Mungesh Simon Peters
Continuous Improvement/ Lean Program Manager at Nor-Am Cold Storage- Claim this Profile
Click to upgrade to our gold package
for the full feature experience.
-
English -
-
Swahili -
Topline Score
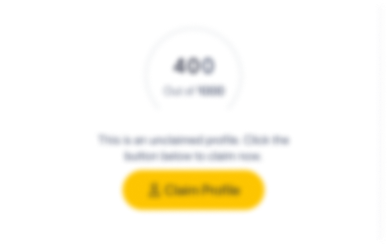
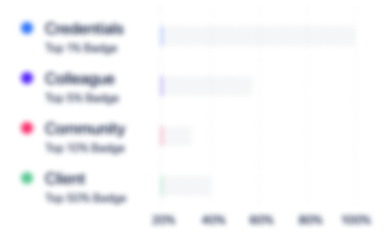
Bio

Md T Jaman
Mungesh brings values to the AGCO business. He works with the value stream and continuous improvement teams. He is supporting the paint shop, and he is responsible for delivering the right part with the right color to the assembly shop. I appreciate his work ethic. I found him a hard working, sincere and co-operative person. It was a pleasure working with him.

Irene Karanja
I met Simon Mungesh in 2006 whilst on a joint government/Civil Society program to resettle poor families in Nyeri. He was on holiday then. He is committed and supportive to local governance issues in Kenya.

Md T Jaman
Mungesh brings values to the AGCO business. He works with the value stream and continuous improvement teams. He is supporting the paint shop, and he is responsible for delivering the right part with the right color to the assembly shop. I appreciate his work ethic. I found him a hard working, sincere and co-operative person. It was a pleasure working with him.

Irene Karanja
I met Simon Mungesh in 2006 whilst on a joint government/Civil Society program to resettle poor families in Nyeri. He was on holiday then. He is committed and supportive to local governance issues in Kenya.

Md T Jaman
Mungesh brings values to the AGCO business. He works with the value stream and continuous improvement teams. He is supporting the paint shop, and he is responsible for delivering the right part with the right color to the assembly shop. I appreciate his work ethic. I found him a hard working, sincere and co-operative person. It was a pleasure working with him.

Irene Karanja
I met Simon Mungesh in 2006 whilst on a joint government/Civil Society program to resettle poor families in Nyeri. He was on holiday then. He is committed and supportive to local governance issues in Kenya.

Md T Jaman
Mungesh brings values to the AGCO business. He works with the value stream and continuous improvement teams. He is supporting the paint shop, and he is responsible for delivering the right part with the right color to the assembly shop. I appreciate his work ethic. I found him a hard working, sincere and co-operative person. It was a pleasure working with him.

Irene Karanja
I met Simon Mungesh in 2006 whilst on a joint government/Civil Society program to resettle poor families in Nyeri. He was on holiday then. He is committed and supportive to local governance issues in Kenya.

