Pat Klug
C-130 Technical Writer at DKW Communications, Inc.- Claim this Profile
Click to upgrade to our gold package
for the full feature experience.
Topline Score
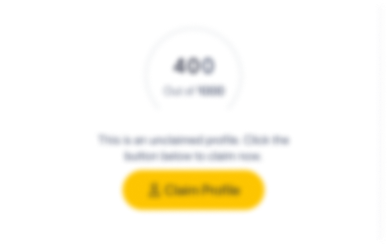
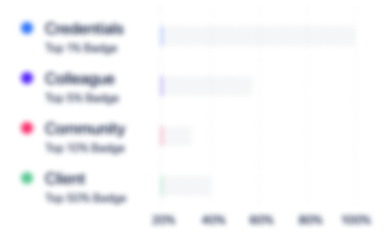
Bio


Credentials
-
Business Etiquette: Phone, Email, and Text
LinkedInMar, 2019- Oct, 2024 -
Communication Foundations
LinkedInMar, 2019- Oct, 2024
Experience
-
DKW Communications, Inc.
-
United States
-
IT Services and IT Consulting
-
100 - 200 Employee
-
C-130 Technical Writer
-
Aug 2019 - Present
Performs research of technical data sources throughout Department of Defense (DoD), Naval Air Technical Data & Engineering Service Command (NATEC), Naval Air Warfare Center Training Systems Division (NAWCTSD), and various government and commercial sources to prepare technical data outfitting packages in support of NAWCTSD. Review and update documents as well as prepare documents for delivery. Maintain the KC-130 technical documentation library. Edit documents using Microsoft Word, AutoCad and TurboCad engineering drawing programs. Prepare and submit KC130 Trainer Equipment Change Directives for hardware modifications and software block updates. Maintain the site Master Publications list, KC-130 TECR database and hardware equipment inventory database. Conduct inventory and maintain database of classified materials and contract deliverables. Show less
-
-
-
Fleet Readiness Center East
-
Cherry Point, NC
-
Data Management Specialist
-
Jun 2017 - Aug 2019
Performs research of technical data sources throughout Department of Defense (DoD), Naval Air Technical Data & Engineering Service Command (NATEC), and various government and commercial sources to prepare technical data outfitting packages in support of FRCE new workload capability establishment, in support of Commander Fleet Readiness Center (COMFRC} "Off Flight Line" maintenance. Ability to organize, compile and manage a wide variety of data elements and coordinate data requirements effectively, with accuracy and completeness. Knowledge of the interrelationship between FRCE LPDCSB and NATEC, regarding the procedures for researching, ordering, tracking and distributing technical data. Update Changes, Revisions, Iracs and, Eracs to technical pubs for H-53, AV8-B, H-1, V-22, C130, F402, P-3. Perform semiannual audits and annual audits for all shops assigned for accuracy of correct information. Knowledge of the interrelationship between FRCE LPDCSB and NATEC, regarding the procedures for researching, ordering, tracking and distributing technical data. Comprehensive knowledge of the NAVAIR 00-25-100 manual, FRCEASTINST 5605.S (Technical Data Control Manual), ISO certification and adherence responsibilities in order to manage technical publication requirements, within an industrial aircraft maintenance facility. Knowledge must demonstrate the ability to manage FRCE's Technical Publication Deficiency Reporting (TPDR) program. Show less
-
-
-
Hatteras Yachts
-
United States
-
Shipbuilding
-
1 - 100 Employee
-
Electrical, Mechanical and Hydraulic installer
-
May 2016 - Jun 2017
Practical knowledge of a wide range of technical engineering methods, principles, requirements, work techniques, and practices of an area of specialization, and skill in applying standardized, analytical, and evaluative methods and techniques sufficient to advise on and/or resolve difficult but well-precedent, factual, procedural, and/or recurring issues. Utilized proper Measuring and tooling devices like torque wrenches, feeler gauges, depth gauges. Made informed decisions on problems and issues, with the use of technical directives and various manuals to analyze segments of broader issues or problems (e.g., the impact of a change in one area on the entire system). Used analytical thinking to diagnose operational failures on various systems in the engine room. Determined extent of repairs, rework or replacement parts in multiple types of components. Perform installation, maintenance, operation, and testing duties and employ unique and specially designed precision instruments. Maintained one-of-a-kind equipment, custom equipment, developmental equipment, or equipment which is continually being modified and adapted and does not usually have adequate documentation and completed moderately difficult and complex survey work. Managed the installation, inspection of all electrical and mechanical components in the Hatteras 45 express Sport Fishing Yacht engine room. Thoroughly read and understand blueprints to ensure parts are installed in correct locations. Responsible for reading and understanding shop orders to ensure correct part delivery and accountability of correct parts before installation began. Managed and maintained accountability for all engine room parts and tools needed to complete daily tasks. Show less
