Nigel Robinson
Chief Operating Officer at Digital Manufacturing Centre (DMC)- Claim this Profile
Click to upgrade to our gold package
for the full feature experience.
-
English Native or bilingual proficiency
Topline Score
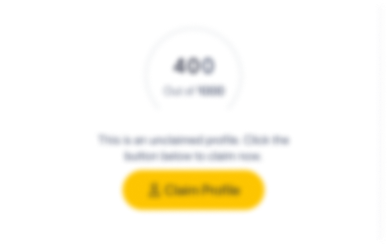
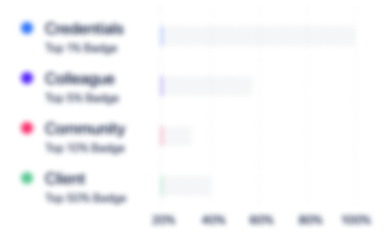
Bio


Experience
-
Digital Manufacturing Centre (DMC)
-
United Kingdom
-
Industrial Machinery Manufacturing
-
1 - 100 Employee
-
Chief Operating Officer
-
Jun 2020 - Present
WE ARE NOT A 3D PRINTING SERVICE BUREAU - WE ARE AN ENGINEERING SOLUTION PRODUCTION CENTRE FOR ADDITIVE MANUFACTURING. With a sound engineering solution approach to produce Additive Manufactured the Digital Manufacturing Centre is a positive disruptor to the additive manufacturing industry. Servicing various sectors for Metal and Polymer including powder bed laser sintering, FDM, SLA etc. the DMC has a full on site production supply chain to enable sustainable high quality production… Show more WE ARE NOT A 3D PRINTING SERVICE BUREAU - WE ARE AN ENGINEERING SOLUTION PRODUCTION CENTRE FOR ADDITIVE MANUFACTURING. With a sound engineering solution approach to produce Additive Manufactured the Digital Manufacturing Centre is a positive disruptor to the additive manufacturing industry. Servicing various sectors for Metal and Polymer including powder bed laser sintering, FDM, SLA etc. the DMC has a full on site production supply chain to enable sustainable high quality production finished qualified components to the required quality standard. Show less WE ARE NOT A 3D PRINTING SERVICE BUREAU - WE ARE AN ENGINEERING SOLUTION PRODUCTION CENTRE FOR ADDITIVE MANUFACTURING. With a sound engineering solution approach to produce Additive Manufactured the Digital Manufacturing Centre is a positive disruptor to the additive manufacturing industry. Servicing various sectors for Metal and Polymer including powder bed laser sintering, FDM, SLA etc. the DMC has a full on site production supply chain to enable sustainable high quality production… Show more WE ARE NOT A 3D PRINTING SERVICE BUREAU - WE ARE AN ENGINEERING SOLUTION PRODUCTION CENTRE FOR ADDITIVE MANUFACTURING. With a sound engineering solution approach to produce Additive Manufactured the Digital Manufacturing Centre is a positive disruptor to the additive manufacturing industry. Servicing various sectors for Metal and Polymer including powder bed laser sintering, FDM, SLA etc. the DMC has a full on site production supply chain to enable sustainable high quality production finished qualified components to the required quality standard. Show less
-
-
-
3T Additive Manufacturing Ltd
-
United Kingdom
-
Mechanical Or Industrial Engineering
-
1 - 100 Employee
-
CEO
-
Mar 2019 - May 2020
• Appointed CEO to manage Board and shareholder communications at £11M turnover 3D Printing Metal and Polymer Production Components Manufacturer for the Aerospace, Automotive, Oil and Gas Sectors
-
-
Director of Operations
-
Sep 2014 - Mar 2019
• Fully accountable for P&L of £11M, developed and executed annual operations strategy and budget to support aggressive business growth strategy of 20% year on year through continued business process and service level improvements • Directed Safety, Quality, Sales, Marketing and Manufacturing operations, consistently met targets of 10% EBIT and 97% OTD and strengthened the added value Supply Chain offering to key customers • Led, mentored and performance managed team of 100 people… Show more • Fully accountable for P&L of £11M, developed and executed annual operations strategy and budget to support aggressive business growth strategy of 20% year on year through continued business process and service level improvements • Directed Safety, Quality, Sales, Marketing and Manufacturing operations, consistently met targets of 10% EBIT and 97% OTD and strengthened the added value Supply Chain offering to key customers • Led, mentored and performance managed team of 100 people including senior managers both daily and strategic performance management with focus on safety, productivity, quality and delivery • Innovated site wide people development programmes for staff at all levels including apprentice and graduate schemes • Improved business EBIT margins from breakeven to £1.5m profit within two years through strategic growth development • Drove continuous improvement programmes across production facilities using Six Sigma techniques, e.g. increased manufacturing OTIF from 50% to 97% and RFT from 85% to 98% • Mentored team in various lean manufacturing and Six Sigma techniques to improve RFT of products from 60% to 99% • Transformed organizational structure and sales operations from internally focused to customer- and delivery- centric, increased order volume from 40% to 300% inside 12 months • Re-engineered key processes to drive efficiencies • Developed full post processing capability in house and through supply chain including heat treatment, multi axis machining, hand finishing and inspection, immediately doubled metal business unit turnover • Specified and oversaw implementation of companywide ERP system • Increased corporate exposure to existing and new customers by 150% through rebranding the company from 3T RPD ltd to 3T Additive Manufacturing ltd and executing a new marketing strategy pivoting away from traditional prototyping networks to production ready customers
