Ollie Knight
Global Projects Forecasting Manager at Hawk-Eye Innovations Ltd- Claim this Profile
Click to upgrade to our gold package
for the full feature experience.
Topline Score
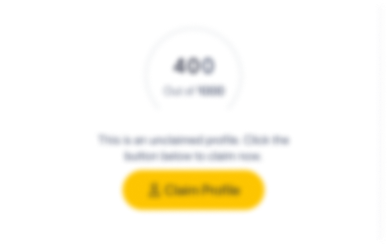
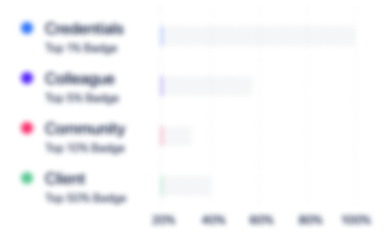
Bio

Anne Billson
Ollie has a proactive approach to tasks to ensure deadlines and customer satisfaction is met. He has excellent interpersonal skills in order to deal with people in a variety of situations. I would recommend Ollie highly.

Anne Billson
Ollie has a proactive approach to tasks to ensure deadlines and customer satisfaction is met. He has excellent interpersonal skills in order to deal with people in a variety of situations. I would recommend Ollie highly.

Anne Billson
Ollie has a proactive approach to tasks to ensure deadlines and customer satisfaction is met. He has excellent interpersonal skills in order to deal with people in a variety of situations. I would recommend Ollie highly.

Anne Billson
Ollie has a proactive approach to tasks to ensure deadlines and customer satisfaction is met. He has excellent interpersonal skills in order to deal with people in a variety of situations. I would recommend Ollie highly.

