Nikola Segedi
Procurement Specialist | Inventory Controller at ROR Group- Claim this Profile
Click to upgrade to our gold package
for the full feature experience.
-
English -
-
German -
-
Italian -
-
Russian -
Topline Score
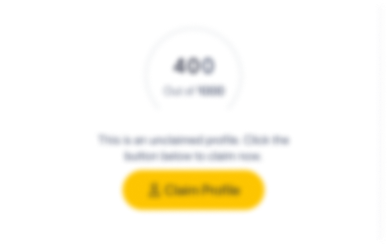
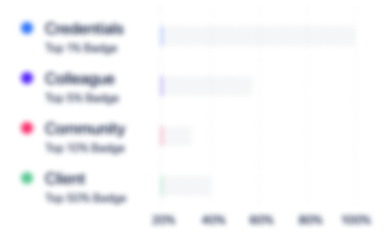
Bio


Experience
-
ROR GROUP
-
Australia
-
Consumer Services
-
1 - 100 Employee
-
Procurement Specialist | Inventory Controller
-
Jan 2023 - Present
Implementing new ERP System, Processes & Procedures Synchronization, Organizing Stock Take, Continuous Improvement in Warehousing and Storage Operations, Reducing Costs and Business Expenses related to Procurement and External Storage Units. Implementing new ERP System, Processes & Procedures Synchronization, Organizing Stock Take, Continuous Improvement in Warehousing and Storage Operations, Reducing Costs and Business Expenses related to Procurement and External Storage Units.
-
-
-
Boutique AV
-
Australia
-
IT Services and IT Consulting
-
1 - 100 Employee
-
Procurement Specialist | Inventory Controller
-
Jan 2023 - Present
Implementing new ERP System, Processes & Procedures Synchronization, Organizing Stock Take, Continuous Improvement in Warehousing and Storage Operations, Reducing Costs and Business Expenses related to Procurement and External Storage Units. Implementing new ERP System, Processes & Procedures Synchronization, Organizing Stock Take, Continuous Improvement in Warehousing and Storage Operations, Reducing Costs and Business Expenses related to Procurement and External Storage Units.
-
-
-
Port Melbourne Forklift Drivers
-
Australia
-
Transportation, Logistics, Supply Chain and Storage
-
1 - 100 Employee
-
Head of Association - Logistics, Supply Chain & Warehousing (Associate Member - Master Tradesman)
-
2020 - Present
Interim administrator and governance officer taking charge of the trade association and third-party warehouse supervisions, by monitoring, leading, organizing training, support, and managing onsite staff, conducting research, market analysis, resource allocation, developing business platforms and operational processes, as well as setting goals to ensure that overall day-to-day operations run smoothly.Tasks and Projects: Contract and Records Management, Business Development, Data Analysis, Market Analysis, Workflow Automation, Scheduling Operations on Site, Teams Coordination, Process Implementation, OHS Policy Implementation, Compliance Matters, Operations Strategy, Procurement Operations, Supply Chain Management, Cost Reduction and Zero-Based Budgeting, Industry 4.0, Lean Six Sigma Performance Improvement, Audit and Reporting.
-
-
Individual/Sole Trader (Associate Member/Craft Fellow - Foreman: 22 573 453 798)
-
2018 - 2022
Supply Chain Management, Commercial Facility Operations Management, Industrial Facility Operations Management, Warehouse Operations Management, Space Optimization (Interior Design and Architectural Planning), Shipping Container Terminal - Yard Coordination, Timber Yards Coordination, Drive/Factory/Production Plant Traffic Coordination, 3PL Software & Cross-Docking System Operations.
-
-
Individual/Sole Trader (Associate Member/Craft Fellow: 22 573 453 798)
-
Jul 2016 - 2018
Casual freelancer hired to work for different logistics, transport, and warehousing companies on particular assignments as a team member, mainly assisting Third-Party Container Schedulers, Container Management, and Managed Labour Providers or otherwise engaged in various high-risk jobs such as container loading and unloading, cross-docking and order picking, reverse logistics, and reworks (restacking and repacking) across different sites in Greater Melbourne. Geographical Experience: Greater Melbourne - Qube Vic Dock Intermodal Terminal, Vic Dock Warehouse, Dynon Intermodal Terminal, Dynon Empty Park, Somerton Intermodal Terminal, Altona Freight Terminal, Silk Terminal, Caterpillar Parts Distribution Centre, Schiavello-Modular Construction Assembly Tullamarine, Greater Melbourne Construction Sites, Events and Projects.
-
-
-
JEA Technologies
-
Australia
-
Computer Hardware Manufacturing
-
1 - 100 Employee
-
Logistics and Warehousing Coordinator
-
Nov 2021 - Jan 2023
Logistics, Transport and 3PL Coordination, Supply Chain Coordination, Incoming Parcels and Deliveries Processing, Data Inputs, Commercial Invoices/Export Documentation, Harmonization Codes Search and Identification, Inventory and Stock Control (Movement Monitoring, Data Analysis), Warehouse Facilities Coordination, Inventory Check (Cycle Counting, Slotting, Stock Takes, Labelling, Reporting and Ticketing), Space Optimization, Material Handling, Recycle Material Removal, Plant Operations (Assembly and Production Line Assistance), Branch Operations/General Support.