-
-
-
CD Power Pty Ltd
-
Australia
-
Machinery Manufacturing
-
1 - 100 Employee
-
General Manger - Eastern Australia
-
May 2013 - Aug 2014
• Led multi-location Manufacturing Operations, Service, Parts and Aftermarket Development for $45M revenue Oil and Gas Mining Power Generation Manufacturing and After Sales Service Centre • Managed P&L of $10M and operational budget of $6M, improved EBIT margins from 3% to 11% in 6 months • Developed and executed business strategy to increase turnover in manufacturing and aftermarket by 300% by increasing portfolio of services offered • Increased site capacity by 300% in 5 months to… Show more • Led multi-location Manufacturing Operations, Service, Parts and Aftermarket Development for $45M revenue Oil and Gas Mining Power Generation Manufacturing and After Sales Service Centre • Managed P&L of $10M and operational budget of $6M, improved EBIT margins from 3% to 11% in 6 months • Developed and executed business strategy to increase turnover in manufacturing and aftermarket by 300% by increasing portfolio of services offered • Increased site capacity by 300% in 5 months to meet increased sales demand and changing customer requirements, improved manufacturing and service centre utilization from 60% to 95% • Oversaw customer relationships, chaired key account customer meetings on sales, operations and technical issues, personally managed relationships with Santos, Arrow Energy, AGL, Halliburton, NACAP • Project managed the engineering, design and launch of new Gas/Diesel Generator range ‘Endeavour’ with a design for assembly methodology that cut product cost by 30% and drove sales by 500% over a 5-year contractual period Show less • Led multi-location Manufacturing Operations, Service, Parts and Aftermarket Development for $45M revenue Oil and Gas Mining Power Generation Manufacturing and After Sales Service Centre • Managed P&L of $10M and operational budget of $6M, improved EBIT margins from 3% to 11% in 6 months • Developed and executed business strategy to increase turnover in manufacturing and aftermarket by 300% by increasing portfolio of services offered • Increased site capacity by 300% in 5 months to… Show more • Led multi-location Manufacturing Operations, Service, Parts and Aftermarket Development for $45M revenue Oil and Gas Mining Power Generation Manufacturing and After Sales Service Centre • Managed P&L of $10M and operational budget of $6M, improved EBIT margins from 3% to 11% in 6 months • Developed and executed business strategy to increase turnover in manufacturing and aftermarket by 300% by increasing portfolio of services offered • Increased site capacity by 300% in 5 months to meet increased sales demand and changing customer requirements, improved manufacturing and service centre utilization from 60% to 95% • Oversaw customer relationships, chaired key account customer meetings on sales, operations and technical issues, personally managed relationships with Santos, Arrow Energy, AGL, Halliburton, NACAP • Project managed the engineering, design and launch of new Gas/Diesel Generator range ‘Endeavour’ with a design for assembly methodology that cut product cost by 30% and drove sales by 500% over a 5-year contractual period Show less
-
-
-
MAN DIESEL & TURBO UK LTD
-
United Kingdom
-
Machinery Manufacturing
-
Operations Manager
-
Oct 2006 - Jan 2013
• Managed production engineering and customer services operations at £25M turnover Engine Production and Aftersales Service Centre supplying major customers e.g. MoD, British Rail, Worldwide Export, Power Generation with full P&L accountability • Led team of 75, supervised new engine manufacturing, field service, spare parts and aftermarket processing component/engine strip, inspection, build, testing, paint shop, machine shop, fabrication shop, electrical and stores, materials control, site… Show more • Managed production engineering and customer services operations at £25M turnover Engine Production and Aftersales Service Centre supplying major customers e.g. MoD, British Rail, Worldwide Export, Power Generation with full P&L accountability • Led team of 75, supervised new engine manufacturing, field service, spare parts and aftermarket processing