Ndumiso Mjweni
Acting Foreman at Hendok Group- Claim this Profile
Click to upgrade to our gold package
for the full feature experience.
Topline Score
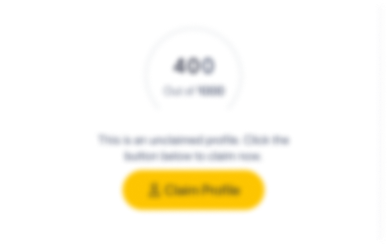
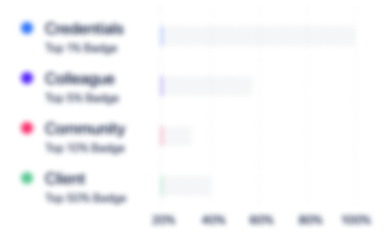
Bio


Experience
-
Hendok Group
-
South Africa
-
Construction
-
100 - 200 Employee
-
Acting Foreman
-
Nov 2022 - Present
Working a 9 Hours shift Monday to Friday 45 Hours a WeekLeading a Team of 160 Employees working 12 Hour shifts 3 ShiftsEnsure Factory Performs Smoothly and Efficiently taking into consideration-that All orders are completed in Due time.Products Produced under the Department, Roofing Sheets (6 Machines), Barbwire (22 machines), Netting (16 Machines), Diamond Mesh (2 Machines) and Razor Wire (4 Machines).Weekly Target is 1450 Tons from this tonnage 45% is made up of the Roofing machines and 30% from the Barbwire Machines and the other 25% from the remaining machines efficiencies Range from 80% to 97% taking into Consideration Number of Breakdowns, the demand in OrdersAnalyse Production Reports and see if targets are met if not take disciplinary action if no valid reason for Poor Production, send through Production reports to higher management.Have Morning meetings with Production Manager and work on Qlik SENCES to update on the system how much orders are complete.Every Morning Ensure stock take is done for Raw Material used for Roofing Products which is about 400 Tons Different types of Material this is completed in 45 minutes This Count helps in The Planning for the day on what is going to Run on Production.Work on Microsoft Teams and set Shifts and add Times for All the Employees Reporting under me.compile reports on the Number of absenteeism and communicate with HR on a Daily Basis.Drive 8 Ton Forklift to Assist on the Workflow by Moving about 40Tons Daily to the Warehouse about 3 Hours spent on the Forklift.Ensure a Safe and clean working environment by educating and directing Personnel on the use of all control points, equipment and resources; maintain compliance with established polices and procedures.Every afternoon Communicate with the Supervisors of what is required out of them for their shift on the Night
-
-
Assistant Manager Administrative
-
Mar 2022 - Oct 2022
Compiling reports on UPKEEP for Maintenance and Production Mangers for the Entire Factory for Morning meetingsDo Production Capturing on Excel Spreadsheets for 3 Factories which Consisted with a variety of Different Machines and ProductsDo TIME SCHEDULES for PAYROLL which had about 390 employees this Work was done on MICRO SOFT TEAMS and Sort out shifts for the Factory created a Forecast of one Month ahead for the shifts.Work on MIX TELEMATICS by doing an analysis on the efficiency of the Forklift Machine by Analysing how Much work did the Machines do compared to the time standing and idling and actually doing work this was done for 3 Departments Work on QLIK SENCE to compile a report for Monday afternoon Meetings where I Present the stats to the Directors on Behalf of the Production Manager on How the 3 different Departments Performed the Previous Week and what % of the efficiencies was dropped due to Breakdowns Absenteeism, Planned Maintenance, unforeseen circumstances and due to Short times. This report was compile and Presented Via MICROSOFT POWERPOINT.
