Mohd Norazam Shah Md. Anoorhak Change for Betterment
Vice President, Continual Improvement at MIDF- Claim this Profile
Click to upgrade to our gold package
for the full feature experience.
Topline Score
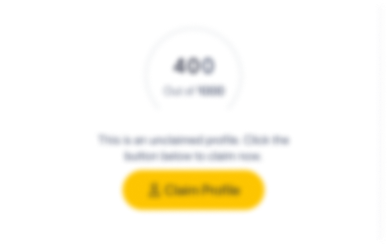
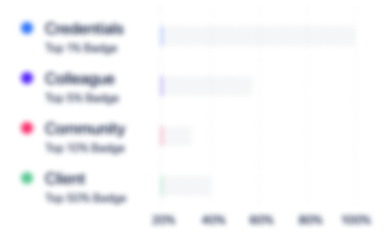
Bio
0
/5.0 / Based on 0 ratingsFilter reviews by:
Credentials
-
Certified IMS Lead auditor
SIRIM QAS International -
Lean Six Sigma Black Belt (ICBB)
MBizM Group -
Lean Six Sigma Green Belt (ICGB)
Sony Electronics
Experience
-
MIDF
-
Financial Services
-
200 - 300 Employee
-
Vice President, Continual Improvement
-
May 2023 - Present
- Developing the Process improvement project journey. - Identify CI project via SLPR and SLA performance and P & P. - Facilitate and conduct training to project team members. - Managing and controlling the Policy and Procedure. - Developing framework and methodology in managing Documentation the whole group. - Introduce Record Management control. - Establish Customer Management Methodology. - Developing the Process improvement project journey. - Identify CI project via SLPR and SLA performance and P & P. - Facilitate and conduct training to project team members. - Managing and controlling the Policy and Procedure. - Developing framework and methodology in managing Documentation the whole group. - Introduce Record Management control. - Establish Customer Management Methodology.
-
-
-
Malakoff Corporation Berhad
-
Malaysia
-
Utilities
-
400 - 500 Employee
-
Strategic Business Process Improvement
-
Apr 2022 - May 2023
-
-
Process Improvement Specialist
-
Oct 2015 - Apr 2022
•Change management agent in company, establish lean six sigma methodology to improve company performance to ensure the Business, Financial, Process and operational run smoothly.•Establish DMAIC methodology, plan, develop and manage systematic approach in analyzing and evaluation of current systems, business processes, practices and structures within the company. Conduct analysis and study the current weaknesses in the specific business process areas. Provide recommendations and advice improve specific processes and practices while ensuring the internal controls are adequately in place.•Coaching, guide, train and mentoring staff in implementation of process improvement.Collaborate with all stakeholder such as Corporate Division, Subsidiary on Improvements initiative•Identify and lead the study to analyse specific work processes and provide recommendations to improve the existing work-flow to improve organization’s efficiencies. •Establish plans and manage organization’s Business Process Improvements (BPI) programs. Act as the champion for BPI initiatives within the organization.•Plan and manage the implementation of systematic examination approach in analyzing and evaluation of current systems and structures.• Implement Policy & Procedure gap analysis to promote continuous improvements for both compliance and methodologies as well as best practices to stakeholder•Conduct regular review on work methods and operational practices Process mapping VSM, Root cause analysis (why-why anakysis, tree diagram, DEsign of experiment DOE•Review and monitor the implementation recommendations including recording and analyzing Malakoff’s business flow charts, records, reports and manuals.Project In pipeline1. Procurement Improvement2. HR Improvement3. Finance Improvement Show less
-
-
-
Malaysia Airports
-
Malaysia
-
Airlines and Aviation
-
700 & Above Employee
-
Operational Excellence/ Business Transformation /LeanSixSigma Specialist Manager
-
Mar 2012 - Oct 2015
