Olena Lyubetska
Quality Assurance Manager at Polproduct Netherlands BV- Claim this Profile
Click to upgrade to our gold package
for the full feature experience.
-
English Full professional proficiency
-
Ukrainian Native or bilingual proficiency
-
Russian Native or bilingual proficiency
-
French Elementary proficiency
-
Polish Limited working proficiency
-
Dutch Elementary proficiency
Topline Score
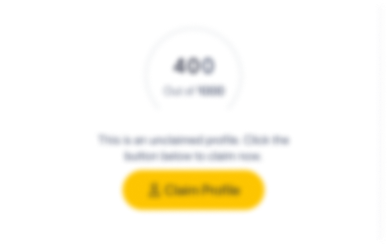
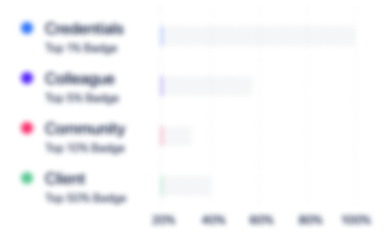
Bio

Iryna Vladimirova
I have worked with Olena as a colleague on a number of cross-functional initiatives while her work in the Production and EHS departments in Philip Morris Ukraine. She is a strong professional keen on new initiatives and continuous improvement in the organization. Her work at every new assignment is reflected in successful projects that produced very effective business results. Olena has always demonstrated a high level of ownership and commitment, being capable of taking increased level of responsibilities in new areas of business and cross-functional projects. An example of such a successful project was the attestation of working places for the Ukraine market, which required cross-functional interaction outside of the Manufacturing area. Olena is an Achiever. She was able to lead production lines in her Business Unit to great manufacturing results: Production uptime of more than 82% (which was a record result for an affiliate). She has a deep knowledge of manufacturing practices and possesses combined with strong people management skills. Olena can easily operate in any manufacturing environment.

Dmytro Milashchuk
Olena was a young specialist hired to the Quality Assurance department at Japan Tobacco Ukraine in 2000. She came to the Company when an old "Post-soviet" style factory was transforming into a modern production facility and part of multinational. The new production model required drastical improvements in manufacturing practices and uptake in quality performance and management. Despite the lack of experience in the tobacco manufacturing field Olena quite quickly got an excellent understanding of the technological processes and organized the work of the analytical group in the Quality Assurance department. Soon after the start-up, she was assigned to a QA Chief Analyst position direcrly supervising several employees.

Iryna Vladimirova
I have worked with Olena as a colleague on a number of cross-functional initiatives while her work in the Production and EHS departments in Philip Morris Ukraine. She is a strong professional keen on new initiatives and continuous improvement in the organization. Her work at every new assignment is reflected in successful projects that produced very effective business results. Olena has always demonstrated a high level of ownership and commitment, being capable of taking increased level of responsibilities in new areas of business and cross-functional projects. An example of such a successful project was the attestation of working places for the Ukraine market, which required cross-functional interaction outside of the Manufacturing area. Olena is an Achiever. She was able to lead production lines in her Business Unit to great manufacturing results: Production uptime of more than 82% (which was a record result for an affiliate). She has a deep knowledge of manufacturing practices and possesses combined with strong people management skills. Olena can easily operate in any manufacturing environment.

Dmytro Milashchuk
Olena was a young specialist hired to the Quality Assurance department at Japan Tobacco Ukraine in 2000. She came to the Company when an old "Post-soviet" style factory was transforming into a modern production facility and part of multinational. The new production model required drastical improvements in manufacturing practices and uptake in quality performance and management. Despite the lack of experience in the tobacco manufacturing field Olena quite quickly got an excellent understanding of the technological processes and organized the work of the analytical group in the Quality Assurance department. Soon after the start-up, she was assigned to a QA Chief Analyst position direcrly supervising several employees.

Iryna Vladimirova
I have worked with Olena as a colleague on a number of cross-functional initiatives while her work in the Production and EHS departments in Philip Morris Ukraine. She is a strong professional keen on new initiatives and continuous improvement in the organization. Her work at every new assignment is reflected in successful projects that produced very effective business results. Olena has always demonstrated a high level of ownership and commitment, being capable of taking increased level of responsibilities in new areas of business and cross-functional projects. An example of such a successful project was the attestation of working places for the Ukraine market, which required cross-functional interaction outside of the Manufacturing area. Olena is an Achiever. She was able to lead production lines in her Business Unit to great manufacturing results: Production uptime of more than 82% (which was a record result for an affiliate). She has a deep knowledge of manufacturing practices and possesses combined with strong people management skills. Olena can easily operate in any manufacturing environment.

