Patrick Gipper
System Engineer at Array of Engineers- Claim this Profile
Click to upgrade to our gold package
for the full feature experience.
Topline Score
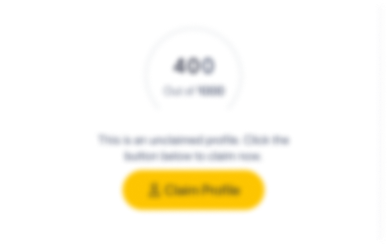
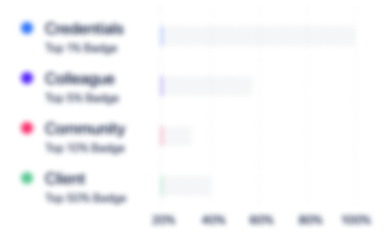
Bio


Experience
-
Array of Engineers
-
United States
-
Electrical Equipment Manufacturing
-
1 - 100 Employee
-
System Engineer
-
Jun 2020 - Present
Providing expertise in architecting and defining hardware/software requirements to the Aerospace industry. Providing expertise in architecting and defining hardware/software requirements to the Aerospace industry.
-
-
-
Parker Aerospace
-
United States
-
Aviation and Aerospace Component Manufacturing
-
700 & Above Employee
-
Principal Engineer
-
2009 - May 2020
-System engineer for the XCAC MA700 Hydraulic System Controller. The Hydraulic System Controller is a software embedded electronic unit intended to perform control functions on the airplane. I assumed responsibility for the definition of hardware/software requirements on this project with a highly accelerated schedule while customer requirements were still changing. As a result, software development proceeded quickly, and the controller was delivered according to customer schedule.-Lead system engineer for the Boeing 777-8/-9 Main Gear Steering System. The Main Gear Steering System, consisting of a control unit and pair of actuators, was originally qualified for the 777 in the 1990s. This project certified this system for operation in the environment expected for the 777-8/-9. I was involved in all aspects of this project, starting with test plans, procedures, test fixture drawings, system integration, testing, and finally concluding with qualification reporting/similarity analyses. The entire effort concluded successfully prior to the airplane first flight.-Lead Avionic System Engineer on the Hydraulic Module operating as a hosted function in the integrated modular avionics architecture on the COMAC C919. The module will incorporate all the typical control, indication and maintenance functions of the hydraulic system, but will interface to the IMA via data concentrators. During the early phases of development this required international travel for on-site negotiations with the customer as well as interfacing aircraft partners. The airplane is currently undergoing flight testing directed towards certification. Show less
-
-
Principal Engineer
-
2009 - 2015
-Electrical system engineer for the Airbus A350 hydraulic system. This entailed coordinating with internal and external equipment suppliers to ensure that the specific Airbus Directives for electrical requirements are understood and followed. Specifically, the EMI/HIRF/Lightning requirements of ABD0100.1.2 and the electrical interface requirements of ABD0100.1.9. The large amount of composite structure on the aircraft made the lightning requirements especially challenging for equipment interfaces with the aircraft power bus.-Lead On-Board Maintenance System definition for Hydraulic Monitoring Control Application as a hosted application for the integrated module avionics architecture on the Airbus A350. My specific technical contributions consisted of; 1) Defining the system boundaries for testing 2) Specifying the monitoring logic 3) Definition of interactive testing method such that each hydraulic system’s dual parallel hosted applications could uncover latent failures 4) Integrating hydraulic sub-system component fault detection capability into the overall application reporting interface 5) Simulation of the monitoring and control application functionality with a system model to validate customer design. 1-4 above is captured in the system’s Fault Detection Specification per Airbus processes of ABD0100.1.4. Show less
-
-
Principal Engineer
-
2004 - 2009
-Lead Avionic System Engineer embedding the Hydraulic Interface Function as a hosted application for the integrated modular avionics architecture on the Boeing 787. The application is responsible for control, indication and maintenance functions for the aircraft triply redundant hydraulic system. The deliverable source lines of code (100K SLOC) are orders of magnitude greater than the division previous experience. To allow software certification to DO-178B, we had to greatly enhance our capabilities for requirements management, configuration management and problem reporting. New tools had to be deployed (DOORS, MKS) and the processes to utilize them had to be developed. We were very successful in this endeavor becoming one of the earliest to deliver to Boeing integration labs. In addition our software was often used to judge the operability of other interfacing systems. My specific technical contributions consisted of; 1) Several years of on-site customer system requirement definition and design 2) ARINC 664 messaging system definition for communication interfaces 3) Crew Alerting and Synoptic Page high and low level function definition 4) Various hydraulic components control definition 5) Hydraulic system fault logic definition 6) Lead engineer for On-Board Maintenance System interface and functional test definition 7) Lead engineer for test definition and integration testing of initial lab and flight test aircraft deliveries prior to availability of formal certification test capability 8) Lead engineer for system requirement document design 9) Document release engineer for iterative development effort and system level updates for problem reports Show less
-
-
Project Engineer
-
2003 - 2004
-Design, integration and verification test of DSP embedded controller for hydraulic motor driven 5 KVA/3 phase aircraft emergency generator.
