Patricio Morton Perez
Quality Engineering Supervisor at SLPT Global Pump Group- Claim this Profile
Click to upgrade to our gold package
for the full feature experience.
-
English -
-
Spanish Native or bilingual proficiency
Topline Score
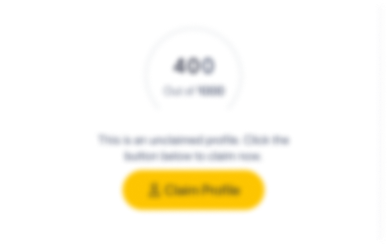
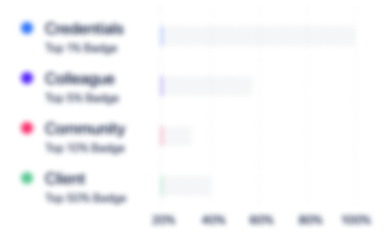
Bio


Credentials
-
Exemplar Global-Certified ISO 9001:2015 Internal Auditor Training with IATF 16949:2016 Automotive Emphasis
AIAG - Automotive Industry Action GroupNov, 2019- Nov, 2024
Experience
-
SLPT Global Pump Group
-
United States
-
Motor Vehicle Manufacturing
-
1 - 100 Employee
-
Quality Engineering Supervisor
-
Jul 2023 - Present
• Maintain access to customer web sites and databases to ensure compliance to customer specific requirements, including customer plant quality issues requiring 8-D responses • Lead the 24hr response to customer complaint with timely follow-up & Closure of the 8D’s • Lead or support problem solving analysis; report on customer field returns with product engineering as part of a cross functional team. This analysis includes visual, mechanical, dimensional and metallurgical characteristics. Determine the root cause to drive corrective/preventive actions • Prepare PPAP packages as required • Lead & mentor a team with quality technicians, quality engineer with focus on the customer & internal quality • Lead or support problem identification, resolution, and continuous improvement • Review and analyze performance (i.e. Machining, Contamination, Assembly, End of Line Data, etc.) using SPC/other tool and drive timely corrective actions in support of process capability maintenance and improvement. • Perform Layered Process Audit, internal audits, manufacturing process audits & support closure of findings and resolution • Support development of risk reduction and detection (Poka Yoke) of non-conforming product characteristics • Report quality issues and trends to management • Support IATF 16949, VDA, ISO 14001 activities to maintain its certification • Other quality related & cost saving projects as assigned in support of business goals • Lead investigation of non-conforming product. • Review customer drawings, specifications and change requests as required, ensure that the criteria and provisions are included in the Quality documents. • Conduct data acquisition verifications to ensure the production data collection system aligns with the control plan and product drawings • Support and lead APQP tasks (i.e. prototype control plan, process flow, PFMEA, process documentation, problem solving, gauge planning and acquisition) Show less
-
-
-
ZF Group
-
Germany
-
Motor Vehicle Manufacturing
-
700 & Above Employee
-
Senior Quality Engineer
-
Nov 2017 - Jul 2023
Customer Senior Quality Engineer • Act as key interface between customer and the Chasis Technology (CT) - Suspension organization (Product Plants, Sales Org, Engineering Org, Purchasing / Supply Quality). • Communicate regularly with all levels of customer quality organization to keep the customer view of CT quality performance up to date. • Collect all information about CT quality situation in the North America market using face to face meetings with the customer and using all specific portals. • Understand and follow all customer specific quality systems and procedures. • Coordinate and control closure of all customer related corrective and preventive quality subjects (e.g. product development issues, 0 ppm’s, warranties) in close cooperation with CT production plant quality, supplier quality and engineering organizations. • Lead presentation of CT quality issues to the customer and discussions with the customer. • Report regularly the customer specific CT quality status to CT Top Management in a transparent and complete manner. • Lead Root Cause analysis investigations with the core team in the plant, assure ICA’s/PCA’s are implemented in time and form. • Develop readiness, horizontal deployment and lesson learned activities for continuos improvement. Show less
-
-
-
Takata
-
United States
-
Motor Vehicle Manufacturing
-
700 & Above Employee
-
Quality Assurance Engineer
-
Dec 2015 - Oct 2017