Credentials
-
Lean Six Sigma Black Belt Training
Sealed Air CorporationApr, 2021- Nov, 2024 -
Strategic Customer Service Skills Certified (SCSSC)
Management & Strategy InstituteSep, 2020- Nov, 2024 -
Problem Solving Techniques Certified (PSTC)
Management & Strategy InstituteAug, 2020- Nov, 2024 -
Advanced Communications Skills Certified (ACSC)
Management & Strategy InstituteJul, 2020- Nov, 2024 -
Certificate of Achievement Dale Carnegie (CADC) Program
Dale Carnegie TrainingJul, 2020- Nov, 2024 -
Time Management Skills Certified (TMSC)
Management & Strategy InstituteJun, 2020- Nov, 2024
Experience
-
Nor-Am Cold Storage
-
United States
-
Warehousing and Storage
-
1 - 100 Employee
-
Continuous Improvement/ Lean Program Manager
-
May 2022 - Present
• Coordinating inter-plant continuous and Lean improvement activities • Redeploying a standardized Lean platform across multiple plants • Development of improvement activities and coordinated implementation and best practices sharing • Working with regional VPs to develop a realistic strategic Hoshin plan and horizontal alignment • Management of the Lean Program, structural elements and training program • Championing of Continuous improvement principles and development of Lean culture • Managing and facilitation of the digital and visualization overarching objective within the organization and framework and systems to support that. • Re-orienting of the KPMs framework to meet manufacturing per excellence through optimization of current process efficiency and resource utilization metrics and standardizing the same. Show less
-
-
-
PPC Flexible Packaging
-
United States
-
Packaging and Containers Manufacturing
-
1 - 100 Employee
-
Plant Lean Engineering Lead
-
Jun 2021 - Apr 2022
• Provides guidance and support in regard to Lean manufacturing processes. • Facilitates development, evaluation and improvement methodologies • Drives good manufacturing practices and benchmarking them to leverage cost reduction, productivity and quality improvement, and on-time customer delivery. • Responsible for leading plant-wide Lean activities and deployment of key Lean tools such as 6S, A3 Process, 6S, Kaizen events, PFEP, Material flow Analysis, Safety, Problem solving, etc. • Acts as a change agent leading continuous improvement • Responsible for facilitating key projects to improve quality, reduce costs, improve cycle time, etc., through waste reduction. • Trains employees in the basics of lean manufacturing and train production teams in lean manufacturing initiatives such as Kanban, Value Stream Mapping, Takt Time Analysis, and Kaizen. • Leads Lean waste reduction activities within the processes and works with teams • Member of Management of change management (MOC) teams on site. • Provides Lean training to key stakeholders, such as Safety, Quality, Production and/or Maintenance departments. • Collaborates with Maintenance and Production on Preventative Maintenance (PM) recommendations for optimal product quality and machine uptime. Supports review and deployment of TPM Metrics • Facilitates Kaizens and SMED activities on site working with other functional team members. • Works with process teams to capture best practice machine setup parameters, to support deployment of Standard Operating conditions (SOC), Leader Standard Work (LSW), Health checks, etc., for key machines and processes. • Works with teams to review and improve efficiencies, machine utilization, material flow, space, and floor layout. • Works with site managers in implementation of the Hoshin plan, development of activities, milestones, etc. • Helps with facilitation of Lean Daily Management System (LDMS) Tiered accountability structure on site. Show less
-
-
-
Sealed Air Corporation
-
United States
-
Packaging and Containers Manufacturing
-
700 & Above Employee
-
Performance Improvement Leader
-
Jul 2018 - Jun 2021
• Responsible for CI efforts for the site and ensuring business objectives are in • alignment with KPI’s, department KPI goals, and improvement initiatives. • Responsible for implementation, success and sustainability of the Performance Management • System (PMS) across the site. • Acts as the Initiator, leader and facilitator for continuous improvement initiatives focused on • improving performance, while acting as the change agent, challenges the status quo. • Working with the plant manager in developing and proposing goals which support strategic business objectives for the site. Ensure these goals are cascaded throughout the site and also ensure improvement initiatives are in place to reach these goals (Hoshin plan) • Ensuring the PMS is implemented and sustained through verification at all levels of the organization. This includes having an effective system in place that ensures audits are taking place at all levels of responsibility. • Acts as the owner