Myka Quinlivan
Senior Process Engineer - Manufacturing at Fortescue Future Industries- Claim this Profile
Click to upgrade to our gold package
for the full feature experience.
Topline Score
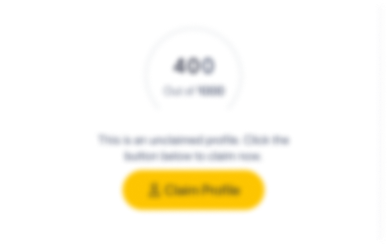
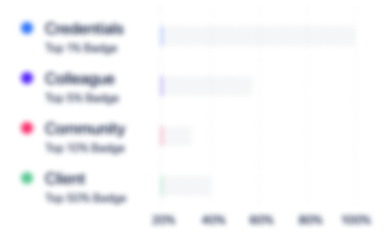
Bio


Experience
-
Fortescue Future Industries
-
Australia
-
Renewable Energy Semiconductor Manufacturing
-
700 & Above Employee
-
Senior Process Engineer - Manufacturing
-
May 2022 - Present
-
-
-
Technip Energies
-
France
-
Engineering Services
-
700 & Above Employee
-
Senior Process/Project Engineer
-
Dec 2018 - May 2022
-
-
-
Atkins
-
United Kingdom
-
Engineering Services
-
700 & Above Employee
-
Senior Process Engineer
-
Jan 2018 - May 2022
-
-
-
Momentum Engineering
-
Australia
-
Oil and Gas
-
1 - 100 Employee
-
Senior Process Engineer
-
Aug 2017 - Jan 2018
Process Engineering support for Orbost Gas Plant Project Detailed Design • Verification role within Owner Engineering Team to review process deliverables and vendor packages, and promptly resolve technical queries arising from project management of change and HAZOP. A key activity was reviewing the line list and rationalising low and high design temperatures to optimise valve selection during the critical phase for package procurement. Process Engineering support for Orbost Gas Plant Project Detailed Design • Verification role within Owner Engineering Team to review process deliverables and vendor packages, and promptly resolve technical queries arising from project management of change and HAZOP. A key activity was reviewing the line list and rationalising low and high design temperatures to optimise valve selection during the critical phase for package procurement.
-
-
-
Chevron
-
United States
-
Oil and Gas
-
700 & Above Employee
-
Process Engineer
-
Oct 2016 - Jan 2017
Provided process engineering expertise to support Project Execution of Wheatstone LNG Plant. • Developed the Wheatstone LNG Plant Chemical Management Plan, a critical document describing regulatory and Company health, safety and environment (HSE) protocols for safe selection, use and disposal of chemicals. • Defined design issues with chemical injection systems, including incorrect water and vessel material selection for a compressor cooling water loop, and proposed options for resolution with Project and vendors.• Performed procedural HAZOP reviews for safety- and production-critical operating procedures and advised close outs for technical queries on alarm and trip settings in Flare area.
-
-
Pre Start-Up Safety Review Coordinator
-
Jan 2016 - Oct 2016
Site-based role to support Project Execution and safe start-up of Wheatstone LNG Plant. • Facilitated all aspects of corporate pre start-up safety review (PSSR) process including PSSR training and proactively supported PSSR inspectors via subject matter expertise of PSSR process to ensure Specific, Measurable, Achievable, Realistic and Timely (SMART) checks, leading to improved action close out and clearer communications across shifts. • Coordinated multiple sub-system scopes for first gas introduction to align with commissioning and start-up schedule to ensure common knowledge between Commissioning, Operations and broader stakeholders. • Lead workshops between Commissioning and Operations teams to identify and agree on critical items and removal of non PSSR items. This significantly increased PSSR completion efficiency by eliminating circa 50% of checks duplicated in commissioning and checks not safety-critical for start-up.
-
-
Process Engineer
-
Dec 2012 - Dec 2015
Provided flow assurance and process engineering technical review expertise to support Gorgon LNG Project close out and facility improvements. • Performed technical and formal safety assessments for Subsea and Inlet units which led to: modifying alarm and trip set points to meet designed safety integrity limits (SIL) and as-building of subsea operating manuals, control and safeguarding narratives, P&IDs and PFDs to ensure accurate data for field start-ups. • Revalidated design phase HAZOP/SIL studies for debottlenecking the gas export pipeline and completed a management of change project to modify control hardware and logic to permit gas backflow at high rates required for start-up. This involved close collaboration with control and instrument engineers to define the safe operating window and redesign the control system to maintain operation within safe operating limits. • Participated in HAZOP/SIL revalidation workshops for Utilities, Subsea and Inlet units which improved safety integrity levels on the plant and reduced the burden on operator actions.
