Mohammed Luqhman Basha
Outgoing Quality Control Engineer at LS Automotive- Claim this Profile
Click to upgrade to our gold package
for the full feature experience.
-
Tamil Native or bilingual proficiency
-
UDRU Native or bilingual proficiency
-
English Full professional proficiency
-
Hindi Full professional proficiency
-
Arabic Elementary proficiency
Topline Score
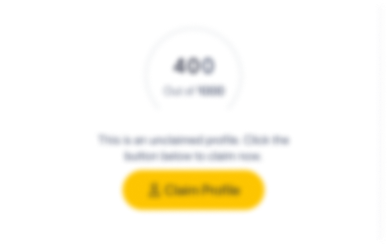
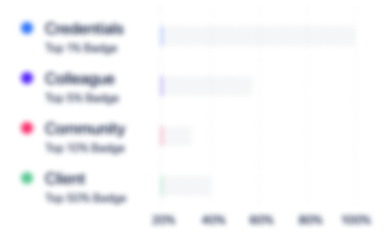
Bio

Indukumar TR
Mohammad Luqhman Basha I can recommend as a person with great proficiency and deep experience of solutions. Mohammad Luqhman Basha is a self motivated and wise person but also an inspiring perfectionist. Creative strategist with great interpersonal skills. Customer focused and honest team player. If you ever need someone to deliver under pressure, no slip-ups, just results, Mohammad Luqhman Basha is your go-to person

Indukumar TR
Mohammad Luqhman Basha I can recommend as a person with great proficiency and deep experience of solutions. Mohammad Luqhman Basha is a self motivated and wise person but also an inspiring perfectionist. Creative strategist with great interpersonal skills. Customer focused and honest team player. If you ever need someone to deliver under pressure, no slip-ups, just results, Mohammad Luqhman Basha is your go-to person

Indukumar TR
Mohammad Luqhman Basha I can recommend as a person with great proficiency and deep experience of solutions. Mohammad Luqhman Basha is a self motivated and wise person but also an inspiring perfectionist. Creative strategist with great interpersonal skills. Customer focused and honest team player. If you ever need someone to deliver under pressure, no slip-ups, just results, Mohammad Luqhman Basha is your go-to person

Indukumar TR
Mohammad Luqhman Basha I can recommend as a person with great proficiency and deep experience of solutions. Mohammad Luqhman Basha is a self motivated and wise person but also an inspiring perfectionist. Creative strategist with great interpersonal skills. Customer focused and honest team player. If you ever need someone to deliver under pressure, no slip-ups, just results, Mohammad Luqhman Basha is your go-to person

