Parth Gandhi
Process Metallurgist/ AOD (Argon-Oxygen-Decarburization) Technical Supervisor at Valbruna ASW- Claim this Profile
Click to upgrade to our gold package
for the full feature experience.
-
English Native or bilingual proficiency
-
Gujarati Native or bilingual proficiency
-
Hindi Elementary proficiency
Topline Score
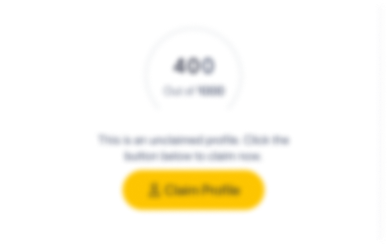
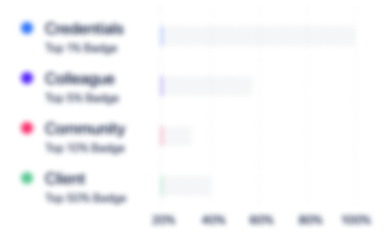
Bio


Credentials
-
Training in Liquid Penetration Testing Level 2
Durham CollegeDec, 2019- Oct, 2024 -
Training in Ultrasonic Testing Level 1
Durham CollegeDec, 2019- Oct, 2024 -
Training in introduction to Non-Destructive Testing
Durham CollegeDec, 2019- Oct, 2024 -
Internship Certificate
LAXCON STEELS LIMITEDJun, 2015- Oct, 2024
Experience
-
Valbruna ASW
-
Canada
-
Industrial Machinery Manufacturing
-
1 - 100 Employee
-
Process Metallurgist/ AOD (Argon-Oxygen-Decarburization) Technical Supervisor
-
Nov 2020 - Present
Key Responsibilities in EAF, AOD & LRF includes:-Scrap charge design, minimizing delays & decreasing tap-to-tap time in order to meet Caster sequence & quality standards.-Process optimization & cost reduction of ferro alloys (Ni, Cr, Mo, Ti, Al, Mn, Si) by achieving maximum recoveries.-Slag making & slag designing with respect to Resulphurized & Desulphurized SS grades which in terms enhance Vessel life & decrease $$/lbs of refractory cost.-Training Operators, Melting Supervisors & new hires quarterly & annually on Melting procedures & process manipulation in critical heats.-Yield & Recovery Analysis of ferro alloys.-Leading various improvement projects such as minimizing VORS/ LRF/ AOD additions & prioritizing more usage of chilled scrap in AOD; minimize Ar consumption; enhancing ingot quality surface etc.-Addressing issues of Quality department by reviewing heats & melting procedure in order to sort out major/ minor defects before ESR/ VAR or Rolling/ Forging.-Complete metallurgical solutions regarding any miscellaneous problems regarding Melt Shop Operations (EAF, AOD, CCM, BP) Show less
-
-
EAF/ AOD Helper
-
Nov 2020 - Nov 2020
Key responsibilities as a Melt shop helper includes working in & as a part of union on melt floor to identify melting dissimilarities & reporting to Melting Supervisor & following Operators & Seniors members of the union.
-
-
-
Canadian Specialty Castings
-
Canada
-
Mechanical Or Industrial Engineering
-
1 - 100 Employee
-
Production Technician
-
Jul 2020 - Nov 2020
Key Responsibilities includes: -Scheduling & Planning of Heats. -Determining Melting procedure for Carbon steel, Stainless steel, Cast iron, Aluminum alloys, Copper alloys, Zinc alloys, Nickel alloys for Induction furnace. -Assisted to repair refractory of furnace frequently. -Accomplished Spectro-Analysis by Spectrometer as well as sample preparation techniques prior to analysis. -Statistical heat calculations for heat making. -Scrap design prior to melting. -Verifying surface quality of casting as well as Visual & Dimensional analysis & Report writing regarding final shipped product. -Verifying temperature of green sand molds before pouring operation. -Addressing quality meetings & resolving problems of melt shop. -Assisted in NDT mainly Magnetic Particle Inspection, Dye Penetrant test & Ultrasonic test on castings periodically. Show less
-
-
-
Calstone
-
Canada
-
Manufacturing
-
1 - 100 Employee
-
Production MIG Welder
-
May 2020 - Jun 2020
Key responsibilities accomplished during my contract were: -Metal Joining (MIG Welding) to join small to intermediate size parts prior to assembly in furniture manufacturing. -Metal Cutting with Oxy-Acetylene torch & Plasma torch. -Metal Grinding with wheel grinders, wires & fine grinding disc. -Stamping operations. -Assisted in lifting objects & guided forklift operators for smooth operations. -Followed senior welders & learned new welding techniques from them. -Setting up welding machines on frequent basis. -Operated a manual machine press. Show less
-
-
-
Cleaver-Brooks
-
United States
-
Industrial Machinery Manufacturing
-
400 - 500 Employee
-
Welding intern
-
Jan 2019 - Mar 2019
During internship organized by Fanshawe college, St. Thomas got an opportunity to learn & get hands on different types of welding such as TIG, MIG & Stick. Apart from this, was totally exposed to entire Boiler making process right from start & X-Ray testing at the end. Also went through their internal training sessions in order to pass TSSA test after trials. During internship organized by Fanshawe college, St. Thomas got an opportunity to learn & get hands on different types of welding such as TIG, MIG & Stick. Apart from this, was totally exposed to entire Boiler making process right from start & X-Ray testing at the end. Also went through their internal training sessions in order to pass TSSA test after trials.