-
-
-
thyssenkrupp
-
Germany
-
Industrial Machinery Manufacturing
-
700 & Above Employee
-
Lift Components | Supply Chain & Warehousing - Automotive (Vertical Transportation)
-
Apr 2018 - Nov 2021
Supply Chain Management, Warehouse Coordination/Facility Management, Inventory Control, Space Optimization, Slotting, Yard and Containers Supervision, Plant Operations, Incident/Critical Incident Management, Parts Interpretation, Procurement and Delivery Coordination, Branch Operations, Procurement & Purchasing Support, Fleet Coordination (40+ Company Vehicles - Vans and Trucks, Special Purpose Vehicles, Forklifts, Walkie-Stackers, Material Handling Machines, 3PL, Freight Forwarders, Internal and External Drivers, Contractors), Material Handling, Logistics & Parcel Delivery. Involved in the Incident Responses, Essential Services, Creation of the Space Optimization Plan, Racking Development Plan and New Racking Installation, Traffic Management Plan, Hazard, and Risk Assessments, Safety Management Plan, Emergency Evacuation Plan (Chief Fire-Warden organizing 6-Monthly Drills and attending Real Evacuations), Dangerous and Hazardous Substances Manual Datasheet Digital Library, Business Process Mapping, Flowchart Processes, Process Mapping Software, Critical Errors Improvement by Analysis, Archiving Processes and Policy.
-
-
-
Toyota Motor Corporation
-
Motor Vehicle Manufacturing
-
700 & Above Employee
-
Process Worker | Quality Check & Robot Maintenance - Automotive
-
Sep 2016 - Sep 2017
Paint Shop and Resin | Manufacturing Line - Toyota Aurion and Toyota Camry Member of the Quality Circle - ED Line Quality Check and Manufacturing Processes including Corrosion Control, Offshore Erosion Control, Sealer Application Defects, Under-body/Leak Check, Quality Improvement Suggestion Scheme, Gulf (Middle East and Q8) Car Series Inspection, Detailing, Refinishes and Improvements. Industrial Cleaning and Maintenance - Robots and Coat Appllicators (Primer Applicator and Top-Coat Applicator), Tunnels, Car-Washing Systems, Filter Control, Replacement and Application, Storage Tanks (Primer, Top Coat and Water), TOLO, HRW Licensed, First Aid Certified. Trainee @ General Asset Protection | Power-Train - Toyota Hybrid System II Trainee Mechanic - Hybrid Synergy Drive/Toyota Hybrid System II for Toyota and Lexus, Manufacturing and Production Process Operations, General assembly, Checking lubricants, oils, and other liquids, Water testing. Certificate II in Automotive Studies - "Toyota Way"
-
-
Community
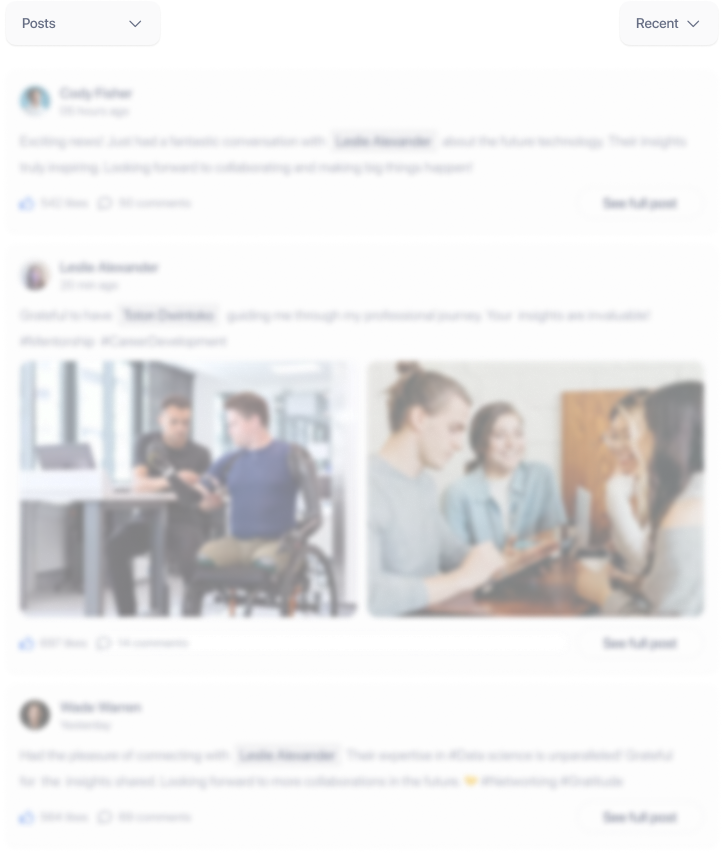