of the continuous improvement tools and their application on site. Developing and execution of coaching of all levels of the site on the PMS with a focus on 3 principles of lean leadership; Go See, Ask Why, and Always Show Respect. • Ensures proper training is provided for all levels to support and sustain the Performance Management System including lean tools to support the system. • Responsible for tracking performance to targets and make sure the PCDA cycle is • functioning in a manner that addresses gaps. • Supports the site with global improvement activities and initiatives. • Participating in new projects from planning phases and throughout the implementation to ensure • the Lean/6s principles are applied including Kaizen's and A3s. • Leading and facilitating cost savings projects in WAVE. • Leading the team and training on knowledge-based manufacturing (KBM) best practices. Show less
-
-
-
AGCO Corporation
-
United States
-
Machinery Manufacturing
-
700 & Above Employee
-
Manufacturing Process/ Continuous Improvement Engineer
-
Sep 2011 - Jun 2018
• Identification of bottlenecks, continuous improvement, and decision sciences • Working with SQE, DE, and Manufacturing planners to drive best practices • Line flow analysis , capacity optimization, and value stream mapping • Development and execution of KPI’s, Training on LDMS • Working with a robust paint system – Wet to Wet application, e-coat, Powder coat • Designing paint system fixtures to facilitate material movement, painting, and immersion • Working with Engineering to set up paint recipes, paint routes, and paint maintenance plans • Working with Quality and product engineering to trouble shoot and resolve finish surface issues • Training design engineering on critical success factors for paint -Design for paint (DFP) • Aligning MRP scheduling to production system (Flexnet) for parts requiring Finish specs • Developing cost reduction and productivity measures for the new paint system • Developing SOPs, Work Instructions, and project charts for the new Paint System • Facilitating continuous improvement projects through team efforts • Make versus buy decisions, material flow analysis, and Cost of production analysis • Leveraging QCDS to optimize system uptime, throughput, RFT, and on-time performance • Leading efforts to troubleshoot quality and productivity issues • Improving New Paint System productivity- Tooling, SOP’s, Layout, Show less
-
-
-
Institute for Research on Global Business (IRGB)
-
Greater Chicago Area
-
Operations Director (Pro Bono)
-
Mar 2007 - Jan 2011
• Responsible for all operational aspects of the organizations forums and scheduling. • I and my colleagues ensured all papers were peer reviewed to ensure accuracy and adherence. • I personally authored various papers and presented in a number of forums. • Responsible for all operational aspects of the organizations forums and scheduling. • I and my colleagues ensured all papers were peer reviewed to ensure accuracy and adherence. • I personally authored various papers and presented in a number of forums.
-
-
-
LSI, an Avago Technologies Company
-
Semiconductor Manufacturing
-
700 & Above Employee
-
Business / Production Analyst
-
Apr 2006 - Jun 2008
• Gathering and analyzing daily production data • Working with the Plant Director to develop and roll out QCDS metrics • Highlighting trends and opportunities based on production, Cost, Delivery and Quality data • Preparation of Key reports related to production performance, resource management, scheduling • Working with cross functional teams as needed to design, test out and execute new processes • Execution of key reports impacting production metrics such as throughput, on-time performance, right first time, and line flow. • Helped in development of line models. Show less
-
-
-
Wolters Kluwer Tax & Accounting US
-
United States
-
IT Services and IT Consulting
-
700 & Above Employee
-
Release and Support Analyst
-
Dec 2005 - Dec 2006
• Tested Accounting and Tax Engagement software • Integrated, backed up, migrated, and executed data. • Pulled and pushed design docs • Helped with customer support • Wrote, tested script for bugs and performed system stress test • Tested Accounting and Tax Engagement software • Integrated, backed up, migrated, and executed data. • Pulled and pushed design docs • Helped with customer support • Wrote, tested script for bugs and performed system stress test
-
-
Education
-
Friends University
Master of Science in Operations Management (MSOM) -
Newman University
Masters of Business Administration (MBA), International Business -
Wichita State University
Masters of Science in Industrial Engineering (MSIE) -
Wichita State University
Bachelors of Business Administration (BBA), Management Information Systems, General
Community
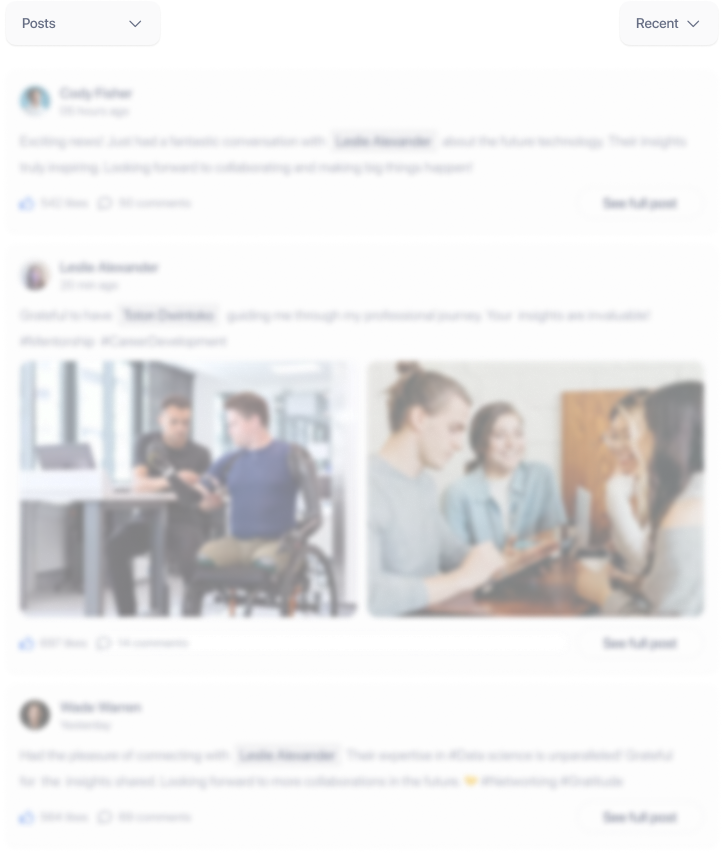