Mohd Isma
Head (Product Safety & Sustainability) at Petronas Chemicals Group Bhd (PCHEM)- Claim this Profile
Click to upgrade to our gold package
for the full feature experience.
-
English Professional working proficiency
-
Bahasa Malaysia Native or bilingual proficiency
Topline Score
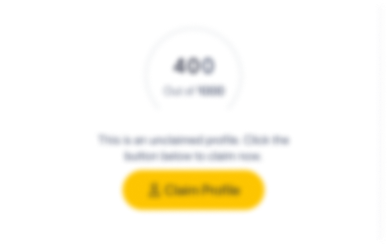
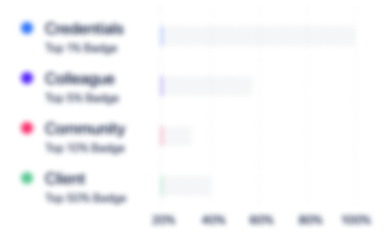
Bio


Experience
-
-
Head (Product Safety & Sustainability)
-
Oct 2019 - Present
-
-
-
DuPont Malaysia
-
Malaysia
-
Wholesale Import and Export
-
1 - 100 Employee
-
Country Product Stewardship & Regulatory Affairs
-
Aug 2011 - Oct 2019
Country PSRA (Product Stewardship & Regulatory Affair) Coordinator 1. Commitment to Compliance with Corporate Requirements and Government Regulations * Support /execute new chemical notifications, hazardous chemical registrations and food contact/food additives registrations in Malaysia * Implement volume reporting process in Malaysia * Complete GHS implementation scheduled tasks for Malaysia 2. Strengthen the PS&R Capability in ASEAN/South Asia region * Strengthen management and monitor capability of local product & application specific regulation compliance * Support the simplification of MSDS creation processes and effective MSDS MOC (Management of Change) process * Communicate/roll-out relevant global advocacy positions (GHS classification and Labeling, etc) * Develop the career development plan and mentoring program * Continue to drive the strengthening of in-country PS&R business network * Improve the PS&R engagement with suppliers, operations, contract manufacturers & distributors network through supporting businesses 3. Improve Productivity and Effectiveness of PS&R Implementation and Performance Measurement * Implement FSOP standardized checklist in Malaysia * Actively support the completion of FSOP simplification and automation project and improve FSOP import/export processes within ASEAN/South Asia * Clarify roles and responsibilities, needs, opportunities, gaps within the new collaborative center team * Support productivity metrics development for newly-established collaborative center 4. Increase Business Value through Product Sustainability and Advocacy Initiatives * Support distributors and contract manufacturer’s regulations training and PS&R campaign in R&D process such as Product Commercialization Framework (PCF) * Effective advocacy on key issues in Malaysia N&R scheme and GHS * Strengthen country management engagement in PS&R activities and processes Show less
-
-
-
DuPont Malaysia Sdn Bhd
-
Malaysia
-
Wholesale Import and Export
-
1 - 100 Employee
-
Country SHE Coordinator (PSM/Fire/Contractor/ER/M&A/Distribution/Occupational Safety)
-
Aug 2011 - Aug 2019
Country SHE (Safety, Health & Environment) Coordinator a.Provide SHE leadership across entities in the country, including manufacturing sites, R&D facilities, technical centers, training centers and offices; b.Provide SHE functional guidance for all business activities in the country, including manufacturing, contract manufacturing, tolling, licensing and sale activities; c.Support new business development including major construction project, Merger & Acquisition project on request by Supply Chain SHE Leadership d.Lead country SHE networks and competency networks; e.Participate in country SHE council/ committee and serve as SHE resources; f.Develop and maintain country SHE policies; g.Define & implement Country SHE COTs for continuous improvement; h.Help to assess and develop SHE competencies for entities in the country; i.Network with global and regional SHE competency leaders and resources to leverage best practices; j.Support SHE 2nd party audit program; k.Lead SHE & Security country function team, provide support to operation SHE, product stewardship & regulatory team, and Emergency Response team; (SHE / PS & R/ Security) l.Responsible for country SHE managing processes including but not limited to SHE compliance, SHE communication, SHE reporting m.Work with government agencies and NGOs on SHE advocacy roles to promote Corporate Image and Reputation at some countries. (PS&R) Show less
-
-
-
DuPont Powder Coatings
-
Plastics Manufacturing
-
1 - 100 Employee
-
Country SHE/ Maintenance Engineer
-
Jan 2007 - Jul 2011
