Niklas Grzegorzewski
Senior Airframe Design Engineer at AutoFlight- Claim this Profile
Click to upgrade to our gold package
for the full feature experience.
-
Deutsch Native or bilingual proficiency
-
Englisch Full professional proficiency
-
Französisch Elementary proficiency
Topline Score
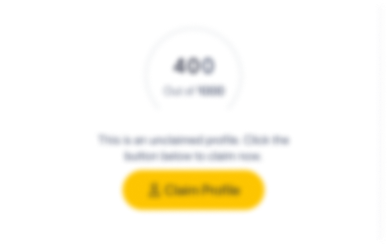
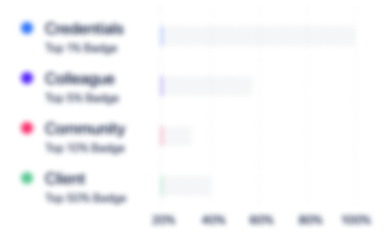
Bio


Credentials
-
Internal Auditor for EN 9100
VOREST AGApr, 2020- Nov, 2024 -
CAE - Cambridge Certificate in Advanced English (C1)
Cambridge English Language Assessment
Experience
-
AutoFlight
-
Germany
-
Aviation and Aerospace Component Manufacturing
-
1 - 100 Employee
-
Senior Airframe Design Engineer
-
Apr 2023 - Present
-
-
-
Volocopter
-
Germany
-
Aviation and Aerospace Component Manufacturing
-
400 - 500 Employee
-
Product Owner Airframe and Integration - VoloDrone
-
May 2022 - Mar 2023
Technical lead of the Airframe Design and Integration team for the VoloDrone guiding the development and improvement of the airframe. Main point of contact of the structural airframe for system integration, prototyping/production, and flight test.
-
-
Senior Design Engineer - VoloDrone
-
Nov 2021 - Jul 2022
Structural design engineer for the airframe structure and system integration of the VoloDrone.
-
-
Structural Design Engineer
-
May 2018 - Oct 2021
Structural design engineer for the composite airframe structure of the eVTOL “2X” and "VoloCity". Focal point for structural airframe systems coordinating the interests of performance, stress analysis, manufacturing, system interfaces, and certification.Support of the manufacturing and assembly of prototype components and systems, as well as planning, execution, and documentation of structural tests required for EASA certification.Technical liaison selecting and managing component suppliers, and creating and maintaining technical specification based on EASA CS requirements.CAD and PLM Key-User. Defining software requirements and test implementation of modifications to ensure a smooth work environment necessary for the entire design team.Former Scrum Master of the Agile Development Team for the structural airframe design and prototype production. Show less
-
-
-
Kasaero GmbH
-
Germany
-
Aviation and Aerospace Component Manufacturing
-
1 - 100 Employee
-
Development Engineer
-
Dec 2016 - Apr 2018
Structural design and FEM analysis (FEMAP with NX Nastran) of monolithic and sandwich components made of fiber-reinforced plastics for civil aviation (CS22 and CS23);Production of prototype parts made of fiber-reinforced plastics using hand lamination and vacuum infusion (RTM)
-
-
Master Thesis
-
May 2016 - Nov 2016
"Production of sandwich shell components with fiber composites" - Process optimization and parameter determination in the production of shell components with local buckling reinforcements (sandwich cores / stringer) without preforms and mech. or chem. fixation aids. Production with vacuum infusion process (RTM).
-
-
Working Student
-
Aug 2015 - Nov 2016
Design, layout and production of fiber composite components for civil aviation (hand lay-up); mold design; manufacturing of prototypes; production planning; documentation
-
-
-
Bosch
-
Germany
-
Software Development
-
700 & Above Employee
-
Working Student
-
Feb 2014 - Feb 2016
Performing leakage tests for automotive pressure sensor models during the design phase. Preparation and processing of technical customer documentation. Performing leakage tests for automotive pressure sensor models during the design phase. Preparation and processing of technical customer documentation.
-
-
-
MTU Aero Engines
-
Germany
-
Aviation and Aerospace Component Manufacturing
-
700 & Above Employee
-
Bachelor Thesis
-
Oct 2013 - Jan 2014
"Investigations on a method for the automated estimation of manufacturing costs in the design phase of civil aircraft engines" - Programming of subroutines (FORTRAN) for the company's own performance calculation tool, implementation of jet-engine models and validation of the method
-
-
Internship
-
Apr 2013 - Sep 2013
Internship in the Department of Advance Development and Performance - Preparation of engine data file for the company's own performance calculation program. Processing of sub-routines (FORTRAN).
-
-
Education
-
Universität Stuttgart
Master of Science, Aerospace Engineering -
Universität Stuttgart
Bachelor of Science (B.Sc.), Aerospace Engineering
Community
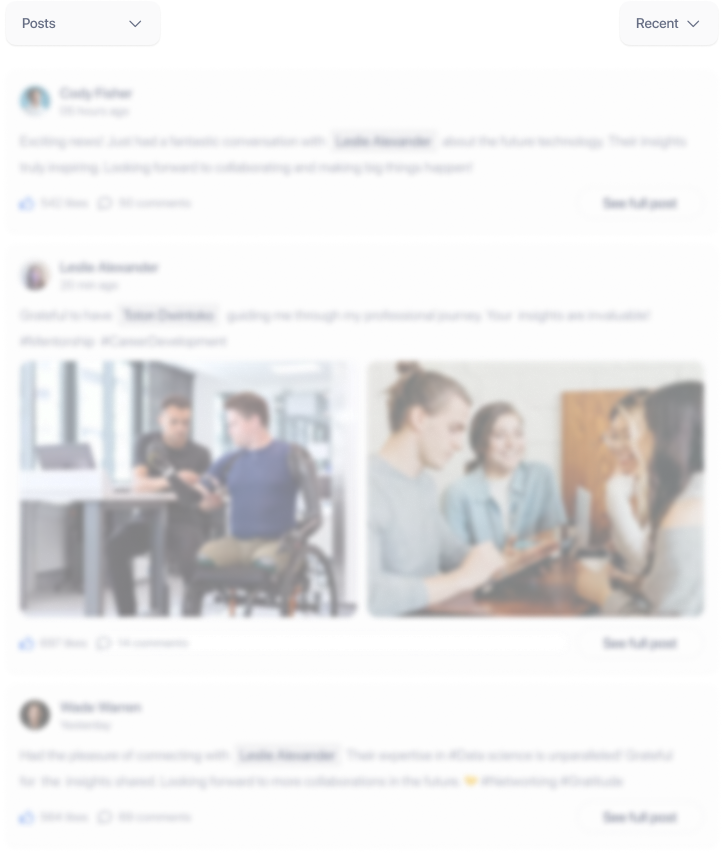