Noah Allen
Customer Engineer at DISCO HI-TEC AMERICA, INC.- Claim this Profile
Click to upgrade to our gold package
for the full feature experience.
Topline Score
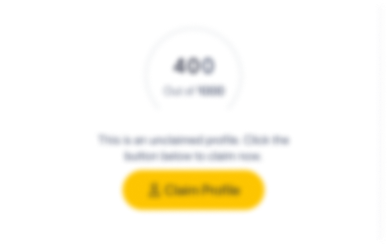
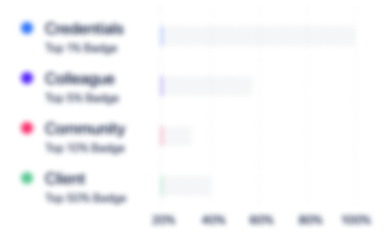
Bio


Experience
-
DISCO HI-TEC AMERICA, INC.
-
United States
-
Semiconductor Manufacturing
-
1 - 100 Employee
-
Customer Engineer
-
Sep 2021 - Present
Primarily responsible for installation, maintenance, and troubleshooting on Disco grinding machines. Primarily responsible for installation, maintenance, and troubleshooting on Disco grinding machines.
-
-
-
Windlift
-
United States
-
Renewable Energy Semiconductor Manufacturing
-
1 - 100 Employee
-
Mechanical Engineering Intern
-
May 2020 - Sep 2021
I returned to interning at Windlift in May 2020, stepped away to finish my engineering degree from August to December, and have resumed working part time in an internship/support role since. The technical expertise that I developed while working on the first electromechanical tether back in 2019 has been crucial in designing lighter-weight, stronger, lower cost tethers for our Airborne Power Generators. Major projects have included: - Reworking tether from two-line to single-line design. - Revising manufacturing plans to save ~75% on manpower and changing materials to save 20% on cost and 13% on weight with minimal impact to electrical performance. - Characterizing thermal performance at a range of electrical currents. - Leveraging resistance heating to rapidly collapse a heat-shrinkable jacket down onto 400 feet of carbon fiber and electrical conductor, saving time and money. - Supported the development of manufacturing documenting for new carbon fiber test aircraft.
-
-
-
Windlift
-
United States
-
Renewable Energy Semiconductor Manufacturing
-
1 - 100 Employee
-
Engineering Intern
-
Jan 2019 - Aug 2019
In this role, I primarily spearheaded research and development of a two-line electromechanical tether for use with Windlift's Airborne Power Generator (APG) test platform. This included: - Material strength testing and characterization. - Analysis of test results primarily using Excel and comparison with expected results based on material specifications. - Generation of reports discussing results and their ramifications, plus detailed documentation of testing procedures. - Creation of final tether design plus build manuals. I led a team of five people to successfully build a full-scale, 400' tether on a blazing hot runway in Butner, NC. Alongside this primary project, I handled a large chunk of fiberglass composite manufacturing for test aircraft parts, assisted in putting together wiring diagrams for various sensors and controllers, hand-wound a brushless DC motor, and built several test rigs. All in a day's work.
-
-
-
North Carolina State University
-
United States
-
Higher Education
-
700 & Above Employee
-
Painter
-
May 2018 - Aug 2018
I worked in the NC State facilities paint shop during summer 2018 both doing basic touch-up work and, periodically, more sophisticated total repaints around the university's campus. The primary focus was on dorm rooms, but exterior doors, outdoor furniture and walkways were also attended to. I worked in the NC State facilities paint shop during summer 2018 both doing basic touch-up work and, periodically, more sophisticated total repaints around the university's campus. The primary focus was on dorm rooms, but exterior doors, outdoor furniture and walkways were also attended to.
-
-
Education
-
North Carolina State University
Bachelor’s Degree, Mechanical Engineering
Community
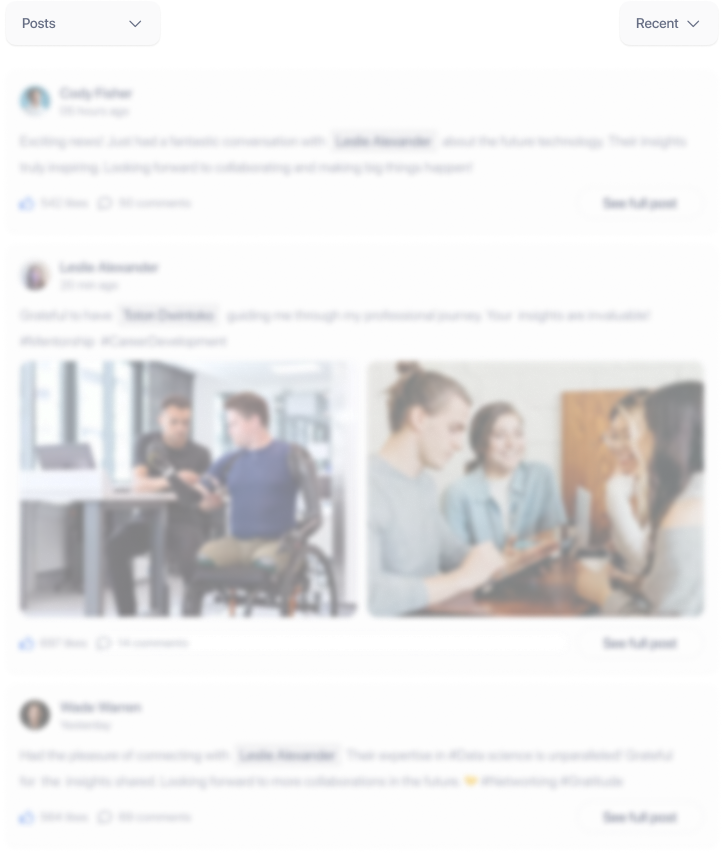