Ovidiu Mazilu
Transformation Manager at Fresco Expert - professional kitchen, commercial refrigeration, coffee systems & laundry solutions- Claim this Profile
Click to upgrade to our gold package
for the full feature experience.
-
English Full professional proficiency
-
French Professional working proficiency
-
Italian Professional working proficiency
-
German Elementary proficiency
Topline Score
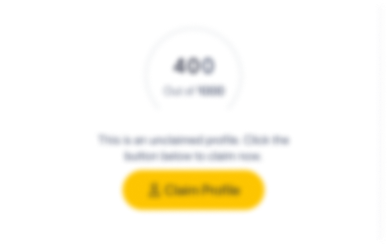
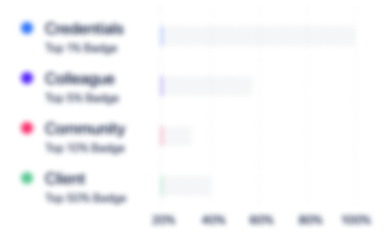
Bio


Credentials
-
Design for Six Sigma
- -
Lean Green Belt
- -
Six Sigma Black Belt
-
Experience
-
Fresco Expert - professional kitchen, commercial refrigeration, coffee systems & laundry solutions
-
Romania
-
Business Consulting and Services
-
1 - 100 Employee
-
Transformation Manager
-
May 2023 - Present
-
-
-
Mainfreight
-
New Zealand
-
Transportation, Logistics, Supply Chain and Storage
-
700 & Above Employee
-
Branch Manager
-
Aug 2021 - Dec 2022
Led Transportation Branch of Mainfreight Romania, with a team of 130+ members, supervising the operations for a 15+ M EUR customers portfolio Led Transportation Branch of Mainfreight Romania, with a team of 130+ members, supervising the operations for a 15+ M EUR customers portfolio
-
-
-
IVECO DEFENCE VEHICLES
-
Italy
-
Defense & Space
-
300 - 400 Employee
-
Program Manager - IDV Romania Ramp-up
-
Sep 2020 - Aug 2021
Managed the full ramp-up of IVECO DEFENCE VEHICLES (IDV) program in Romania, coordinating a cross-functional team of industrial partners across the country, IDV stakeholders at local level and Group level, in relation with the Romanian Ministry of Defence (MoD) as direct customer. Industrialized the production of military vehicles within local partners, coordinated capacities ramp-up, secured MoD approvals and kick-ed off deliveries for 10 vehicle types across the Romanian armed forces. Managed the full ramp-up of IVECO DEFENCE VEHICLES (IDV) program in Romania, coordinating a cross-functional team of industrial partners across the country, IDV stakeholders at local level and Group level, in relation with the Romanian Ministry of Defence (MoD) as direct customer. Industrialized the production of military vehicles within local partners, coordinated capacities ramp-up, secured MoD approvals and kick-ed off deliveries for 10 vehicle types across the Romanian armed forces.
-
-
-
Honeywell
-
United States
-
Appliances, Electrical, and Electronics Manufacturing
-
700 & Above Employee
-
Plant Manager
-
Nov 2016 - Jun 2019
Led the largest manufacturing site of Garrett worldwide, with a team of 800+ employees and serving 25 automotive OEM brands with shipments to 70+ customer locations globally. Directed all operations with P&L responsibility on manufacturing and related functions including HS&E, Quality, Manufacturing Engineering, Logistics and Production Planning, Equipment Maintenance, Facilities, New Product Launch and Factory Digitization. Established operating budget, developed and executed plant capital projects to sustain SQDCI results. • Championed plant Safety Programs. Maintained OSHAS and ISO Standards (14001, 18001, 50001); championed transformational projects to address HSE risks. Achieved Best Safety Award 2018 within Garrett for zero accidents and best TCIR • Improved customer PPM and Quality VOC; main achievements - Audi PPM reduction by 70%, RSA incidents rating down to 0 from 50; maintained Gold level within Supplier Quality Excellence by Caterpillar; maintained overall PPM below 20; Garrett Bucharest awarded as 2018 Most Improved Plant on Zero Defect Mindset • Successfully transitioned the plant from ISO TS to IATF 16949 standard • Maintained on time delivery at 98% and integrated Net Promoter Score metric with all customers • Launched 40+ new products with customer PPAP and SOP; Integrated 3 additional production lines • Increased direct labor productivity by 4%; championed the integration of 8 collaborative robots in production area; • Kicked-off the mid-term Automation project – supervised the introduction of 8 Cobots on the production lines • Participated at Union/ Employees Rep’s negotiations; supported to improve and maintain positive LER and social dialogue at all levels (directs, indirects, staff population). Championed plant HR strategy and initiatives. • Achieved Best Kaizen Award 2018 within Garrett for continuous improvement best practices. • Championed Factory Digitization projects with $200K+ saving in 2018 Show less
