Patrick Leonard
Senior Project Manager at Marietta by Voyant Beauty- Claim this Profile
Click to upgrade to our gold package
for the full feature experience.
Topline Score
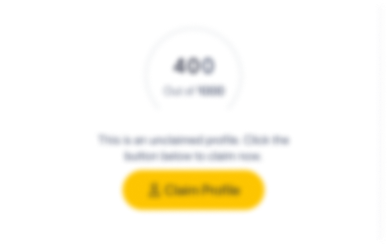
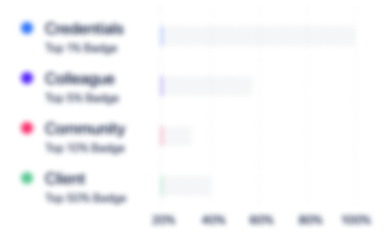
Bio


Experience
-
Marietta by Voyant Beauty
-
United States
-
Hospitality
-
100 - 200 Employee
-
Senior Project Manager
-
Jun 2022 - Present
-
-
-
Oil-Dri Corporation of America
-
United States
-
Mining
-
300 - 400 Employee
-
Plant Manager
-
Jul 2019 - May 2022
• Led team of 100 in the support of the 65% of the business’ kitty litter production. • Sustained a 99.8% customer service lever during the COVID pandemic as an essential business outperforming completion which resulting in a ~15% business growth. • Developed and managed $17MM annual budget. • Increased overall plant OEE by 2.5% (10% growth on key line) in year 1 through data analysis and the implementation of select TPM programs. • Elevated site Safety and quality awareness / culture through the development and implementation of BBS (Behavior Base Safety), team safety engagement and BBQ (Behavior Based Quality) initiatives. • Developed and implemented site growth strategy to coincide with business growth. • Increased team moral and recognition through the implementation of “Raising the Bar” Teammate of the Month program. Show less
-
-
-
Mars
-
United States
-
Manufacturing
-
700 & Above Employee
-
Production Manager
-
Mar 2017 - Jul 2019
• Led operations team to include production, logistics, sanitation and training departments in a highly automated pet food manufacturing facility of 300+ associates. • Launched TPM pillar to improve associate communication, capture amoralities and determine root causes. • Conducted autonomous maintenance (AM) initiative that drove a waste reduction of 80% resulting in $100M in annual savings. Effort is being duplicated and is expected to result in $500M + in annual savings. • Developed and implemented performance based training and implemented virtual knowledge capture and knowledge transfer system. • Captured $125M in Arkansas state training grants to increase associate skills and site expansion readiness. • Championed launch and integration of SAP in factory and off-site warehouse. Show less
-
-
-
The Scotts Miracle-Gro Company
-
United States
-
Consumer Goods
-
700 & Above Employee
-
Operations Manager
-
Jul 2015 - Mar 2017
• Led Operations team of 100 + associates to support the southern US and Mexico markets and safely produce products that meet business cost requirements. •Developed program with a focus on team work and changeover reduction that resulted in a 4% increase in plant efficiency. •Identified key area training lapses and filled knowledge gaps by providing focused training and launching AM and break down analysis programs. •Optimized labor that resulted in a $101M savings. • Led Operations team of 100 + associates to support the southern US and Mexico markets and safely produce products that meet business cost requirements. •Developed program with a focus on team work and changeover reduction that resulted in a 4% increase in plant efficiency. •Identified key area training lapses and filled knowledge gaps by providing focused training and launching AM and break down analysis programs. •Optimized labor that resulted in a $101M savings.
