Patty Goodwill
Vice President Of Global Supply Chain at AA Metals, Inc - COVID-19 Response Supplier- Claim this Profile
Click to upgrade to our gold package
for the full feature experience.
Topline Score
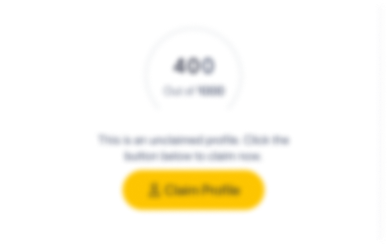
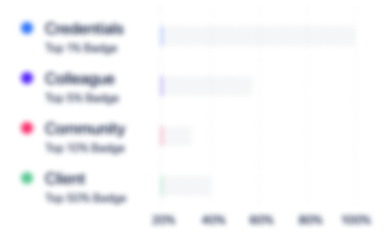
Bio


Credentials
-
CPM
-
Experience
-
AA Metals, Inc
-
United States
-
Mining
-
1 - 100 Employee
-
Vice President Of Global Supply Chain
-
Feb 2021 - Present
-
-
-
Eaton
-
Ireland
-
Appliances, Electrical, and Electronics Manufacturing
-
700 & Above Employee
-
Director, Supply Chain
-
2017 - 2020
Lead the overall supply chain function for the Fluid and Motion Controls Division ($1.2B Sales) across the 9 locations of the division. Responsible for definition and execution of the supplier strategies for all externally supplied material. Management of the divisions purchases globally, coordination and execution of the division's NPI programs as it relates to external suppliers, continuous improvement of supplier quality and supplier delivery. Responsibility for purchase order compliance to DFAR/FAR purchasing regulations.
-
-
-
GE Transportation, a Wabtec company
-
United States
-
Truck Transportation
-
700 & Above Employee
-
Executive - Global Purchasing Director
-
2014 - 2017
Key responsibilities include leading a team of 100+ employees globally to purchase $2B in material annually to support multiple domestic and global factories and distribution centers. Led teams to support initiatives such as deflation ($111M in 2015), lean and lead time reduction on purchased material. Centralized team functions globally, including 4 US sites, 3 in Mexico and one in South Africa to improve on time delivery by 30% in our global operations.
-
-
Senior Locomotive Purchasing Manager
-
2012 - 2014
Key responsibilities included leading a team of 45+ salaried employees in the US and Mexico to purchase $1.1B in material annually to support locomotive production in 2 facilities in the US. Acted as a change agent creating a centralized purchasing function creating standard work between the organizations and leveraged the standard work to improve supplier on time delivery from 75% to 94% while achieving 4% productivity annually. Lead the purchasing function to implement a new MRP system for the factory start up in Fort Worth, Tx working closely with IT to ensure the system would meet the business needs while having zero interruption to our customers and suppliers.
-
-
Senior NPI Sourcing Proposal Leader
-
2010 - 2012
Successfully worked cross functionally with proposal engineering, commercial proposals and program management to ensure the target costs and program schedules were aligned to achieve the business operating margin targets during the proposal process for purchased materials.
-
-
Senior NPI Sourcing Program Manager
-
2007 - 2010
Managed new product development with suppliers to support new locomotive requisitions both domestically and internationally to ensure that the target costs and program schedules were met to support customer requirements and business needs. Worked cross functionally with engineering to ensure drawings and product specifications were delivered on time to support the build plan. Worked closely with the commodity team to support price negotiations on the new product launch, including the service requirement and after market, as well as with supplier quality engineering to ensure all parts delivered met all quality requirements before acceptance.
-
-
Plant Manager
-
2005 - 2007
Lead a team on 250 union hourly employees and six salaried employees to build steel fabricated, welded and painted components to support both new production as well as the service parts business while ensuring a safe environment for all team members and compliance with all government regulations for paint emissions and waste water management. Reduced cycle time by 50% on large structures and improved OTD from 57% to 92% by implementing lean principles. Worked closely with the EHS team to reduce injury rates by 35% utilizing combined management and hourly safety teams to identify risks and implement projects to eliminate or reduce those risks.
-
-
Project Manager
-
2004 - 2005
Managed locomotive and engine overhauls for aging locomotive fleets in Mexico. Key responsibilities included forecasting material consumption rates, forecasting labor hours to complete the overhauls and ensuring the operations team met the customer targets on delivery of the units while meeting the operating margins targets for the program.
-
-
Global Commodity Manager
-
2001 - 2004
Managed domestic and global suppliers on $30M in gearing for the supply chain. Key responsibilities included negotiating multi-year contracts, achieving deflation goals of 8-10% annually as well as identifying and developing new suppliers in low cost countries to reduce single sources and achieve the deflation targets.
-
-
Supply Chain Specialist
-
1995 - 2001
Various supply chain roles in materials, quality, and operations with increasing responsibility include shop floor supervisor, materials advisor, quality engineer, supplier development engineer, and buyer.
-
-
Education
-
Gannon University
Master of Business Administration (M.B.A.) -
Gannon University
Bachelor's Degree, Electrical Engineering
Community
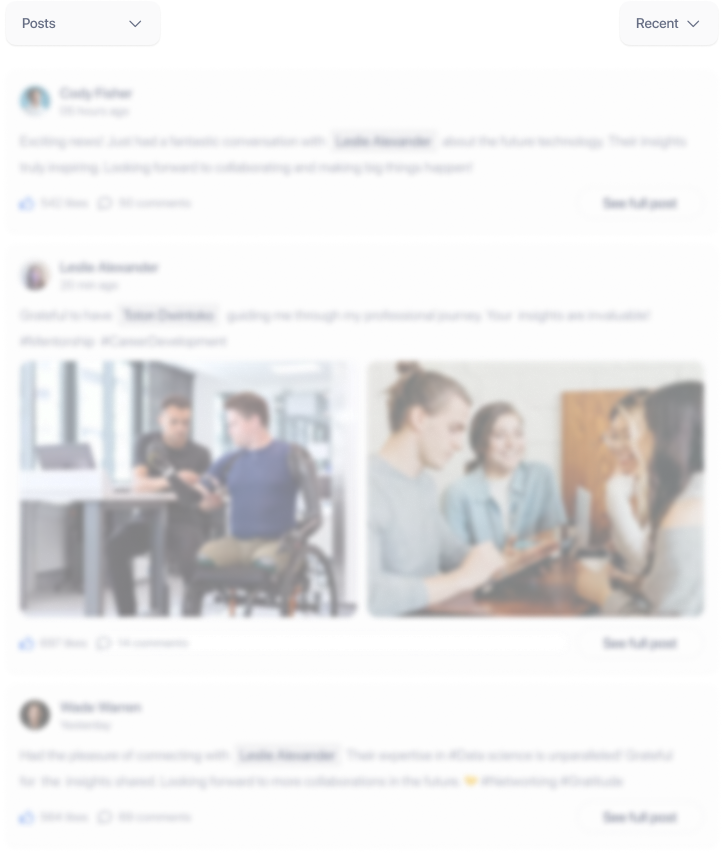