-
-
Global ISC Transitions Strategy Leader
-
Oct 2013 - Oct 2016
Developed Global Transition Business Cases and coordinated the approval process. Coordinated strategic projects planning and execution (transitioning of processes and products across Honeywell WW footprint and across key suppliers) within the operational strategies, at Global level • Coordinated the business cases and managed approval of 5 strategic projects at Integrated Supply Chain (ISC) Headquarters level – Downsizing & Repositioning, Core processes transitions upon manufacturing footprint analysis (make-to-make), Core volumes insourcing (buy-to-make) • Lead the projects’ planning and execution at global ISC level, with cross functional (HSE, Quality, Manufacturing, Engineering, SC, Legal, LER, HR, GR, Finance) and cross cultural teams (Europe, Americas, Asia) • Ensured projects adherence to the operations strategy through Standard Transitions Process (STP), aligned timing plans and crisp execution • Defined mid-long term manufacturing footprint strategies, as part of the annual STRAP (STRategic Action Plan) exercise at ISC Headquarters level • Delivered quarterly STP training in the regions (Shanghai, Glasgow, Birmingham) as key facilitator within Global Transitions Team. Show less
-
-
New Product Introduction Manager
-
Feb 2010 - Sep 2013
Secured flawless launches of new products in the manufacturing plant by managing the NPI process with a team of 9 engineers over a portfolio of 15+ customers • Developed the team and put in place the cross functional process for new product launching • Developed all the process related procedures, MOS and communication flows internally and with regional functions • Supervised the launch of 36 new turbocharger applications from initial batches to PPAP/ Customer Approval and SOP in mass production • Contributed to the increase of plant customers’ portfolio by 4 additional (Ford, Honda, Toyota, MTU) • Reduced the NPI process cost YOY in line with the financial productivity targets – $0. 3M yearly avg. Show less
-
-
ProtoShop Manager
-
Dec 2009 - Dec 2011
Planned and executed the start-up of the Proto Shop within Bucharest manufacturing site. Managed the proto activities (within the first 18 months after SOP) from Annual Operating Plan to daily manufacturing and shipment, through monthly P&L reporting. • Recruited and developed the proto organization - 9 staff (manufacturing, logistics, purchasing, customer management) and 7 top-skilled technicians • Designed and implemented the end-to-end processes from Customer Order to Purchasing, Manufacturing and Shipping • Coordinated the layout and process-flow design, shop-floor equipments transfer and installation, customers’ approvals and readiness for SOP - started production within the 1’st month of Photoshop readiness • Increased the production output by 40% within the first year of operations • Improved the customer PPM level to 1 digit after SOP • Improved the OTTR delivery performance by 14% in 2011 • Implemented Honeywell Operating System processes, tools and standards to sustain growth and results Show less
-
-
Production Manager
-
Sep 2005 - Nov 2009
Led a team of 350 directs, 36 technicians and 4 staff including general supervisors, process quality engineers and product launch functions. • Achieved Customer View PPM reduction to double digit level in 2006 | stable 98% On Time to Request delivery performance by means of sustained MPS adherence | increased direct productivity by 7% in average YOY; • Initiated the “24/7 Safety Behavior” program deployment on the shop floor; • Developed the internal production planning process to support the increased complexity and efficiently allocate the manpower; • Demonstrated robust manufacturing processes leading to the VW Class A certification as per VDA Quality standard, granted in 2008. • Championed 4 Green Belt and 2 Lean Green Belt projects with direct impact on conversion cost and internal PPM reduction. • Continuously improved the 5S and Visual Management standards on the shop floor as part of the KAIZEN process; • Facilitated the HOS (Honeywell Operating System) implementation in production as to sustain the plant key metrics defined in the Annual Operating Plan: HS&E, customer PPM, OTTR, direct productivity. • Facilitated the installation and SOP of 6 additional production lines and the growth of customer’s portfolio from 3 to 6 between Q3 2005 and Q2 2008 • Contributed to the ISO TS survey audits and demonstrated consistency in terms of production process control and continuous improvement. Show less