component/engine strip, inspection, build, testing, paint shop, machine shop, fabrication shop, electrical and stores, materials control, site maintenance, procurement, logistics, HR • Developed harmonious working relationship with unions, negotiated with shop floor representatives • Innovated new product and productivity strategy such as flexible production planning, new product offering all MAN PrimeServ portfolio and used spares warehouse which increased sales by 64% in four years • Project managed introduction of new manufacturing processes to reduce lead-time by 50% and increase product service offering across product range e.g. cylinder heads, turbochargers, machining, fabrication, engine build, test beds etc • Managed company response to £ multi-million new business tenders and quotations, negotiated contracts directly with existing and potential customers • Revised budget spend and internal processes and introduced new capacity planning tools to deliver 5% year on year savings on site operational costs based of sales revenue • Drove continuous improvement of quality management system to improve training, in-process control etc. • Authored a complete HSE and environmental management system to ensure compliance with regulations • Extended operational production life by implementing apprentice-to-degree training programmes in collaboration with the University of Essex Show less • Managed production engineering and customer services operations at £25M turnover Engine Production and Aftersales Service Centre supplying major customers e.g. MoD, British Rail, Worldwide Export, Power Generation with full P&L accountability • Led team of 75, supervised new engine manufacturing, field service, spare parts and aftermarket processing component/engine strip, inspection, build, testing, paint shop, machine shop, fabrication shop, electrical and stores, materials control, site… Show more • Managed production engineering and customer services operations at £25M turnover Engine Production and Aftersales Service Centre supplying major customers e.g. MoD, British Rail, Worldwide Export, Power Generation with full P&L accountability • Led team of 75, supervised new engine manufacturing, field service, spare parts and aftermarket processing component/engine strip, inspection, build, testing, paint shop, machine shop, fabrication shop, electrical and stores, materials control, site maintenance, procurement, logistics, HR • Developed harmonious working relationship with unions, negotiated with shop floor representatives • Innovated new product and productivity strategy such as flexible production planning, new product offering all MAN PrimeServ portfolio and used spares warehouse which increased sales by 64% in four years • Project managed introduction of new manufacturing processes to reduce lead-time by 50% and increase product service offering across product range e.g. cylinder heads, turbochargers, machining, fabrication, engine build, test beds etc • Managed company response to £ multi-million new business tenders and quotations, negotiated contracts directly with existing and potential customers • Revised budget spend and internal processes and introduced new capacity planning tools to deliver 5% year on year savings on site operational costs based of sales revenue • Drove continuous improvement of quality management system to improve training, in-process control etc. • Authored a complete HSE and environmental management system to ensure compliance with regulations • Extended operational production life by implementing apprentice-to-degree training programmes in collaboration with the University of Essex Show less
-
-
-
FläktGroup
-
Germany
-
Industrial Machinery Manufacturing
-
700 & Above Employee
-
Manufacturing Area Manager
-
Apr 2004 - Sep 2006
Flaktwoods produces air movement equipment such as fabricated fans/acoustic silences for various construction and air system distribution customers. Applications are for cooling systems, car parks, industrial ventilation. I was responsible for the Primary facility supplying made in our purchased parts direct to line side. My remit covered machine shop, powder coating shop, acoustic build, fabrication, inspection, goods inwards, stores and the management of sub contract metal coating… Show more Flaktwoods produces air movement equipment such as fabricated fans/acoustic silences for various construction and air system distribution customers. Applications are for cooling systems, car parks, industrial ventilation. I was responsible for the Primary facility supplying made in our purchased parts direct to line side. My remit covered machine shop, powder coating shop, acoustic build, fabrication, inspection, goods inwards, stores and the management of sub contract metal coating companies. My broad