-
-
-
Reckitt
-
United Kingdom
-
Manufacturing
-
700 & Above Employee
-
Operations Manager
-
Dec 2014 - Sep 2015
• Led team of 80+ production and maintenance team associates ensuring products were manufactured in alignment with quality standards and within cost parameters. • Implemented processes that balanced maintenance budget after a FY2014 $1.1MM overage. • Developed and implemented site growth plan that moves site from reactive to planned maintenance and integrates TPM methodology into daily operational processes. • Led team of 80+ production and maintenance team associates ensuring products were manufactured in alignment with quality standards and within cost parameters. • Implemented processes that balanced maintenance budget after a FY2014 $1.1MM overage. • Developed and implemented site growth plan that moves site from reactive to planned maintenance and integrates TPM methodology into daily operational processes.
-
-
-
Unilever
-
United Kingdom
-
Manufacturing
-
700 & Above Employee
-
TPM Manager
-
Jan 2014 - Dec 2014
•Managed $10 million dollar maintenance budget assuring the manufacturing facility and 29 production lines are optimized and fully support business requirements.•Led team of 3 supervisors and 50 + team associates assuring departmental goals are achieved.•Implemented factory change using TPM methodology and direction resulting is a 5 point increase in factory OEE.• Delivered $3.5 million dollars in site cost savings.
-
-
Site Integration Project Manager
-
Jan 2012 - Jan 2014
•Managed $40 million dollar site expansion project with a scope that consisted of adding 6 highly automated production lines, multiple mixing assets and an increased site staff of 125 new employees.• Developed and implemented site master, knowledge transfer and training plans to assure project met established metrics.• Launched VIP (Value Improvement Program) and exceeded target by 40% resulting in over $1.1 million in first year savings.
-
-
-
Unilever / Alberto Culver
-
Jonesboro, Arkansas Area (Unilever Acquired Alberto Culver)
-
Contract Manufacturing Manager
-
Jul 2009 - Mar 2012
•Managed $80 million dollar contract manufacturing business at Unilever’s Jonesboro Arkansas manufacturing facility. •Supported business unit by providing direction and focus of plant activities to produce custom label products for new and existing customers. •Led teams to ensure metrics for customer service, quality and cost of producing custom label products are aligned with corporate objectives and consistently achieved through continuous improvement. •Reviewed first run cost audits and coordinating actions to achieve quote costs. •Reported variances and requested activity to aid Finance to accurately measure performance to standard and gauge profitability. •Developed and implemented program that led to an increased customer service level by nineteen points that resulted in a sixty percent (1.2MM unit) increase in business. •Managed customer visits, delivered introductory presentations, plant tours and served as the plant’s contract manufacturing ambassador. •Developed processes and procedures to streamline the quoted request and contract manufacturing formula registration process. Show less
-
-
-
Alberto Culver
-
Personal Care Product Manufacturing
-
100 - 200 Employee
-
Project Coordinator - Senior Project Coordinator - Global Brand Supply Chain Leader
-
May 2004 - Jun 2009