Current Quality Assurance Engineer for the GM Business Unit for the manufactured devices produced by Takata in the North America's region. Principal activities described as following:• Contribute to follow up the tendencies chart of the global Quality Complaints (General Motors - PRR's) for all Takata plants, by analyzing the current failure modes and the proper following up to problem solve the most contributors in order to reduce 80/20 of the issues.• Coordinate and lead the transition of the GM certification -Built in quality supplier based (BIQS)- which is the current target to have all the plants merged into this specific certification that has emigrated from QSB+.• Follow up on the CTF's (Car Test Fleet) issues for all devices of NA region.• Work in the re-engineering of the process on some specified projects to improve and reduce PRR’s / CTF's / PRTS's and most of the customer complaints for the NA's plants.• APQP activities for new models as a Quality contact to the plants in order to meet with the target time and form of each component / program.• Quality bridge contact between the plants of Mexico and the Corporation at Auburn Hills, Michigan, currently handle QRDCP meeting at GM.Extra Activities / Targets & Goals:• Risk Mitigation Gap Analysis between current PFMEA vs DFMEA. Reduction of the gap analysis by a 44% on Airbags, Seatbelts and Steering Wheels devices by performing the gap analysis at the NA Plants. Planned to continue with the critical Tier 2’s.• Perform a deeply analysis of all global plants in order to complete all exit criteria of the current status of the company with one of the customers which is New Business in Hold, Bi-weekly meetings with the plants in order to show the progress to the customer. Current progress as of 2015 is 90%.• Cost reduction by disputing quality customer complaints directly at the customer manufacturing plants. Show less
-
-
QC Customer Service Engineer
-
Oct 2013 - Nov 2015
Quality contact of Takata Steering Wheels Monterrey Plant of all the Ford Assembly Plants, which are located at the North America area, with the goal of having the customer satisfied. Specific functions: • Follow up on the quality customer complaints. Since this is issued until this one needs to be closed. • Quick reaction at the plant when a customer complaint is issued. Assurance of the containments in all the locations when a quality complaint is already informed. • Coordinate every requirement from the customer at the manufacturing facility. • Usage of the different quality tools to answer to the customers (8D, 5P, 7Steps, DDW, etc.) • Follow up on the Quality scorecards of the plant (PPM’s, KPM, Quality Index) • Coordinate Quality Projects and Continuous improvements of the different programs in order to reduce the customer complaints (Reduction of PPM’s) and the current % of the scrap of the plant at the mentioned BU.• Travel to the Customer Manufacturing Plants to assure the satisfaction and requirements of the Customers. Extra Activities / Targets & Goals:• Ensure that the Permanent Containment Actions are already validated and proved on the assembly lines; following up on the systemic permanent actions to ensure that the problem will not be repetitive. • Coordination with the Business Unit Engineers for the update of the quality documents PFMEA, Quality Control Plan and Past Problem History, etc.• Almost 50% of reduction of the PPM’s and IPPM’s of Steering Wheel plant with the OEM (Ford), per the defined goal on the beginning of the FY15 70PPM’s per month, to almost the half 36 PPM’s per month at the end of FY15. Show less
-
-
Warranty Department
-
Jun 2011 - Oct 2013
• Responsible to receive, inspect (visually and technically) and give a root cause of the warranties such as Airbags, Seatbelts and Steering Wheels to the assigned customers (Experience with US and Japanese Customer), finding the optimal solution of each one and provide a response to the customer in time and form. • Perform efficient action plans in the plants or locations to follow up on failure modes in order to avoid them on future parts. • Generate reports to costumers, with success to response and let know them the investigation, analysis and a final root cause. • Directly negotiation with the costumer for the warranty cost reduction. • Investigation and quality improvement directly in the production lines for the success of customer requirements. Extra activities / Targets & Goals:• Qualified Auditor of ISO/TS 16949 having internally audits directly at mass production lines. • With the PDCA Tool, was nullified the high cost of warranties on the Toyota Matrix front Seatbelts, on the specific following up of the top failure modes. Show less
-
-
-
Grupo DEACERO
-
Mexico
-
Primary Metal Manufacturing
-
700 & Above Employee
-
Logistica / Servicio de Mejora
-
Aug 2010 - Dec 2010
• Find the root cause solution of the different complaints from the costumers. • Responsible to carry out and the validation of the preventive and corrective actions of the complaints from the customers to ANSA (Aceros Nacionales, S.A. de C.V.) • Report and control of the process to validate complaints. • Find the root cause solution of the different complaints from the costumers. • Responsible to carry out and the validation of the preventive and corrective actions of the complaints from the customers to ANSA (Aceros Nacionales, S.A. de C.V.) • Report and control of the process to validate complaints.