-
-
-
United States Marine Corps
-
United States
-
Armed Forces
-
700 & Above Employee
-
Training Coordinator
-
Jan 2010 - Feb 2015
Coordinated USMC-wide training programs with Workforce Development personnel to ensure scheduling, course registration, classroom setup, and overall management of logistical arrangements associated with the training are accomplished. Required to participate in office or shop visits, meetings, or conferences to provide advice and assistance in the development of career management plans, programs, and initiatives. . Managed individual and collective tasks, skills, and certification requirements ensuring personnel were trained on operation, maintenance, and capabilities of all equipment and resources assigned to unit. Training classes were presented with visual aids mainly with the use of power point and handouts. Re-structured the training and education program for the Heavy Equipment platoon of MWSS 274.Classes were given to both entry level Marines as well as senior level advisors. Monitored, reported progress, and completion of training agreements. Assisted in the development of training curriculum and conducted lessons regarding career development as assigned. Participated in the design and creation of employee development programs to meet strategic organizational goals and objectives. Utilized life-cycle career development practices, principles, and evaluative methods sufficient to advise on and/or resolve moderately complex problems which are typically standard in nature. Researched career development/training requirements of all training agreements for Junior Marine, NCO’s and Staff NCO’s and reported findings/recommendations to the division chief. . Monitored various actions such as Junior Marine’s needs, on-the-job and promotion requirements, performance management, and recruiting. Conducted periodic non-complex training/information sessions to ensure awareness of initiatives, polices, and procedures that impact the programs. Show less
-
-
Foreman
-
Jan 2010 - Feb 2015
Planned use of worker's equipment, facilities, and materials on a day-to-day, project-by-project and on a week-to-week or month-to-month basis. Established deadlines, priorities, work sequences and planned work assignments based on general work schedules, methods and policies set by superiors. Coordinated work with supporting or related work units controlled by other supervisors. Determined the number and types of workers needed to accomplish specific projects; redirected individual workers and resources to accomplish unanticipated work. Informed higher level supervisors of the need to revise work schedules and re-estimated labor and other resource needs. Participated with superiors in initial planning of current and future work schedules, budget requests, staffing needs and estimates. Made recommendations as to scheduling projected work. Observed work in progress to anticipate and resolve problems; reassigned personnel and coordinates work among the work force and with other supervisors to maintain progress and to meet schedules. Inspected completed work for quality and work order requirements. Reported possible or actual work delays to higher level supervisors. Investigated work-related problems such as excessive costs or low productivity and determines causes. Implemented corrective actions to resolve work problems. Recommended solutions to staffing problems and/or work operations directed by other supervisors. Supported and explained management programs to subordinates. Investigated grievances and complaints, resolves them informally and notified superiors grievances that were of a serious nature. Assured safety and housekeeping practices were observed. Maintained work reports and records. Maintained accountability of equipment and personnel in the platoon. Managed the operational life cycle the company’s engineer equipment assets. Reviewed the maintenance production report daily and report equipment deadline status to the company commander. Show less
-
-
Tool Room Supervisor
-
Jan 2010 - Feb 2015
