Ramaswamy (Alan) Lakshminarayanan, PhD
Senior Process Engineering Manager at MetOx Technologies, Inc.- Claim this Profile
Click to upgrade to our gold package
for the full feature experience.
Topline Score
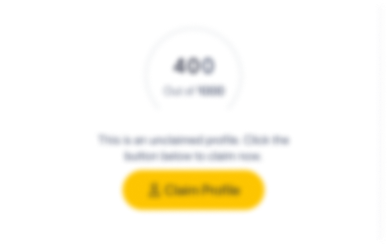
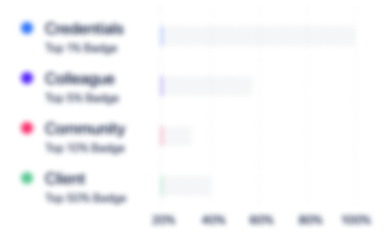
Bio


Experience
-
MetOx Technologies, Inc.
-
United States
-
Appliances, Electrical, and Electronics Manufacturing
-
1 - 100 Employee
-
Senior Process Engineering Manager
-
Mar 2022 - Present
Houston, Texas, United States
-
-
Process Engineering Consultant
-
Apr 2021 - Feb 2022
Houston, Texas, United States
-
-
-
Corning Incorporated
-
United States
-
Glass, Ceramics and Concrete Manufacturing
-
700 & Above Employee
-
Applied Mechanics Modeling Manager, Research
-
Apr 2018 - May 2020
Corning, New York, United States • Managed 9 applied mechanics modeling scientists in support of addressing product / process reliability issues for Optical Connectivity, Display, Gorilla Glass, Auto-glazing and interior, Auto filters and substrates divisions. • Established a mechanical reliability analysis program/initiative to reduce the prototype development time, and time to market by 50%, to aid in the design phase of critical polymer assemblies, while ensuring reliable products.
-
-
Reliability Manager, Research
-
Sep 2015 - Mar 2018
Corning, New York, United States • Led a 13 member centralized corporate department for reliability engineering and generation of reliability life models; tools used – environmental, UV, mechanical, vibration, HALT, HAST, shock and drop testing, failure analysis, Weibull++, ALTA, Minitab and JMP; responsibility – reliability support and resolution of reliability issues. • Enhanced reliability awareness and better integration of reliability in projects by introducing an in-depth Reliability training to 24 scientists and… Show more • Led a 13 member centralized corporate department for reliability engineering and generation of reliability life models; tools used – environmental, UV, mechanical, vibration, HALT, HAST, shock and drop testing, failure analysis, Weibull++, ALTA, Minitab and JMP; responsibility – reliability support and resolution of reliability issues. • Enhanced reliability awareness and better integration of reliability in projects by introducing an in-depth Reliability training to 24 scientists and engineers across multiple Research and development organizations. • Created a new team centric approach to early stage reliability management in product and process development and reduced the redesign cycles by 50% prior to product launch leading to 75% reduction in time to market.
-
-
-
University of Utah
-
1 - 100 Employee
-
Adjunct Professor, Dept of Materials Science and Engineering
-
Jun 2014 - Jun 2017
-
-
-
The KPI System
-
United States
-
Business Consulting and Services
-
1 - 100 Employee
-
Consultant - Lean Six Sigma, Process Engineering, Continuous Improvement
-
Mar 2015 - Sep 2015
Salt Lake City, Utah, United States • Developed and conducted training course on investigative methodology and reporting for CAPAs.
