Obinna Aniakor
QC Lead at MG Vowgas Group- Claim this Profile
Click to upgrade to our gold package
for the full feature experience.
Topline Score
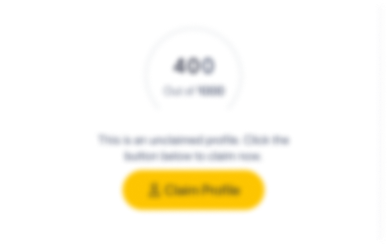
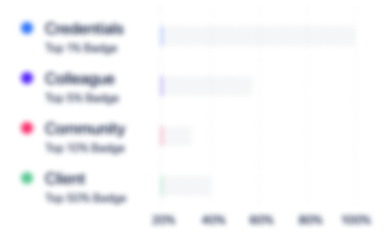
Bio


Experience
-
MG Vowgas Group
-
Nigeria
-
Oil and Gas
-
1 - 100 Employee
-
QC Lead
-
Nov 2020 - Present
Ensuring that Testing, Qualification and Certification process for welding are in compliant with project code and client specifications Ensuring that Testing, Qualification and Certification process for welding are in compliant with project code and client specifications
-
-
-
Aquaterra Energy
-
United Kingdom
-
Oil and Gas
-
100 - 200 Employee
-
Welding Inspector
-
Aug 2019 - Mar 2020
Ensuring that, testing, qualification and certification process for welding are in compliant with project code and client specifications Ensuring that, testing, qualification and certification process for welding are in compliant with project code and client specifications
-
-
-
Chevron
-
United States
-
Oil and Gas
-
700 & Above Employee
-
Qc Site Rep.
-
Aug 2018 - Aug 2019
-
-
-
ENFRASCO LIMITED
-
United Kingdom
-
Industrial Machinery Manufacturing
-
-
Aug 2017 - Aug 2018
• Preparation of quality documents such as ENFRASC – NLNG quality Valve Maintenance Daily report and Final Check List.• Liaising with client representatives at NLNG Bonny Island and ENFRASCO QA/QC (Expatriate)Valve Maintenance Team on quality/ documentation issues.• Collection / Review of ENFRASC – NLNG quality Valve Maintenance Daily Report and Final Check List.• Preparing and Monitoring ENFRASC – NLNG quality Valve Maintenance Inspection Data Report (IDR).
-
-
-
Aug 2017 - Aug 2018
-
-
-
-
welding Inspector
-
Apr 2014 - Jun 2017
• Preparation of quality documents such as quality plan, procedures, work instructions, Inspection and Test Plan, Traveler, Weld Log and Weld Map as per ASME requirement. • Studying codes, procedures and required project specifications and ensuring that they are followed strictly. • Preparation of testing, qualification and certification processes for welding as per project specifications. • Liaising with client representatives on quality issues. • Calibration of Welding Machine using Clamp meter. • Calibration of Quiver and Electrode baking oven using Infra-Red thermometer. • Materials inspection & traceability. • Dimensional (Fit-up) inspection before and after welding. • Continuous surveillance and in-process inspection to ensure that all stages of production meet specifications and client requirements. • Provision of accurate data of the welding inspection parameters. • Carrying out visual inspection, during and after welds. • Preparation of NDT work order sheets as per project specifications. • Review of Radiographic Film and Signing of RT, MT, PT and UT Reports. • Preparation of final test pack and inspection of hydro test (pressure test) & pneumatic test. • Carrying out Ultrasonic Thickness Inspection on Carbon Steel Plates and Dish Heads using Ultrasonic Thickness Gauge Machine • Preparing and Monitoring Manufacturing Data Book (MDB). Show less
-
-
-
-
Lead Welding Inspector
-
Dec 2010 - Apr 2014
•Preparation of quality documents such as quality plan, procedures, work instructions, Inspection and Test Plan, Traveler, Weld Log and Weld Map as per ASME requirement. •Studying codes, procedures and required project specifications and ensuring that they are followed strictly. •Preparation of testing, qualification and certification processes for welding as per project specifications. •Liaising with client representatives on quality issues. •Calibration of Welding Machine using Clamp meter. •Calibration of Quiver and Electrode baking oven using Infra-Red thermometer. •Materials inspection & traceability. •Dimensional (Fit-up) inspection before and after welding. •Continuous surveillance and in-process inspection to ensure that all stages of production meet specifications and client requirements. •Provision of accurate data of the welding inspection parameters. •Carrying out visual inspection, during and after welds. •Preparation of NDT work order sheets as per project specifications. •Review of Radiographic Film and Signing of RT, MT, PT and UT Reports. •Preparation of final test pack and inspection of hydro test (pressure test) & pneumatic test. •Carrying out Ultrasonic Thickness Inspection on Carbon Steel Plates and Dish Heads using Ultrasonic Thickness Gauge Machine •Preparing and Monitoring Manufacturing Data Book (MDB). Show less
-
-
Education
-
Enugu State university of science and Technology [ESUT]
Bachelor’s Degree, Metallurgical / Materials Engineering
Community
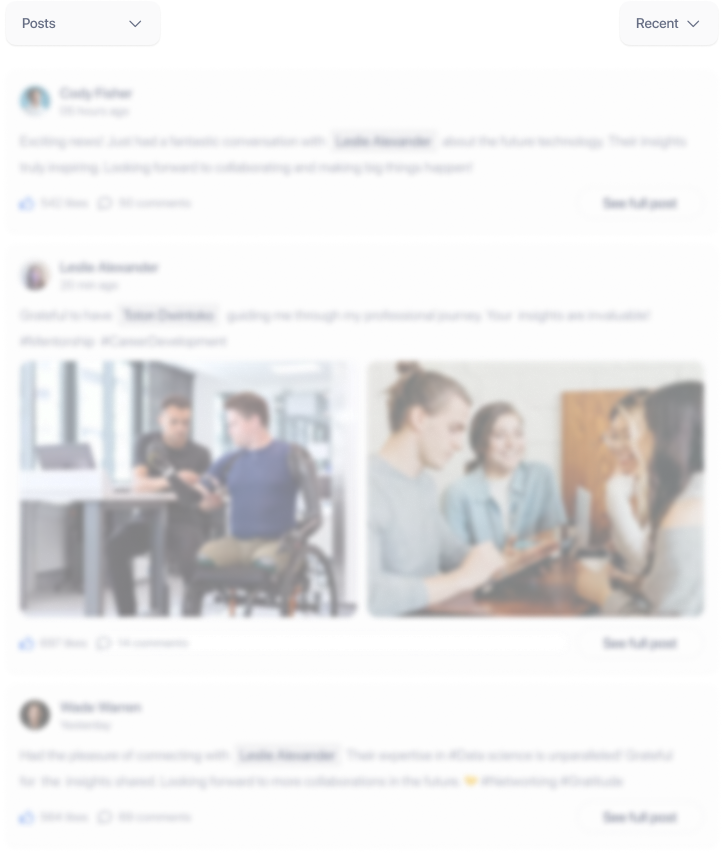