remit to supply 100% supply allowed me to work closely with internal and external suppliers and therefore involved me in leading various improvement initiatives. Due to the nature of the business headcount management was key to ensure all three shifts were adequately resourced at all times. This involved many training initiatives to break down the processes to individual steps and therefore reduce the training requirements without compromising quality or delivery. I was also responsible for the transition of the primary production facility to a new site within Colchester. This included the introduction of new plasma welding and duct production equipment. Show less Flaktwoods produces air movement equipment such as fabricated fans/acoustic silences for various construction and air system distribution customers. Applications are for cooling systems, car parks, industrial ventilation. I was responsible for the Primary facility supplying made in our purchased parts direct to line side. My remit covered machine shop, powder coating shop, acoustic build, fabrication, inspection, goods inwards, stores and the management of sub contract metal coating… Show more Flaktwoods produces air movement equipment such as fabricated fans/acoustic silences for various construction and air system distribution customers. Applications are for cooling systems, car parks, industrial ventilation. I was responsible for the Primary facility supplying made in our purchased parts direct to line side. My remit covered machine shop, powder coating shop, acoustic build, fabrication, inspection, goods inwards, stores and the management of sub contract metal coating companies. My broad remit to supply 100% supply allowed me to work closely with internal and external suppliers and therefore involved me in leading various improvement initiatives. Due to the nature of the business headcount management was key to ensure all three shifts were adequately resourced at all times. This involved many training initiatives to break down the processes to individual steps and therefore reduce the training requirements without compromising quality or delivery. I was also responsible for the transition of the primary production facility to a new site within Colchester. This included the introduction of new plasma welding and duct production equipment. Show less
-
-
-
SPX Hydraulic Technologies
-
United States
-
Machinery Manufacturing
-
1 - 100 Employee
-
Production Project Manager
-
Jul 2002 - Jan 2004
SPX Fluidpower produces Hydraulic and Pneumatic actuating equipment as either a second tier supplier to truck suppliers or medical equipment manufactures or a first tier supplier to the rail network. This includes grade one safety critical rail crossing barriers, points and train break systems. I was responsible for supporting three production cells for the Quality, Delivery & Output of 120 employees. My duties included to find, evaluate & manage reduction of waste to increase… Show more SPX Fluidpower produces Hydraulic and Pneumatic actuating equipment as either a second tier supplier to truck suppliers or medical equipment manufactures or a first tier supplier to the rail network. This includes grade one safety critical rail crossing barriers, points and train break systems. I was responsible for supporting three production cells for the Quality, Delivery & Output of 120 employees. My duties included to find, evaluate & manage reduction of waste to increase operational efficiency. During my time at SPX Fluidpower I Implemented 5s, Kaizen & cellular methods for One-Piece flow which, increased productivity 38%. I was responsible as the UK Project Manager to move production from its Romford facility to Rockford, USA while including a finished product warehouse in Holland. This project was complete with seamless transition supply to our end customers. Show less SPX Fluidpower produces Hydraulic and Pneumatic actuating equipment as either a second tier supplier to truck suppliers or medical equipment manufactures or a first tier supplier to the rail network. This includes grade one safety critical rail crossing barriers, points and train break systems. I was responsible for supporting three production cells for the Quality, Delivery & Output of 120 employees. My duties included to find, evaluate & manage reduction of waste to increase… Show more SPX Fluidpower produces Hydraulic and Pneumatic actuating equipment as either a second tier supplier to truck suppliers or medical equipment manufactures or a first tier supplier to the rail network. This includes grade one safety critical rail crossing barriers, points and train break systems. I was responsible for supporting three production cells for the Quality, Delivery & Output of 120 employees. My duties included to find, evaluate & manage reduction of waste to increase operational efficiency. During my time at SPX Fluidpower I Implemented 5s, Kaizen & cellular methods for One-Piece flow which, increased productivity 38%. I was responsible as the UK Project Manager to move production from its Romford facility to Rockford, USA while including a finished product warehouse in Holland. This project was complete with seamless transition supply to our end customers. Show less