-
-
Senior Project Manager - Site Expansion
-
Nov 2004 - Aug 2005
Coordinated, synchronized and monitored 6 local and regional project teams aimed to achieving Bucharest Plant Growth during 2005 and 2006. • Conducted the program risk assessment with direct involvement of the European SBU Leadership; • Supervised the Plant Readiness project. Reengineered the site layout on Lean principles including warehouse extension, shop floor extension by 20%, offices surface extension by 85%, parking area extension to three times the surface, site security system, waste management area and fire protection system. • Monitored the Outsourcing projects for the non-core processes. Planned and executed the transfer of 4 processes with a total of 42 machines from Honeywell Bucharest to suppliers’ locations. • Completed the Turbocharger Capacities Insourcing project. Planned the hiring and training program for 60 operators, transferred 2 production modules and 16 applications for 4 new customers. Show less
-
-
Six Sigma Manager | Plant Growth Program Manager
-
Apr 2002 - Oct 2004
Planned, coordinated and monitored 4 local project teams aimed to transform the local business from components machining to turbocharger assembling. Successfully met the Program objectives in terms of customer delivery and quality, budget spending and program timelines. • Engineered and upgraded the shop floor and warehouse layout to integrate the new production capacities as part of the Plant Readiness. • Closely monitored the outsourcing of Non-core machining processes. Scheduled and facilitated the transfer of 2 machining processes with a total of 79 machine tools. • Managed the insourcing of the assembling processes and SOP for the Passenger Vehicle and Commercial Vehicle products. • Organized the transfer of 5 production lines into Bucharest site with the first part produced within only 5 weeks after the project kick-off. • Facilitated the ramp-up of production output to 3000+ turbochargers per day (100+ P/N’s PV & CV) in 9 months. • Successfully kicked-off mass Turbocharger production and deliveries in October 2003, with 95%+ delivery performance. • Contributed to the site alignment for the customer approval audit - “Class A” supplier granted by VW (Nov 2003)Managed the plant Six Sigma/ Continuous Improvement (PI) process with a team of 3 PI Engineers and developed the Six Sigma culture within the local organization • Coordinated the Operational Excellence process at site level with direct impact on Cost Savings metric; • Delivered 250+ hours of Six Sigma training for Green Belt candidates and directly mentored 37 Green Belt projects with direct impact on the average increase of 7% productivity YOY; • Led the local teams at the European Quest for Excellence completion within Honeywell. • Coordinated the Annual Operations Planning (AOP) process at site level; consolidated the AOP pack and reviewed the AOP goal deployment for European leadership approval. Show less
-
-
Rotational Engineer (ERP Project Manager/ Application Engineer/ Production Engineer)
-
Jul 1999 - Mar 2002
• Production Engineer - Atessa, Italy (January 2001-May 2001): Coordinated one cross-functional team with the aim of internal PPM improvement - achieved a reduction from 63.000 down to 39.000 in 3 months. • Application Engineer - Skelmersdale, UK (August 2000-Dec. 2000): Part of VOLVO customer team. Engineered and led the early stages of the launch for 3 turbochargers for VOLVO engines. Built and maintained customer relationship on prototyping. Organized and monitored the performance tests on resourced components. • ERP Implementation Project Manager – Bucharest; Master Production Scheduler & SIOP Coordinator – Bucharest(July 1999-July 2000) Show less
-
-
Education
-
University POLITEHNICA of Bucharest
Aerospace, Aeronautical and Astronautical Engineering
Community
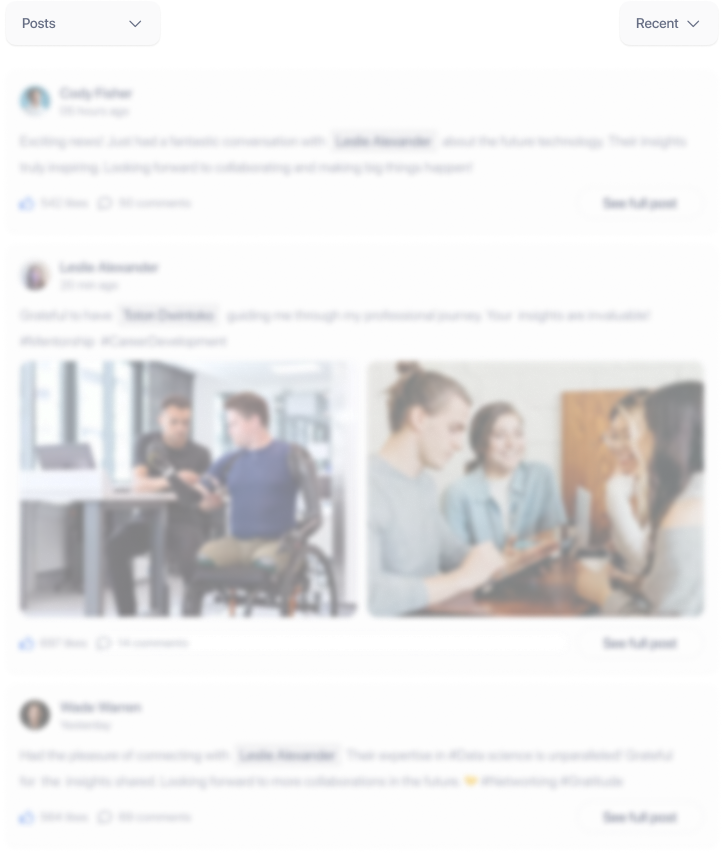