Orlando Mijares
Engineering Fellow, Materials, and Process Engineering at Raytheon Technologies- Claim this Profile
Click to upgrade to our gold package
for the full feature experience.
-
Spanish Native or bilingual proficiency
Topline Score
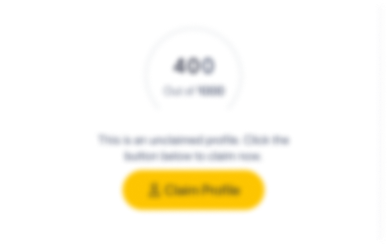
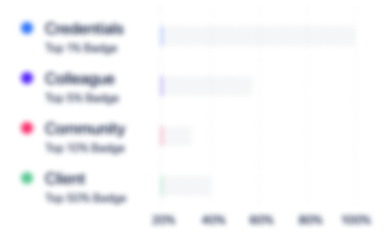
Bio

Joe Rulo
I came to work for Orlando as a Senior Producibility Engineer. Orlando was at once colleague, mentor, director and visionary. Colleague because Orlando had a motivation style that made clear the team goals, directives and missives of the department, while engendering a team environment. Mentor because Orlando loves teaching and developing people. One often got the impression that Orlando may have served very well as an educator at a school of higher learning. Director because Orlando excelled in managing a team of diverse backgrounds, skills and assignments scattered through-out the various facilities of our employer. Visionary because Orlando envisioned a server based database containing a wealth of data designed to serve up virtually anything a design engineer of mechanical parts and systems might require. The proposed system was proclaimed by some in the IT development department to be impossible. Orlando created a small team of individuals to circumnavigate the difficult project. With his guidance and direction, the team was successful. Orlando has certainly contributed toward my own skill, knowledge and experience. I will always be grateful for our shared experience together.

Terrell Holsinger
I found Orlando to be a serious, dedicated Engineer. He is meticulous and interested in getting to the basics of a problem and solving it. Easy to work with - good sense of humor and interested in his work. He is an excellent supervisor/leader for intricate projects and major program management.

Joe Rulo
I came to work for Orlando as a Senior Producibility Engineer. Orlando was at once colleague, mentor, director and visionary. Colleague because Orlando had a motivation style that made clear the team goals, directives and missives of the department, while engendering a team environment. Mentor because Orlando loves teaching and developing people. One often got the impression that Orlando may have served very well as an educator at a school of higher learning. Director because Orlando excelled in managing a team of diverse backgrounds, skills and assignments scattered through-out the various facilities of our employer. Visionary because Orlando envisioned a server based database containing a wealth of data designed to serve up virtually anything a design engineer of mechanical parts and systems might require. The proposed system was proclaimed by some in the IT development department to be impossible. Orlando created a small team of individuals to circumnavigate the difficult project. With his guidance and direction, the team was successful. Orlando has certainly contributed toward my own skill, knowledge and experience. I will always be grateful for our shared experience together.

Terrell Holsinger
I found Orlando to be a serious, dedicated Engineer. He is meticulous and interested in getting to the basics of a problem and solving it. Easy to work with - good sense of humor and interested in his work. He is an excellent supervisor/leader for intricate projects and major program management.

Joe Rulo
I came to work for Orlando as a Senior Producibility Engineer. Orlando was at once colleague, mentor, director and visionary. Colleague because Orlando had a motivation style that made clear the team goals, directives and missives of the department, while engendering a team environment. Mentor because Orlando loves teaching and developing people. One often got the impression that Orlando may have served very well as an educator at a school of higher learning. Director because Orlando excelled in managing a team of diverse backgrounds, skills and assignments scattered through-out the various facilities of our employer. Visionary because Orlando envisioned a server based database containing a wealth of data designed to serve up virtually anything a design engineer of mechanical parts and systems might require. The proposed system was proclaimed by some in the IT development department to be impossible. Orlando created a small team of individuals to circumnavigate the difficult project. With his guidance and direction, the team was successful. Orlando has certainly contributed toward my own skill, knowledge and experience. I will always be grateful for our shared experience together.

Terrell Holsinger
I found Orlando to be a serious, dedicated Engineer. He is meticulous and interested in getting to the basics of a problem and solving it. Easy to work with - good sense of humor and interested in his work. He is an excellent supervisor/leader for intricate projects and major program management.