Received, stored, identified, and issued various items and tools used by shop personnel. Converted shop terms to standard nomenclature to identify and locate items. Items may include but are not limited to calibrated hand measuring tools, reamers, counter bores, milling cutters, cutting inserts and holders, die sets, jigs or fixtures, machine accessories or attachments, templates or form blocks, and tool kits. Performed necessary documentation, tagging and binning. Followed up to assure return of nonexpendable items and checks upon return for damage and maintenance needs. Initiated acquisition requests for unserviceable or worn tooling. Performed accuracy checks on calibrated items and recommended changes to calibration cycles to account for usage trends or ensure availability. Coordinated delivery and receipt of calibrated items between hand receipt holders and the calibration department. Performed preventative maintenance such as cleaning stock and parts, applying protective coatings, or replacing missing common hardware or other expendable accessories in tool kits or items. Contacted and scheduled visits of vendors to assist shop personnel with tooling solutions. Built consolidated tooling kits to support specific or commonly produced items using available or one-off tooling and creates storage locations for such kits. Coordinated with Production Control or shop supervisors to ensure availability of tooling or tool kits for planned/scheduled work. . Reported obviously damaged or inoperative tools, used or excess stock, or parts to superior. applied part or other identification numbers onto tooling using computer driven laser engraver, by hand stamping or etching, or by creating and attaching bar coded labels, as needed. Skilled in verifying short, over, and damaged conditions of incoming stock by such-means as opening, counting, and visually checking the contents of containers. Show less
-
-
Employment Coordinator
-
Jan 2010 - Feb 2015
Utilized life-cycle career development practices, principles, and evaluative methods sufficient to advise on and/or resolve moderately complex problems which are typically standard in nature. Provided life-cycle career development planning for new employees from entry to retirement or transition. Provided data, information, and routine guidance to program managers in the execution of the Intern programs and mid/senior level workforce development programs. Researched career development/training requirements of all training agreements for Junior Marine, NCO’s and Staff NCO’s and reported findings/recommendations to the division chief. Assisted in providing up-to-date training and career management information. Assisted training personnel to ensure course information is provided to attendees and resolve any problems. Performed a variety of administrative tasks associated with workforce career management, development and training programs. Reviewed materials to ensure certifications are codified correctly in position descriptions, assigned personnel have been notified by the proper authority. Certification requirements are identified, and tracked certification to ensure compliance. Advised division chief or other Senior Executive personnel when deficiencies are noted or projected. Evaluated and distributed approved information to the workforce that directly impacts their careers. Assists in the evaluation of Individual Development Plans (IDP) of acquisition personnel for currency and accuracy. Provided information and assistance to applicants on various boarded opportunities (e.g., training, career development, long-term assignments, Re-enlistment). Conducted periodic workforce member surveys to ensure information is current. Monitored various actions such as Junior Marine’s needs, on-the-job and promotion requirements, performance management, and recruiting. Show less
-
-
Heavy Equipment Platoon Sergeant
-
Mar 2007 - Feb 2015
Skills in interpreting project requirements to set up detailed work operations on a daily, monthly, yearly, and five-year schedule to meet established work schedules. Knowledge of relationships of organization and operations with agency organizations and operations and personal contacts, and with installation support organizations to coordinate daily work operations. Skill in using judgment to make selections, to set performance standards, evaluate performance, and determine additional training needs of subordinate personnel. Skill and knowledge of office automation programs and systems to include the Integrated Facilities System software. Established deadlines, priorities, and work sequences, in accordance with general work schedules, methods, and policies established by higher-level supervisors. Provided higher level supervisors of both task progress and completion. Determined the number and types of workers needed to accomplish specific projects through research and guidance of higher level supervisors. Assigned tasks to workers by verbal and written instructions. Counseled employees on a monthly basis on work performance, perform on the spot counseling for behavioral issues. Initiated and carried out disciplinary actions as needed Show less