-
-
-
Atkins
-
United Kingdom
-
Engineering Services
-
700 & Above Employee
-
Senior Process/Flow Assurance Engineer
-
Jul 2012 - Nov 2012
Provided process and flow assurance engineering expertise for Oman Oil Company Exploration and Production (OOCEP) Abu Tubul Block 60 Gas Processing Plant detailed design phase. • Performed calculations and advised critical process design requirements for the plant relief and blowdown system and utility systems including fuel gas, hot oil, nitrogen and instrument air, to enable finalisation of mechanical and instrument datasheets, Heat and Material Balances and Cause and Effects. • Prepared safety-related process calculations and HYSYS simulations for flare capacity, hydrate formation and blowdown studies as required for equipment sizing and procurement.
-
-
Senior Process/Flow Assurance Engineer
-
Mar 2011 - Jun 2012
Provided process and flow assurance expertise during FEED and Detailed Design for INPEX Ichthys LNG Project. • Developed the subsea basis of design documents, ensuring clear presentation and accurate collation of a wide range of as-built design data from reservoir to onshore (e.g. production profiles, fluid compositions, well trajectories, pipeline bathymetries, pressure and temperature design limits, and onshore and topsides interfaces). • Conducted OLGA and PIPESIM simulations and prepared technical reports for various steady state and transient scenarios on wells, flowlines, gas export pipeline and MEG injection system. This work included detailed operability studies for the gas export pipeline including ramp-up and liquids surge, to enable finalisation of slug catcher sizing. • Advised newer team members on consistent application of as-built design data, as well as standard methodologies for calculations and technical reports to ensure high quality deliverables to the client.
-
-
Operations Support Engineer
-
Feb 2010 - Feb 2011
Seconded to Apache Energy to provide process engineering support to Ningaloo Vision FPSO during facility start-up and initial year of operation. • Monitored the facility’s production, uptime and safety management system performance against Contract expectations and raised deviations to Contracts team. • Defined and tracked-to-resolution specific issues where safety critical element performance standards, as given by the Safety Case, were not met or were poorly defined, including: swivel leakage, slow shutdown valve timings and disconnect/reconnect system performance issues.• Managed interface between Apache and FPSO Contractor engineering departments to resolve production constraints (e.g. slugging and poor oil-water separation performance) and safety device non-conformances, via procedural change and management of change projects as appropriate.
-
-
Senior Process/Flow Assurance Engineer
-
Oct 2008 - Feb 2010
Provided process and flow assurance expertise for detailed design of Woodside Pluto LNG Project. • Performed OLGA and PIPESIM flow assurance calculations and technical studies to develop field operating envelopes, including flowline and trunkline pigging, field start-up, and flowline/trunkline re/depressurisation scenarios.• Completed a detailed analysis of the MEG injection system hydraulic performance using PIPESIM models, which was used to optimise the MEG control system design under dynamic conditions. • Prepared procedures for managing critical transient scenarios including cold and warm well start-ups.
-
-
Operations Support Engineer
-
Jul 2007 - Oct 2008
Seconded to BHPB to support Griffin Venture FPSO safe operations and plant improvement projects at near to end of field life. • Conducted an extensive root cause investigation into gas export compressor liquid carry over and mechanical failure incident. The investigation included: a fluids sampling program to identify carryover from upstream equipment; Computational Fluid Dynamics (CFD) analysis of gas and liquid flow patterns in the compressor suction scrubber and scrubber sizing analysis; review of historical process conditions in PI historian and review of compressor valve failure history in Computerised Maintenance Management System (CMMS). This led to my recommendation to retrofit the scrubber with conventional internals to minimise carryover and prevent repeat compressor damage, and subsequently raised this modification via the BHPB management of change process.
-
-
Operations Support Engineer
-
Apr 2007 - Jul 2007
Seconded as Operations Support Engineer at Coogee Resources to support safe operation and plant improvement projects for Challis Venture and Jabiru Venture FPSOs. • Identified management of change opportunities to improve facilities' efficiency at end of field life including: modifications to the swivel leak recoup systems which were leaking excessively; and modifications to compression circuits to address gas lift compressor poor efficiencies and high discharge temperatures.