•Provided management oversight to develop and launch new products by partnering with all cross-functional groups and stakeholders to create an active supply chain and optimize operational efficiencies where possible.•Ensured strategic alignment across the supply chain disciplines including: Procurement, Packaging, Engineering, Manufacturing, Quality and Logistics.•Worked closely with Regional Project Coordinators to guarantee the proper execution of globally directed initiatives.•Managed and coordinated new product launches from ideation to full commercialization. •Supported twelve consumer brands and multiple domestic and international projects.•Built teams consisting of and not limited to Research and Development Scientists, Package Engineers, Purchasing Agents, and Marketing Managers.•Conducted task force meetings that drove results by providing members with time lines and guidance with a focus on customer service and on-time delivery.•Led project status presentations for department managers, company directors and vice presidents.•Coordinated all significant investment requirements for projects in terms of capital (equipment, molds, and change parts) and materials needed for project implementation.•Provided training, mentoring and guidance to Project Coordinators and company personnel involved in the Alberto Culver Innovation Process. •Represented department as a subject matter expert in the mapping of site’s SAP system.•Led sustainability projects that resulted in $250M in yearly cost savings through the modification and implementation of policies that changed the way materials were managed with suppliers and the distribution network.•Wrote department policies and procedures. Show less
-
-
Chemical Processing Area Manager - Production Area Manager
-
Jan 1999 - May 2004
•Supervised 50+ union and nonunion employees in a multi-line, high-speed, production environment.•Managed staffing levels to maximize department output while maintaining variances.•Monitored, tracked, and posted output and efficiencies providing employees with clear focus and upper management with updates on shift performance.•Utilized computer driven MRP system (Prism) to track materials, work status, and customer requirements.•Facilitated several unique continuous improvement teams ranging from safety improvements to cost reductions.•Established $300M in yearly cost savings by modifying processes and improving line change-over efficiencies. •Conducted plant meetings communicating company growth, quality initiatives, and safety issues.•Managed payroll and all time-keeping issues for personnel.•Managed a chemical processing department in the support of 13 filling lines with a staff of union sanitation and salaried chemical processing technicians.•Monitored department output that averaged 17 million pounds of product per month.•Established, tracked, and processed blend schedules utilizing computerized MPR system.•Built sound relationships with Production, Research and Development, and Quality staffs.•Performed production floor and chemical processing area GMP and safety audits.•Developed and implemented production line sanitation procedures. Show less
-
-
-
Filtration Group
-
United States
-
Manufacturing
-
300 - 400 Employee
-
Production Supervisor
-
Jan 1994 - Jan 1999
•Hired, trained, and evaluated employees, planned production and work schedules, and maintained quality and quantity standards. •Managed multiple departments ranging from assembly line production to job-cell manufacturing. •Tracked departmental inventories and planned production utilizing QAD MRP system. •Established a quality program that reduced scrap and promoted “quality” throughout the department. •Performed monthly safety meetings to coincide with OSHA requirements. •Composed, edited, and published departmental SOP’s and JSA’s. Show less
-
-
Education
-
University of Maryland College Park
BS, Business Management -
Villanova University
Master Certificate in Six Sigma, Six Sigma
Community
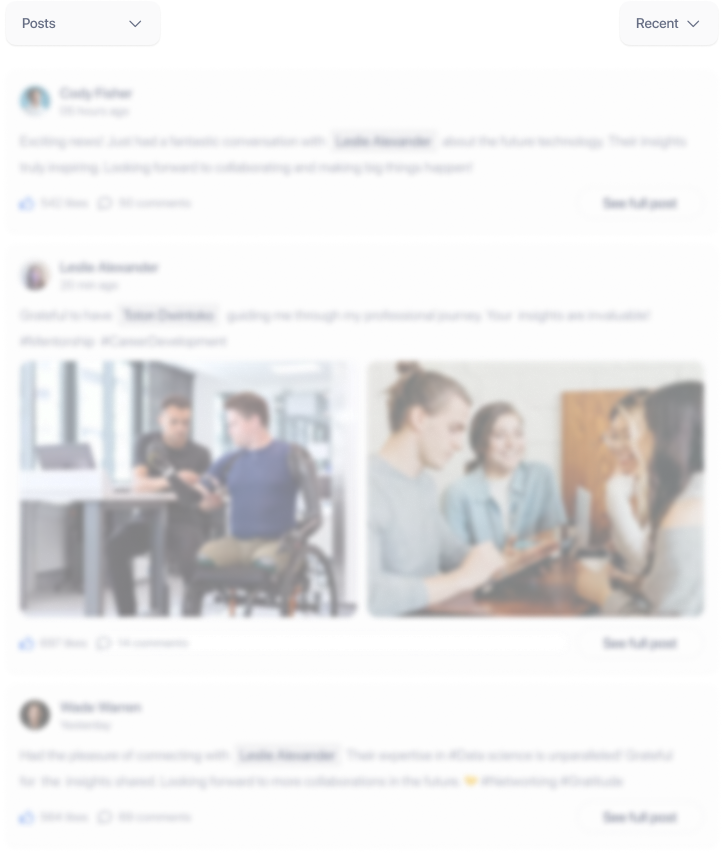