-
-
Shift Supervisor
-
Nov 2020 - Feb 2022
• Make sure there is a smooth work Flow of production• Analyse and report breakdowns and increase production scores• Lead team into working efficiently and reduce costs to Company and increase productivity• Maintain Housekeeping throughout the Factory• Fill in production reports and IR reports for any incident• Fill in attendance register make sure all machines are running at a required time• Monitor the production processes and adjust schedules as needed.• Ensure all changes are communicated to all relevant parties.• Manage and motivate bottling staff and achieve results.• Maintain quality service by establishing and enforcing organizational standards.• Ensure a safe and clean work environment by educating and directing personnel on the use of all control points, equipment, and resources; maintain compliance with established policies and procedures.
-
-
Foreman
-
Mar 2021 - Apr 2021
As Foreman Supervised 2 Departments which had 4 shifts with 160 employees and 4 Supervisors Reporting to me Firstly Do Stock Take which had a Variety of Products which Summed up to about 200 Tons including Raw MaterialPrepare Stock Sheets and Production Paperwork and send Through to Higher Management via Email, Had morning meetings with Production Manager To report on the previous days Production whats Successes and challenges were In-counted, report on which machines Did job change overs as per ordersWorked on TEAMS to Record Time Schedules for the Employees and Also created Forecast for the Shifts which was always one month AheadCommunicated with Management and sales Teams Regarding orders Via Emails had lead times to keepInsured that Teams Worked efficiently at all timesHad to Make sure and check if all orders are completed and the quality of the orders are with in spec Insure that Change overs are being done correctly,Report any breakdowns and how Big the Breakdown is to upper Management and communicate it to the Maintenance manager
-
-
Data Controller
-
Apr 2019 - Nov 2020
Invoicing using SAGE System an average of 300Tons on a Daily Basis with Flexible hoursMAINTENANCE Record Analysis of about 400 Machinery on Site how Much time is spent Servicing and Repairing by the Artisans of which there were 25 Employees For maintenance and Also took into account how much time was spent installing machinery All this was Recored On SAGE Maintenance SystemFLEET COST Analysis Created a Spreadsheet to Analyse The cost to Run The Fleet of the Company which had 41 Trucks and 61 Trailers.The Analysis Consisted of much Much was Spent on each Truck or trailer to keep in working Condition for e.g No of Tyres Used for that Specific year, How much was Spent on individual Parts for each Truck or trailer also took Labour Hours into consideration as company had in house Workshop, i had a list of individual Cost of all items Inter-grated them into a Spreadsheet. This Mad it easy to See which Asset is efficient or not in terms of the Fleet. The workshop had 5 Employees which were Also inter-grated into the spreadsheetWorked on a SITE CONTROL Tracker On Excel SpreadsheetAnalyse the Hours Spent Fixing all the defects on Site with the Costs Inter-grated on the spreadsheetwhich made it easy for management to Decide should they outsource the repairs and do them in house as this also took Labour Hours of the employees doing Site maintenance Which had 6 Employees
-
-
-
Fedics
-
Hospitality
-
300 - 400 Employee
-
Sales Team Supervisor
-
Mar 2017 - Apr 2019
Started of as a Cashier for 4 Months(2017) made an Average of 3k Sales working for only 4 Hours with an Average of 25 Meals a day Promoted to be Team Leader During the Shutdown which was for 3 Months (2017)had a team of 6 Employees. Sales increased to and average of 9k in 4 hours at an Average of 400 Meals per day. Transferred to Transnet Site From October (2017) as a Shift Supervisor (3Days Shift) 3 Days dayshift than 3 days off than 3 Days Nightshift worked for 9 Months. As Shift Supervisor would Motivate team to Perform efficiently would Also Issue Raw Material worth 10k to cover the Following shift to ensure smooth workflow for the Following Shift. As a Supervisor would be In charge of the safe and would also Cash up at the end of the shift and do handover to the Manager and explain the Successes we had during the shift an Average of 14k Per-Day on shift of that which was 30% was Meals and 40% which was Cold Beverages 30% other Food Items. Stock Balance sheets and Sales vs Cash On hand Balance sheet On the 1st of July 2018 Transferred back to Sapref Site as Administrator, Store-man, Cost Analysis. As Administrator Would ensure All Files and Paperwork of all the Representatives are in order and check if all Balances sheets are filled in Correctly and matches the Income statement there were 5 Satellite kitchens which all the Paper work had to be accounted for. As Store-man Every afternoon would issue stock to all Relevant kitchens about 4 Tons of raw material on a daily basis then Fill in the stock Issue Book to balance it out at the End of each Month for Monthly Stock Take. On Daily Basis would Order stock on MY MARKET for the Site Kitchen to be able to Operate Order everything according to the MENU set for The Week As Cost Analysis would use MENU-TEK Excel Spreadsheet to Insure Minimum Cost for each meal prepared and communicate should there be a high Cost on a Specific menu Put up for the Week.
