Paramesh Reddy
Process Engineer at Saeplast- Claim this Profile
Click to upgrade to our gold package
for the full feature experience.
-
English Full professional proficiency
-
Hindi Full professional proficiency
-
Kannada Full professional proficiency
-
Telugu Full professional proficiency
-
Marathi Elementary proficiency
Topline Score
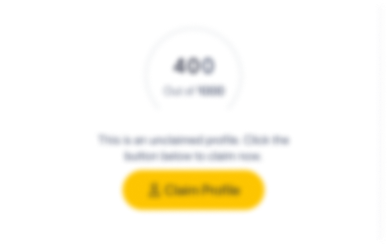
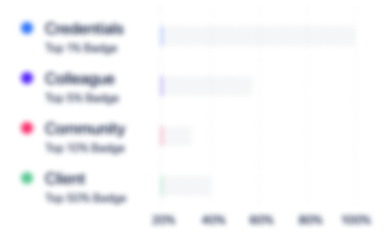
Bio

Justin Sweeney
Para completed a robust market analysis project for us. His workmanship, ability to integrate within the team, and commitment to satisfying the needs of the project were top notch. Para was very resourceful in acquiring usable data sets and completing an analysis that created actionable recommendations. I would happily include him on any of my teams.

SAMISH THAKUR
He is a good leader and worked with me during the period 2008-2011.He has good experience in manufacturing excellence .

Justin Sweeney
Para completed a robust market analysis project for us. His workmanship, ability to integrate within the team, and commitment to satisfying the needs of the project were top notch. Para was very resourceful in acquiring usable data sets and completing an analysis that created actionable recommendations. I would happily include him on any of my teams.

SAMISH THAKUR
He is a good leader and worked with me during the period 2008-2011.He has good experience in manufacturing excellence .

Justin Sweeney
Para completed a robust market analysis project for us. His workmanship, ability to integrate within the team, and commitment to satisfying the needs of the project were top notch. Para was very resourceful in acquiring usable data sets and completing an analysis that created actionable recommendations. I would happily include him on any of my teams.

SAMISH THAKUR
He is a good leader and worked with me during the period 2008-2011.He has good experience in manufacturing excellence .

Justin Sweeney
Para completed a robust market analysis project for us. His workmanship, ability to integrate within the team, and commitment to satisfying the needs of the project were top notch. Para was very resourceful in acquiring usable data sets and completing an analysis that created actionable recommendations. I would happily include him on any of my teams.

SAMISH THAKUR
He is a good leader and worked with me during the period 2008-2011.He has good experience in manufacturing excellence .

