Munira Jayes
Operations Director at VITTLES FOODS LIMITED- Claim this Profile
Click to upgrade to our gold package
for the full feature experience.
Topline Score
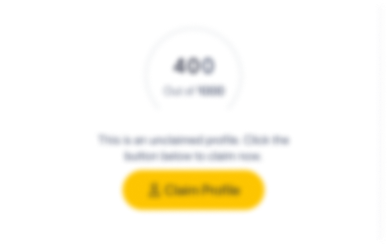
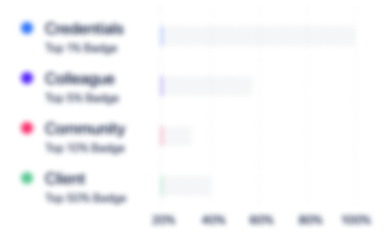
Bio

Seamus Gallamoy
I would absolutely recommend Munira as a top class leadership candidate for any operational roles. While I worked along with Munira she demonstrated a seriously impressive work ethic and pulled the team together under times of tremendous change within the business.

Jp Lee
I have worked with Munira for 18 months, she is very committed to her role and puts 110% in to everything, she is supportive through good and bad times, willing to pass experience and knowledge on, I am sure she will be an assist to any business

Seamus Gallamoy
I would absolutely recommend Munira as a top class leadership candidate for any operational roles. While I worked along with Munira she demonstrated a seriously impressive work ethic and pulled the team together under times of tremendous change within the business.

Jp Lee
I have worked with Munira for 18 months, she is very committed to her role and puts 110% in to everything, she is supportive through good and bad times, willing to pass experience and knowledge on, I am sure she will be an assist to any business

Seamus Gallamoy
I would absolutely recommend Munira as a top class leadership candidate for any operational roles. While I worked along with Munira she demonstrated a seriously impressive work ethic and pulled the team together under times of tremendous change within the business.

Jp Lee
I have worked with Munira for 18 months, she is very committed to her role and puts 110% in to everything, she is supportive through good and bad times, willing to pass experience and knowledge on, I am sure she will be an assist to any business

Seamus Gallamoy
I would absolutely recommend Munira as a top class leadership candidate for any operational roles. While I worked along with Munira she demonstrated a seriously impressive work ethic and pulled the team together under times of tremendous change within the business.

Jp Lee
I have worked with Munira for 18 months, she is very committed to her role and puts 110% in to everything, she is supportive through good and bad times, willing to pass experience and knowledge on, I am sure she will be an assist to any business