-
-
-
Amedica Corporation
-
Spain
-
Real Estate
-
Senior Director, Research and Development
-
Mar 2011 - Jan 2015
Greater Salt Lake City Area • Oversaw a department of 15 members, while securing the strategy and managing the budget, for the advanced product development, process engineering and regulatory clearance/approval of Spine, hip, and knee implants. • Developed silicon nitride as a biomaterial platform for bone fusion and articulation achieving FDA 510(k) clearance for spinal fusion implants and FDA acceptance for ceramic femoral heads during pre-IDE discussions. • Developed spinal implants (750+ SKUs) with zero… Show more • Oversaw a department of 15 members, while securing the strategy and managing the budget, for the advanced product development, process engineering and regulatory clearance/approval of Spine, hip, and knee implants. • Developed silicon nitride as a biomaterial platform for bone fusion and articulation achieving FDA 510(k) clearance for spinal fusion implants and FDA acceptance for ceramic femoral heads during pre-IDE discussions. • Developed spinal implants (750+ SKUs) with zero implant-failure-related revision surgeries over 12 years. • Managed the Process FMEA for all manufacturing processes, recommending and implementing actions to mitigate critical risks; in addition, represented the process engineering team in Design FMEA. Detailed Areas include: Strategy – Biomaterials Platform and product launch • Developed a 5-year technology roadmap, based on a biomaterials platform, synthesizing information from six departments, across three different implant markets leveraging three forms of silicon nitride. • Identified and proposed a company-wide product launch strategy by evaluating competing designs for marketability, logistics, instrument turns, cost, ease of implementation, and regulatory ease. Execution – Materials, Process and Product Development • Achieved product launch for an IDE in 9 months, as compared to anticipated 18 months, completing process validation and verification, as well as design, development, tests and FEA analyses of femoral heads. • Converted a leading Industrial ceramics manufacturer into a spinal implant vendor within 12 months with a judicious use of process and product validation. • Reduced new-design manufacturing time by 67% (from 9 to 3 months) by establishing standards for strength requirements and developing FEA based validation methodology for brittle ceramic implants.
-
-
Director, Research and Development
-
Jan 2009 - Feb 2011
Greater Salt Lake City Area • Oversaw a department of 15 members, while managing the budget, for the advanced product development, process engineering and regulatory clearance/approval of Spine, hip, and knee implants. • Developed new value propositions for ceramic implants as an alternate for long-standing metal or plastic options to gain entry into a pre-existing market with a new material. • Managed and completed an accelerated European product launch (Design review to finished goods) in 9 months, reducing the… Show more • Oversaw a department of 15 members, while managing the budget, for the advanced product development, process engineering and regulatory clearance/approval of Spine, hip, and knee implants. • Developed new value propositions for ceramic implants as an alternate for long-standing metal or plastic options to gain entry into a pre-existing market with a new material. • Managed and completed an accelerated European product launch (Design review to finished goods) in 9 months, reducing the time from anticipated 2 years, for a combination Dense-Porous (Cortico-Cancellous) implants. • Reduced the product development and launch phase times by ~60% by employing risk mitigation strategies focused on DMADV, DfM, DfR, and Dfx during process development, validation, and testing. • Established materials specifications, CTQ process parameters, quality plans, product attributes, inspection plans and testing standards for the bio-material platform. Developed value stream maps and process maps. • Obtained multiple 510(k) clearances with a comprehensive biocompatibility profile for the entire platform of 4 compositions of ceramic (3 Dense and 1 porous composition). • Enabled the 510(k) clearance of a spinal fusion device by obtaining FDA Buy-in for assessing product strength with a new superior test method effectively replacing the incumbent industry standard.
-
-
Manager, Research and Development
-
Jan 2007 - Dec 2008
Greater Salt Lake City Area • Developed Amedica’s status of “First in the world to market a spinal implant made of a ceramic material”. Obtained FDA 510(k) clearance. First Spinal Ceramic implant in a patient, April 2008. • Integrated quality by design into processes and methodology, using Design For Six Sigma (DFSS-DMADV), for an accelerated launch of a ceramic spinal implant, from concept to finished goods in 9 months, reducing the development time from anticipated 2 years. • Pioneered development of standards… Show more • Developed Amedica’s status of “First in the world to market a spinal implant made of a ceramic material”. Obtained FDA 510(k) clearance. First Spinal Ceramic implant in a patient, April 2008. • Integrated quality by design into processes and methodology, using Design For Six Sigma (DFSS-DMADV), for an accelerated launch of a ceramic spinal implant, from concept to finished goods in 9 months, reducing the development time from anticipated 2 years. • Pioneered development of standards, protocols and equipment for mechanical testing and proof testing of dense and porous silicon nitride spinal implants. • Directed a six sigma team to utilize DMAIC methodology to provide an initial annual savings of over $700k and continuous potential annual savings of over $1MM by reducing cosmetic defects in ceramic implants. • Qualified a variety of hi-tech processing equipment (EQ’s, IQ’s, OQ’s and PQ’s) of spray dryer, nitrogen atmosphere Batch, Belt and HIP furnaces, etc.