-
-
-
The Home Depot México
-
Mexico
-
Retail
-
700 & Above Employee
-
COOP- Global Sourcing
-
Mar 2009 - Mar 2010
• Internship at Global Sourcing Area with different activities. • Statistic Control of the suppliers from Latin-American for the correct fulfillment of the purchase order´s. • Satisfactory development of Final Evaluation Program (Thesis Carrier) “Costs reduction per devolutions to The Home Depot México”. • Development of quality project, “Reduction of cycle time in the process to select a new supplier, factory and/or new product for The Home Depot México”. • Research and selection of new suppliers from Latin-America for the market of North America. • Research of innovation products to introduce to the store. Show less
-
-
Education
-
Universidad de Monterrey
Engineer's degree, Industrial and Systems Engineer -
Takata Monterrey 1
Green Belt Certification, Quality -
International House Vancouver
English Program Immersion, English Inmerssion Program
Community
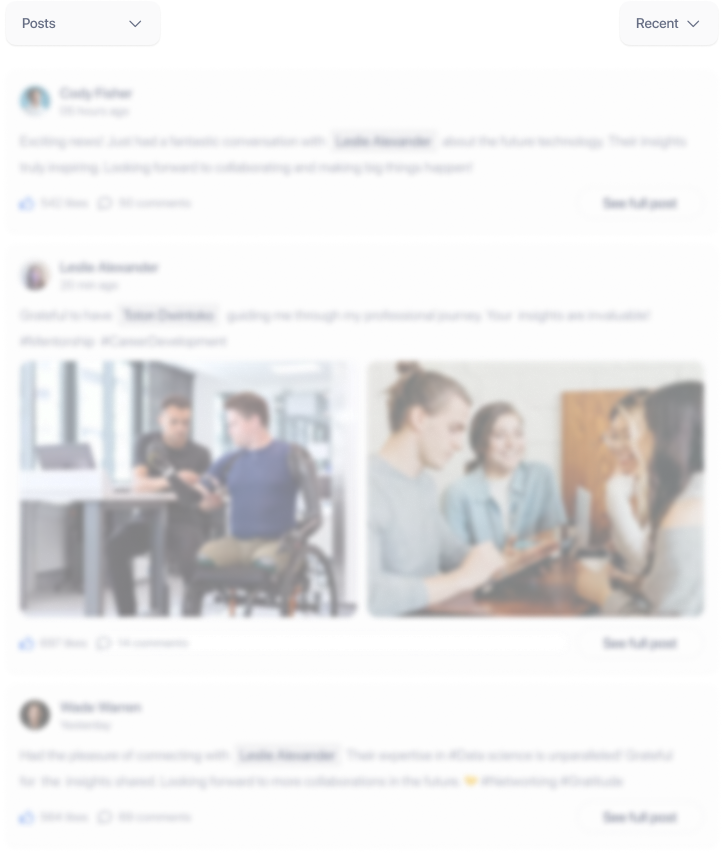