-
-
-
Laxcon Steels Limited
-
Mining
-
Process Metallurgist/ Process Control Engineer/ AOD (Argon-Oxygen-Decarburization) Operator
-
Jun 2016 - Jul 2018
Key Responsibilities undergone were: -Melting procedure design for Austenitic, Martensitic, Ferritic, Duplex & Precipitation Hardened grades & review processes for IF, AOD, LRF & Cored Wire Injections. -Scrap design & Heat making. -Data collection, documentation & recovery analysis. -Refractory design & improvise vessel life. -Slag making & design with respect to grades & temperature as well as vessel life. -Maintaining sequence between IF, AOD & Caster/ Bottom pour to get maximum productivity. -Report writing regarding any off analyzed heat & addressing the concerns pertaining the same. -Periodic presence during calibrations of Valve train of AOD. -Maintaining a close eye on tapping temperatures, additions, superheats & casting temperatures, primary & secondary water flow in caster, EMS (Electro Magnetic Stirrer) frequency etc. for good quality billets/ ingots. -Designing ratio of flow rates of O2, N2 & Ar in AOD process with respect to various grades. -Analyzing tank pressures on consistent basis for smooth operating conditions. -Ensured all workers are operating safely by wearing proper PPE. -Assisted by training new hires & always coordinated with Furnace Melter, Scrap yard Supervisor, CCM Supervisor, Store Manager, Lab-in-charge, Crane drivers & workers in order to maintain sequential balance of heats to prevent unwanted delays/ breakdowns & achieve production targets. -Cored Wire Injections (Ti, Al, CaSi, C, Si, S) to generate micro-inclusions in steel. Show less
-
-
-
-
Metallurgical Engineering Intern- QA (Quality Assurance)
-
Jun 2015 - Jul 2015
During this second semester break, I was asked to learn regarding Metal working process such as Rolling & Reheating furnace for billets, Heat treatment such as Annealing, Normalizing, Hardening & Tempering of various grades & their respective cycles as well as I got an exposure to Ultimate Tensile tester, Impact tester, Rockwell & Brinell Hardness tester & Bar straightening operations. During this second semester break, I was asked to learn regarding Metal working process such as Rolling & Reheating furnace for billets, Heat treatment such as Annealing, Normalizing, Hardening & Tempering of various grades & their respective cycles as well as I got an exposure to Ultimate Tensile tester, Impact tester, Rockwell & Brinell Hardness tester & Bar straightening operations.
-
-
-
-
Metallurgical Engineering Intern- SMS (Steel Melting Shop)
-
Jun 2014 - Jul 2014
During my first internship entering into a Steel mill for the very first time, I had an opportunity to visualize Induction furnace, AOD Converter, CCM, Ingot pouring & Scrap grading operations in SMS. During my first internship entering into a Steel mill for the very first time, I had an opportunity to visualize Induction furnace, AOD Converter, CCM, Ingot pouring & Scrap grading operations in SMS.
-
-
Education
-
Durham College
Mechanical NDE -
Fanshawe College
Skilled Trades Certificate, Welding Techniques -
Government Engineering College, Nr GEB Cross Road, Sector-28, Gandhinagar- 382028.
B.E Metallurgical Engineering, Physical Metallurgy, Foundry Technology, Manufacturing Processes, Material Testing, Heat Treatments -
Best High/Higher Secondary School.
H.S.C & S.S.C
Community
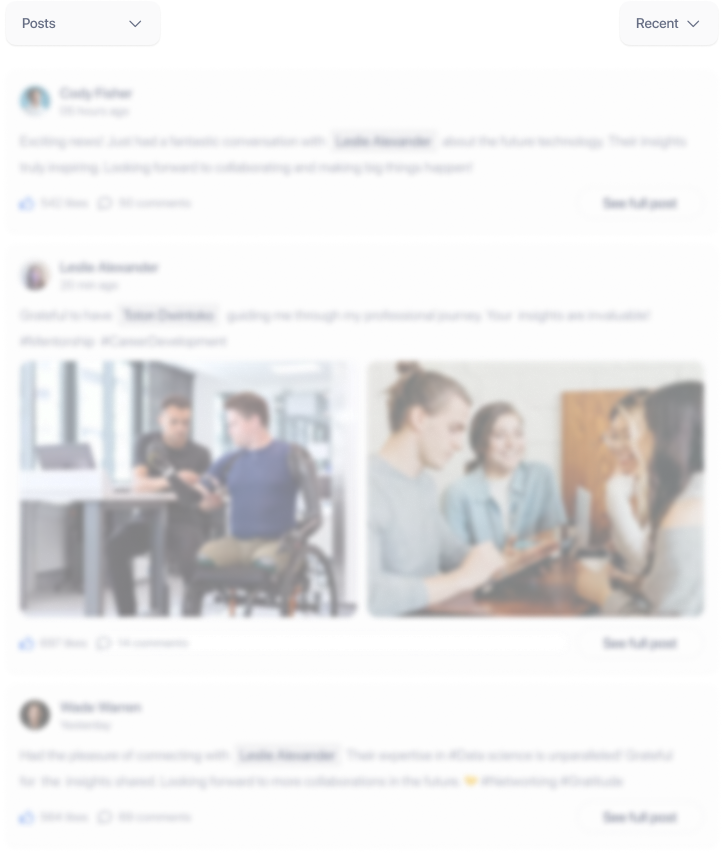