Nathan Reynolds
Manager of Operations at ENVE Composites- Claim this Profile
Click to upgrade to our gold package
for the full feature experience.
-
Tagalog -
Topline Score
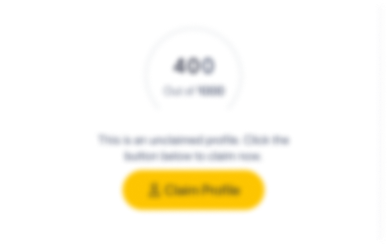
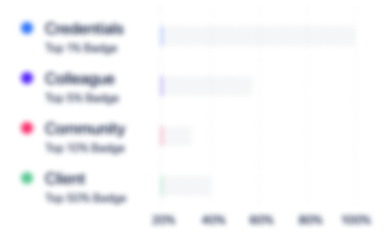
Bio

Allen Keetch
I had the opportunity to work with Nathan at Weber State in multiple group environments and found him to be very helpful and insightful in our group projects. He is a great asset to have on any team and works well with others. Nathan is a very intelligent person who is willing to work very diligently to see a project to completion. I would recommend Nathan to any company looking for a smart qualified engineer to add to their team.

Allen Keetch
I had the opportunity to work with Nathan at Weber State in multiple group environments and found him to be very helpful and insightful in our group projects. He is a great asset to have on any team and works well with others. Nathan is a very intelligent person who is willing to work very diligently to see a project to completion. I would recommend Nathan to any company looking for a smart qualified engineer to add to their team.

Allen Keetch
I had the opportunity to work with Nathan at Weber State in multiple group environments and found him to be very helpful and insightful in our group projects. He is a great asset to have on any team and works well with others. Nathan is a very intelligent person who is willing to work very diligently to see a project to completion. I would recommend Nathan to any company looking for a smart qualified engineer to add to their team.