Credentials
-
Becoming a Psychologically Safe Leader
University of New BrunswickJul, 2023- Oct, 2024 -
Promoting a Psychologically Safe Workplace
University of New BrunswickJul, 2023- Oct, 2024 -
Psychologically Safe Workplaces
University of New BrunswickJul, 2023- Oct, 2024 -
Internal Auditor ISO TS 16949 / 2002
Krit Quality and Safety ServicesAug, 2008- Oct, 2024
Experience
-
Saeplast
-
Iceland
-
Packaging and Containers Manufacturing
-
1 - 100 Employee
-
Process Engineer
-
Jan 2020 - Present
Insulated Container Manufacturing through Rotomolding Process Insulated Container Manufacturing through Rotomolding Process
-
-
-
Nordia Inc.
-
Canada
-
Consumer Services
-
700 & Above Employee
-
Customer Service Representative
-
Nov 2019 - Dec 2019
-
-
-
University of New Brunswick
-
Canada
-
Higher Education
-
700 & Above Employee
-
MBA Graduate
-
Oct 2018 - Oct 2019
Developed business plans, strategic plans, and project reports; conducted market research and financial analysis; analyzed various case studies; and presentations. Developed business plans, strategic plans, and project reports; conducted market research and financial analysis; analyzed various case studies; and presentations.
-
-
-
Saint John Community Loan Fund
-
Canada
-
Civic and Social Organizations
-
1 - 100 Employee
-
MBA Intern
-
May 2019 - Jul 2019
Worked on Small Business succession project, conducted market research for quantifying the business succession opportunities, identified and built relationships with succession facilitators including bankers, brokers, commercial lawyers, and accountants, and provided the hypothesis of future demand for business succession. Worked on Small Business succession project, conducted market research for quantifying the business succession opportunities, identified and built relationships with succession facilitators including bankers, brokers, commercial lawyers, and accountants, and provided the hypothesis of future demand for business succession.
-
-
-
JBM Group
-
India
-
Motor Vehicle Manufacturing
-
700 & Above Employee
-
Supplier Quality Assurance Manager
-
Jan 2018 - Sep 2018
• Led the SQA team for developing new vendors and parts for three new city-bus projects • Developed Quality Systems at small vendors of the automotive industry • Developed quality inspection plans for each part based on drawings and specification sheet • Led the SQA team for developing new vendors and parts for three new city-bus projects • Developed Quality Systems at small vendors of the automotive industry • Developed quality inspection plans for each part based on drawings and specification sheet
-
-
-
BITANA BUSINESS MANAGEMENT
-
India
-
Appliances, Electrical, and Electronics Manufacturing
-
1 - 100 Employee
-
Senior Business Consultant
-
Mar 2017 - Dec 2017
• Developed Quality systems at tier 2 & 3 vendors, conducted audits, and approved PPAP. • Provided Strategic consultancy to improve plant performance through Lean manufacturing, TQM practices, 5S, and Visual Management practices. • Facilitated third-party inspection services for Incoming, Process and Final Inspection activities • Developed Quality systems at tier 2 & 3 vendors, conducted audits, and approved PPAP. • Provided Strategic consultancy to improve plant performance through Lean manufacturing, TQM practices, 5S, and Visual Management practices. • Facilitated third-party inspection services for Incoming, Process and Final Inspection activities
-
-
-
Ashok Leyland
-
India
-
Motor Vehicle Manufacturing
-
700 & Above Employee
-
Manager - Supplier Quality
-
Jun 2016 - Mar 2017
• Ensured adherence of Quality Systems and documentation by the vendors through audits and performance motoring• Monitored and resolved field issues related to parts supplied by vendors• Monitored and controlled DPV (Defect Per Vehicle) from vendors • Implemented design change of parts and updated quality documents accordingly • Verified PPAP documents (production part approval process) at vendors• Conducted root cause analysis and implemented action plans for reducing PPM• Audited critical processes such as welding, painting, and pre-treatment• Conducted periodic certification of operators related to critical operations Show less
-
-
Manager, Material department
-
Mar 2012 - Jun 2016
