Nigel Brookes
Head Of Production at MiniTec UK Ltd- Claim this Profile
Click to upgrade to our gold package
for the full feature experience.
Topline Score
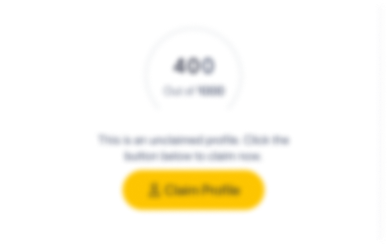
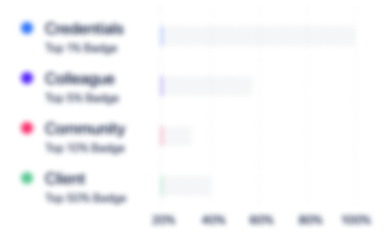
Bio


Credentials
-
Lean Organisation Management Technique
vision2learn for businessJun, 2015- Nov, 2024 -
NVQ level 4 In Management
-
Experience
-
MiniTec UK Ltd
-
United Kingdom
-
Mechanical Or Industrial Engineering
-
1 - 100 Employee
-
Head Of Production
-
Apr 2021 - Present
MiniTec UK provides businesses with bespoke industrial solutions using the MiniTec aluminium profile solution, complementing facilities around the world. MiniTec UK provides businesses with bespoke industrial solutions using the MiniTec aluminium profile solution, complementing facilities around the world.
-
-
-
SCHLEIFRING SYSTEMS LIMITED
-
United Kingdom
-
Appliances, Electrical, and Electronics Manufacturing
-
1 - 100 Employee
-
Team Leader
-
Nov 2017 - Mar 2021
Responsibilities: • To optimise resource and capacity to meet daily/weekly targets • Progress production orders across all department to meet customer expectations • Responsible for the Health, Safety and Welfare of all employees • Manage staff’s development and performance • Liaise with key departments to resolve any problems which arises • Deliver quality in line with company standards and expectations Achievements: • Part of the operations leadership team which has improved OTIF by 35% by simplifying manufacturing processes and inducing Gantt chart production planning tool • Reduced number of RMA by 50% • Improved a key customer supply by 100% by creating SOP’s • Implemented a excel based planning tool which is used across five functional department • Solved an existing/ long term quality problems by using 8D, Saving the company £72k • Planned along side the Operations Director the strategy to close the UK plant by the end of 2020. Show less
-
-
-
Thinking Space Systems Ltd
-
United Kingdom
-
Furniture
-
1 - 100 Employee
-
Production Manager
-
Aug 2015 - Sep 2017
Responsibilities - Organise and lead the planning and implementation of the production after sales processes - Manage Health, Safety and Welfare of the operation team - Construct KPI's for the production team - Maintain and build relationships with key supplier - Identify and source project specific subcontract parts - Manage company ISO 9001 requirements - Create and execute production schedule Achievement - Introduce waste management to achieve 100% recycling - Introduce Kanban to manage and reduce stock holding - Work with supplier to achieve just in time supply - Implement apprenticeship program Show less
-
-
-
Emerson
-
United States
-
Industrial Machinery Manufacturing
-
700 & Above Employee
-
Production Supervisor
-
Feb 2015 - Jul 2015
Responsibilities: • To optimise resource and capacity to meet daily/weekly targets • Responsible for the Health, Safety and Welfare of all employees on second shift • Manage staff’s development and performance • Liaise with key departments to resolve any problems which arises • Deliver quality in line with company standards and expectations • Maintain and achieve company’s KPI’s • Ensure all equipment is in good safe working order Responsibilities: • To optimise resource and capacity to meet daily/weekly targets • Responsible for the Health, Safety and Welfare of all employees on second shift • Manage staff’s development and performance • Liaise with key departments to resolve any problems which arises • Deliver quality in line with company standards and expectations • Maintain and achieve company’s KPI’s • Ensure all equipment is in good safe working order