Credentials
-
Finance for Non-Financial Managers
LinkedInMay, 2021- Nov, 2024 -
Productive Leadership Tips
LinkedInJan, 2021- Nov, 2024 -
Post graduate Certificate & Diploma
Post Gradauate
Experience
-
VITTLES FOODS LIMITED
-
Food and Beverage Manufacturing
-
1 - 100 Employee
-
Operations Director
-
Apr 2022 - Present
Managing the manufacturing of cheesecakes & pastry deserts Managing the manufacturing of cheesecakes & pastry deserts
-
-
-
Simtom Food Products
-
United States
-
Food Production
-
1 - 100 Employee
-
Operations Controller
-
Jun 2021 - Aug 2021
Leading site operations Leading site operations
-
-
-
Samworth Brothers
-
United Kingdom
-
Food and Beverage Services
-
700 & Above Employee
-
Factory Manager
-
Dec 2019 - Jun 2021
Managing Mid shires Factory for major retailers. Managing site to deliver Business KPIs Support and drive site performances through key basic fundamentals and continuous improvement initiatives Implementing standards for labour to achieve better cost recovery Implementing site projects for efficiency and productivity Engage shop floor culture through change management Managing Mid shires Factory for major retailers. Managing site to deliver Business KPIs Support and drive site performances through key basic fundamentals and continuous improvement initiatives Implementing standards for labour to achieve better cost recovery Implementing site projects for efficiency and productivity Engage shop floor culture through change management
-
-
-
Dairy Crest - SAPUTO
-
Frome Somerset
-
Interim Operations Support Management
-
Jan 2019 - Dec 2019
Managing Operations of Production & Hygiene processing of cheese portioning & packing for all major retailers M&S, JS, Asda & Aldi • Managed Shift Manager to change work ethic to ‘Can do’ approach and deliver business KPI • Support and drive company initiative on business cost savings project through continuous improvement engagement • Increased OEE performance on nightshift and escalated on to shifts • Changed shop floor culture through engagement/trust and ownership. • Waste savings from 18 month losses to £k week on week Initially Joined on 6 mth contract as Shift Manager cover and within 2 months was promoted to support business and extended contract
-
-
-
Palethorpe Pork Farms Addo Group
-
Market Drayton
-
Interim Nightshift Operations Manager
-
Dec 2018 - Jan 2019
-
-
-
Bespoke Kitchen Foods
-
United Kingdom
-
Food and Beverage Manufacturing
-
1 - 100 Employee
-
General Manager
-
Jul 2017 - Dec 2018
Managing Business requirements with both factories producing Vegan Savoury and Sweet products. full accountability including Accounts/Budgets, Customer Services, Engineering, Health & Safety, Environment, Technical/NPD, Hygiene, Planning, HR, Training & Payroll. Production & Continuous Improvement. Implementing business vision & KPIs by increasing productivity and reducing cost as well as change management and engagement of staff. * Labours cost reduced from 16% to 14% * Factory KPIs created and benchmark on Average for Target - productivity increase by 15% * Negotiated contracts saving of 5%-10%
-
-
-
Dunkleys Ltd
-
United Kingdom
-
Food and Beverage Manufacturing
-
1 - 100 Employee
-
Operations Director
-
Aug 2007 - Jul 2017
Managing Business KPIs, increasing productivity and reducing cost to maximise profit margin as well as change management and continuous improvement. Responsible for Customer services, Engineering, Health & Safety/Environment, Hygiene, Planning, HR, Training & Payroll, budget, daily production and continuous improvement * labour cost saving year on year 6% * Yr on Yr Productivity growth by 20% from 10M to 30M in 2016 * BRC Yr on Yr from Grade 'C' to Grade 'A' and 'AA' version 7 Managing Business KPIs, increasing productivity and reducing cost to maximise profit margin as well as change management and continuous improvement. Responsible for Customer services, Engineering, Health & Safety/Environment, Hygiene, Planning, HR, Training & Payroll, budget, daily production and continuous improvement * labour cost saving year on year 6% * Yr on Yr Productivity growth by 20% from 10M to 30M in 2016 * BRC Yr on Yr from Grade 'C' to Grade 'A' and 'AA' version 7
-
-
-
Boots Manufacturing
-
Nottingham, United Kingdom
-
Production Manager
-
2005 - 2007
Managing factory department producing licence product Nurofen and Body Scrubs through all business KPIs, Safety/Quality/Quantity & Cost. Engaging and developing staff to multi-skilling and changing culture as strong unionised site for continuous improvement. * Production lines OEE & Output increased from 50% to 60% * Improved Plan Attainment to 100% * Developed an individual to become motivated and drive productivity Managing factory department producing licence product Nurofen and Body Scrubs through all business KPIs, Safety/Quality/Quantity & Cost. Engaging and developing staff to multi-skilling and changing culture as strong unionised site for continuous improvement. * Production lines OEE & Output increased from 50% to 60% * Improved Plan Attainment to 100% * Developed an individual to become motivated and drive productivity
-
-
-
The Cheese Company
-
Food and Beverage Manufacturing
-
