Mustafa Oztemel
Group Leader System Engineering at NTS-Group- Claim this Profile
Click to upgrade to our gold package
for the full feature experience.
-
English Full professional proficiency
-
Turkish Native or bilingual proficiency
-
Dutch Elementary proficiency
Topline Score
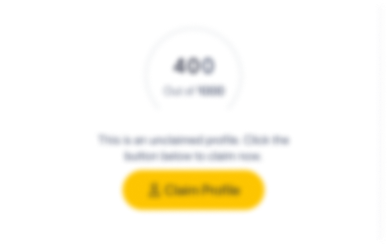
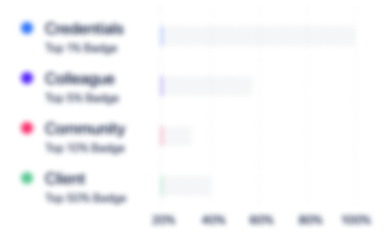
Bio


Credentials
-
IPMA - Level D
-Jan, 2017- Oct, 2024 -
Hardware in Loop Testing
dSPACE GmbH
Experience
-
NTS-Group
-
Netherlands
-
Industrial Machinery Manufacturing
-
400 - 500 Employee
-
Group Leader System Engineering
-
Oct 2021 - Present
-
-
-
TMC
-
Netherlands
-
Technology, Information and Internet
-
700 & Above Employee
-
Mechatronics Project Leader
-
Apr 2020 - Sep 2022
-
-
Junior Project Leader
-
Apr 2018 - Apr 2020
-
-
Mechatronics Development Engineer
-
Nov 2015 - Mar 2018
-
-
-
ASML
-
Netherlands
-
Semiconductor Manufacturing
-
700 & Above Employee
-
Main Deliverable Owner
-
Jun 2021 - Sep 2021
Project Manager of a complex production machine development Involved in- Project & Resource Planning- Project Risk Management- Suppliers Management
-
-
Mechatronics Lead Engineer
-
Dec 2019 - Jun 2021
Leading mechatronics development and system integration in complex machine development for Pellicle production improvements. Main responsibilities are• Architecture decomposition of the system• Mechatronics development for early HVM and HVM• System Integration planning and execution for PoP and HVMBeside the main responsibilities, I am involved in early phase of tool introduction to production process.
-
-
-
NTS-Group
-
Netherlands
-
Industrial Machinery Manufacturing
-
400 - 500 Employee
-
System Lead Engineer
-
Mar 2018 - Apr 2020
Development of ink supply module for high flow rate through-flow high precision print heads. Responsibilities are • Market research and concept development for high flow ink supply system • Design feasibility studies, including mechanical, electrical and SW development for test units • Direct leading mechanical design • Specify module requirements for electrical and SW team • Setting priorities to meet the project deadlines and follow-up development, including reporting to the Project Manager • Prepare module verification plan and merge to system integration plan Show less
-
-
-
Punch Powertrain
-
Belgium
-
Motor Vehicle Manufacturing
-
700 & Above Employee
-
Lead Hybrid Controls Engineer
-
Oct 2014 - Jan 2018
Leading Control development of Plug-in Hybrid Powertrain • SW architecture creation and assess customer SW change request for feasibility and compatibility for SW architecture and product requirements • Define WBS of Controls Development, SW testing, SW BASE development, Application teams • Setting priorities to meet the project deadlines and follow-up as a scrum master and reporting to the Project Manager • Setting-up continuous integration process for vehicle SW • Functional Safety Analysis and implementation • Creating V&V plan for the control unit and execute • Setting-up Hardware-in-Loop test environment for verification team • Troubleshooting and root-cause-analysis for validation failure • Translate the driver demand to optimal request for powertrain which consists of internal combustion engine and electric motor • Development of secondary functions, for instance: Stop-Start or Hill Hold Support Show less
-
-
-
Irmato
-
Eindhoven Area, Netherlands
-
Mechanical Engineer
-
Dec 2012 - Sep 2014
Working as a mechanical engineer who has the responsibility in following tasks • System modeling for dynamic/static analysis and simulation, • Leading group of 2-3 designers for design tasks, • Testing and Integration of clean-room products, • Safety assessment of mechanical designs (CE declaration), • Leading trainer of the clean-room products, • 3D CAD modeling, • Technical Product Documentation. Working as a mechanical engineer who has the responsibility in following tasks • System modeling for dynamic/static analysis and simulation, • Leading group of 2-3 designers for design tasks, • Testing and Integration of clean-room products, • Safety assessment of mechanical designs (CE declaration), • Leading trainer of the clean-room products, • 3D CAD modeling, • Technical Product Documentation.
