Nick Walter
VP of Operations - Las Vegas at The Fi Company - Las Vegas- Claim this Profile
Click to upgrade to our gold package
for the full feature experience.
Topline Score
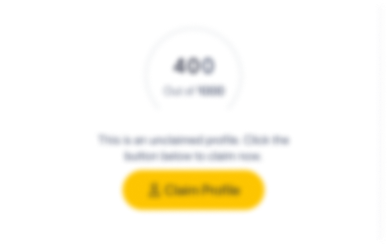
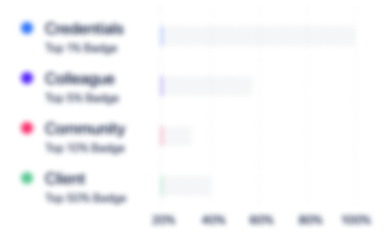
Bio


Experience
-
The Fi Company - Las Vegas
-
United States
-
Gambling Facilities and Casinos
-
1 - 100 Employee
-
VP of Operations - Las Vegas
-
Aug 2021 - Present
Las Vegas, Nevada, United States
-
-
-
-
Director of Global Sales
-
Oct 2018 - Aug 2021
Las Vegas, NV
-
-
-
Gamesman Inc
-
United States
-
General Manager - USA
-
Jan 2011 - Sep 2018
www.gamesman.co.uk • Responsible for the ground-up development & day to day management of operational, sales & service facility in North America, recruiting a team of 13 persons and with annual sales revenue responsibility of $34m. P&L and budget responsibility for the Business Unit. • Specify, justify & project manage capital installations during site development. • Direct sales & after-sales responsibility for customer accounts in North America & Australia. Responsibility for establishing & supporting… Show more • Responsible for the ground-up development & day to day management of operational, sales & service facility in North America, recruiting a team of 13 persons and with annual sales revenue responsibility of $34m. P&L and budget responsibility for the Business Unit. • Specify, justify & project manage capital installations during site development. • Direct sales & after-sales responsibility for customer accounts in North America & Australia. Responsibility for establishing & supporting 3rd-party service vendor in Australia. Delivered double-digit percentage year on year revenue growth in North America. • Responsibility for Asia supply chain coordination & development of low-cost country manufacturing opportunities. • Management of US inventory to ensure support of customer requirements whilst meeting internal financial metrics. Ownership for supply chain management at the global level for 3 primary customers. • Support N. American customer visits & audits at Gamesman China facility and other Asia based supplier visits. • Primary contact for technical support in North America; worked with customers to develop technical product solutions, managing the process from concept through to production. • Developed an operational team which won repeat, year-on-year awards from multiple customers for Quality, On-Time Delivery & Customer Service performance. • Transitioned the business unit successfully from Private ownership to being part of a publically traded US Corporation, implementing new processes and procedures, adjusting metrics and driving the necessary change to adopt new practices. Show less
-
-
-
-
Manufacturing and Operations Manager
-
Aug 2007 - Dec 2010
• Responsibility for the all aspects of UK Manufacturing, Purchasing and Site Operations. • Implementation of modern manufacturing techniques to UK injection moulding and assembly operation to demonstrate a professional manufacturing environment. • Training for supervisors on completion of Risk Assessments. • Ownership for all aspects of site and equipment contracts and maintenance. • Cost, working hours and labour reduction to match reducing business levels. • Manufacturing… Show more • Responsibility for the all aspects of UK Manufacturing, Purchasing and Site Operations. • Implementation of modern manufacturing techniques