Nigel May
Quality Manager at Nammo AS- Claim this Profile
Click to upgrade to our gold package
for the full feature experience.
Topline Score
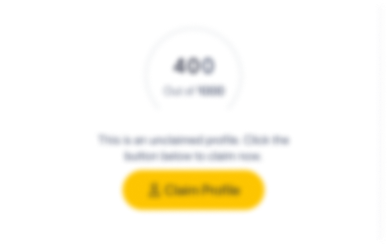
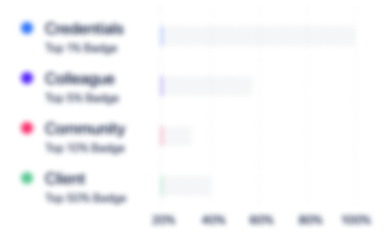
Bio


Experience
-
Nammo AS
-
Defense & Space
-
100 - 200 Employee
-
Quality Manager
-
Mar 2009 - Present
Responsible for Quality Control & Product Assurance activities at the Westcott facility now owned by Nammo (formerly Moog and AMPAC ISP). Maintaining the site's AS9100 Rev D registration. Represent the company at meetings and reviews with customers and suppliers on Quality matters Ensure the end product and production activities meet the customer's requirements. Just successfully completed the transition from a multi-site to single site certification, which involved effectively going through the whole AS9100 audit process as though we had never been certified before, plus a change of third party auditor at the same time. Show less
-
-
-
Eastman Kodak Company
-
Manufacturing
-
700 & Above Employee
-
Business Support
-
Jan 2007 - Dec 2008
This role includes my previous functions of Quality System Manager, Training Manager and Site Capital Co-ordinator, however the Quality and training roles are now expanded to include the paper manufacturing department as well as the central engineering group.A key function of this role was to streamline the processes used and ensure a common approach is used across the departments to reduce the administrative burden on the departments. Other functions of the role are:Ensuring KPI data is up to date and reported.Facilitate / chair management meetings, HSE standard reviews, HSE committee meetingsMonitor and report spend on orders for key services and materials.Owner of the reliability data for paper manufacturing.Assisting any member of the management team with additional tasks, Key contact for roll out of new time recording system for all employees including delivering of user training.Raw materials buying for paper manufacturing department on a stand in basis. Show less
-
-
Quality System & Training Manager
-
Apr 2005 - Dec 2006
As Quality System ManagerChair management system review meetings and report status of the quality system to management.Lead one site audit per year and take part in others as required.Department key contact for both internal and external audits.Ensure that key department documents & Service Level Agreements are reviewed and updated on schedule.Progress open corrective actions through to closure.As Training ManagerAgree the standard training plan with the management team each year for all employees.Ensure that every department member has an individually tailored training plan in place each year.Ensuring that training records are maintained for each employee.Arrange training with external suppliers as required.Regularly reporting to senior management on the training progress against plan and spend on the training budget.At the end of 2005 I also took on the role of site capital budget co-ordinator. This involved:Setting up projects in SAP and a separate project reporting system.Making sure that the project managers keep their schedule and cost forecasts up to date in the systemProviding monthly reports to senior management on total capital budget spend against plan.Ensuring that projects are capitalised and closed in a timely manner.During 2006 & 2007 I was the cost control engineer on a major restructuring programme at the site ($50M). The project was completed within budget and on schedule. Show less
-
-
Special Projects
-
Oct 2004 - Mar 2005
Implement a dashboard process within the engineering technical group to communicate progress on key tasks at regular meetings between engineering management and customersManage project to relocate engineering team to new offices on site (Completed on time and within budget).Manage project to refurbish office for site finance team and relocate them to that office with minimum impact on their year end close out activities.Part of team charged with closing down two production departments, ensuring that vacated areas were left safe and that fixed assets were dealt with correctly in accordance with accounting procedures. Show less
-
-
Maintenance Coordinator
-
May 2000 - Sep 2004
Owner of the planned maintenance system.Negotiating engineering opportunities with production managers.Planning and co-ordination of all engineering stops.Owner of OEE data and reporting it at worldwide level.Key member of site team for the migration of maintenance data from legacy system into SAP R3.Allocation of maintenance budget to engineering, monitoring of spend against budget and reporting spend to senior management.Manage small capital projects (<$100k).Department lead for upgrade from SAP R3 to R4.6.Reliability Centred Maintenance facilitator.Department lead for transfer of engineering inventory into SAP. Show less
-
-
Project planning and cost control engineer
-
May 1995 - Apr 2000
At Kodak's Harrow site, working in the projects division. Production of plans for all levels of capital investment from top level management summaries down to detailed installation schedules.Cost control included initial production of budget for capital expenditure approval to the issuing, monitoring and reporting of spend through the life of the project.As an additional task I was responsible for the planning and coordination of major engineering shutdowns within the production departments across the site. Show less
-
-
Mechanical Craftsman
-
Sep 1991 - Apr 1995
-
-
Apprentice
-
Jul 1987 - Aug 1991
One years off the job training followed by three years on the job moving through workshops and technical offices within the company. City & Guilds Mechanical Craft Studies and Basic CAD/CAM plus BTEC Ordinary National Certificate in Engineering completed on a day release basis during this time
-
-
Education
-
University of Hertfordshire
BEng (Hons), Manufacturing Systems Engineering -
Nower Hill High School
Community
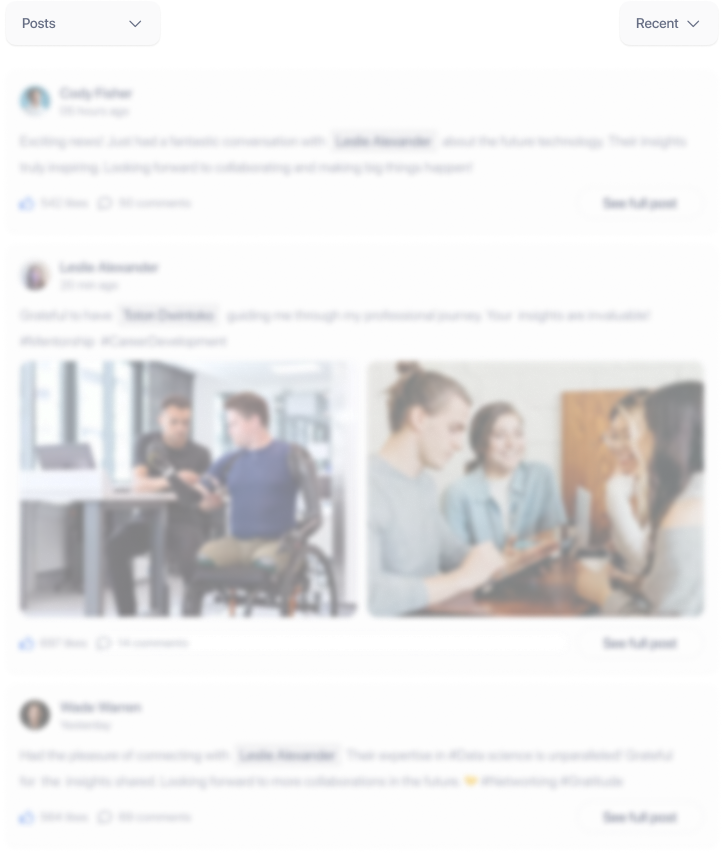