Experience
-
Hawk-Eye Innovations Ltd
-
United Kingdom
-
Technology, Information and Internet
-
700 & Above Employee
-
Global Projects Forecasting Manager
-
Jul 2022 - Present
-
-
-
AMETEK Airtechnology Group
-
United Kingdom
-
Aviation & Aerospace
-
1 - 100 Employee
-
Cell Lead
-
Jun 2020 - Jun 2022
Cell Lead for Heaters (inc. A350), Switches and Systems product at AMETEK Airtechnology Group in Sunbury-On-Thames. Managing 15 shop floor operatives including three team leaders, I am responsible for the on time delivery and quality of the components/assemblies manufactured in my cells. Health, Safety and Environmental issues in the cell along with the daily welfare of my staff is always considered along with robust plans to maintain up-skilling and training. Load and Capacity planning enables realistic and 'do-able' manufacturing plans to be executed in the cells whilst working cross functionally with Manufacturing Engineering and Planning. Show less
-
-
-
Rolls-Royce
-
Industrial Machinery Manufacturing
-
700 & Above Employee
-
Business Improvement Manager
-
Apr 2019 - Jan 2020
The CRF is a world class facility in two welding commodities - Linear Friction Welding Blisks (bladed disks) and Inertia Welding Disks and Drums.Key Functional Accountabilities:•Leading 'Blue Chip' Business Plan Deployment (BPD) development and execution of the improvement program. Focused on performance improvement and strategy delivery. Deployment of the 'one' plan in the business- driving the improvement activities•Lead and manage business improvement strategic reviews and business governance sessions. Facilitate Kaizen & Lean Engagement Events, problem resolution, Production System activities and improvement meetings. Coaching project sponsors, Green & Yellow belts and business leaders in lean thinking•Accountable for coaching and maintaining minimum standards in the Rolls-Royce Production System (RRPS); ensuring the business understands their production system maturity as well as the route to improve it. Coach the business to ensure they understand which minimum standards affect the performance metrics – SQCDPProgram managed BPD projects:1. Blisk Lead Time Reduction (Black belt Value Stream aligned project)Program managed and governed reducing the lead time of all Blisks in the facility, This directly reduced the inventory, thus increasing stock turn. The planned lead time in SAP was reduced from 14 weeks to 8 weeks. SMED event carried out on bottle neck machining centres, OEE managed weekly2. Supplier Improvement – Peening (Metal improving) CompanyHighlighted as a constraint within the value stream. Regular visits to govern all rate increase and lead time reduction actions – new dedicated robot identified and installed, ‘securing’ capacity to enable required rate through supplier3. F1 Vision/Visual FactoryPrimarily a plant wide 5S package of work to raise the standard of the shop floor to aid throughput and reduce part damage/non-conformance. Project milestones governed weekly to drive timely execution of the project Show less
-
-
Production Leader
-
Jul 2017 - Apr 2019
Having completed over 2 years as a Production Leader in the PMF, and still hungry to gain more experience in operations, I took a role in the TBF as a Value Stream aligned PL. I lead the largest value stream (Airbus) with the most complex part portfolio in the TBF, which itself is the single most important SCU Rolls-Royce PLC requires to deliver blades to keep planes in the air (Not AOG) and satisfy the largest roll programs in the company.Key Points:• Built on experience in PMF to now be operating in the TBF with over 60 works reporting directly to me over three core processes in turbine blade machining – Makino grinding, Die Sink & Film Cool EDM• Lead the team through regular communication (team briefs & bi-weekly newsletter entries) and enable them to develop through delegation and assigning champion roles • Drive increased throughput across the whole value stream using OEE capture, sessions & action plans to act on identified improvements. Taken the lead with engaging the team to accelerate these OEE increases• Closely manage absences within my team and the whole plant as a PL/HR team• Identified as a turbines Performance through our People ambassador to drive better performance in the team Show less
-
-
Production Leader
-
Apr 2015 - Jul 2017
After successfully completing my final role on the Ops Man graduate scheme (1 year as a PL), I was permanently recruited with Turbines in a GG11 PL role in April 2016. In my two years as a PL in the PMF, I managed up to 54 semi-skilled works population and it was my first role as a people manager.• Centre of the Team of 3 – managing this to generate the right results• In charge of final inspection areas needing to drive the team to deliver whilst managing any risks• HS&E tasks – I was RP in PMF, HAVS project to reduce exposure, updating risk assessments• Implementation of Production System and maintaining minimum standards with a drive to improve• Dealing with plant closure - motivating a workforce when the closing date has been extended many years – mixed emotions including agency recruitment• Owned FPAs to better the process and influence improvements within the area• Load and Capacity (PMF 4 weekly planning champion) leader from the PL/Ops side• Increasing rates – My Welding area was demonstrating +1.0 productivity. Due to Trent 1000 roll over program, I increased the machines by 50% and introduced x2 new welders. Initial hit on DP but then was able to achieve a better throughput and relieve an otherwise bottle necked area. Show less
-
-
Operations Management - Graduate Leadership Program
-
Sep 2013 - Apr 2015
