Ni'Chelle B.
Operations Manager at Park Aerospace Corp.- Claim this Profile
Click to upgrade to our gold package
for the full feature experience.
Topline Score
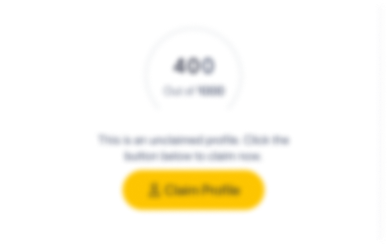
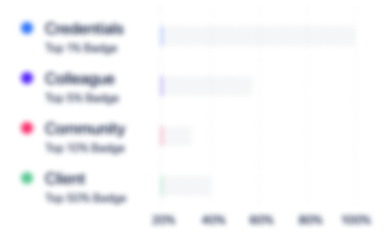
Bio

Mike Sobieski
I am pleased to write this letter of reference for NiChelle Bruce. While VP of Operations for Bodycote, NiChelle worked directly for me as Operations Manager over two (2) Wichita heat treat plants. This assignment included a complete closure and consolidation of one plant into the other while maintaining daily operations including customer satisfaction and profitability. She accomplished this early in her career operating far above any expectations. NiChelle has a strong background in operations across technologies focused on the basics of SQDPA (Safety, Quality, Delivery, Productivity, and Asset Utilization). She balances the often competing interest of different stake-holders and finds a solution acceptable to all. Most of all, her word is her bond. She communicates professionally to all levels of the organization. I fully recommend NiChelle for any operational role. She has demonstrated her ability to manage projects, people, and operations in a professional manner with strong performance.

Mike Sobieski
I am pleased to write this letter of reference for NiChelle Bruce. While VP of Operations for Bodycote, NiChelle worked directly for me as Operations Manager over two (2) Wichita heat treat plants. This assignment included a complete closure and consolidation of one plant into the other while maintaining daily operations including customer satisfaction and profitability. She accomplished this early in her career operating far above any expectations. NiChelle has a strong background in operations across technologies focused on the basics of SQDPA (Safety, Quality, Delivery, Productivity, and Asset Utilization). She balances the often competing interest of different stake-holders and finds a solution acceptable to all. Most of all, her word is her bond. She communicates professionally to all levels of the organization. I fully recommend NiChelle for any operational role. She has demonstrated her ability to manage projects, people, and operations in a professional manner with strong performance.

Mike Sobieski
I am pleased to write this letter of reference for NiChelle Bruce. While VP of Operations for Bodycote, NiChelle worked directly for me as Operations Manager over two (2) Wichita heat treat plants. This assignment included a complete closure and consolidation of one plant into the other while maintaining daily operations including customer satisfaction and profitability. She accomplished this early in her career operating far above any expectations. NiChelle has a strong background in operations across technologies focused on the basics of SQDPA (Safety, Quality, Delivery, Productivity, and Asset Utilization). She balances the often competing interest of different stake-holders and finds a solution acceptable to all. Most of all, her word is her bond. She communicates professionally to all levels of the organization. I fully recommend NiChelle for any operational role. She has demonstrated her ability to manage projects, people, and operations in a professional manner with strong performance.

Mike Sobieski
I am pleased to write this letter of reference for NiChelle Bruce. While VP of Operations for Bodycote, NiChelle worked directly for me as Operations Manager over two (2) Wichita heat treat plants. This assignment included a complete closure and consolidation of one plant into the other while maintaining daily operations including customer satisfaction and profitability. She accomplished this early in her career operating far above any expectations. NiChelle has a strong background in operations across technologies focused on the basics of SQDPA (Safety, Quality, Delivery, Productivity, and Asset Utilization). She balances the often competing interest of different stake-holders and finds a solution acceptable to all. Most of all, her word is her bond. She communicates professionally to all levels of the organization. I fully recommend NiChelle for any operational role. She has demonstrated her ability to manage projects, people, and operations in a professional manner with strong performance.