-
-
Senior Engineer
-
2002 - 2003
-Analyzed field returns of electro-mechanical locking system exhibiting high failure rate, tracing primary cause to thermal low cycle fatigue induced mechanical failure of encapsulated circuit board. I developed the Pareto analysis serving as basis for subsequent redesign. I also served as the project engineer and DER in the re-qualification effort of the new design. This new design has now been in the field for many years and exhibits significantly reduced failure rates.
-
-
Controls Engineer
-
1984 - 2002
-Spent many years working on the design of electro-mechanical actuators as applied to missile controls. Responsible for many areas; 1) Selection of electric motors and gearing to optimize dynamic performance 2) Design of position control in either analog or embedded digital controller 3) Simulation/modeling to predict hardware performance 4) Lab testing for validation and verification
-
-
Controls Engineer
-
1996 - 1997
-On the F18 E/F aircraft, re-designed four way dual system hydraulic valve and mode select valve for performance improvement that alleviated problems with stability, hydraulic lock and thermal heating.
-
-
Senior Specialist
-
1992 - 1995
-Design and test of flow force compensated, high flow rate direct drive valve (DDV). This DDV was the first for force compensated and highest flow rate valve ever developed for the division. I was responsible for sizing, valve geometry selection, testing and analysis.-Design and integration test of a high performance thin wing hydraulic actuation system on a black aircraft program. I was responsible for all analysis, simulation development and integration testing of a variable area, large inertial loaded actuator. My design for an analog electronic controller incorporated dynamic pressure feedback for load stabilization, as well as mode switched gain and filter time constants.-Member of a trouble shooting team to solve qualification test problems for aircraft engine thrust reverser actuation system. Re-design of the test system electronic controller for load control using novel techniques achieved higher levels of load accuracy, preventing over-testing. The thrust reverser system subsequently completed qualification and entered production. Show less
-
-
Education
-
Cleveland State University
MSEE, Control Systems -
Michigan State University
BSEE
Community
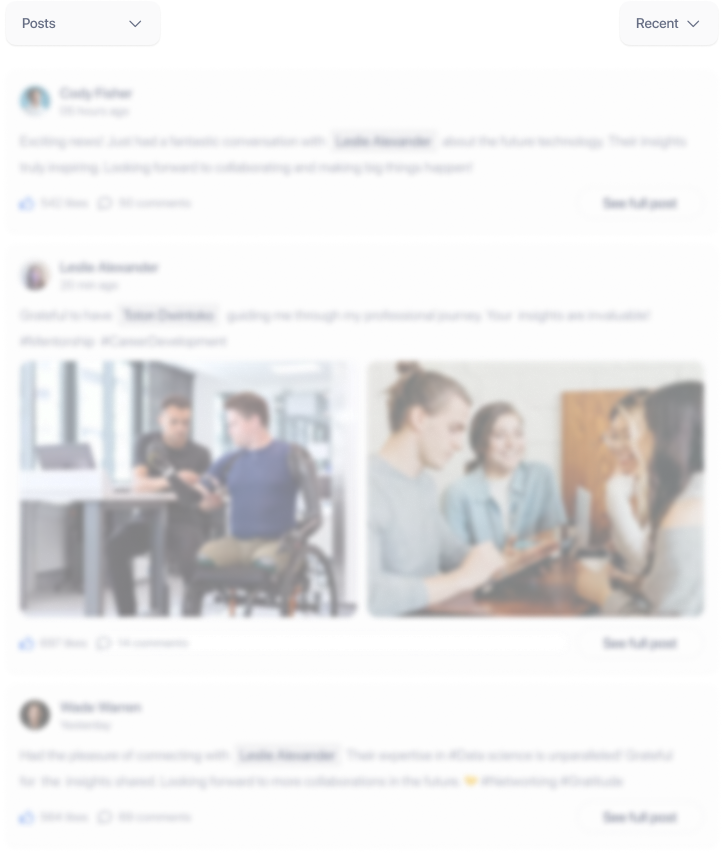