Joe Rulo
I came to work for Orlando as a Senior Producibility Engineer. Orlando was at once colleague, mentor, director and visionary. Colleague because Orlando had a motivation style that made clear the team goals, directives and missives of the department, while engendering a team environment. Mentor because Orlando loves teaching and developing people. One often got the impression that Orlando may have served very well as an educator at a school of higher learning. Director because Orlando excelled in managing a team of diverse backgrounds, skills and assignments scattered through-out the various facilities of our employer. Visionary because Orlando envisioned a server based database containing a wealth of data designed to serve up virtually anything a design engineer of mechanical parts and systems might require. The proposed system was proclaimed by some in the IT development department to be impossible. Orlando created a small team of individuals to circumnavigate the difficult project. With his guidance and direction, the team was successful. Orlando has certainly contributed toward my own skill, knowledge and experience. I will always be grateful for our shared experience together.

Terrell Holsinger
I found Orlando to be a serious, dedicated Engineer. He is meticulous and interested in getting to the basics of a problem and solving it. Easy to work with - good sense of humor and interested in his work. He is an excellent supervisor/leader for intricate projects and major program management.

Experience
-
Raytheon Technologies
-
United States
-
Aviation and Aerospace Component Manufacturing
-
700 & Above Employee
-
Engineering Fellow, Materials, and Process Engineering
-
Sep 2007 - Present
Concurrent engineering input for new designs. Advanced material selection and qualification. Resolution of material obsolescence issues. Material and process specification preparation and maintenance. Technology roadmap development. Production support of internal and external suppliers. Development and implementation of new, emerging material and process technologies and pursuit and capture of IR&D, CR&D and ManTech programs. Heavily engaged in development of thermoplastic composites. Special assignments as directed by senior management. • Pursued, captured and led $12M combined CR&D/ManTech program. Demonstrated 60% recurring cost savings over legacy part. • Working with a cross-functional team, helped to develop a new manufacturing process for a composite part that was pacing one of our most important programs. Part has now been on schedule for well over 5 years, with yields exceeding 95%. • Staffed composite section with additional subject matter experts. Built bridges to Design, Operations and Supply Chain Organizations. Evolved these relationships into an integrated composites solutions team. Started up and staffed an advanced materials and prototyping lab. • Routinely provide DFMA and SME inputs/peer reviews for our programs. • Helped to develop and implement standard templates for material and process specifications. • Developed a composites technology roadmap and supplier strategy for the division. Provided input to Operations and Engineering Capital Plans. POC for Composites on Airframes Tech Council.
-
-
-
Raytheon Aircraft Company/HawkerBeechcraft
-
Wichita, Kansas Area
-
Technical Manager, Composites Operations
-
Aug 1998 - Aug 2007
Reported to the Director of Operations. Ensured that all existing or new designs incorporating composites or metal-bond technologies could be manufactured in the most cost-effective manner possible. Accountable for Manufacturing Engineering, Industrial Engineering, Facilities Engineering, Capital Equipment, Tooling, and Planning. Main interface with Design Engineering. Promoted from Group Manager, Producibility Engineering to Manager III, Manufacturing Engineering to Sr. Principal Multi-Disciplined Engineer. • Delivered 450 composite and over 1500 metal bond parts every 5 days. • Implemented disciplined and systematic data driven approaches to problem solving, process engineering and documentation (SPC, DOE, R6σ). Double digit improvement results in quality achieved year over year as documented in reductions of MRB actions and in standard cost to repair/rework/scrap per standard hour. • Reduced negative variance from multi-million to break–even. Met or exceed every Technical Operations Goal for the last 5 years there. Participated in or led many Lean, Kaizen or 5S projects. • Organized the