-
-
Quality Control Inspector
-
Mar 2007 - Feb 2015
Thorough knowledge of all pertinent QC principles, practices, and methods, including statistical analysis and sampling applicable to the performance of a full range of QC responsibilities in Heavy Equipment. Broad knowledge of construction and maintenance standards, practices and techniques, building materials, and installation and maintenance of utilities sufficient to develop QC controls, to ensure product quality. Knowledge of inspection, test and measurement techniques. Skill in interpreting engineering drawings and specifications sufficient to identify potential quality problems. Skill in conducting studies and investigations. Plans and schedules periodic surveys or audits of Heavy Equipment and provides quality control (QC) advice and guidance to supervisors engaged in a full range of H.E. maintenance and operations functions, including the, mechanical maintenance, electrical maintenance, electronic systems maintenance, roads and grounds maintenance, vehicle maintenance, customer services support and the provision of professional and technical services. Investigates and analyzes customer complaints and associated QC deficiencies to determine origin, causes, and contributing elements, and prepares written evaluation reports concerning findings. Reports typically contain graphs, charts, and recommendations for changes in operating procedures. Serves as Safety Coordinator, with responsibility for developing an overall safety plan, conducting safety training, holding safety review meetings, ensuring that supervisors carry out their individual safety responsibilities, and monitoring various safety activities and reports. Serves as Warranty Enforcement Coordinator, with responsibility for monitoring and tracking all USMC Heavy Equipment property covered by manufacturers warranties, and exercising warranties to repair or replace any property/equipment that fails during the warranty period. Show less
-
-
Logistics Coordinator
-
Mar 2007 - Feb 2015
Extensive knowledge of all logistics disciplines with in-depth expertise in transportation and distribution operations (strategic and tactical) and systems. Knowledge of the combat development cycle and how the enhanced Concept Based Requirements System integrates modernization efforts. Knowledge of formal logistics guidance (doctrine and related documents) in order to execute the duties of analysis and development of solution sets to deployment and distribution process modernization issues. Extensive knowledge of strategic deployment and distribution planning, preparation and execution in order to identify deficiencies, develop solutions to such deficiencies, and assess the overall impact of planning and development activities. Knowledge of logistical automation systems, analytical methods, techniques and mechanisms, including the use of computers and computer simulations in order to develop sound problem identification and documentation and determine impact and effect of solutions. Knowledge of higher headquarters and agency information system standards, policies and authorized systems designs approaches, including DoD and Army Life Cycle Management techniques and documentation requirements. Knowledge of management principles, methods, techniques, and practices, mission and functions in order to complete initiatives and/or projects, developed new or improved techniques/methods, and applied such knowledge to the design, development, and implementation of management systems, supporting automation/information technology components. Working knowledge of Microsoft word, Microsoft Power Point, Microsoft Excel and windows to develop briefings, reports and findings. Proficiency in oral and written communications to include the ability to prepare and present briefings at all levels from Division through General officers of the United States Marine Corps for the logistical coordination and control of all motor transportation and heavy equipment assets. Show less
