Oluwafemi Bejide
Plant Production Manager at Saint-Gobain Africa- Claim this Profile
Click to upgrade to our gold package
for the full feature experience.
-
English Professional working proficiency
Topline Score
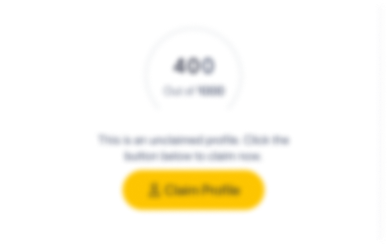
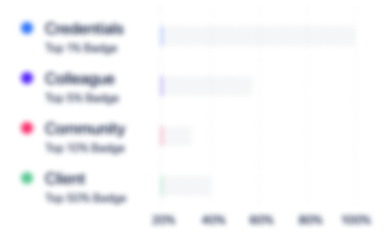
Bio


Credentials
-
Mechatronics Proficiency
Institute for Industrial Technology LagosMar, 2009- Nov, 2024
Experience
-
Saint-Gobain Africa
-
South Africa
-
Building Materials
-
100 - 200 Employee
-
Plant Production Manager
-
May 2023 - Present
The world's top producer of Light and sustainable construction materials. An international brand with more than 350 years of experience in the production of light and sustainable materials that offers cutting-edge solutions for building new structures, making repairs, and renovating existing ones. In my position, I am responsible for Saint-Gobain Weber Nigeria's on-site, cost-efficient, and sustainable manufacturing operations using SAP B1. Monitoring a factory for drying sand and producing cementitious powder. Responsible for safety, projects, logistics, and production. • Set priorities and oversee production processes. • Engaging the supply chain in discussions about production needs • Production scheduling and personnel management for two production plants • Developing and maintaining SOPs and Work Instructions for all operational activities • Keeping production master data, resources, BOMs (Bill of Materials), production versions, and Master Recipes up to date on a regular basis in SAP B1 • Facilitating the discovery of workplace hazards, risk assessment, and the development of creative risk mitigation recommendations. • In charge of processes for managing change (MOC). • Ensuring that employees report near-misses and potential hazards Show less
-
-
-
MBCC Group
-
Germany
-
Chemical Manufacturing
-
700 & Above Employee
-
Production Supervisor
-
Mar 2020 - Apr 2023
PRODUCTION SUPERVISOR. MB CONSTRUCTION CHEMICAL 2020 Till date •Provide support and join improvement-based methods. • Ensure compliance of team members with process policies. • Ensure compliance with applicable laws and company policies • Analyze and ensure better result to fulfill all business requirement. • Provide training to workers and provide upgrade on various technical skills. • Supervise production personnel and Prepare effective production schedules. • Complete Production plans by scheduling and assigning personnel to specific tasks • Analyze all opportunities and recommend ways to improve efficiency and reduce costs. • Prioritize work assignment to ensure product are completed within production lead time. • Ensure health, safety and environmental regulations are all enforced on production plant. • Manage and prioritize all production processes and implementation on the production floor • Documenting production report on daily basis and recommending ways to improve the process. • Ensure daily transactions for semi-finished product, finished product, and packing material on SAP • Provide efficient backup to operation manager ensuring achievement of all internal & external needs. • Ensure strict adherence to MB Construction Chemical Solution/EHS standards in all areas of operation. •Supervise everyday working of department operation process and increase efficiency of workers for various growth-oriented programs Show less
-
-
-
BASF
-
Germany
-
Chemical Manufacturing
-
700 & Above Employee
-
Operation Supervisor
-
Jul 2018 - Mar 2020
•Supervised everyday working of department operation process and increase efficiency of workers for various growth-oriented programs• Carried out supervisory responsibilities in accordance with the organization’s policies and applicable laws.• Maintained and provide efficient backup to supply department and ensure achievement of all internal and external needs• Developed plans and supervise various departmental meetings and participate in various growth-based campaigns.• Analyzed and identified all performance related issues and ensure appropriate steps to prevent loss. • Administered all indoor performance in department through efficient coaching and monitoring.• Provided training to workers and provide upgrade to various technical skills.• Analyzed and ensured better result to fulfill all business requirement.• Provided support and joined improvement-based methods.• Prepared regular reports, performed audit on various operations and evaluated processes as per business requirements.• Analyzed all opportunities and recommended ways to improve efficiency and reduce costs.•Provided support and joined improvement-based method.• Monitored all administrative functions as per requirement. • Ensured compliance with applicable laws and company policies. Show less
-
-
Production/Maintenance Engineer
-
May 2015 - Jun 2018