composites support operations into effective product teams. Implemented disciplined and systematic data driven approaches to problem solving, process engineering and documentation • Organized the Producibility Engineering Department. Created and communicated vision, mission, roles, responsibilities and expectations. Established product line ownership. • Operations point of contact for Hawker 450. Assisted with business case development and product launch. Led numerous manufacturing trade studies and provided many design inputs. Identified opportunity for RTM empennage that allows a unit one 2000-hour recurring cost reduction. Developed manufacturing strategy, preliminary WBS and MR&D (risk mitigation) plans.
-
-
-
Hunter-Douglas Inc.
-
Broomfield, Colorado
-
Engineering Manager
-
1996 - 1998
Reported to the Business Unit Manager of a privately held, $50+ million, non-union, build-to order, fast-paced, consumer goods manufacturer. Provided guidance and execution for business unit and division special projects including leading a new product launch team, spearheading yield and productivity improvement teams, and factory rearrangement. Promoted from Project Engineer/Project Manager. • Prepared a two-year engineering strategic plan for the business unit. Developed the necessary technology road map and resource allocations (manpower and capital), prioritizing projects in accordance with business unit strategic marketing direction. • Developed and implemented a plan and layout to facilitate cellular manufacturing, employee cross-training and implementation of lean manufacturing concepts. • Formed and led integrated, cross-functional product teams that achieved a 13% increase in yields and 20% increase in productivity, bringing an unwieldy process under control and achieving a 300% increase in process output. • Formulated and executed a detailed program plan for a ’98 new product launch. Detail design, process and equipment development, facilities layout and production implementation were all accomplished on schedule and budget. Program plan template (Integrated Master Plan/Schedule) was adopted as the baseline for new product launches in all North American Divisions.
-
-
-
Stanley Aviation Corporation
-
Greater Denver Area
-
C-17 Ground Support Equipment Program Manager
-
1995 - 1996
Reported directly to the President of a 200 employee, $24 million, non-union, job-shop environment, manufacturing aerospace components and ground support equipment. Directed and managed all aspects of LIII design and manufacturing program. Developed and implemented internal and external strategies to control costs, return program to on-schedule and profitable status, and recover all outstanding debts. Restored company image with customers, delivering quality engineering package and effectively pursuing new business. • Developed and guided combined engineering/operations team, turning losing $20+ million program into major bottom line contributor. Program booked record profits (20%) in 1996. • Directed team that reconciled accounting records and prepared necessary documentation to allow invoicing and collection of over $2.5 million owed. • Team received letters of appreciation from McDonnell Douglas Aerospace and USAF customers for outstanding performance during FCA/PCA and C-17 RM&AE. Rapidly returned production to scheduled delivery performance. • Prepared and submitted proposals generating $2.7 million in 1995 bookings and $250,000 in 1996. • Delivered to customer, on schedule and within budget, complete LIII Drawing and Engineering Documentation Package consisting of 3,000 drawings and numerous lists and engineering test and analysis reports.
-
-
-
Stanley Aviation
-
Greater Denver Area
-
Manager of Manufacturing Engineering
-
1993 - 1995
Led manufacturing engineering department consisting of one Supervisor, Engineers, N/C Programmers, and shop personnel. Planned, organized, and coordinated all manufacturing engineering, industrial engineering, production planning, N/C programming, tool design, and tool crib activities. Developed and monitored performance metrics to insure performance to plan. • Organized and consolidated ME Department along product lines, reducing headcount from 16 to 9 (44%) and cutting 30% from the $450,000 tooling expense budget, without affecting service quality. Established a system of metrics that was later adopted by the design engineering department. • Using elements of lean manufacturing evolved and implemented a distributed manufacturing cell that reduced LANTIRN manufacturing hours 15% and allowed consistent rate production.