Started in September 2013 on the Rolls-Royce Operations Management Graduate Scheme and completed three, six-month placements working in the UK, Norway and Poland.M.E – Derby, RMGC (Oct 2014 – April 2015)• Green belt project – GP EP 3.2.5 Source and Method change documentation improvement project. DMADV Project with real business need (waste reduction, leading to cost savings). Project delivered with trailing of new processes. • RMGC supplier facing SCU. Engaged with x3 suppliers to undertake reviews of EP 3.2.5 process and put in place the strategy to be fully compliant.Buyer – Norway, Marine (April 2014 – Oct 2014)• Brattvåg’s only operational buyer supporting: Machining, Standard: Mechanical, Electrical & Hydraulic and Raw Material• Lead purchasing / commercial side of SG Seals project to help mitigate the 'Red Top' issues. Organised and coordinated meetings with suppliers and team members. Dealt directly with new suppliers negotiating T&C’s, NDA, RFQs’ and placing PO’s• Casting Transfer to low cost source - Gate 2 C.4.53 passed (stage 1 items) Lead ITP to gate 2 then handed over to new IPT Lead. Representing saving of £125k claimed in 2014 (after gate 3).• Working with GCL Craig Cox and Sykkylven Stål: accelerated progress with changes to the price book reflecting a saving of £44k so far in 2014, with projections of £102k taking Sorb 2015 into considerationMRPC – Barnoldswick, S&T (Oct 2013 – April 2014)• Managed 3 final assembles and detailed parts for MT30, Trent 800, and Industrial RB211• Better transport value streaming at detail level: 5.7% real cash saving. Special Air freight charges to Energy in RRC not used after January 2014. This shows a 4.9% real cash saving over the last 2 months of placement (both for whole of SCAM plant)• Achieved 0 arrears to spares and engine plants• Slow Moving WIP reviews as standard diary event. Weekly report published for plant visual management. £0 Slow Moving WIP achieved in week 8 (reduced from over £50k) Show less
-
-
-
Loughborough University
-
United Kingdom
-
Higher Education
-
700 & Above Employee
-
Industrial Design & Technology Student
-
Oct 2009 - Jul 2013
Studied Industrial Design & Technology in Loughborough Universities new Design School, whilst representing Loughborough in Track & Field athletics at BUCS championships. Completing a sandwich year away from Loughborough at Diam International with a Dissertation gained me a Diploma in Professional Studies (DPS). Whilst at Loughborough I have worked for the Engineering Educational Trust (EET) in Holidays and helped out with tours on open days for the Design School. Studied Industrial Design & Technology in Loughborough Universities new Design School, whilst representing Loughborough in Track & Field athletics at BUCS championships. Completing a sandwich year away from Loughborough at Diam International with a Dissertation gained me a Diploma in Professional Studies (DPS). Whilst at Loughborough I have worked for the Engineering Educational Trust (EET) in Holidays and helped out with tours on open days for the Design School.
-
-
-
DIAM Group · Retail & Merch Solutions
-
France
-
Advertising Services
-
300 - 400 Employee
-
Student Development Designer
-
Jun 2011 - Aug 2012
Worked as part of the Design Development Team. A lot of my time was spent working on Pro Engineer (CAD software), Auto CAD, Adobe Photoshop & Illustrator. I developed carcasses, modules and display units for the cosmetic and perfume industries. I had to quickly learn to work in a very fast paced environment, prioritising and planning my workload. I feel I made a lasting impression on the company proving my ability to not only design but cope with such a fast moving company. One of my projects involved producing the CAD for the injection moulded logo letters for the brand Essie. Diam's clients included L'Oreal, Maybelline, MaxFactor, Channel, P&G, YSL, Essie & many other fashion brands which operate in popualr high street chemist stores & supermarkets. Show less
-
-
-
North West Leicestershire District Council
-
Ashby-de-la-Zouch
-
Lifeguard & Sports Attendant
-
Nov 2009 - Nov 2011
Worked at Hood Park Leisure Centre in Ashby-de-la-Zouch. Life guarded on the indoor and outdoor pools and was sports attendant for the facility. Involved in monthly training which improved my knowledge of life guarding and kept my first aid skills up to date. Worked at Hood Park Leisure Centre in Ashby-de-la-Zouch. Life guarded on the indoor and outdoor pools and was sports attendant for the facility. Involved in monthly training which improved my knowledge of life guarding and kept my first aid skills up to date.
-
-
-
Rolls-Royce
-
Industrial Machinery Manufacturing
-
700 & Above Employee
-
Manufacturing Engineer
-
Aug 2008 - Aug 2009
(Pre University, Post A-Levels) year placement in the Combustions and Casings Department of Rolls-Royce in Hucknall, Nottingham. This was my first job in industry, excluding work experience at MIRA. I found I matured from school pupil to student manufacturing engineer very quickly. I was able to work within the engineering team well and was regularly asked to work with different teams such as 'Quality' and 'Small Projects'. During my year in industry I won the midland region Contribution to Business Award and was runner up in the National event, held in London. Show less
-
-
-
HORIBA MIRA
-
United Kingdom
-
Business Consulting and Services
-
400 - 500 Employee
-
Student Intern
-
Jul 2006 - Aug 2006
As a student I undertook work experience internship at MIRA car testing facility. I gained an understanding of how a large company is run, and what was it was like to work there. I was working in the electronics department. I helped to repair wires from the crash tests. This also allowed me to gain a greater understanding of the electronics involved in a crash test - primarily accelerometers. As a student I undertook work experience internship at MIRA car testing facility. I gained an understanding of how a large company is run, and what was it was like to work there. I was working in the electronics department. I helped to repair wires from the crash tests. This also allowed me to gain a greater understanding of the electronics involved in a crash test - primarily accelerometers.
-
-
Education
-
Loughborough University
Bachelor of Arts (BA), Industrial Design & Technology -
Central College Nottingham
ILM, Level 3 Award in First Line Management -
Dixie Grammar School
GCE A-Levels, D&T, Sport & PE, Physics:
Community
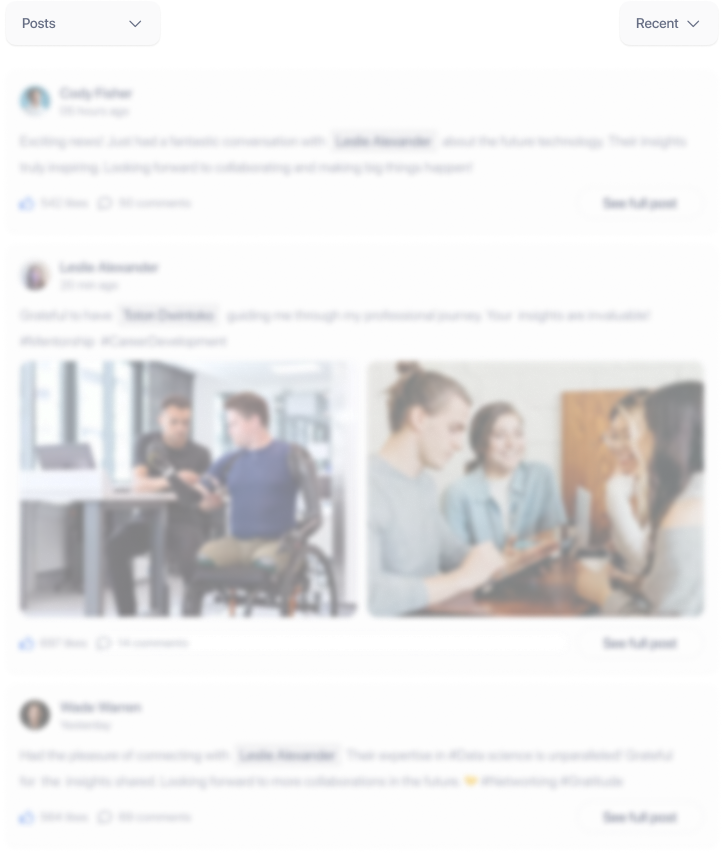