-
-
-
CPI - Compressor Products International
-
United States
-
Oil and Gas
-
100 - 200 Employee
-
Operations Manager
-
Oct 2012 - Jan 2015
Responsibilities: • I reported to the VP operations based in Houston Texas. I managed seven direct reports and overall 70 employees in three locations• Responsible for the Health, Safety and Welfare of all employees in the UK• Responsible for supply chain in the UK• Managed all aspects of staff’s development and performance • Ensure we satisfy our customers needs by meeting their delivery expectations• Ensure our ISO 9001 and 14001 meet external and internal audit schedules• Manage internal QA processes so we delivered the right quality first time every time• Responsible for meeting monthly budget and reducing costs• Liaise with other European plants to improve production processes and capacity• Put forward recommendations for capital projects • Conducted presentations on business performance Achievements:• Investigated and put forward capital project of £400k for three European Plants. This resulted in the purchase of three CNC lathes to increase capacity by 100% and reduce manufacturing product cost by £150K a year.• By introducing a committee based safety culture and implementing a number of key initiatives, we have reduced our injuries rate to zero and greatly reduce our first aid incidents. This resulted in us receiving the President Safety award in 2014• Utilised additional CNC milling resource with a small amount of investment to increase packing ring cell capacity by 150% when necessary.• Increased our moulding capacity by improving the processes to achieve a 30% increase and £100,000 a year saving.• By implementing root cause analysis (A3 and fish bone) I have been able to reduce customer complaints to less than 1% of total orders• Introduced a preventative maintenance program which has reduced critical equipment breakdown to less than 5%• By working with a company who understood our requirement, the recycling rate was increased to 95% with a cost saving of £6000 per year. Show less
-
-
Production and Engineering Manager
-
Mar 2007 - Nov 2012
Responsibilities: • I managed four direct reports and overall 40 employees in two locations• Manage the Health & Safety of all my employees• Manage all staff’s development and performance • Meet agreed customer delivery times• Manage internal processes so we delivered right quality first time every time• Put forward recommendations for capital projects • Maintained internal design standards• Provided specialized technical support to various areas of the business• Maintain product release plans Show less
-
-
QA and Engineering Manager
-
Jul 1997 - Mar 2007
-
-
QA and Engineering Supervisor
-
Mar 1991 - Jul 1997
-
-
Product Engineer
-
Jan 1988 - Mar 1991
-
-
Education
-
Test valley stockbridge
Community
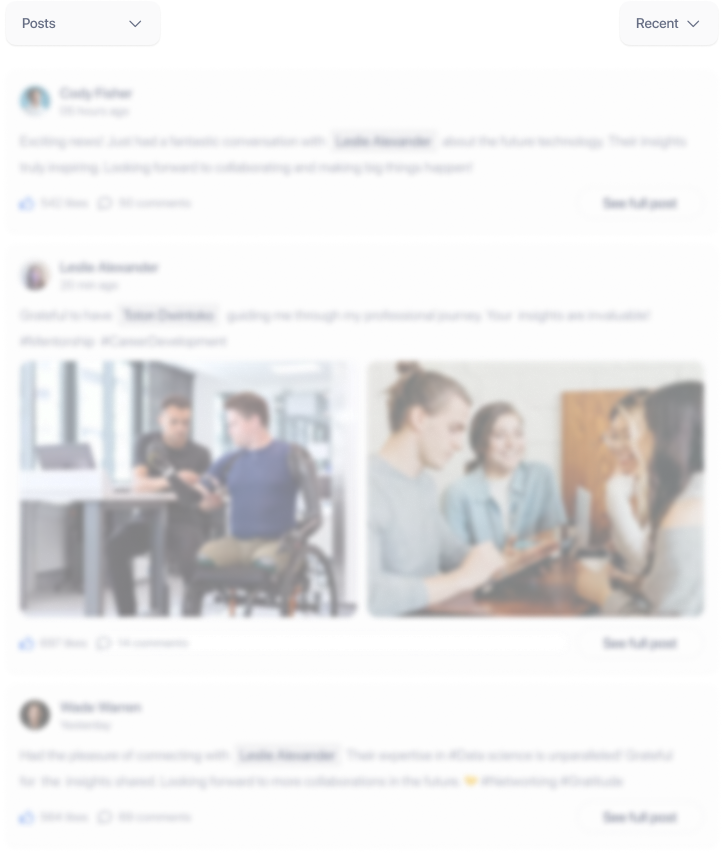