• Exercised effective control on all production processes and ensured production is carried out according to standard process procedures.• Ensured compliance of team members with process policies.• Identified all issues in the team and provide continuous support to all members on the production floor • Supervised effective working of production personnel and Prepared effective production schedules.• Managed and prioritized all production processes and implementation on the production floor.• Executed each production plan as set out by the production manager• Maintained a safe clean and organized working environment. • Documented each production report on a daily basis and recommended ways to improve the process.• Prioritized, scheduled and delegated work assignment to ensure product are completed within production lead time• Ensured all work undertaken is checked and approved in accordance with the company's quality system• Ensured health, safety and environmental regulations are all enforced on production plant.• Risk assessment analysis• Preparation and supervision of technical repairs, modifications and upgrades on production floor.• Directed, instructed, supervised and trained teams of production personnel • Ensured strict adherence to BASF WEST AFRICA LTD/EHS standards in all areas of operation.• Completed Production plan by scheduling and assigning personnel to specific tasks.• Ensured daily transactions for semi-finished product, finished product, and packing materials on SAP. • General readings and Interpretation of Electrical, Pneumatics and P&ID diagrams • Develop test standards and operating instructions for electrical and automated systems • Ensured all work undertaken is checked and approved in accordance with the company's quality system Show less
-
-
-
DANGOTE SUGAR REFINERY PLC
-
Nigeria
-
Food and Beverage Services
-
300 - 400 Employee
-
Instrument/Automation Engineer Tech. (Contract)
-
May 2014 - Apr 2015
A - Installation, Calibration, Commissioning and Maintenance of the following instruments. 1. Electronics and Pneumatic Instruments 2. Electronics and Pneumatic Control 3. Electronics and Pneumatic Measurements (Analog & Digital) Instruments. 4. Flow, Level, Pressure and Temperature measuring instruments. 5. Control Valves, Sensors and Limit Switches. B - Modification, readings and Interpretation of Electronics and Instrumentation diagrams. C - Planning and Designing of Loops Diagrams for Field and Wiring Termination. D - Calibration of Transmitters using Honeywell Hand help Device. Show less
-
-
-
Olam
-
Singapore
-
Food and Beverage Services
-
700 & Above Employee
-
Management information system officer
-
Nov 2011 - Apr 2014
Responsibilities 1. Data Entry and reconciliation of procurement, warehousing and dispatch reports 2. Monitoring and evaluation of stocks quality compliance report 3. Physical stock verification and reconciliation with system generated report 4. Stock in transit monitoring and reporting 5. General plant maintenance. Accomplishments Successful over switch form I-Olam data base to SAP Olam data base Skills Used Self-motivation, value oriented, resourceful, adaptable, flexible and dependable – qualities. Show less
-
-
-
BUA Group
-
Nigeria
-
Manufacturing
-
300 - 400 Employee
-
PLANT ELECTRICAL/INSTRUMENT PROJECT TEAM LEADER
-
Mar 2011 - Oct 2011
• Installation of flow, level, pressure and temperature measuring instruments. • Installation of control valves, sensors and limit switches. • Installation of Pneumatics Measurements (Analog & Digital) Instruments. • Installation of industrial motors and field devices equipment’s. • Installation of flow, level, pressure and temperature measuring instruments. • Installation of control valves, sensors and limit switches. • Installation of Pneumatics Measurements (Analog & Digital) Instruments. • Installation of industrial motors and field devices equipment’s.
-
-
-
BUA Sugar
-
Nigeria
-
Food and Beverage Manufacturing
-
100 - 200 Employee
-
Automation, Electrical/Instrumentation Engineer Tech
-
Mar 2010 - Feb 2011
A - Installation, Calibration, Commissioning and Maintenance of the following instruments. 1. Electronics and Pneumatics Instruments 2. Electronics and Pneumatics Control 3. Electronics and Pneumatics Measurements (Analog & Digital) Instruments. 4. Flow, Level, Pressure and Temperature measuring instruments. 5. Control Valves, Sensors and Limit Switches. B - Modification, readings and Interpretation of Electronics and Instrumentation diagrams C - Planning and Designing of Loops Diagrams for Field and Wiring Termination. D - Calibration of Transmitters using Heart Communication. Show less
-
-
-
Tess Oil (service year)
-
Calabar, Nigeria
-
Electrical/Automation Technician
-
Apr 2008 - Feb 2009
-
-
Education
-
Adekunle Ajasin University
Bachelor of Science (B.Sc.), PHYSICS/ELECTRONICS -
Institute for Industrial Technology Lagos Professional Training & Coaching. Lagos
Associate's degree, MECHATRONICS -
Adekunle Ajasin University
Final year project, House Automation
Community
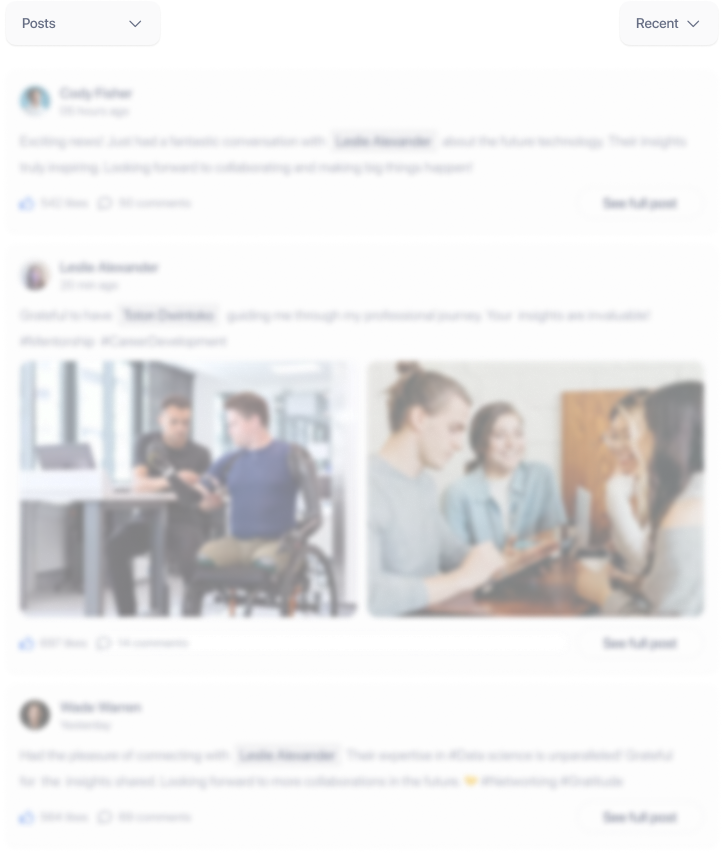