-
-
-
ASML
-
Netherlands
-
Semiconductor Manufacturing
-
700 & Above Employee
-
Graduate Student
-
Jan 2012 - Oct 2012
Graduation Project: “Identification of a 3DOF Pizeo Driven Manipulator” Theoretical and experimental research on system identification and characterization of the limiting factors to performance improvement on piezo driven MIMO systems. Integrated experiments (ASML Sun system) and simulation (Matlab/Simulink) approach. Graduation Project: “Identification of a 3DOF Pizeo Driven Manipulator” Theoretical and experimental research on system identification and characterization of the limiting factors to performance improvement on piezo driven MIMO systems. Integrated experiments (ASML Sun system) and simulation (Matlab/Simulink) approach.
-
-
-
TNO Automotive
-
Helmond
-
Intern
-
Sep 2011 - Dec 2011
The project has focused on Integrated Powertrain Control(IPC) strategy calibration to minimize the operational cost within the legislated the NOx emission level for EURO VI regulations. The calibration method was developed in simulation environment via Matlab-Simulink and toolbox ADVANCE, which is developed by TNO. The project has focused on Integrated Powertrain Control(IPC) strategy calibration to minimize the operational cost within the legislated the NOx emission level for EURO VI regulations. The calibration method was developed in simulation environment via Matlab-Simulink and toolbox ADVANCE, which is developed by TNO.
-
-
-
Carnegie Mellon University
-
United States
-
Higher Education
-
700 & Above Employee
-
Intership
-
Jun 2009 - Sep 2009
“Design Path Generator” for Magnetically Actuated Micro Robot. The project focused on finding optimal path for micro robot to reach desired position with desired orientation to perform object manipulations for assemble purpose. “Design Path Generator” for Magnetically Actuated Micro Robot. The project focused on finding optimal path for micro robot to reach desired position with desired orientation to perform object manipulations for assemble purpose.
-
-
Education
-
Eindhoven University of Technology
Master of Science (MSc), Systems and Control -
Sabanci University
Bachelor of Science (BSc), Mechatronics Engineering; TURKEY -
Adnan Menderes Anatolian High School
High School, Science
Community
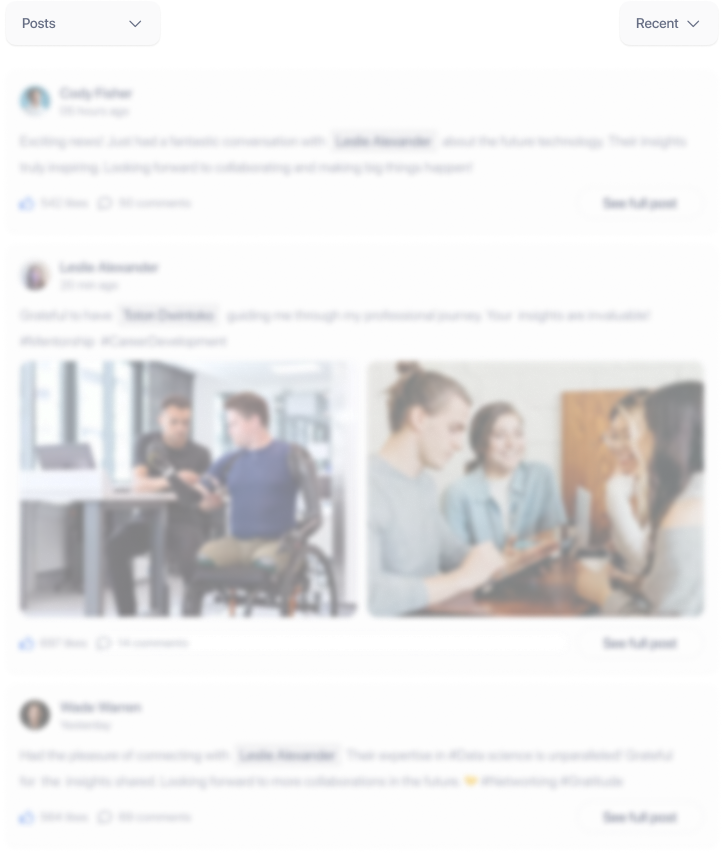