-
-
-
Southernprint Ltd
-
Printing Services
-
1 - 100 Employee
-
Quality/Manufacturing Improvement Manager
-
Sep 2001 - Jun 2002
Southerprint Ltd are part of the Newsquest group and their core business is printing and binding magazines such as Horse and Hound, Amateur Photographer and Front Magazine. I was responsible for defining & developing the Quality Management System and deploying Lean Manufacturing across the facility. In that time I introduced BSI 9001:2000 and many improvements such as a customer complaints procedure with a corrective/preventative actions included before they are closed off. I… Show more Southerprint Ltd are part of the Newsquest group and their core business is printing and binding magazines such as Horse and Hound, Amateur Photographer and Front Magazine. I was responsible for defining & developing the Quality Management System and deploying Lean Manufacturing across the facility. In that time I introduced BSI 9001:2000 and many improvements such as a customer complaints procedure with a corrective/preventative actions included before they are closed off. I also included KPI's across the site to control quality, customer satisfaction and delivery. Show less Southerprint Ltd are part of the Newsquest group and their core business is printing and binding magazines such as Horse and Hound, Amateur Photographer and Front Magazine. I was responsible for defining & developing the Quality Management System and deploying Lean Manufacturing across the facility. In that time I introduced BSI 9001:2000 and many improvements such as a customer complaints procedure with a corrective/preventative actions included before they are closed off. I… Show more Southerprint Ltd are part of the Newsquest group and their core business is printing and binding magazines such as Horse and Hound, Amateur Photographer and Front Magazine. I was responsible for defining & developing the Quality Management System and deploying Lean Manufacturing across the facility. In that time I introduced BSI 9001:2000 and many improvements such as a customer complaints procedure with a corrective/preventative actions included before they are closed off. I also included KPI's across the site to control quality, customer satisfaction and delivery. Show less
-
-
-
-
Six Sigma/Lean Manufacturing Engineer
-
Apr 1997 - Aug 2001
Compair Reavell are a market leader in reciprocating compressors serving various dealership, government and private customers. The facility had 250 people including processes such as a foundry, machine shop and compressor built and test. I was responsible for exceeding business targets for Production & Manufacturing Engineering processes which, included a lot of work developing Kanbans and Faxbans for ordering parts. I also worked extensively on improving our ERP system for order… Show more Compair Reavell are a market leader in reciprocating compressors serving various dealership, government and private customers. The facility had 250 people including processes such as a foundry, machine shop and compressor built and test. I was responsible for exceeding business targets for Production & Manufacturing Engineering processes which, included a lot of work developing Kanbans and Faxbans for ordering parts. I also worked extensively on improving our ERP system for order management and lead time improvement. I also managed all aspects of continuous production improvement & increased profit of the business. In this time I became certified Lean Manufacturing Instructor and Six Sigma Blackbelt, Greenbelt and Yellowbelt. As part of my Six Sigma Blackbelt certification I improved purchased parts OTD to system required date by 80%. This resulted in the company overall OTD improving by 60%. I also lead a team to develop true policy deployment and value steam mapping which, became the platform for many improvement initiatives.
-
-
Apprentice/Engineer
-
Sep 1990 - Mar 1997
Carried out apprenticeship to HNC, mechanical engineering level. Worked to build, configure, test and install compressors on site. I gained much valued experience for engineering and working on the shop floor which, inspired me to make improvements in my next role as Six Sigma/Lean Manufacturing engineer.
-
-
Education
-
University Campus Suffolk
HND - Mechanical Engineering
Community
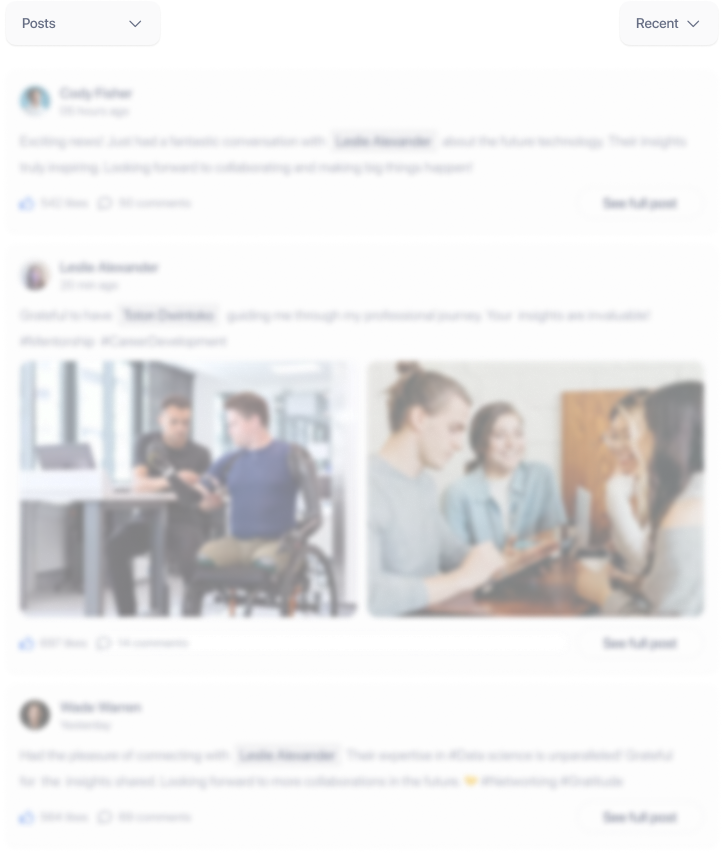