- Manage alignment of overall company - Embark Lean Six Sigma improvement program in company - Develop DMAIC methodology in Transformation Initiative implementation - Manage process performance by comparing against SLS, identify and analyze the causes for divergence - Provide consultation, facilitate, assist and monitor to others - Manage coordination across the various Operating Companies, Subsidiaries and Corporate Centre Divisions in the company to improve process performance that leads to improvement of service delivery. - Manage platforms that would be able to motivate people to generate innovative ideas, implement the initiatives and enhance the capability of achieving company’s objectives. - Formulate and manage development of initiatives that are to maximize company’s value - Provide consultation, facilitate and assist company performance - Utilizing the right methodologies for an effective cost and capital management such as life cycle costing, lean management, Lean six sigma etc. - Develop and implement Manpower optimization throughout company using Manpower mapping, FTE, Productivity and Job evaluation - Train, coach, guide and mentoring team on develop all staff in lean six sigma methodology using ICC and QCC tools. - Develop change management/culture on business process using, Kaizen, 5S, poka yoke, TPM & etc. - Knowledge Sharing on continuous improvement Completed Projects 1) Improvement on baggage system - improve eff. 65%, cost saving 2.4mil and improve customer satisfaction 25%. 2) Improvement on toilet management - improve cust satisfaction 45%, reduce cost 35% and improve availability by 90% 3) Reduce revenue gap on PBB - revenue increase by 37% 4) Centralize maintenance contract - reduce cost by 42%, improve availability by 88% 5) Manpower enhancement through productivity monitoring - cost saving by 37%, improve process efficiency 78% Total cost saving 2012-2013 : 18mil Show less
-
-
-
MARDEC Berhad
-
Malaysia
-
Rubber Products Manufacturing
-
1 - 100 Employee
-
Senior Quality and Industrial Engineer
-
Jan 2010 - Mar 2012
Improvement program (Lean/six sigma Project) - Define & analyse opportunities for improvement in term of financial, productivity, and quality. - Implement productivity improvement activities through identification of area for improvement such as process mapping, time study, line balancing, optimize process capability study, root-cause-analysis and etc. - Lead and manage team of process engineering to ensure productivity, quality, cost and efficiency are controllable and monitoring. - Study and recommend measures to improve manufacturing cost and efficiency. - Develop and review existing processing standard time for each of plant - Develop and maintain model for capacity planning both equipment performance and manpower variables. - Develop and implement productivity improvement and cost saving project through lean six sigma methodology. - Evaluate and develop standardization of work processes, procedures and operating systems for the manufacture of existing products - Design and optimize the space utilization taking into consideration of equipment requirement, product flow, manpower and cost. Project implementation: Project Title: Mardec Business Improvement Program Improvement Objective: Reduction of conversion cost Thru productivity improvement Status: Completed Project Title: Mardec Business Improvement Program Improvement Objective: Introduction of new production operating system and Maintenance operating system Status: In-progress installation to oversea plant Project Title: Mardec Improvement activity Improvement Objective: Optimization and enhance process capability Status: Completed Show less
-
-
-
Texas Instruments
-
United States
-
Semiconductor Manufacturing
