Moritz Büsing
Engineer for Aircraft Predesign - Structural Analysis Methodologies - Certification at AutoFlight- Claim this Profile
Click to upgrade to our gold package
for the full feature experience.
-
German Native or bilingual proficiency
-
English Full professional proficiency
-
Japanese Elementary proficiency
Topline Score
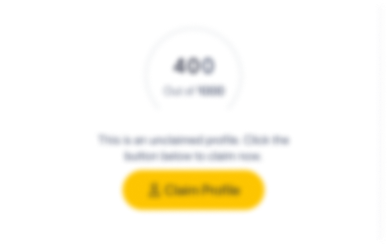
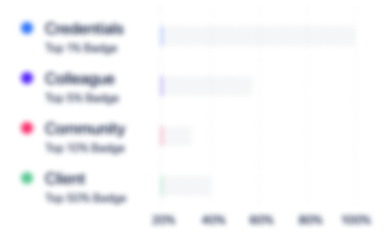
Bio


Experience
-
AutoFlight
-
Germany
-
Aviation and Aerospace Component Manufacturing
-
1 - 100 Employee
-
Engineer for Aircraft Predesign - Structural Analysis Methodologies - Certification
-
Apr 2022 - Present
Contribution to the aircraft specification based on experience with helicopters sales campaigns (what do customers want), helicopter predesign (perfomance, structures) and competition analysis (what is our advantage). I perform predesign studies with focus on aerodynamic stability (static and dynamic), perfomance and structures. For this I use efficient vortex lattice and vortex particle tools for quick iteration loops. These low fidelity simulations are periodically validated and corrected with CFD and flight test data. The performance is analysed with parametrised scripts that simulate individual flight phases and missions consisting of sequences of flight phases. I identified the structural requirements and loads based on SC-VTOL and other regulations. I developed the structural concepts of the aircraft. These are two concepts for EASA certification and CAAC certification. I am developing the structural part of the design manual with material selection, parts classification, static analysis using handbook methods and Finite Element methods, fatigue analysis methods and damage tolerancs analysis methods. I create mass and balace estimates based on a combination of bottom up approaches, such as structural sizing, and top down using empirical weight functions. I also optimize the lift rotors aerodynamically for efficiency and low noise, and structually for strength and reduced vibrations. Show less
-
-
-
Airbus Helicopters
-
France
-
Aviation & Aerospace
-
700 & Above Employee
-
Engineer for the Products Policy and Architecture Department
-
Sep 2020 - Apr 2022
-
-
Structural Analysis Engineer for Rotors and Rotorcontrols, Work Package Manager
-
May 2013 - Sep 2020
• Static strength, fatigue strength and damage tolerance analysis of the following parts of the so called “dynamic system”:o Rotors of various helicopters consisting of composites and metal parts.o Mechanical flight control partso Hydraulics such as pumps, actuators, accumulators, valves, lines and dampers • Creation of test orders and analysis of test resultso Composite coupon tests o Component testso Monitoring of flight tests (loads and performance)• Serial support:o Production support (quality notes, concessions)o Definition and substantiation of repair criteriao Classification and analysis of incidents and definition of corrective and preventive measureso Verification of supplier substantiation documents.o Answering customer questions• Methods and Tools developmento Programming of in-house-toolso FE Methods exploration, validation, implementationo Member of the industrial panel “Industrieausschuss Struktruberechnung” for the advancement of the “HSB” structural analysis manual• Work package management for the static and fatigue analysis of the dynamic system of the Tiger helicopter (rotors, controls, hydraulics) for serial support and upgrades. Show less
-
-
Structural Analysis Engineer, Rotors and Rotorcontrols
-
Dec 2011 - May 2013
• Static substantiation of the main rotor blades and mechanical rotor control elements for the research project "Bluecopter", including analyses, test definition and test evaluation.• Serial support for EC135 and Tiger main rotor blades. Static and fatigue substantiation of quality notes, concessions and repairs.
-
-
-
Airbus Defence and Space (Space Systems, Inc.)