-
-
Licensing Coordinator
-
Mar 2007 - Feb 2015
In-depth knowledge of the WSMR Weight Handling Program and a comprehensive practical hands-on knowledge of all engineering/construction equipment typically used for projects found at military missile test installations, with a minimum of 5 years’ operating experience in all related trade disciplines. Thorough knowledge of modern weight handling theories, principals, methods, and procedures as they apply to mobile, bridge, overhead, jib, monorail, and commercial truck mounted cranes and associated rigging gear. Ability to collect, prepare, create, and write training materials for presentations. Experience in utilizing various instructional methods. Ability to evaluate the effectiveness of the training programs and determine the needs of the shops to be incorporated into future lesson plans and training programs. Good oral and written communication skills and the ability to comfortably make presentations in front of diverse audiences. General knowledge of computer hardware and software applications. sufficient to successfully maintain training and licensing records of those trained and to communicate with clients, students, and upper management. Conducts an organized training program in the following areas: New equipment and techniques, safety procedures, mandated initial 40-hour crane operator safety training for new crane operators, equipment maintenance training, and crane and equipment operator refresher instruction in state-of-the-industry techniques. Conducts training within formal, organized programs for Selection, Training, Testing, Qualifying and Licensing Operators of Construction and Material Handling Equipment. In addition, may be required to perform training in accordance with manufacturer's recommendations, Department of Transportation (DOT), Occupational Safety and Health Agency (OSHA), and locally established policies and requirements. Show less
-
-
Heavy Equipment Operator
-
Mar 2007 - Feb 2015
Coordinated machine actions with other activities, positioning or moving loads in response to clear and precise hand or audio signals from crew members. Loaded and moved dirt, rocks, equipment, or other materials, using trucks, crawler tractors, power cranes, shovels, graders, or related equipment. Checked fuel supplies at sites to ensure adequate availability. Drove and maneuvered equipment equipped with blades in successive passes over working areas to remove topsoil, vegetation, or rocks or to distribute and level earth or terrain. Aligned machine, cutter heads, or depth gauge makers with reference stakes and guidelines or ground or position equipment. Operated tractors or bulldozers to perform such tasks as clearing land, mixing sludge, trimming backfills, or building roadways or parking lots. Repaired and maintained equipment, making emergency adjustments or assisting with major repairs as necessary. Operated equipment to demolish or remove debris or to remove snow from streets, roads, or parking lots. Operated loaders to pull out stumps, rip asphalt or concrete, rough-grade properties, bury refuse, or perform general cleanup. Selected and fastened bulldozer blades or other attachments to tractors, using hitches. Pushed or pulled other equipment when extra traction or assistance is required. Spoke to clients and studied instructions, plans, or diagrams to establish work requirements. . Experience in Crane set up and safe operations. Efficient in heavy equipment hand and arm signals for a variety of different types of heavy equipment. Proficiently understands Load Charts and diagrams. Consult technical documents and manuals (e.g., manufacturer's manuals, technical publications) to verify heavy mobile equipment maintenance and repairs are completed correctly. Carry out pre-repair inspection on complete combat vehicles, tactical vehicles, components, assemblies, and systems to determine economic reparability and depth of repair. Show less
-
-
Records Management Specialist
-
Mar 2007 - Feb 2015
