Nancy Miller
at Golden Temple- Claim this Profile
Click to upgrade to our gold package
for the full feature experience.
Topline Score
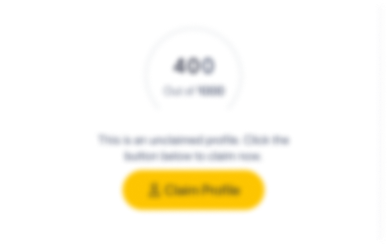
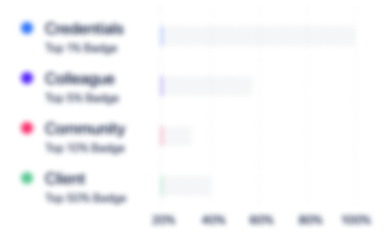
Bio


Experience
-
Golden Temple
-
Manufacturing
-
1 - 100 Employee
-
-
Dec 2005 - Present
Materials: Control of materials into production thru 8 warehouses. Inventory management, establish annual inventory projections, and maintain inventory within given threshholds.Forecasting and Demand Planning: Rolling 18-month plan, drives annual material contracting. Establish warehouse rules to support inventory plan and maintain order fulfillment rates at 99%. Manage production scheduling to support overall plans. Established monthly consensus forecasting process.
-
-
-
Dec 2005 - Present
Cereal and Tea manufacturing, Natural and Organic. GMP's, Food Safety, Regulatory Requirements.Forecasting, annual frozen forecast process revised to rolling 18-month S&OP Consensus Forecast process, updated monthly Capacity Planning developed for each production line, driven from the forecast, reviewed monthly with Production and Operations Managers for right-sized staffing and capitol spend planning Scheduling parameters developed, to balance FG inventory levels, available capacity, and seasonal sales Inventory Projections published for CY, performance to plan reported monthly Inventory accuracy as continuous improvement: 73% abs accuracy (2005), to 84% (2007), and 96% (2009) Inventory reduction from $9.8M to $6.2M in 2009, with no reduction to order fulfillment Inventory turns increased from 2.5 (2005) to 8.7 (2009) Implementation of Change Management process in 2009, gaining control of obsolesce, waste, and system management Warehousing and Material Flo Materials residing in 8 warehouses, development of processes and disciplines to manage material flow to support production and gain increases in inventory accuracy Labor projections for Production and Warehousing, Warehousing labor and OT, performance to plan, reported monthly Implementation of Oracle from legacy system in 2008 (18-month preparation and planning to "go-live") Show less
-
-
-
Hearthside Food Solutions
-
Food and Beverage Manufacturing
-
700 & Above Employee
-
Materials and Forecast Manager
-
2005 - 2010
-
-
-
Medallion Cabinetry
-
Wholesale Building Materials
-
1 - 100 Employee
-
-
Jan 2000 - Jan 2005
Cabinet manufacturing, satellite facility. Lean environment encouraged resourcefulness.Material Management: Established inventory control procedures, dependent on BOM accuracy and yield loss Purchasing: Instituted stock level policies, reduced inventory, with increased fulfillment of customer orders Increased inventory accuracy, 89% in 2002, to 98.7% in 2004 Improved On-Time shipments, to end user, from 94% (2002) to 99% (2003) Accelerated inventory turns: 14.3 in 2002, 34.1 in 2004 Lean Manufacturing techniques, applied to material flow and production processes Visual warehouse, Kanbans for non-MRP items, single piece flow into production Team involvement in identifying and eliminating non-value-added process stepsSupply Chain Management, Vendor Relations: Developed supplier excellence, on-quality, on-time-delivery Manage through growth: Production increased 600% in 5 years Conduct year-end physical inventory, annually Relocated factory: Created stores layout, planned material move, completed with zero material loss or accidents System development: Team developed program to "issue" material into production, in a back flush environment Production and Inventory Management Show less
-
-
-
2000 - 2005
Materials management, cabinetry manufacturing facility. Developed a visual warehouse, material flow into production ahead of need. Established issuing of key, high value components, in a back flush environment. Responsible for purchasing, and inventory control. Implemented kan bans, and vendor managed inventories.
-
-
-
-
Production and Inventory Management
-
Jan 1995 - Jan 2000
Data Collection, Bar Code reader manufacturer. Production primarily outsourced. Master Scheduler, capacity planner, production scheduler: 98% on-time completion of production schedule Production Control, capacity sensitive to 25-40 subcontractors and 3 internal work centers Inventory Management of 1.5M raw inventory, maintained 100% accuracy in FG Created and maintained Gantt charts for all product lines Developed process documentation for all production departments, for ISO 9001 Certification Selection and implementation of MRP9000 from legacy system, 1/1/98, and development of work instructions Show less
-
-
-
-
Business Owner
-
Jan 1991 - Jan 1995
Florist, seasonal industry, highly perishable product, customer service oriented. Established successful retail floral business, managed staffing, accounting, advertising Purchasing and staffing for holidays and events, with sales peaks 25-times normal business Teaching, public speaking, featured guest designer at floral design shows Business grew 500% in the first 3 years and continues to be a successful venture for current owner Prior to Business Owner Florist, 14 years, managed 3 businesses, taught floral design, participated in competitions and design shows Show less
-
-
Education
-
Oregon State University
-
Oregon State University
BS, communication
Community
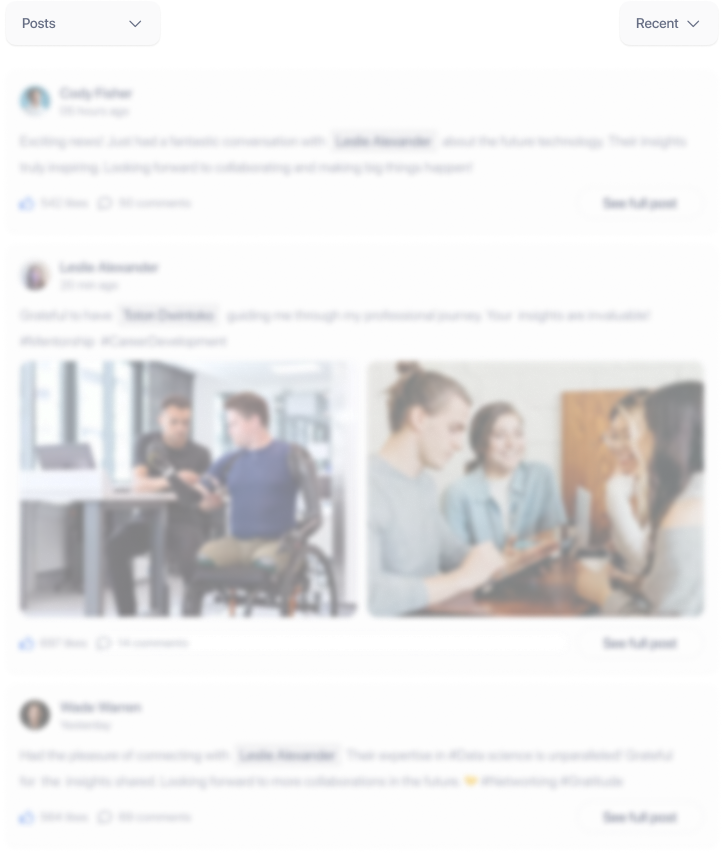