engineer promoted to Plant Manager for the Engineering Center. Activities included product design, development and scale up, initial production, launch support and technology transfer of new products from the R&D center to the regional manufacturing sites. • Managed all aspects of development and production operations, $7 million expense budget, annual budgeting process, capital project management and production of 6000 batches generating in excess of $70 million in sales. • Staffed two additional production lines and shifts and completed training to support line construction, process scale-up and initial launch of Ecolab’s most significant product line introduction in the last 15 years. • Integrated test kit production operations into Eagan location, including 225 manufactured items and 800 raw materials. Generated $200,000 annual cost savings from a $1 million operation. • Personally led in excess of 100 plant tours for customers and in-house training sessions. Customer tour responsibility included all levels of clients from $40 million corporate accounts to regional dairy/restaurant cooperatives. Closure rate on toured customers exceeded 90 percent. • Functioned as site safety and emergency response director. Team director for eight incidents over three years. Wausau rated facility safety and housekeeping programs as the best in corporation from ’95-’98. • Developed ISO-9002 production plant certification program. • Reduced out-of -specification (non-conforming) product by over 90% from ’95-’97. • Supervised application developer/LAN manager while acting as site IT manager. Directed site network, software and anti-virus strategies. Wrote 1998 capital projects for server, cabling and OS replacement. • Was member of Ecolab’s IT Steering Committee, a four-member committee determining and directing information systems priorities for the R,D&E community. Show less
-
-
-
US Navy
-
United States
-
Armed Forces
-
700 & Above Employee
-
Lieutentant
-
Apr 1988 - Aug 1993
Served in the Naval Nuclear Power Program aboard USS Trepang (SSN-674) with deployments on the USS Grant (SSBN-631) and the USS Seahorse (SSN-669.) Reactor Controls Assistant, Main Propulsion Assistant and Assistant Engineer. • Diverse experience managing engineering divisions while operating and maintaining naval nuclear power plants. Completed 22-month major refueling overhaul. Directed portions of core replacement, initial core testing and criticality. As Assistant Engineer… Show more Served in the Naval Nuclear Power Program aboard USS Trepang (SSN-674) with deployments on the USS Grant (SSBN-631) and the USS Seahorse (SSN-669.) Reactor Controls Assistant, Main Propulsion Assistant and Assistant Engineer. • Diverse experience managing engineering divisions while operating and maintaining naval nuclear power plants. Completed 22-month major refueling overhaul. Directed portions of core replacement, initial core testing and criticality. As Assistant Engineer responsible for all aspects of a four division, 63 person engineering department of the nuclear attack submarine USS Trepang (SSN 674.) Experience provided excellent leadership training and extensive management insight into optimizing decision making while operating in a highly integrated complex system. Show less Served in the Naval Nuclear Power Program aboard USS Trepang (SSN-674) with deployments on the USS Grant (SSBN-631) and the USS Seahorse (SSN-669.) Reactor Controls Assistant, Main Propulsion Assistant and Assistant Engineer. • Diverse experience managing engineering divisions while operating and maintaining naval nuclear power plants. Completed 22-month major refueling overhaul. Directed portions of core replacement, initial core testing and criticality. As Assistant Engineer… Show more Served in the Naval Nuclear Power Program aboard USS Trepang (SSN-674) with deployments on the USS Grant (SSBN-631) and the USS Seahorse (SSN-669.) Reactor Controls Assistant, Main Propulsion Assistant and Assistant Engineer. • Diverse experience managing engineering divisions while operating and maintaining naval nuclear power plants. Completed 22-month major refueling overhaul. Directed portions of core replacement, initial core testing and criticality. As Assistant Engineer responsible for all aspects of a four division, 63 person engineering department of the nuclear attack submarine USS Trepang (SSN 674.) Experience provided excellent leadership training and extensive management insight into optimizing decision making while operating in a highly integrated complex system. Show less
-
-
Education
-
University of Minnesota
MS, Material Science & Engineering -
University of Virginia
BS Chemical Engineering, Chemical Engineering
Community
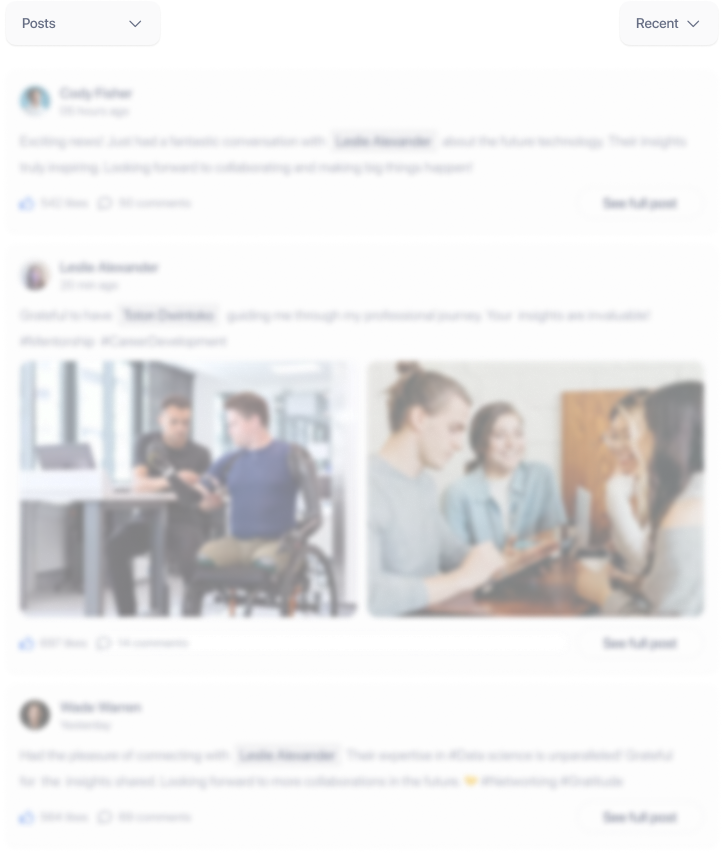