-
-
Research And Development Scientist
-
Apr 2002 - Dec 2006
• Developed new product pathways with ceramic implants, processing methods and testing methodology. • Generated ceramic implant IPs in the areas of articulation, dense and porous spinal implants which form the core technology for Amedica. • Established vendors and managed external testing programs worth $1.5MM for Mechanical Testing, Biocompatibility, Hip Simulator Testing, and Anti-infective studies as well as internal testing programs.
-
-
-
-
Research Instructor, Dept. of Bioegineering
-
Aug 2001 - May 2002
-
-
-
University of Utah School of Medicine
-
United States
-
Higher Education
-
700 & Above Employee
-
Adjunct Assistant Professor, Dept. of Orthopedics
-
Oct 1998 - Mar 2002
Greater Salt Lake City Area • Hip Implant Development – Managed processing, testing and test development for ceramic hip implants. Performed Finite Element Analysis (FEA) and ASTM testing of femoral head implants. • Spinal Implant Development – Developed processes for making porous spinal and bone growth implants. Developed mechanical test methods for porous implants.
-
-
-
University of Utah College of Engineering
-
Civil Engineering
-
1 - 100 Employee
-
Research Assistant
-
Jun 1992 - Aug 1998
Greater Salt Lake City Area • Ceramic Processing and Characterization – Performed processing, physical, and mechanical characterization of oxide and non-oxide ceramics. Established methodology for measuring and characterizing apparent fracture toughness of layered ceramic composites. • Layered Ceramics – Demonstrated improved strength, fracture toughness and Rolling-Contact-Fatigue (RCF) performance of layered ceramics with residual surface compression.
-
-
Education
-
University of Utah College of Engineering
Ph.D., Materials Science and Engineering (Ceramic Science) -
Indian Institute of Technology, Madras
B. Tech., Metallurgical Engineering
Community
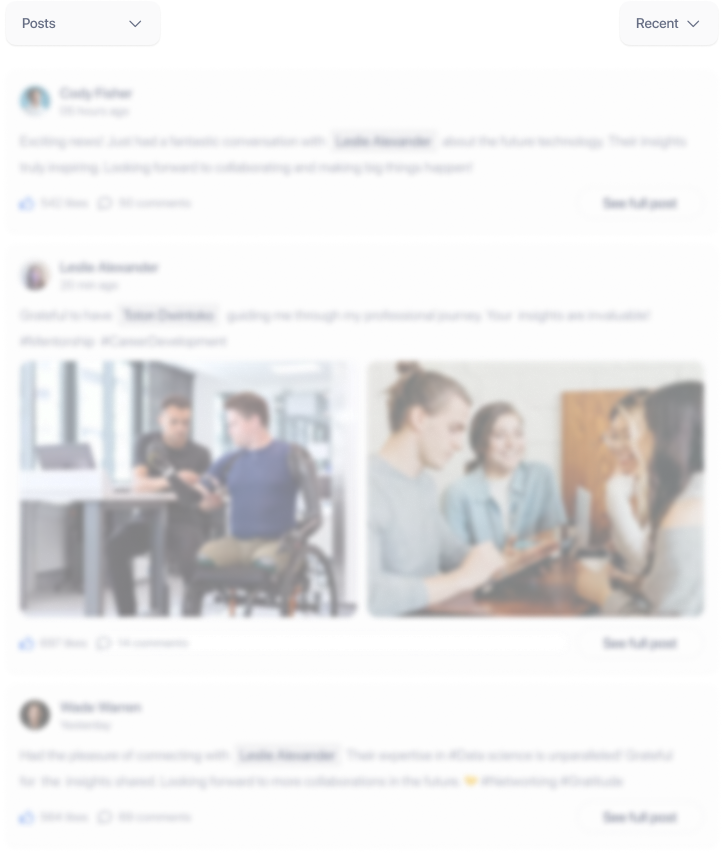