to UK injection moulding and assembly operation to demonstrate a professional manufacturing environment. • Training for supervisors on completion of Risk Assessments. • Ownership for all aspects of site and equipment contracts and maintenance. • Cost, working hours and labour reduction to match reducing business levels. • Manufacturing support for New Product Introduction, both in UK and China. Managing supply chain aspects from first builds into full production. • Implementation of Management Policies to ensure consistency within the business. Includes sickness & absence, disciplinary, vacations and safety related procedures. Show less
-
-
-
MacDermid Autotype
-
United Kingdom
-
Plastics Manufacturing
-
Production Manager
-
Aug 2001 - Aug 2007
Production Manager – Conversion, Warehouse & Despatch, Jan 2005 – Aug 2007 • Responsibility for the day-to-day operations of 3 manufacturing teams, totalling 53 people, with the primary goal of delivering cultural change and improved business performance. • Developing team members in existing supervisory positions to better deliver their job role and where this was not possible, restructuring the department. • Ensuring regular reviews and annual development reviews are… Show more Production Manager – Conversion, Warehouse & Despatch, Jan 2005 – Aug 2007 • Responsibility for the day-to-day operations of 3 manufacturing teams, totalling 53 people, with the primary goal of delivering cultural change and improved business performance. • Developing team members in existing supervisory positions to better deliver their job role and where this was not possible, restructuring the department. • Ensuring regular reviews and annual development reviews are implemented. • Implementing metrics for the delivery of performance improvement in manufacturing areas, in the areas of Quality, Cost, On-Time Delivery and Health & Safety. • Implementing the first stages of improvement activities, such as Good Ideas Boards, basic 5S & housekeeping initiatives. Improving methods and practices in cleanroom operations to better meet the cleanliness requirements. Production Manager – Optics Division, Oct 2001 – Jan 2005 • Responsibility for establishing and continually developing a manufacturing cell in a new business division. Accountability for an operational budget of £1.8 million and a team of 25 operating on flexible shift patterns. • Recruitment and development of a production team to operate state of the art, bespoke manufacturing equipment in a Class 10,000 clean room. • Achievement of 98% on time delivery to exacting, customer defined, quality standards. • Provision of manufacturing direction on the development of the next generation process and cleanroom to provide a step-change improvement in quality. • Tracking of monthly financial performance, delivering on target, or better, performance. • Key driver behind culture change programme on site with specific target of developing line managers to perform to higher standards. • Completed redundancy selection processes and where necessary notified individuals of their position of redundancy when a business partner withdrew and the project closed. Show less
-
-
-
Dyson Ltd
-
United Kingdom
-
Construction
-
Front Line Manager
-
Aug 1999 - Aug 2001
-
-
-
-
Team Coordinator
-
1996 - 1999
-
-
Education
-
Loughborough University
BSC, Materials & Business Sudies
Community
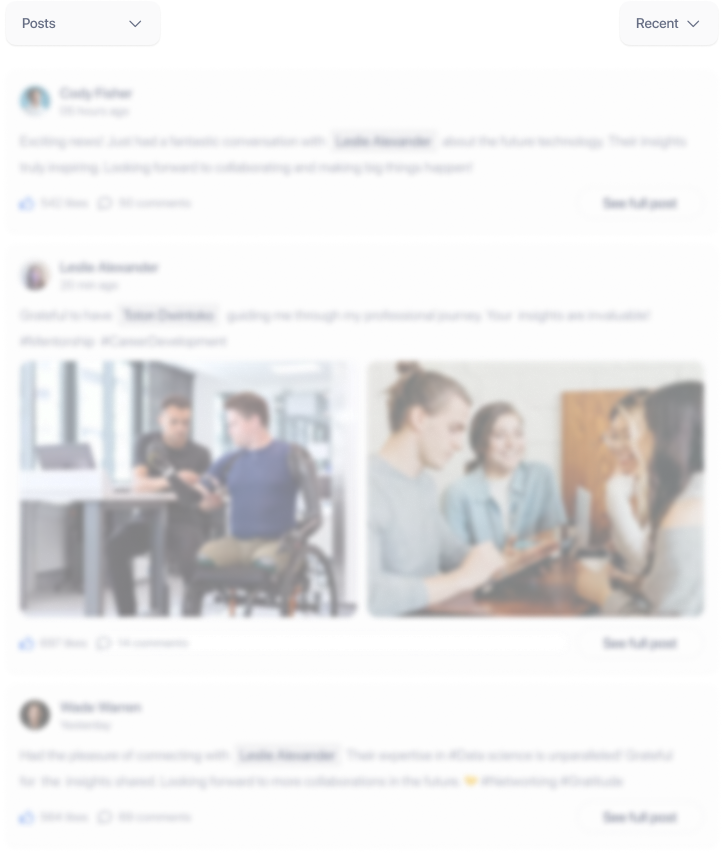