1 - 100 Employee
-
Senior Production & Engineering Manager
-
2003 - 2005
Responsibility for all factory Operations, Production, H&S, HR and Engineering. Managing short & long term strategy planning in all departments by increasing productivity, reducing labour cost & waste in line with the budgets and PIP cost-saving projects. Engaging and developing staff through clear objectives. H&S compliance on accident reduction. Engineering engagement and improve equipment performance. * Crumbing cost saving reducing labour & increasing productivity - 40% saving on current * Staff labour re-structure saving 8% Yr on Yr * H&S Audit level from 0 to level 2 improvement
-
-
-
SOLWAY FOODS LIMITED
-
United Kingdom
-
Food and Beverage Manufacturing
-
1 - 100 Employee
-
Materials/ / Prep Manager
-
2002 - 2003
Managing 3 factories producing sandwiches and mayonnaise in the preparation departments. Full site responsibility of material managment in line with Business KPIs. Engaging and developing staff. * implemented Process controls for Material management * Reviewed Planning to meet maximise material usage as fresh ingredients Managing 3 factories producing sandwiches and mayonnaise in the preparation departments. Full site responsibility of material managment in line with Business KPIs. Engaging and developing staff. * implemented Process controls for Material management * Reviewed Planning to meet maximise material usage as fresh ingredients
-
-
-
Kettleby Foods Samworth Brothers
-
Melton Mowbray
-
Area Shift Manager
-
2002 - 2002
Managing a shift department for ready meals from Goods in, Prep/Cook, Assemble, Pack and Goods out. Responsibility for the day to day operation taking into account H&S, Quality, Quantity & Cost in line with business KPIs. Developing staff and engaging for efficient run with controlled labour and reduced waste., maintaining Quality and increasing Quantity. * Visual Management implemented - Performance displayed to engage control * Short interval controls to manage changeovers and labour * Variance reporting and planning of prep to assembly to manage downtime and waste
-
-
-
Bourne Salads
-
Spalding
-
Shift Production / Continuous Improvement Manager
-
2002 - 2002
Project Management for the site producing Salads. Implementation of a scoping study created by me to review cultural and efficiency, breakdown barriers for continuous improvement. Presented findings/conclusion and provided/trained Managers for implementation. * Implemented 'CANDO' (workplace organisation * set up committee to breakdown barriers identified in the scoping study Project Management for the site producing Salads. Implementation of a scoping study created by me to review cultural and efficiency, breakdown barriers for continuous improvement. Presented findings/conclusion and provided/trained Managers for implementation. * Implemented 'CANDO' (workplace organisation * set up committee to breakdown barriers identified in the scoping study
-
-
-
McVitie's UK
-
United Kingdom
-
Food and Beverage Manufacturing
-
1 - 100 Employee
-
Team Manager / Continuous Improvement Manager
-
1997 - 2002
Responsible for an area producing variety of biscutis from chocolate Digestives/Chocolate hobnobs etc.. on a day to day production in line with H&S, Quality, Quantity & Cost business KPIs. Managing and organised the project management of a a pilot world class manufacturing of TPM and Workplace Orgnisation. Pilot programme defined and organised by own preparation/scoping study of culture and efficiency as well as engaging Engineering and Production staff. * Line Efficiency from project OEE achieved consistant instead of sporadic * Change over reduced from 1 hour to 10mins and engaging strong unionised Engineers * Communication changed to visual management in monetary value for staff to understand
-
-
-
THE JACOB'S BAKERY LIMITED
-
Leicester, United Kingdom
-
Leader / Continuous Improvement Facilitator
-
1986 - 1997
The role at Jacobs biscuit manufacturer was where my management career started. At the age of 17 I was employed for 11 years and over this period I carried out varied roles and was promoted along the way from machine operator to creating all the training documents and becoming train the trainer. I was asked to be a supervisor/chargehand recognise my personal style of management, engaging staff and delivering business results. KPIs and implementation of World Class Manufacturing techniques. I was selected to work with consultants and implement pilot programme throughout the site. I also did work on Technical Procedure implementation and was champion for the sites Continuous Improvement as well running lines/areas.
-
-
Education
-
De Montfort University
MBA - Masters Degree, Masters of Businesss Administration -
De Montfort University
Post-Graduate Degree, Diploma in Management Studies -
De Montfort University
Post-Graduate Degree, Certificate in Management Studies -
South Wigston College
NEBSM Diploma NVQ level, Supervisory Management -
South Wigston College
NEBSM Supervisory Management, Certificate of Supervisory Management -
Billinge High School
CSEs, High School/Secondary Certificate Programs
Community
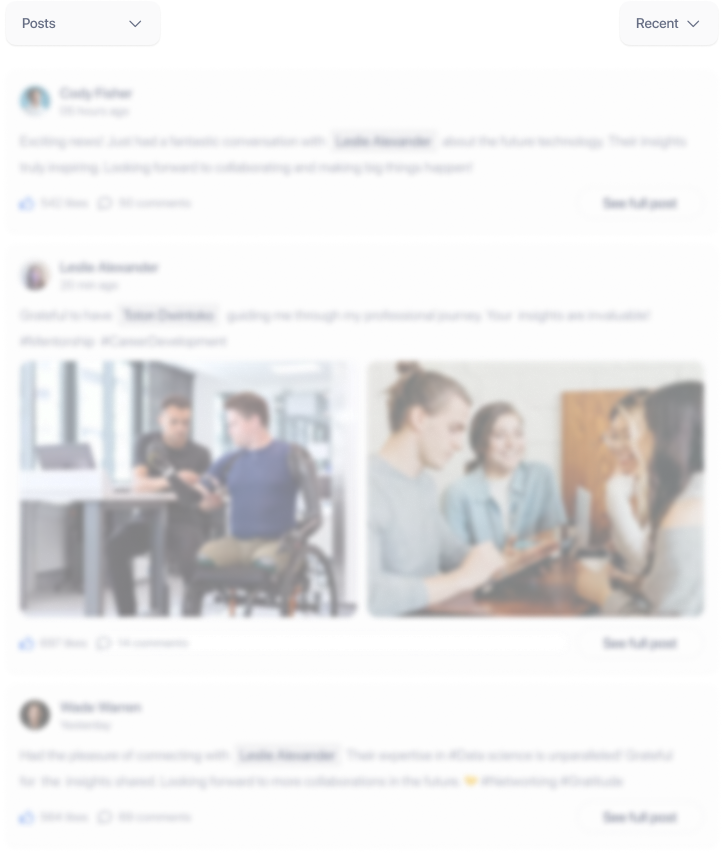