Head of Mechanical & Electrical Department (a) Responsible for the maintenance and safety of the overall plant. (b) Plan, schedule, organize and implement preventive, corrective, predictive, proactive maintenance program and energy saving program (c) Develop, implement and maintain standard working procedures for maintenance activities from PID and manuals. (d) Plan, organize and lead a team of maintenance technicians to perform maintenance works including facilities equipment and preventive maintenance. (e) Responsible to ensure that company are compliance to all legislated regulations, company policies and procedures based on the local law requirements of the machinery act (f) Work closely with the production, laboratory, store and office so that the company equipment are in good order. (g) Support production team so that the plant output meets the targets set by the management (h) Build up good network of supporting vendors/suppliers for plant spares and repairs. (i) Ensure sufficient work force is available to perform maintenance activity and hold regular meetings with staff to discuss performance and problems. (j) Ensure good housekeeping of the plant. (k) To keep inventory of spare parts for plant equipment and introduce bin card system & systematic storage racking arrangements. (l) Maintain and review the procedure as laid out in ISO 14001, ISO 9001, SHE and appointed as Internal auditor. (m) To participate in continuous improvement at DPCM site eg. Lean implementation, Kaizen , Value Accelerator and etc. (n) Manage a team of technician to do upgrading project of machineries for better performances. Provide them with technical info & data analysis of machinery benchmarking. (o) Provide online job coaching and offline job training to the subordinate, prepare test bench for equipment used in plant to enhance their skill, knowledge, competency and technical expertise Show less
-
-
-
-
HSE Coordinator/ PSM Site Resource
-
Jan 2007 - Mar 2011
HSE Coordinator (a) Focal person on safety issues, updating incident cases - safety, PSM, OH, Distribution, Environment, Fire and Driving safety into internal tracking system web site. (b) Chair the monthly safety meeting, develop schedule for weekly and monthly safety first party audits. Initiate monthly safety program, highlight safety concerns, path forward and second party audit follow up. (c) Established yearly site safety critical operating task which in line with global platform direction, keep focus on achieving the goal of zero incidents, be prudent and think ahead of program implemented to safeguard people, machinery and business from major safety setback. (d) Prepare safety manuals and ensure site comply with local authorities requirement, site policy and Dupont policies. (e) Implement Line of fire program, hazard identification, task risk analysis, electrical safety, do not touch, lock out tag out, perform corrective action and make sure all findings are close. (f) Perform incident investigation & classification. Report is complete enough which comprehensively consider other factors such as PSM, environmental, distribution safety, fire and occupational health. Using RCFA and 5 why’s method on drilling in to find the actual cause of the fault. (g) STOP (Safety Training Observation Program) audits, looking at deficiencies to be corrected on reactions of people, personal protective equipment, positions of people, tools and equipment, procedure and orderliness standards. (h) Plant Audit (first party audit) on housekeeping, PSM, environmental, distribution, fire and distribution are conducted monthly. (i) Responsible on Managing Process Safety in the plant - Establishing a safety culture, Providing management leadership and commitment, Implementing a comprehensive Process Safety & Risk Management program and Achieving operating excellence through operational discipline based on PSM’s 14 elements. Show less
-
-
-
Megasteel Sdn Bhd
-
Malaysia
-
Software Development
-
Senior Executive
-
Sep 1997 - Dec 2006
Plant Operation and Engineering section ( Caster Electrical ) (1) Head of electrical section for maintenance group (a) To plan and prepare a comprehensive maintenance schedule, daily check list, effective maintenance guide and efficient troubleshooting steps for plant machineries through Computerised Management Maintenance Schedule (CMMS) inclusive of electrical & instruments items. (b) To ensure all daily check list, work order and predictive maintenance check list are genuinely executed and completed as promptly as schedule. (c) Prepare procedure, standard operating practices and work instructions for each equipments from PID and manuals. (d) Designed work permit and incident report forms for maintenance department in order to perform works in very systematic channel. (e) Control on inventory and spare parts to ensure parts are available. Show less
-
-
Education
-
UUM/NIOSH
Master of Science (MS), Occupation Safety and Health Management -
University Utara Malaysia/ NIOSH
Master's degree, Occupational Safety & Health -
University Sains Malaysia
Bachelor of Engineering (BEng), Electrical and Electronics Engineering
Community
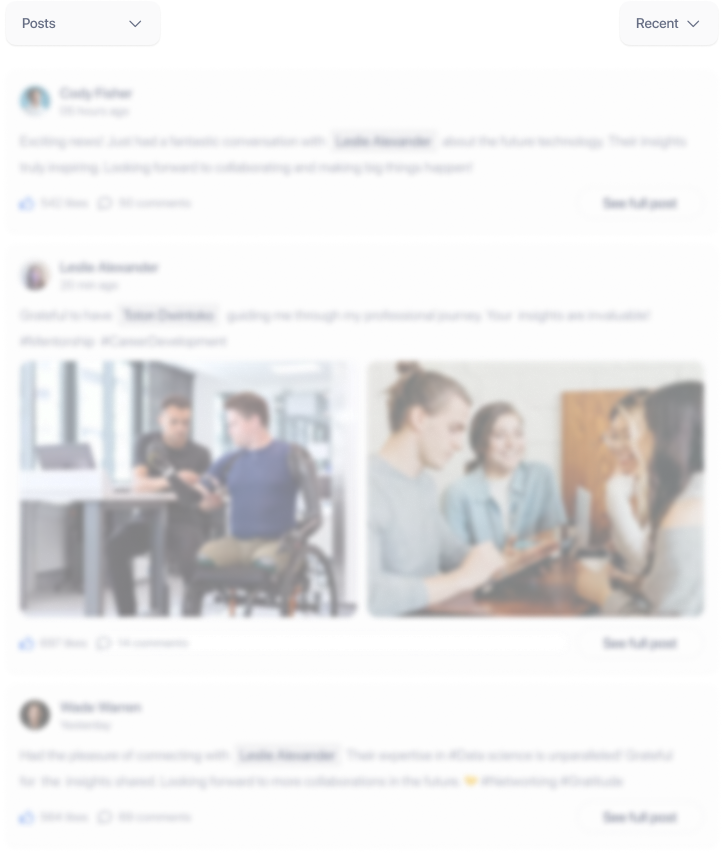