-
-
Process Engineer
-
Feb 2007 - Apr 2007
Process design for various small projects - Apache Energy Stag Platform well clean-up and produced water system upgrade; Arc Energy – Canning Basin Gas Recycle / Liquids Stripping Plant FEED; and Advanced Well Technologies – Theo-3 Well Test rig capacity review. • Conducted process calculations including line, control valve and equipment sizing and pump NPSH checks. • Developed heat and material balances and process flow diagrams.• Developed HYSYS simulations for optimisation studies, e.g. HP separator selection based on fuel gas requirements.
-
-
Process Engineer
-
Mar 2005 - Jan 2007
Site-based secondments as a Process and Project Engineer supporting safe operation and plant improvement initiatives at BP Kwinana Refinery. • Managed the progress of over 20 safety-related and energy improvement plant modification projects, including producing communication packs for Operations personnel for each project. • Conducted HAZOPs and commercial risk, design and constructability reviews for multiple concurrent plant modification projects for the Vacuum Distillation, Bitumen and other refinery units. • Troubleshot daily and long-term performance issues on Vacuum Distillation and Bitumen units such as trips, alarm management and heat exchanger fouling. • Conducted turnaround inspections of heat exchanger tube bundles, column tray installations, and catalyst loading.• Completed a 7-month review of relief valve sizing based on present operating conditions across the refinery units.
-
-
-
Clough
-
Australia
-
Construction
-
700 & Above Employee
-
Graduate Process Engineer
-
Jan 2003 - Mar 2005
Detailed design and pre-commissioning for two Greenfields projects, PNG Napa Napa Refinery for Interoil, and BassGas Plant for Origin Energy. • Conducted instrumentation and equipment hazardous area compliance inspections. • Validated the element-to-element testing of the fire and gas system and the SIS. • Conducted as-building of the cause and effect diagrams including modification of control software logic. • Prepared various process calculations and deliverables, including: as-building of P&IDs and isometrics for piping modifications; sizing of ROs, relief valves and lines; development of first fills list and equipment and safety system descriptions for operations manual. • Prepared hydrotest packs and conducted quality audits of hydrotesting during site-based role.
-
-
Education
-
Curtin University
Bachelor of Engineering - BE, Chemical Engineering -
Curtin Graduate School of Business
Graduate Certificate of Business
Community
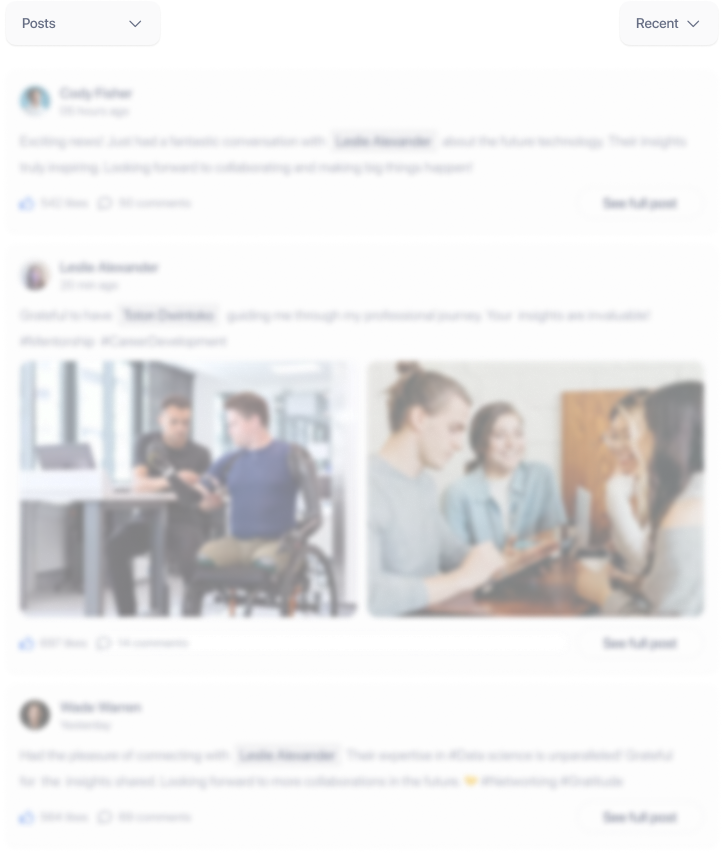