-
-
-
Laurence Auto
-
South Africa
-
Service Technician
-
Sep 2010 - Jan 2016
Working on Toyota, VW, Audi, Isuzu, Mitsubishi, Nissan and Ford Vehicles Planned Major and Minor Service for at least 10 Vehicles per day Changing of clutch for all manual Cars, Each car Maximum of 3 Hours Breaking System Repairs and adjustment using the Necessary tools Cylinder head replacement including head Gasket Timing Belts Replacement using Timing Marks and Tools Differential repairs with the correct Final drive ratios and refurbishment Suspension Repairs and refurbishment Minor electrical repairs Installing Sound system and adding extra Lights with own independent relays
-
-
Education
-
Gateway City College
Mechanical Engineering, Mechanical Engineering N2 (Fitting and Turning) -
University of Zululand
Honors, Business, Management, Marketing, and Related Support Services -
University of Zululand
Bachelor of Commerce - BCom, Business, Management, Marketing, and Related Support Services -
Port Shepstone High School
National Senior Certificate
Community
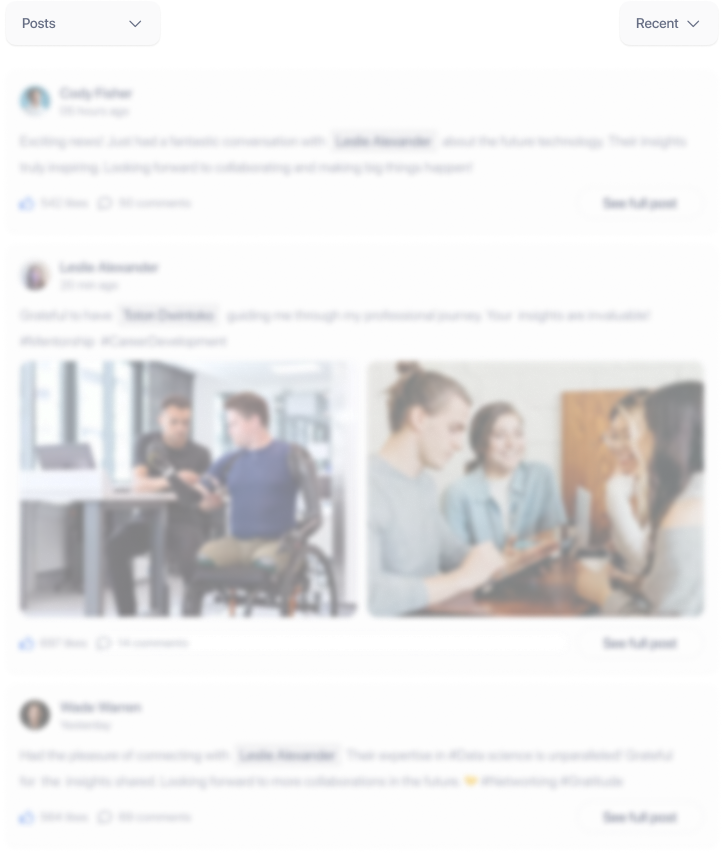