Dmytro Milashchuk
Olena was a young specialist hired to the Quality Assurance department at Japan Tobacco Ukraine in 2000. She came to the Company when an old "Post-soviet" style factory was transforming into a modern production facility and part of multinational. The new production model required drastical improvements in manufacturing practices and uptake in quality performance and management. Despite the lack of experience in the tobacco manufacturing field Olena quite quickly got an excellent understanding of the technological processes and organized the work of the analytical group in the Quality Assurance department. Soon after the start-up, she was assigned to a QA Chief Analyst position direcrly supervising several employees.

Iryna Vladimirova
I have worked with Olena as a colleague on a number of cross-functional initiatives while her work in the Production and EHS departments in Philip Morris Ukraine. She is a strong professional keen on new initiatives and continuous improvement in the organization. Her work at every new assignment is reflected in successful projects that produced very effective business results. Olena has always demonstrated a high level of ownership and commitment, being capable of taking increased level of responsibilities in new areas of business and cross-functional projects. An example of such a successful project was the attestation of working places for the Ukraine market, which required cross-functional interaction outside of the Manufacturing area. Olena is an Achiever. She was able to lead production lines in her Business Unit to great manufacturing results: Production uptime of more than 82% (which was a record result for an affiliate). She has a deep knowledge of manufacturing practices and possesses combined with strong people management skills. Olena can easily operate in any manufacturing environment.

Dmytro Milashchuk
Olena was a young specialist hired to the Quality Assurance department at Japan Tobacco Ukraine in 2000. She came to the Company when an old "Post-soviet" style factory was transforming into a modern production facility and part of multinational. The new production model required drastical improvements in manufacturing practices and uptake in quality performance and management. Despite the lack of experience in the tobacco manufacturing field Olena quite quickly got an excellent understanding of the technological processes and organized the work of the analytical group in the Quality Assurance department. Soon after the start-up, she was assigned to a QA Chief Analyst position direcrly supervising several employees.

