Narendra Namdev
Senior Purchasing Manager at SPC Lifesciences Pvt. Ltd- Claim this Profile
Click to upgrade to our gold package
for the full feature experience.
Topline Score
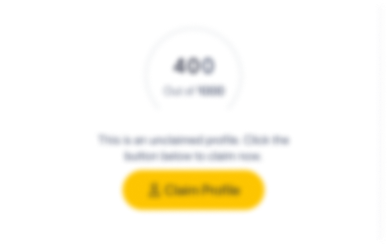
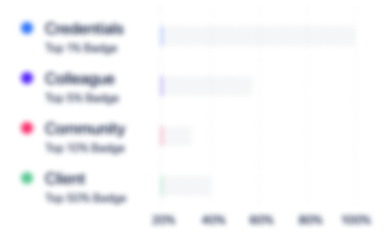
Bio


Experience
-
SPC Lifesciences Pvt. Ltd
-
Pharmaceutical Manufacturing
-
1 - 100 Employee
-
Senior Purchasing Manager
-
Apr 2019 - Present
Vadodara, Gujarat, India • Leading overall 2 plants procurement for direct & indirect materials, capex, external services, R&D etc. • Leading expansion of new plant & facility at Ankleshwar (cost 10 Cr) and Sika (cost 60 Cr) • Leading import purchase, managing strategic sourcing to take maximum cost benefits, purchase price trend & analysis, purchase forecast & negotiation, annual procurement plan, vendor development etc. • Managing purchasing budget, target yearly cost reduction projects etc. • Leading new… Show more • Leading overall 2 plants procurement for direct & indirect materials, capex, external services, R&D etc. • Leading expansion of new plant & facility at Ankleshwar (cost 10 Cr) and Sika (cost 60 Cr) • Leading import purchase, managing strategic sourcing to take maximum cost benefits, purchase price trend & analysis, purchase forecast & negotiation, annual procurement plan, vendor development etc. • Managing purchasing budget, target yearly cost reduction projects etc. • Leading new innovative projects – Plant efficiency improvement programme, digitalization of manual log sheets, production process improvement, equipment process improvement etc. • Implementation of ERP System all modules successfully at plant & corporate office. • Leading inventory functions including monitoring of sales trend, quarterly plan, JIT, PPIC etc. Show less
-
-
-
-
Sr. Manager - Purchase
-
Jun 2016 - Apr 2019
Surat, Gujrat, India • Leading overall plant procurement for direct & indirect materials, capex like production machineries, lab equipments, tooling die & mould parts, civil projects etc. • Leading import purchase, import logistic, import shipment management, import license etc. • Managing strategic sourcing to stable / reduce existing cost including purchase price trend & analysis, purchase forecast & negotiation, annual procurement plan etc. • Managing purchasing budget, target yearly cost reduction… Show more • Leading overall plant procurement for direct & indirect materials, capex like production machineries, lab equipments, tooling die & mould parts, civil projects etc. • Leading import purchase, import logistic, import shipment management, import license etc. • Managing strategic sourcing to stable / reduce existing cost including purchase price trend & analysis, purchase forecast & negotiation, annual procurement plan etc. • Managing purchasing budget, target yearly cost reduction projects. • Leading purchase QMS as per ISO:13485, WHO PQDx, 21CFR part 820 etc. Including • Supplier qualification, supplier performance evaluation, risk mitigation programme, vendor audit plan to control quality defects & NC, supplier agreement, service agreement & contract negotiation, departmental training, SOP’s, skill mapping, activity calendar etc. • Leading inventory functions including monitoring of sales trend, MRP run, safety stock mechanism, re-ordering level, MOQ, EOQ, TAT standardization, JIT, inventory financial ratio etc. • Leading new projects - material outsourcing for group companies like Phillipines, Japan etc. Achievements • Successfully qualified international audits - WHO PQDx and ISO:13485 at Arkray. • Successfully implemented QCD module & Kaizen practices in 2018. • Achieved material cost down by negotiation and alternate source development INR 6.5 Million in 2017 and INR 11.50 Million in 2018, target in 2019 INR 16 Million. • Packaging material change project in 2017, results INR 1.8 Million annual cost down. • Successfully implemented cost reduction and output improvement - machine automation projects – Cartonating, Bottling, Devise Assembly, Laminator, FFS Pouching, Spotting Machine, Process Standardization etc. Results 52 manpower cost reduction. Show less