Experience
-
Park Aerospace Corp.
-
United States
-
Aviation & Aerospace
-
1 - 100 Employee
-
Operations Manager
-
Sep 2022 - Present
-
-
Quality Assurance Manager
-
Jan 2020 - Sep 2022
Here, I drive the quality improvement of each product, leading a team of 15 in the internal laboratory—ensuring all physical, analytical, and mechanical testing of products to meet specification requirements. ➤ Reduced lead times for products from three weeks to two by establishing a scheduling system and cross training program for employees. ➤ Managed digital transformation to a new QMS system, consolidating data into one accessible location with instant access to internal audit procedures and training, resulting in a $400K ROI. ➤ Increased lab efficiency by 40%, putting processes in place for the lab to become independently certified and meet ISO standards. ➤ Established an internal audit system, performing 10 internal audits per month with four internal auditors—resulting in a 40% drop in customer complains. ➤ Maintain AS 9100 certification through process improvements, better documentation, and internal audit procedures. ➤ Created a succession plan for key positions within the department including quoting manager, quality engineer, quality supervisors, and inspectors. ➤ Responsible for two NADCAP certifications in Composite Parts Manufacturing and Non-Metallic Materials Testing/Manufacturing.
-
-
Composite Parts Manager
-
Jun 2019 - Jan 2020
As Composite Parts Manager, I oversaw a manufacturing team of 12 including machining, lay up technicians, and manufacturing engineers—providing end-to-end oversight of the product to ensure the timely delivery of high-quality products. ➤ Boosted yield by 60% within the first three months, working with engineers, lay up team, and operations to produce parts correctly the first time. ➤ Increased autoclave running time from 6 hours per day to 20 by implementing a swing shift with the crew, increasing product flow, on-time delivery, and sales. ➤ Increased on-time delivery by 40% within the first 90 days, successfully resolving three contracts that were three months past due by working with the planning and operations team to manufacture the materials. ➤ Implemented a scheduling system, breaking down all aspects of the job to show each phase, ensuring accurate communication between all team members.
-
-
-
Spirit AeroSystems
-
United States
-
Aviation and Aerospace Component Manufacturing
-
700 & Above Employee
-
Fabrication Specialist Senior Manager
-
Nov 2017 - Feb 2019
At Spirit Aerosystems, I led 12 first-level managers to improve operations and system flow for 300+ employees—identifying issues and working with team to implement innovate solutions that streamlined processes to meet production targets. ➤ Increased third-party processing OTD from 71% to 97% and quality improvement from 97% to 99.7% in the first six months. ➤ Reduced hexavalent chromium exposure through site-wide initiative, bringing the facility into compliance with OSHA regulations by developing and implementing standardized procedures organization wide. ➤ Established the use of 3D printing in the masking department, improving operational flow to grow from 400 parts per day to 1200. ➤ Cut costs by $700K within one year by successfully implementing lean projects.
-
-
-
Valence Surface Technologies
-
United States
-
Aviation and Aerospace Component Manufacturing
-
100 - 200 Employee
-
Production Manager
-
Aug 2015 - Oct 2017
At Valence, I oversaw daily production of 21 departments, with 170 employees, across three shifts, delivering consistent gains in throughput and sales by applying lean process management and improvement techniques, rapidly developing innovative solutions for any processing bottlenecks. ➤ Boosted department throughput by 30% and facility throughput by 25% over two years by implementing daily huddles and metric boards—establishing daily goals for each department. ➤ Drove sales by 13% year-over-year while decreasing labor percentage 10%, by streamlining processes to improve efficiency and on-time delivery. ➤ Increased throughput from 60% to 95% by developing an improved masking operation, including individual screens and stations for each operator. ➤ Decreased scrap and rejections by 60% by creating a new production flow for highly technical parts.
