Niema Lemzabi
Supply Chain Director - Label Vie at LabelVie- Claim this Profile
Click to upgrade to our gold package
for the full feature experience.
-
English Full professional proficiency
-
French Native or bilingual proficiency
-
Arabic Native or bilingual proficiency
Topline Score
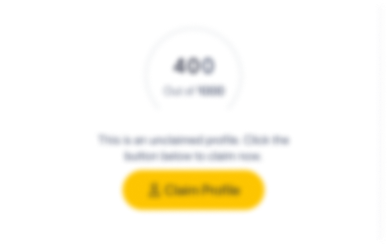
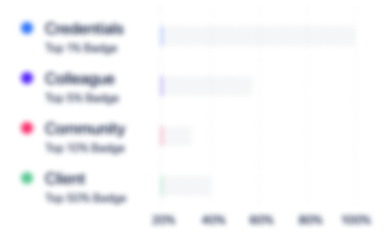
Bio


Experience
-
LabelVie
-
Morocco
-
Retail Groceries
-
700 & Above Employee
-
Supply Chain Director - Label Vie
-
Jan 2022 - Present
Responsible of Logistics Management (Material planning and procurement, Management of logistic hub (75000 pallets spot), Import and export operations) Key achievements: - Development of vision, objectives and road map - Development of the organisation vision - Definition/Implementation of monitoring and guidance system (Meetings, KPI....) - Définition of the platform masterplan (capacity, planning, design...) - Cost reduction through KPI improvment - Contribution to the company strategic projects (Digital factory, export, franchise.....) - Support to Cote d'Ivoire operations - People coaching to reach their full potentiel Show less
-
-
-
RYB Building
-
Rabat
-
General manager
-
Jan 2013 - Present
Creation and management of a real estate development and construction company Creation and management of a real estate development and construction company
-
-
-
Safran
-
France
-
Aviation and Aerospace Component Manufacturing
-
700 & Above Employee
-
Operations manager - SAFRAN
-
Dec 2015 - Dec 2021
Responsible of plant operations (engineering, manufacturing, supply chain, program management technical, lean), +1300 people. Assignment objective is to meet customers needs (quality, on time delivery, projects), comply with aerospace regulatory requirements, while driving down cost thanks to the development, deployment and implementation of strong strategies and the empowerment of employees. Key achievements: - Development of the vision, objectives and strategies to achieve compelling business need - Organisation redesign in line with strategies - KPI's improvement (on time delivery, quality, cost, stocks..) - Sucessfull audits (quality, safety, MRP²...) - Projects delivery (SAP implementation...) Show less
-
-
-
-
Business consulting and training (free lance)
-
Jun 2013 - Nov 2015
Assisting customers to develop their performance and competitiveness through the implementation of customized systems and training programs - Strategic planning (development of the vision, objectives and strategies) to achieve compelling business need - Leadership of multifunctional teams - Coaching and capabilities development (people management skills) - Organization assessment and redesign, change management - Supply chain management (Customer service, Finished product planning, materials sourcing, export, warehouse management, storeroom management...) - Operations management (operation, quality, safety, cost...) - Expertise in manufacturing programs (Process reliability, lean management, HS&E, quality, TPM, productivity and cost) - End to end Project management - Systems and processes reengineering Show less
-
-
-
Procter & Gamble
-
United States
-
Manufacturing
-
700 & Above Employee
-
Liquids Operation Director
-
Feb 2012 - Sep 2012