-
-
-
Lifespan Biotech
-
India
-
Pharmaceutical Manufacturing
-
1 - 100 Employee
-
DGM - Procurement, Packaging Development & Commercial
-
Oct 2009 - Jun 2016
Bhopal, MP • Headed overall Supply Chain Operations i.e. Procurement, PPIC, Sales Order Execution, Product Costing, Logistics, Customer Co-ordination, Product Delivery, Customer Complaint Handling, Customer Visit, Warehouse, Launching of new product in market etc. • Planning & procurement of raw material all API’s (domestic and import purchase), packaging material, packaging machinery, lab instruments, capital machinery, service contract & AMC’s etc. • Vendor management and development for best… Show more • Headed overall Supply Chain Operations i.e. Procurement, PPIC, Sales Order Execution, Product Costing, Logistics, Customer Co-ordination, Product Delivery, Customer Complaint Handling, Customer Visit, Warehouse, Launching of new product in market etc. • Planning & procurement of raw material all API’s (domestic and import purchase), packaging material, packaging machinery, lab instruments, capital machinery, service contract & AMC’s etc. • Vendor management and development for best price, quality compliance & delivery time, development of alternative local sources for imported raw materials which helps in cost saving. • Product cost sheet, strategic purchase plan, purchase budget and maintaining product price variation within given budget, ensure savings on input materials purchase. • Inventory analysis and control - stock verification, warehouse documentation, daily MIS report & so on. Fund management and optimum utilization of working capital. • Logistic management – inward & outward inventory logistic, transporter agreement & so on. • QMS for purchasing and warehouse function - represented both departments for customer and WHO plant audit. • Project Management – Procurement, planning and execution of project for plant facility renovation. • Packaging design & development for new and existing products for export and domestic market, run various operations such as: • Packing Material Costing, preparation of packaging material specifications, master packaging card & departmental SOP’s. Achievements • Successfully qualified WHO at Lifespan Biotech Pvt. Ltd. • Established inhouse packaging development department results “zero outsourcing”. • Successfully implemented ERP system to streamline inventory & commercial function. • Ensured 10% cost saving on product cost sheet. • Value engineering on packaging component, sizable cost savings in overall material cost results increased sales volume. Show less
-
-
-
Ranbaxy
-
India
-
Pharmaceutical Manufacturing
-
700 & Above Employee
-
Executive (Packaging Development)
-
Jan 2008 - Oct 2009
Dewas Area, India
-
-
-
Aparna
-
Public Health
-
1 - 100 Employee
-
Coordinator – Packaging Development & Vet. Division
-
Jul 2002 - Jan 2008
Indore, MP
-
-
Education
-
Symbiosis Centre for Management Studies- Pune
Post Graduate Diploma in Supply Chain Management, Logistics, Materials, and Supply Chain Management -
MPBOU, Bhopal University, MP
Master of Business Administration (M.B.A.), Marketing -
Udemy
Certificate for Six Sigma Green Belt & Black Belt, Business, Management, Marketing, and Related Support Services -
Indian Institute of Packaging, Mumbai
Graduate Diploma in Packaging Technology, Packaging Technology -
Vikram University, MP
Bachelor of Science (B.Sc.), Computer Science
Community
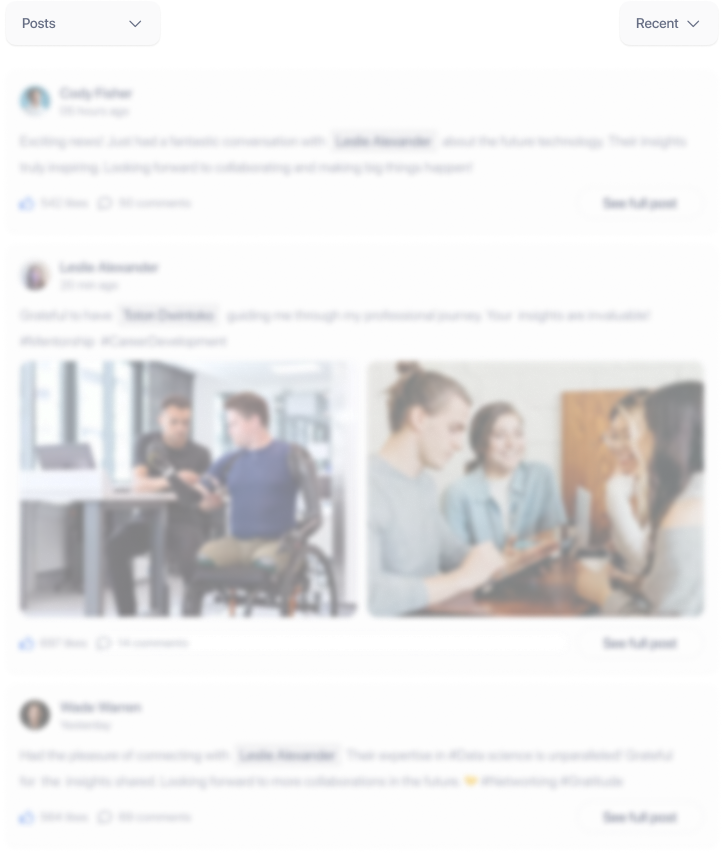