-
-
-
Aerosync Support
-
Wichita, Kansas Area
-
General Manager
-
Feb 2015 - Aug 2015
Overhauled manufacturing operations, getting a facility six months behind back on track within just two months—putting systems and processes in place to drive efficiency and deliver parts on-time. Managed the design, manufacture, and installation of customer tooling. ➤ Delivered a $1.5M tool two weeks ahead of schedule, developing strong supplier relationships to ensure timely delivery of supplies. Overhauled manufacturing operations, getting a facility six months behind back on track within just two months—putting systems and processes in place to drive efficiency and deliver parts on-time. Managed the design, manufacture, and installation of customer tooling. ➤ Delivered a $1.5M tool two weeks ahead of schedule, developing strong supplier relationships to ensure timely delivery of supplies.
-
-
-
Bodycote
-
United Kingdom
-
Metal Treatments
-
700 & Above Employee
-
Operations Manager
-
Jan 2013 - Feb 2015
Revitalized two struggling facilities with 200+ employees, improving P&L margins through sales growth, improved delivery, and the consolidation of both facilities. Oversaw all sales and operations with direct responsibility for P&L, business development, customer relationships, human resources, and sales. ➤ Successfully consolidated two facilities four months ahead of schedule and $800K under budget. ➤ Achieved 92% on-time delivery within three months—a 40% increase—by developing a facility bus schedule.
-
-
-
Thermal Specialties
-
Oklahoma, United States
-
Plant Manager
-
2012 - 2012
Managed daily operations of facility, leading a team of 20 to consistently maintain throughput above established targets. Developed staffing and training programs for employees, improving team engagement and reducing turnover. ➤ Grew number one customer from 500K per month to 1.5M within six months by using Kanban, just-in-time delivery, and production scheduling methods. ➤ Eliminated 300+ hours of downtime in six months by developing and implementing a preventative maintenance system.
-
-
-
Kaman Aerospace Corporation
-
United States
-
Aviation and Aerospace Component Manufacturing
-
400 - 500 Employee
-
Quality Engineer
-
Jul 2007 - Jan 2011
Provide quality assurance input and guidance to operations and engineering for critical product and process developments required for Aerospace Composite Manufacturing. Responsible for multiple areas within the quality organization including but not limited to: data analysis and report of current processes; review and approve First Articles to AS 9102 and customer requirements; utilize critical thinking/writing skills to assist in developing and documenting improved processes throughout the facility and auditing to the requirements of customer and regulatory requirements.
-
-
-
-
Group Quality Director
-
May 1997 - Jul 2007
Throughout 10 years of service advanced to increasingly responsible position, culminating in a Group Quality Manager role with oversight for three local thermal processing facilities. Promoted in 2001 to Division Quality Manager assuming management representative responsibilities for the overall operation of the management system; additional advancements in 2005 as Group Quality Manager responsible for overall quality operations throughout all facilities within the Wichita group. Throughout 10 years of service advanced to increasingly responsible position, culminating in a Group Quality Manager role with oversight for three local thermal processing facilities. Promoted in 2001 to Division Quality Manager assuming management representative responsibilities for the overall operation of the management system; additional advancements in 2005 as Group Quality Manager responsible for overall quality operations throughout all facilities within the Wichita group.
-
-
Education
-
University of Phoenix
Bachelor of Science in Management, Leadership -
Newman University
Six Sigma Black Belt, Business Administration and Management, General
Community
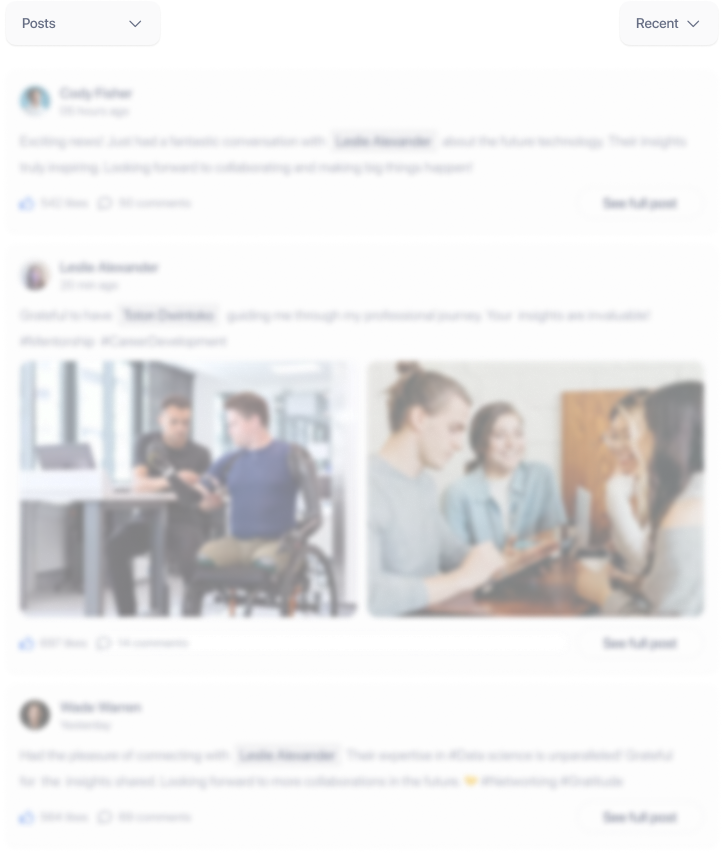