Allen Keetch
I had the opportunity to work with Nathan at Weber State in multiple group environments and found him to be very helpful and insightful in our group projects. He is a great asset to have on any team and works well with others. Nathan is a very intelligent person who is willing to work very diligently to see a project to completion. I would recommend Nathan to any company looking for a smart qualified engineer to add to their team.
0
/5.0 / Based on 0 ratingsFilter reviews by:
Experience
-
ENVE Composites
-
United States
-
Sporting Goods
-
1 - 100 Employee
-
Manager of Operations
-
Oct 2021 - Present
• Management of Operations activities in Production, Logistics, Planning, Inventory, Purchasing, and Maintenance. Direct management of 6 and indirect management of 150 persons. • Operations Excellence Stream Lead for strategic initiative to grow the business in the next 3 years. • Maximize throughput, improve service levels, and control operating expenses while manufacturing products to customer expectations. • Mentorship of supervisors and team leads to empower and to improve technical ability at every level of operations. • Evaluated production capacities based on standard minutes to determine appropriate staffing levels. • Assist production supervisors in safety and personnel management including hiring, personal improvement plans, and disciplinary action. • Data management and development and report creation using Tableau and Microsoft excel used to identify quality trends and operations efficiencies. • Lead implementation of a lean initiative to add automated lacing and truing machines and lean methods to layout wheel build area increasing efficiency by over 30%. • Implemented a tiered meeting system to maintain operations performance through Safety, Quality, Delivery, Productivity, & Morale (SQDPM) metrics tracking • Assist with effective planning and layout of workflow, equipment, and assembly procedures.
-
-
-
GE Healthcare
-
Medical Equipment Manufacturing
-
200 - 300 Employee
-
Refurbishment Value Stream Manager
-
Oct 2018 - Sep 2021
• Manage refurbishment value stream of imaging healthcare products. Full project life-cycle management from new product introduction, engineering, parts procurement, program management, budget, profit and loss reporting, manufacturing production, inventory, and engineering operations. • Increased revenues by 15% in a 2-year period without increasing labor force. • Conducted business market analysis and beginning plan to increase operations 25% to increase market share. • Define production schedule based on customer demand and inventory allotments. • Supervise direct and indirect employees of up to 23 including engineers, planners, material handlers, technicians, and production associates. • Financial data as it applies to preparing budgets, analyzing operations, capital project planning, cost, revenue, and performance. • Meet with internal and external customer base to discuss business strategy, negotiations and deals, and direction of product. • Conduct investigations, containment, corrective action preventative action efforts (CAPA). • Lead program management reviews; report scorecards, profits, and KPIs. • Received awards for performance.
-
-
-
L3Harris Technologies
-
United States
-
Defense and Space Manufacturing
-
700 & Above Employee
-
Manufacturing Supervisor II
-
May 2016 - Oct 2018
• Supervised a team of up to 25 direct and indirect employees; team leads, engineers, planners, material handlers test technicians & assemblers.o Define repair, modification, or overhaul procedures, policies, workmanship standards and work instructions.o Supervision of logistics and supply chain to ensure production floor is stocked for efficient turn-around times through manufacturing. o Interviewing, hiring, mentoring, monitoring, performance reviews, and daily operations. o Manage process improvement and capital improvement projects including budget and internal order financials.• Overhauled and released procedures, work instructions, guidelines, and other internal documentation to ensure that DOD requirements were being met.• Participated in AS9100D and ISO audits and provided guidance as SME for the MRO manufacturing team.• Partnered with Design, Marketing, Program Management and Quality departments to ensure clear customer communication and reporting.• Contribute to Program with key information to report in PMRs and customer interactions.• Participated in team problem solving and process improvement efforts, sharing ideas, observations, and support for team action plans. • Participated in an internal SAP go-live which involved up to 50% travel to other locations to validate data and integrate into operations.• Conduct investigations, containment, corrective action preventative action efforts (CAPA).• Received awards for performance.
-
-
Manufacturing Engineer III
-
Jun 2011 - May 2016
• Create processes to build, repair, and overhaul electro-mechanical government owned equipment. Predator, Grey Eagle, Global Hawk, Apache, and more programs.• Capture customer requirements and implement them into build process methods that included review of technical and test requirements.• IPC certified in cables, circuitry, and repair procedures.• Evaluate and provide cost estimates for repair and/or overhaul of systems.• Created a manufacturing plan for the Global Hawk full government retrofit program. o Participated in MRBs of government owned material to disposition defects for repair and servicing.o Developed processes, material requirements, staffing requirements, tool procurement. o Submit Engineering Change Requests (ECR/ECN) for update of drawings and product requirements. o Participate in PMR and weekly cadence calls to report on progress of retrofit. o Delivered retrofit within customer cost and deliverable requirements.
-
-
-
Honeywell Process Solutions
-
Automation Machinery Manufacturing
-
1 - 100 Employee
-
Mechanical Engineering Intern
-
Nov 2010 - Jun 2011
I participated in process management and designed tooling for a high speed automated production line. I designed parts in AutoCAD mechanical, and AutoCAD Inventor. I oversaw the process to submit the new designs to vendor for creation and the implementation of the design into the process. Our team implemented a quick-change system to run several different sizes of the same type of product through an assembly line. I worked with automated testers and machining equipment to create and test prototypes prior to submission for build, installation and implementation. Assisted in designing a turret system for a robot that would pick up bottom assemblies and stack them in a chute to be assembled to the upper can. Was successful in designing a cylinder spacer that would flip assemblies from vertical to horizontal position using back pressure to drop onto silent chain conveyor at proper intervals. Stacking was not an option on the silent chain to prevent jamming in the turret system. The achieved goal was that tooling would be changeable within a 30-minute change over time.
-
-
-
Zions Bank
-
United States
-
Banking
-
700 & Above Employee
-
Treasury Management Item Processing Specialist II
-
Sep 2008 - Oct 2010
Worked with Remote Deposit check system. Processed checks electronically and balanced deposits from customers. Set up new accounts and settings for businesses. Submitted orders for check scanners and differen't products offered. Pulled reports and deposit status using .SQL database. Wrote .SQL statements to pull pertinent data to improve processes from customer scanning through deposit completion. Implemented Kaizen efforts to improve length of wait time for deposit processing. Efforts helped to improve process times by 30%. Compiled department statistics weekly and monthly to chart progress.
-
-
Education
-
Weber State University
Bachelor's Degree, Mechanical Engineering Technology -
Western Governors University
Master of Business Administration (MBA), Management and Strategy
Community
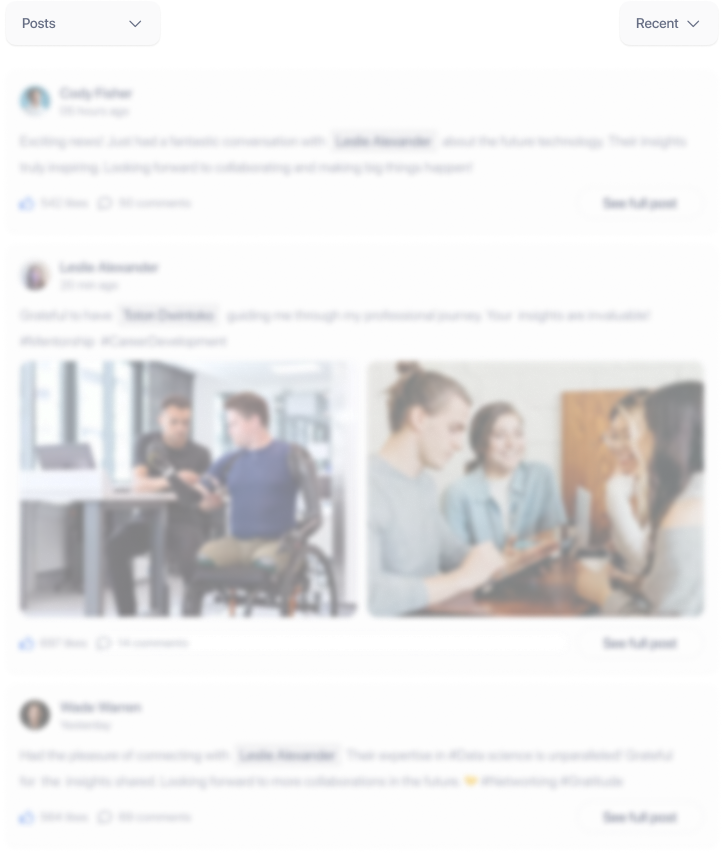