Credentials
-
Certified Food Safety HACCP Manager (CFSHM)
SCS Global ServicesAug, 2022- Nov, 2024 -
Internal Auditor ISO 9000; ISO 14000; OHSAS 18000
Bureau Veritas Consumer Products ServicesNov, 2009- Nov, 2024
Experience
-
Polproduct Netherlands BV
-
Netherlands
-
Food and Beverage Manufacturing
-
1 - 100 Employee
-
Quality Assurance Manager
-
May 2022 - Present
➢ Led the organization towards successful FSSC22000 Certification. ➢ Assured compliance to BRC Standard requirements for Trading organization. ➢ Food Safety Management System development for the production facility. ➢ Customer relations (Contract quality support, complaints’ management, audits) ➢ NOP Organic Certification ➢ Kosher ➢Suppliers’ audit ➢ Led the organization towards successful FSSC22000 Certification. ➢ Assured compliance to BRC Standard requirements for Trading organization. ➢ Food Safety Management System development for the production facility. ➢ Customer relations (Contract quality support, complaints’ management, audits) ➢ NOP Organic Certification ➢ Kosher ➢Suppliers’ audit
-
-
-
-
Consultancy Services
-
Sep 2018 - Mar 2019
Food Safety system development Food Safety system development
-
-
-
Philip Morris International
-
Switzerland
-
Tobacco Manufacturing
-
700 & Above Employee
-
Supervisor EHS
-
Nov 2009 - Aug 2013
➢ Acted as a Project Leader on the successful OHSAS 18000 & ISO 14000 Standards' certification.➢ Was leading Risk assessment execution within the organization.➢ Developed Contractor Management System for the Site: from jobs registration and permit to safety audits at working places. 0 LTI after implementation.➢ Achieved next level in the High Risk Jobs execution: inventory of all HRJ types and registration in SAPresulted in timely training provision and compliance to legislative requirements.➢ Organized Safety promotion programs: I-safety, safe executing of HRJs, accounting of LTI- free hours.➢ Achieved 100% compliance with Ukrainian legislation and Company standards in healthcare management and occupational diseases prevention (passed state audits with zero comments).➢ Developed EHS Strategy (roadmap for the site) encompassing Warehouse safety program; Labor safetyfor Sales and Office organization; Car fleet safety. Show less
-
-
Production Manager
-
Oct 2008 - Oct 2009
➢ Improved Productivity by 9.7% through the successful implementation of the LEAN culture in my Business Unit (short stops program, KAIZEN teams, shift change over communication improvement).➢ Achieved all relevant production KPIs: safety, quality, productivity.➢ Lead implementation of the LEAN tools in my production unit: 6 SIGMA for production process parameters management; KAIZEN teams; 5S, statistical reporting for Line Leaders.➢ Implemented people development program utilizing the teamwork, continuous improvement and knowledge sharing. Show less
-
-
QA&MQA Labs Supervisor
-
May 2006 - Oct 2008
➢ Developed clear criteria for semi-product &FG product rejection; created standard algorithm to manage rejected products (customer complaints decreased by 21%; defective products decreased by 42%).➢ Managed Quality Assurance laboratory (semi-products and FG products quality control performed by 3 shifts of Inspectors, market research, transition to a new Quality Defects Manual executed).➢ Managed Material Quality Assurance Lab: Incoming Quality Control of materials has been performed, Suppliers Quality Index calculated regularly, Suppliers Audit organized, work with material complaints from production, productivity initiatives development. Show less
-
-
QA Projects Analyst
-
Dec 2003 - May 2006
➢ Participated in a project initiated by HQ QA to transform the Quality Methods into Quality Management System in accordance with ISO 9001 Standard. All procedures and processes were adopted to the requirements of ISO 9001 Standard. PM Ukraine QMS was successfully certified to ISO 9001 ➢ Statistical methods (process capability, control charts rules) were proposed as a tool to improve production performance: trainings were developed and delivered to more then 200 employees.
-
-
-
JTI (Japan Tobacco International)
-
Switzerland
-
Tobacco Manufacturing
-
700 & Above Employee
-
QA Chief Analyst
-
Oct 2000 - Nov 2003
Quality Assurance: implemented the standardized reports for quality KPI for the production floor employees; visualisation of the manufacturing performance for further continuous improvement (Pareto diagrams, statistical charts). New product launch coordination: participation in R&D team work at the production site by conducting material testing, cigarettes’ prototypes testing, post product launch evaluation. metrology&certification: development of the measurement methods, certification of measurement devices. Show less
-
-
-
Langmead Herbs
-
United Kingdom
-
Food Production
-
1 - 100 Employee
-
Harvest Supervisor
-
May 1999 - Oct 1999
Harvest management of Iceberg lettuce: quality assurance, quality control, production employees training, reporting. Harvest management of Iceberg lettuce: quality assurance, quality control, production employees training, reporting.
-
-
Education
-
National University of Life and Environmental Sciences of Ukraine
Bachelor, International Agribusiness -
Management Centre Europe
Project Management
Community
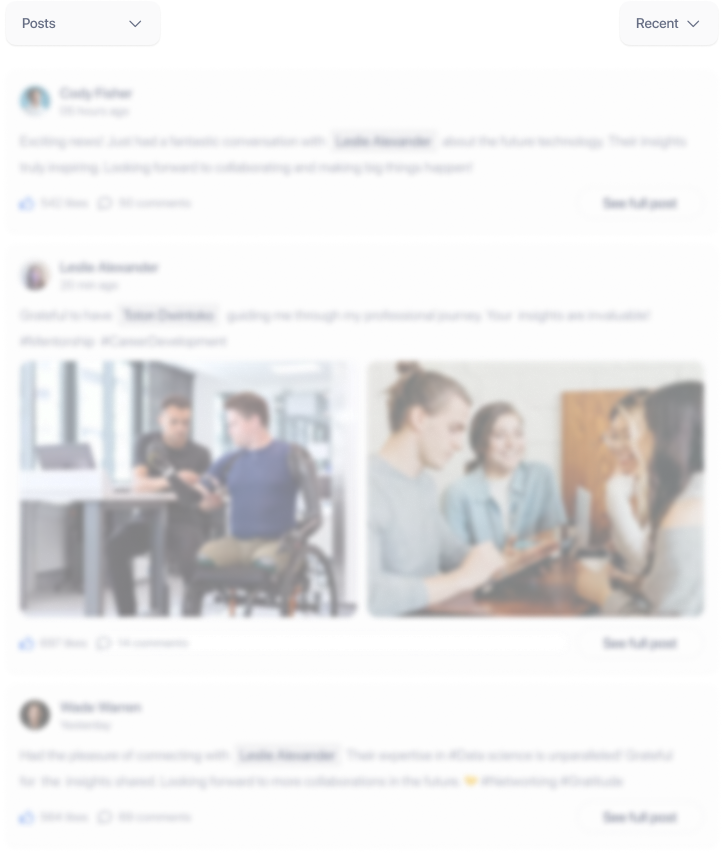