-
-
-
BFGoodrich Aerospace
-
Pueblo, Colorado Area
-
Technical Manager
-
1990 - 1993
Reported directly to Plant Manager, managing staff of 2 Section Heads and 12 Engineers. Provided technical oversight and guidance for Manufacturing Engineering and Research and Development Departments in supporting factory production and developing new Carbon-Carbon products for commercial aircraft brakes. Directed all aspects of plant textile, machine shop, and CVD furnace processing. Prepared and presented short and long term strategic plans, capital project requests, facility expansion plans, and cost and producibility analyses for new methods of production. • Developed and implemented new manufacturing methods which reduced annual cost of carbon production 10%, saving $500,000 per year. • Founded and staffed the R&D Department. Brought to market in two years new, a lower cost, and better performing carbon brake material. Trained and developed engineering personnel in statistical problem solving tools and team practices. Mentored three supervisors and two senior engineers. • Helped guide BFGoodrich-Pueblo from startup into production mode. Brought on line 50% increase in production furnace capacity and two new, proprietary textile processes.
-
-
-
Lockheed-Martin/Lockheed Aeronautical Systems
-
Marietta, Georgia
-
Manager, Manufacturing Research, 1988-1990 and Group Engineer, Advanced Materials, 1986-1988
-
1986 - 1990
Managed multi-site staff of up to 239 - Supervisors, Engineers, Technicians and Administrators. Developed new automated processes, cells, and centers. Established and evolved manufacturing technologies necessary to fabricate finished parts and assemblies from advanced materials. Produced one-of-a-kind tools and shop-aids for production. Provided production offload capacity in order to meet critical schedules. Promoted from Group Engineer. • Saved more than $1 million annually by defining, developing, and implementing world-class manufacturing cells and centers, achieving targeted cost reduction. • Developed and implemented an automated cell for installing nutplates on Boeing parts, saving $436,000 in first six months of implementation. Group Engineer, Advanced Materials, 1986-1988 Led staff of 25 responsible for development of equipment, methods of fabrication and tooling for organic (thermoset and thermoplastic) composites, metal matrix composites and conventional aircraft materials. Developed process to fabricate GR/PEEK panels for F-117A vertical tails. Promoted from Specialist.
-
-
-
LTV Aerospace and Defense/Vought Corporation
-
Grand Prairie, Texas
-
Manufacturing Technology Specialist
-
1978 - 1986
Led development of manufacturing technologies and equipment for organic and metal matrix composites and superplastic forming/diffusion bonding of titanium. Developed the country’s first process for welding aluminum metal matrix composites. Applied the welding process in the fabrication of the ATACMS warhead ($12 million Air Force program). Developed and implemented a RIM cell, saving $8 million on MLRS program. Led development of manufacturing technologies and equipment for organic and metal matrix composites and superplastic forming/diffusion bonding of titanium. Developed the country’s first process for welding aluminum metal matrix composites. Applied the welding process in the fabrication of the ATACMS warhead ($12 million Air Force program). Developed and implemented a RIM cell, saving $8 million on MLRS program.
-
-
-
Kaman Aerospace Corporation
-
Bloomfield, Connecticut
-
Associate Materials and Process Engineer
-
1977 - 1978
Developed manufacturing and test methods for advanced composite structures. Assisted in development of manufacturing processes for filament wound and conventionally fabricated organic matrix composite structures, including many versions of helicopter rotor blades and a 150 foot long NASA windmill rotor blade. Developed manufacturing and test methods for advanced composite structures. Assisted in development of manufacturing processes for filament wound and conventionally fabricated organic matrix composite structures, including many versions of helicopter rotor blades and a 150 foot long NASA windmill rotor blade.
-
-
Education
-
Rensselaer Polytechnic Institute
B.S., Materials Engineering -
Colegio Marista
Elementary through High School, Valedictorian
Community
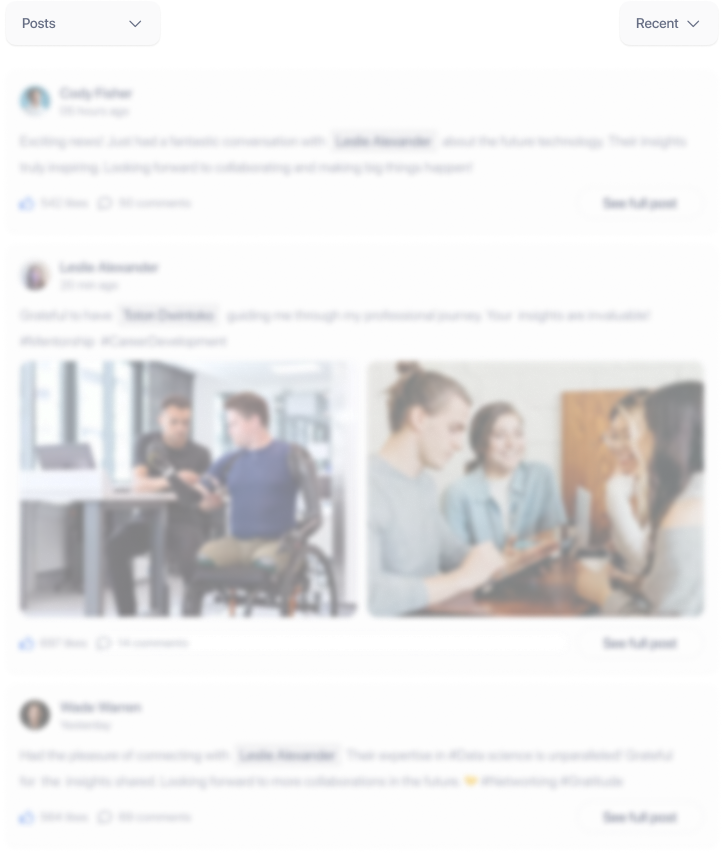