-
700 & Above Employee
-
Diploma Thesis Student
-
May 2011 - Oct 2011
Work on my Aerospace Engineering Diploma Thesis: Creation of a tool for multidisciplinary parameter studies for aircraft predesign. This tool consists of a preprocessor for the structural and aerodynamic models and the links between these for the proprietary solver "Lagrange". The sizing of the structural elements is automated through optimization algorithims for a set of flight states and resulting load cases. Work on my Aerospace Engineering Diploma Thesis: Creation of a tool for multidisciplinary parameter studies for aircraft predesign. This tool consists of a preprocessor for the structural and aerodynamic models and the links between these for the proprietary solver "Lagrange". The sizing of the structural elements is automated through optimization algorithims for a set of flight states and resulting load cases.
-
-
-
Premium AEROTEC GmbH
-
Germany
-
Aviation and Aerospace Component Manufacturing
-
700 & Above Employee
-
Engineering Intern
-
Jul 2010 - Oct 2010
• Designed parts and fixtures using CATIA V5. • Infiltrated, machined and assembled CFRP-parts. • Drafted, constructed, and programmed an electrical drive for a flap. • Designed parts and fixtures using CATIA V5. • Infiltrated, machined and assembled CFRP-parts. • Drafted, constructed, and programmed an electrical drive for a flap.
-
-
-
Airbus
-
France
-
Aviation and Aerospace Component Manufacturing
-
700 & Above Employee
-
Intern
-
Jul 2005 - Oct 2005
• Introduction to the manufacturing technologies and Airbus business culture. • Airplane chassis parts machining, assembly, and quality control. • Introduction to the manufacturing technologies and Airbus business culture. • Airplane chassis parts machining, assembly, and quality control.
-
-
Education
-
Technische Universität München
Diplom-Ingenieur, Luft- und Raumfahrttechnik, Aeronautik und Astronautik -
慶應義塾大学
Keio University: Japanese language program
Community
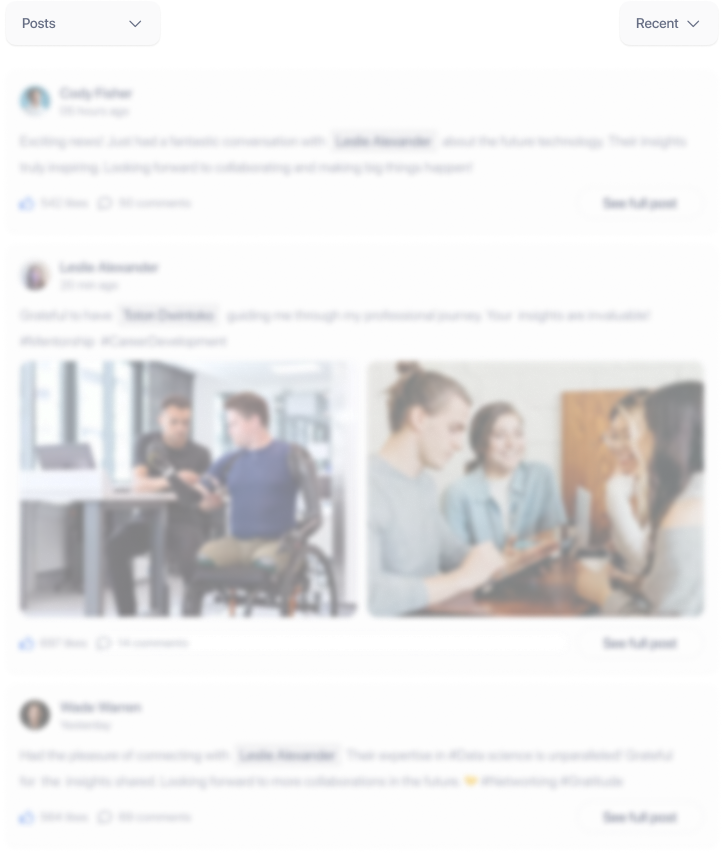