Credentials
-
Master in Mechanical CADD
International Accreditation forum joint Accreditation system of Australia & New ZealandNov, 2018- Nov, 2024
Experience
-
LS Automotive
-
South Korea
-
Motor Vehicle Manufacturing
-
300 - 400 Employee
-
Outgoing Quality Control Engineer
-
Jun 2021 - Present
-
-
Process Quality Control Engineer
-
May 2021 - Jun 2021
- Analysing, handling and reporting of all quality issues and actively participating in Corrective Action Committee processes.- Responsible for communication with customer regarding customer claims - 0km, field complaints.- Responsible for handling and fulfillment of 8D reports related to customer quality issues.- Ishikava, 5 Why, 8D, SAP, PPAP, APQP, SPC, FMEA- Leading and working closely with the internal team on the 8D problem-solving process.- Coordinating corrective actions with the internal engineering team as well as coordinating actions with teams.- Root Cause Analysis to resolve manufacturing issues and recommend solutions to prevent recurrence.- Working directly with the customer's supplier quality and engineering teams to resolve existing and prevent future quality issues.- Preparation of regular reports/analysis on customer claims and customer satisfaction.
-
-
-
Renault Nissan Technology & Business Centre India
-
India
-
Motor Vehicle Manufacturing
-
700 & Above Employee
-
Compliance Engineer
-
May 2021 - May 2021
- Expertise in IMDS and ELV regulations.- Good Knowledge on BOM (Bill of Material) Analysis.- IMDS supplier MDS evaluation as per the Customer guideline and Recommendation 001.- MDS Creation for inhouse MDS as per the BOM requirement.- Understanding of GADSL and Application codes used in IMDS system.- Having a good communication skill to request all the Suppliers to submit the MDS on time - Expertise in IMDS and ELV regulations.- Good Knowledge on BOM (Bill of Material) Analysis.- IMDS supplier MDS evaluation as per the Customer guideline and Recommendation 001.- MDS Creation for inhouse MDS as per the BOM requirement.- Understanding of GADSL and Application codes used in IMDS system.- Having a good communication skill to request all the Suppliers to submit the MDS on time
-
-
-
KOSTAL Group
-
Germany
-
Motor Vehicle Manufacturing
-
700 & Above Employee
-
Customer Quality Engineer
-
Jun 2020 - May 2021
- Applying, controlling, managing and coordinating all internal and external rules, instructions, procedures and policies related to the strong quality standards of the Automotive industry.- Analysing, handling and reporting of all quality issues and actively participating in Corrective Action Committee processes.- Resposinble for communication with customer regarding customer claims - 0km, field complaints and tracking the cost related.- Responsible for handling and fulfillment of 8D reports related to customer quality issues.- Ishikava, 5 Why, 8D, IQUIDOSS, SAP, PPAP, APQP, SPC, FMEA- Leading and working closely with the internal team on the 8D problem-solving process.- Coordinating corrective actions with the internal engineering team as well as coordinating actions with teams from other Kostal Group plants.- Root Cause Analysis to resolve manufacturing issues and recommend solutions to prevent recurrence.- Working directly with the customer's supplier quality and engineering teams to resolve existing and prevent future quality issues.- Preparation of regular reports/analysis on customer claims and customer satisfation.
-
-
Process Quality Engineer
-
Jul 2019 - Jun 2020
- Analyzing, handling and reporting of all quality issues- Handled Weekly and Monthly Process Audits and Products Audits.- Worked with department heads for yearly IATF Audits and has Knowledge in IATF Audits.- Tracked Line issues on Daily basis and Analyze it to find root-cause and corrective actions with CFT team.- Handled Quality related devices such as VMS, Profile projector, Torque/ Linear Tactile machines, Acoustic chamber and Illumination chamber.- Knowledge in SAP and Expert in IMDS.- Knowledge in PPAP and APQP.- Kaizen Activities.
-
-
System and Documentation Engineer
-
Feb 2019 - Jul 2019
-
-
-
Mahindra & Mahindra Ltd., FES, Swaraj Division
-
Motor Vehicle Manufacturing
-
700 & Above Employee
-
Work Manager
-
Jul 2018 - Feb 2019
- Keep a record of sales and restock the store accordingly.- Manage and train store staff.- Mediate any confrontations between staff and clients, and de-escalate the situation.- Accomplishes department objectives by managing staff; planning and evaluating department activities.- Ensures a safe, secure, and legal work environment.- Accomplishes staff results by communicating job expectations; planning, monitoring and appraising.- Maintains quality service by enforcing quality and customer service standards, analyzing and resolving quality and customer service problems, and recommending system improvements.- Assigning and designating job duties to staff according to their performance and history.- Maintaining a positive, empathetic and professional attitude toward customers at all times.- Responding promptly to customer inquiries.- Communicating with customers through various channels.- Acknowledging and resolving customer complaints.- Present reports and updates to the general manager on work activities.- Knowing our products inside and out so that you can answer questions.- Keeping records of customer interactions, transactions, comments and complaints.- Providing feedback on the efficiency of the customer service process.- Ensure customer satisfaction and provide professional customer support.
-
-
-
TVS Motor Company
-
India
-
Motor Vehicle Manufacturing
-
700 & Above Employee
-
Factory work organizer
-
Sep 2015 - Jan 2018
- Gathering students who are all financially backward and making use of those students to work on their free time.- Organising work for those students on contract basis in factories based on their abilities.- Explaining about the work and giving an opportunity to adapt work life environment while studying.- Giving opportunity to overcome Enochlophobia.- Avoiding students from distracting in their free time.- Giving opportunity to know the value of self earned money while studying.
-
-
Education
-
Adhiyamaan college of Engineering
B.E, Mechanical Engineering -
Dalhousie University
MS, Industrial Engineering
Community
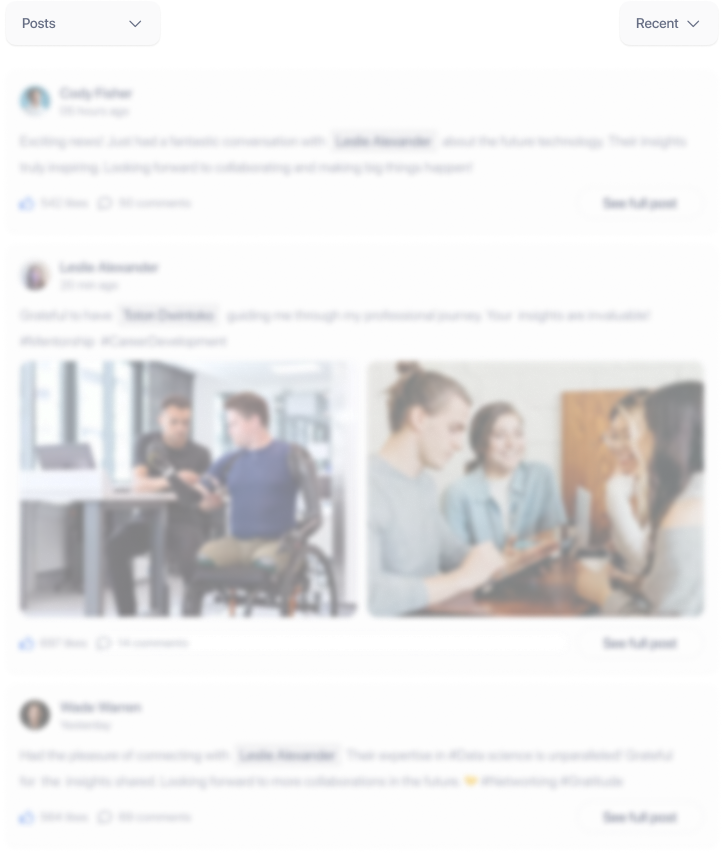