-
700 & Above Employee
-
Production And Quality Engineer
-
Mar 2006 - Jan 2010
- Technical knowledge through new product development. - SME in specific segment of product development technology and utilize expertize in delivering timely, cost effective - To carry out new product process for process robustness - Development of new process assembly, new product investment, and propose suitable - Interface with quality team, designer and mechanization team on process and product optimization. - Provide training to operators and technician on process and equipment related. - Establish and maintain process documentation including WI/FMEA/control plan/process flow/SOP. - Continuously improve the process capability in term of through-put, cost effectiveness and process quality (Yield, OEE, Poka Yoke, PPM). - Drive and implement product optimization and execution of evaluation using analysis tool such as FMEA, SPC, DOE, TFA, 8D. - Research, Explore, Develop, sourcing and testing new material for product robustness eg: 1. Lead-frame 2. .Mold compound 3. Deflash chemical Complet d projects Project: MSL1 Improvement on QFN Status: Qualify Ni roughen Lead-frame Improvement: Customer quality satisfaction Project: Stress Relief and additional low k/stress Status: Implement to all LF design Improvement: Reduction on Warpage issue. Project: Ni roughen Lead-frame Status: Implement to new package/devices Improvement: Improve adhesion, Control RBO, improve MSL performance. Project: Under die delamination on Automotive Status: Finalize material through modeling and evaluation Improvement: Eliminate delamination issue on Automotive Project: New charge weight Status: Qualify for production material Improvement: Eliminate wastage on mold compound. Project: New mold compound and extension clean mold Status: Production run Improvement: Cost reduction, Quality improvement and cycle time reduction Technical involvement Technical paper presentation on Adhesion improvement and MSL improvement Show less
-
-
-
Sony Electronics
-
United States
-
Computers and Electronics Manufacturing
-
700 & Above Employee
-
Production Engineering/ Quality engineer
-
May 2003 - Mar 2006
- Streamline the Lean Six Sigma on continuous improvement program in company, improve daily quality /efficiency performance of production line. - Design and procure production tooling, processing equipment and process workstation. Train, coach, guide and mentoring team on: - Minimize change over time by ensuring program use common set ups where possible. - Verify that machine maintenance is being performed on schedule. - Reduce machine/jigs downtime by monitoring the machine performance and taking corrective action to improve. - Analyse work force utilization, facility layout and operational data such as production cost and process flow and charts - Adhere all safety and health rules and regulations directed by supervisor such as ISO 9001, OHSAS 18001 - Prepare monthly reports on engineering performance, safety progress Project implemented: Project1: Zero hours breakdown per week Objective: Eliminate breakdown and improve machine capability Status: Reduce breakdown time from 15hrs/week to 1hrs/week. Project2: Lean manufacturing Objective: eliminate waiting time and eliminate man factor Status: Optimize the parameter for reduce cycle time – 2 times process Project3: Safety Project Objective: Eliminate hazard and improvement on production & evacuation in-out Status: 60% implement completed with accident& failure reduce. Show less
-
-
Education
-
Universiti Tenaga Nasional
Degree (Hons), Electrical and Electronics Engineering
Community
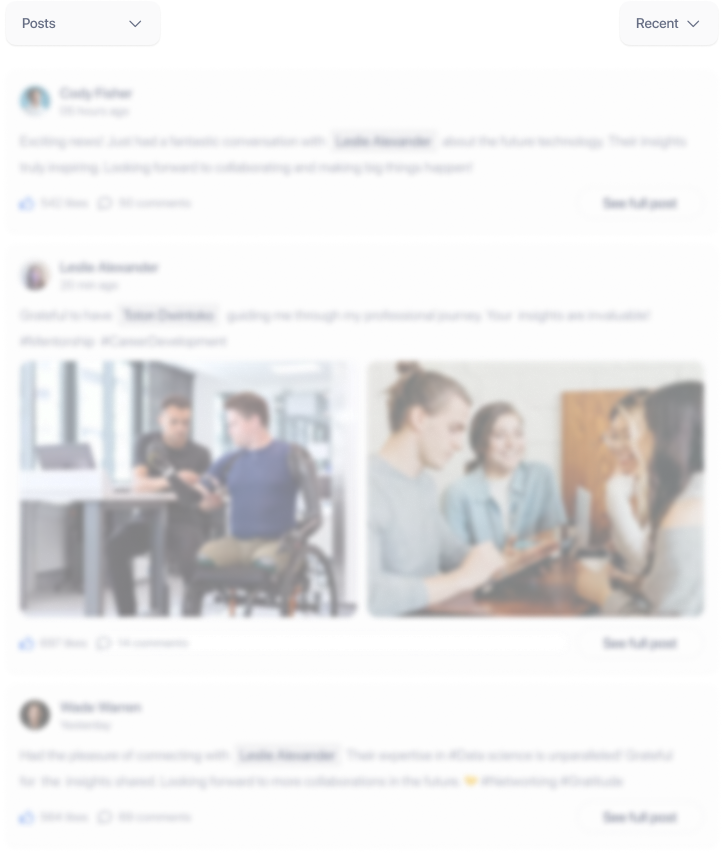