Full responsibility of Ace and Mr Proper plant operations (6 operation technologies, supply chain, warehouse, technical packaging), one site, + 100 people, member of the sites leadership team.Assignment objective is to deliver quality product, on time at the right cost while improving employee morale and plant standards through the development, deployment and implementation of strong strategies and detailed plans. Key deliverables were organization redesign, systems implementation, projects delivery, reliability and product availability improvement, savings implementation and successful auditsKey achievements:- Development of the vision, objectives and strategies to achieve compelling business need- Lean manufacturing implementation - KPI's improvement (reliability, cost, productivity, finished product availability, inventories, stocks..)- 15% manufacturing cost reduction and 20% productivity improvement- Good safety and quality results - People management (hiring, training, performance and careers management) Show less
-
-
Technical Director
-
Oct 2009 - Jan 2012
Responsible of the engineering organization (Projects management, Health, safety and environment program, Capital management, storeroom management) of P&G plants, 2 sites, 40 people, member of the sites leadership team)Key Achievements include:- Development of the vision, objectives and strategies to achieve compelling business need at plant and department level- Organization restructuring (storeroom and Safety)- Vertical startup (on time, 15% capital reduction, quality, process reliability...) of different projects (New equipments to produce new formula, new packing lines….)- Improvement of the score of different audits (HS&E, construction, capital, internal controls)- Update of the plant master plan (10 years)- 10% manufacturing expense reduction- Storeroom indicators improvement (spares availability, inventory…)- People management (hiring, training, performance and careers management)- Plants organization training Show less
-
-
Supply Chain Director
-
Apr 2005 - Sep 2009
Responsible of the supply chain organization of P&G plants (Finished product planning, material planning, initiatives management, exports operation and warehouse management), 2 sites, 3 brands, + 100 peoples, 10000 pallets spot, member of the sites leadership teamKey achievements:- Development of the vision, objectives and strategies to achieve compelling business need - Organization restructuring to support new challenges, new markets and volume increase- Product availability improvement for local and export markets- Cash optimization thanks to inventory reduction- > 100 initiatives delivered with excellence (on time, with no remnant and no out of stocks)- 30% manufacturing expense decrease (productivity improvement, space/transport optimization - >1.5 MM$ savings/year on freight and initiatives- “A “classification (high performing companies) in the Categorization Program initialized by Moroccan Customs.- Worldwide award of customs to P&G Morocco- Lean manufacturing implementation- Step change in the score of the MRP2 (planning systems) audit score and internal control- Strong safety and quality systems in the warehouse area - Development of a new training system and new procedures to ensure business continuity and great results- People management (hiring, training, performance and careers management) Show less
-
-
Supply Chain Manager
-
Jan 2002 - Mar 2005
Supply chain manager of Fabric Care department (Finished product planning, material planning, initiatives, export planning & logistic and warehouse management).
-
-
Polybags department manager
-
Mar 2000 - Dec 2001
Department manager - Polybags department: (10 packing machines).
-
-
Hair Care Department Manager
-
Aug 1998 - Feb 2000
Department manager - Hair Care department (manufacturing and packing).
-
-
Hair Care Process Engineer
-
Aug 1996 - Jul 1998
Process engineer - Hair Care department (manufacturing and packing).
-
-
Education
-
Ecole Mohamadia des ingenieurs
Engineer, Industriel engineering -
Classes préparatoires
Community
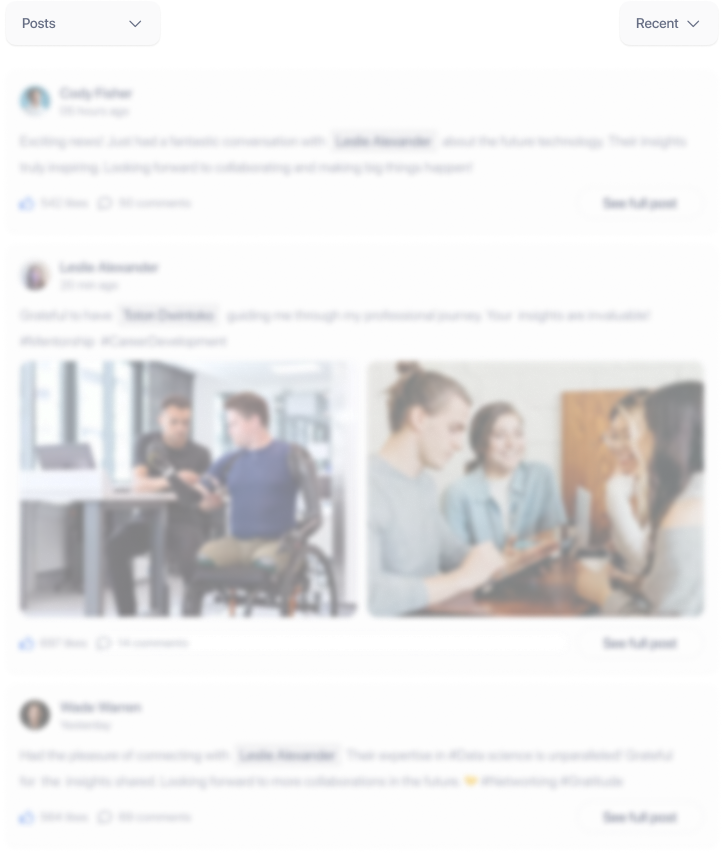