• Managed the material requirement planning at engine and gearbox assembly lines• Managed the logistics activities and material flow at engine and gearbox assembly lines• Received monthly production plan from the corporate office, broken-down it to weekly level, and planned production sequence for the next three days production. • Prepared shortage list for the next three days production requirement and tracked materials availability accordingly by continuous follow-up with the purchase team. • Daily reporting of inventory, shortage parts, excess inventory parts, and stock of A-class items with variance details. • Coordinated with MPS (Master Production scheduler), PPC (Production Planning and Control), MRP (Material Resource Planning), production, procurement, quality, finance, and internal audit teams for day to day activities. • Monitored plan vs actual production schedule, SLA (service level agreement), and gaps if any• Led daily production meeting for materials requirement, planning, and sequencing• Controlled inventory through ABC analysis and defined min-max• Corrected bill of material (BOM) and material master of parts in SAP• Used SAP for all transactions and material queries (MM Module)• Conducted periodic perpetual inventory, input-out reconciliation, and stock accuracy Show less
-
-
Core Team Member - Functional Excellence - Mission Gemba
-
Jan 2011 - Mar 2012
• Transformed operations through the implementation of lean manufacturing techniques including 5S, VMI, eliminate waste and cost management.• Led the company in winning a gold award at national level in 5S (best housekeeping) competitionhttp://www.ashokleyland.com/
-
-
Deputy Manager - Manufacturing Quality Assurance
-
May 2008 - Jan 2011
• Ensured critical processes, CTQ stations, and manufacturing activities are adhering to standard operating procedures (SOP). • Facilitated updated quality information such as model & part matrix, SOP, work instructions, engineering sketch, one-point lesson, do’s & don’ts• Developed and implemented inspection sheets (self-certified history cards) on manufacturing assembly lines, layout inspection sheets for products, and customer specifications audit sheets. • Solved quality issues by using Kaizen, quality circles, and advanced problem-solving techniques • Reduced ZKM (Zero kilometer) defects and Warranty issues • Monitored and controlled cost of poor quality by reducing line rejections. • Conduct product quality reviews (PQR) and management reviews (MR)• Resolved customer and field-related issues through cross-functional team approach (CFT)• On-job training to production and quality team• Corrected bill of material (BOM) and material master of parts in SAP Show less
-
-
-
-
Seniore Officer - Manufacturing Quality Assurance
-
Feb 2007 - May 2008
Process Quality Assurance Engineer @ Bus body division Body shop & Final Trim Assembly line of Low Floor buses Analysis of Customer Complaints, field complaints, Service/marketing feedback Analysis of Incoming Material defects, Process related issues, Final Inspection/PDI feedback, Travel card, Layout Inspection, Preparing Inspection reports, Audit reports Control/reduce Demerit rating of the vehicle Implement & initiate Design Modifications (DCR) Process Effectiveness rated of Pre-treatment, Welding, Sealant application, Painting processes Conducted periodical Welders certification Show less
-
-
-
Tata Motors
-
India
-
Motor Vehicle Manufacturing
-
700 & Above Employee
-
Supplier Quality Engineer
-
Jul 2004 - Feb 2007
Deputed at vendor HMM coaches Ltd, who is a bus coach manufacturer, as a Quality Engineer 1. Provided quality clearance to fully built buses and passed them to the sales division 2. Monitored and reduced defects per vehicle 3. Analyzed customer complaints, field issues, and feedback received from the sales and service department 4. Suggested and implemented design modifications in parts and the final product 5. Rated critical processes including welding, painting, and pre-treatment for effectiveness 6. Played the role of a team member for projects included TATA CNG & Diesel Tarmac Coaches for AUTO EXPO, Jan’06 Show less
-
-
Education
-
University of New Brunswick
Master of Business Administration - MBA -
Visvesvaraya Technological University
Bachelor of Engineering - BE, Mechanical Engineering -
SES Polytechnic, Siriguppa
Diploma in Mechanical, Mechanical Engineering
Community
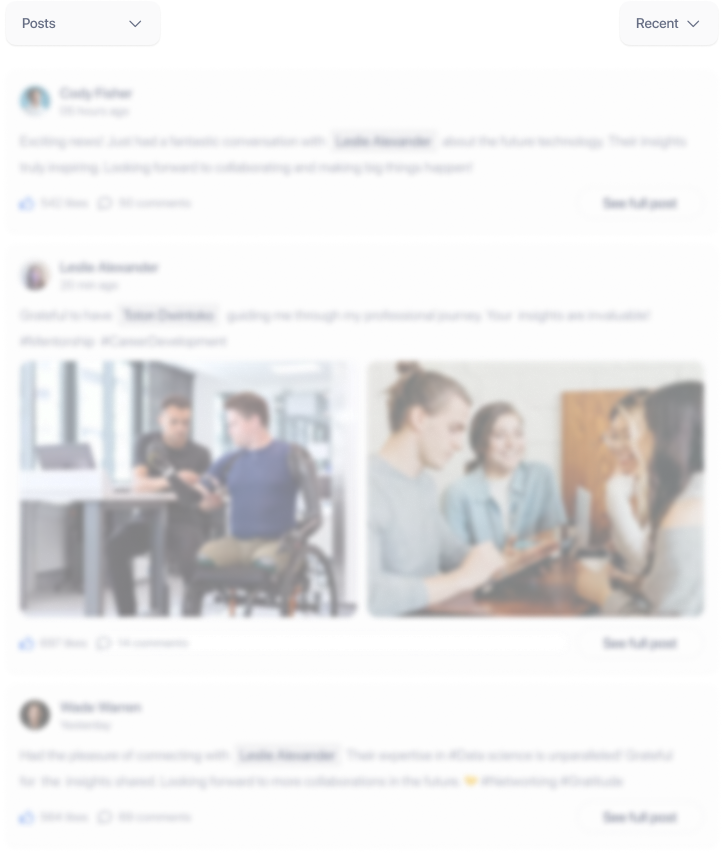