Knowledge of quantitative and qualitative management analysis techniques and procedures as it pertains to the overall departmental records management program.Knowledge of records management laws, regulations, rules, policies and procedures, principles and concepts of information governance of various phases of Records and Information Management (RIM), and the complete records process and content management framework that supports the entire life cycle of agency records.Knowledge of statutory, regulatory and other legal requirements associated with information resources management, records management, privacy, access, copyright and patent, admissibility of documentary evidence, and ethical and professional conduct.Knowledge of important management processes involved in the life cycle of records including forms analysis and design; information systems design; reports and directives management; correspondence and mail management; filing and retrieval systems, both automated and manual; records schedules; records appraisal; archival management; and retirement and transfer procedures. Knowledge of planning, scheduling, and conducting projects and studies to evaluate and recommend ways to improve the effectiveness and efficiency of work operations for the Records Management Program. Knowledge of Federal/Army regulations and laws governing Forms Management, Publications, The Privacy Act, USMC Correspondence, and Printing and Publications. Skill providing policy and governance on the use of records management tools to ensure best practices and agency compliance with Federal statutes. Skill performing a wide variety of tasks such as input, store, and retrieve data in multiple formats from various IT Systems and use those systems to access files, initiate and track projects, analyze data, and generate reports. Ability to interpret and apply FOIA/Privacy Act laws, regulations, policies, and guidance to provide access to Federal agency records and information. Show less
-
-
Safety Specialist
-
Mar 2007 - Feb 2015
Conduct quarterly safety council meetings and advise senior leadership on safety matters. Provide risk management training and maintain an accurate automated system to track records. Managed and accounted for personal protective equipment, rules and directives, and personal protective tactics, techniques, and procedures were ordered, followed, and enforced mitigating risk to personnel and reducing government liability and overall cost in accordance with the safety program. Conducted safety and occupational health surveys at a military installation, recommended measures to eliminate or control hazardous practices and conditions which may cause mishaps; prepared supplemental written safety procedures for application to local organizational components. Planned and scheduled periodic surveys of assigned installation facilities. Tracked periodic inspections through database application and performs analysis of inspection data. Conducted and practiced in opening and closing conferences with managers, supervisors and employee safety representatives to explain; the purpose and scope of pertinent safety and occupational health regulations; the hazards observed or cited; and the legal responsibilities for providing occupationally safe work sites. Inspected worksites, environmental conditions, machine, and equipment operations, protective devices and equipment, work practices, and safety procedures. Recorded and photographed apparent violation of standards for use as evidence of existing hazards. Advised managers, supervisors and, employee safety representatives of appropriate safety and occupational health measures to control or eliminate hazardous operating processes of environmental conditions. Initiated and carried out safety education activities promoting safety awareness through safety seminars, training courses, and participated in preparing brochures and newsletters, explaining safety procedures and practices. Show less
-
-
-
Sunburst
-
United States
-
Leisure, Travel & Tourism
-
1 - 100 Employee
-
Snowboard Instructor
-
Dec 2004 - Aug 2007
-
-
-
Jeff Lambie Bussiness Interiors
-
West Bend, Wisconsin
-
Installation Technician
-
Aug 2006 - Mar 2007
Experince in instalaiton of all types of floor coverings including carpet, carpet tiles, ceramic tile, vinyl, VCT, wood, laminate and more. Moving and reconfiguration of office interiors. Experince in instalaiton of all types of floor coverings including carpet, carpet tiles, ceramic tile, vinyl, VCT, wood, laminate and more. Moving and reconfiguration of office interiors.
-
-
-
Christenson landscaping
-
Kewaskum, Wisconsin
-
Crew Lead
-
Aug 2005 - Aug 2006
Built retaining walls and custom stone patios Built retaining walls and custom stone patios
-
-
Education
-
American Military University
Bachelor of Science (B.S.), Environmental Science conentration in fish and wildlife management -
Rochester Community and Technical College
Environmental Science
Community
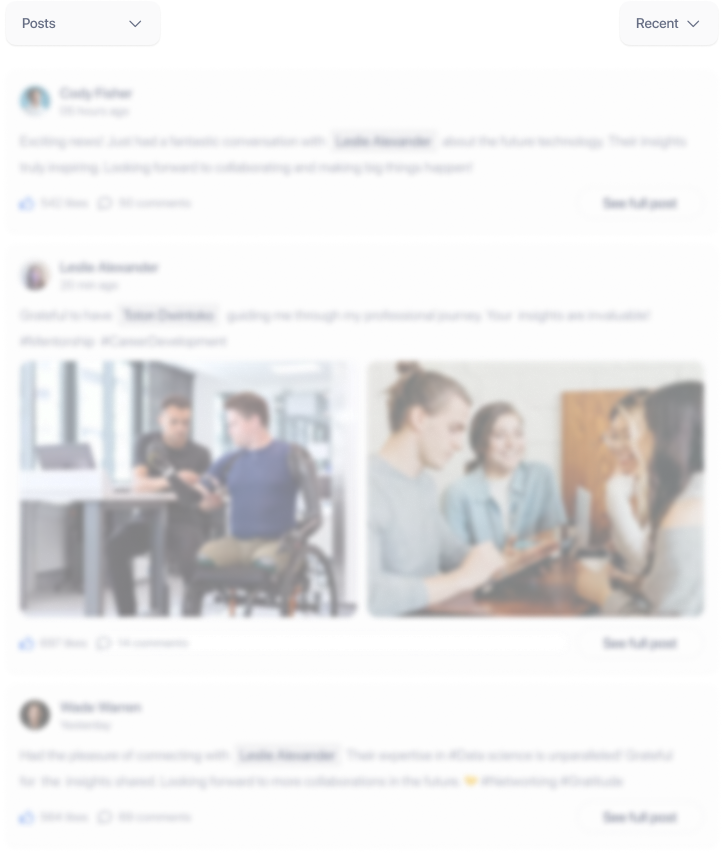