Mohammad Kader Ashrafee
Manager - Production, Warehouse, QA and WSS at Rahimafrooz Renewable Energy Ltd. (RREL)- Claim this Profile
Click to upgrade to our gold package
for the full feature experience.
Topline Score
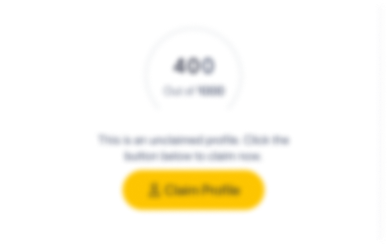
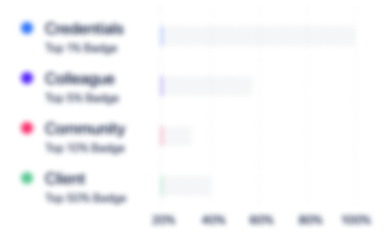
Bio


Credentials
-
Finance Training – Solar (Intro to financial modelling for rooftop solar)
German Energy Solutions Initiative, Project Development Programme (PDP)Jan, 2022- Nov, 2024 -
Digital German Training – Solar (PV System Design and Engineering PV System Installation and Mounting Structure Simulation Software & Solar Irradiation Measurement PV System Operation and Maintenance)
German Energy Solutions Initiative, Project Development Programme (PDP)Nov, 2021- Nov, 2024 -
The Executive Program on Production Management through TPS
by The association for overseas technical cooperation and sustainable partnership (AOTS), Japan.May, 2018- Nov, 2024 -
Cost Reduction & Workplace Organization Through 5S
bdJobs.com, Bangladesh. -
Internal QMS Auditing (ISO 9001:2000
Management System Services, Bangladesh. -
Mastery of Self through Neuro Linguistic Programming (NLP)
SENSEI INTERNATIONAL. -
Training on “Negotiation Skill”
Absolute Solutions Ltd., Bangladesh.
Experience
-
Rahimafrooz Renewable Energy Limited
-
Bangladesh
-
Renewable Energy Semiconductor Manufacturing
-
1 - 100 Employee
-
Manager - Production, Warehouse, QA and WSS
-
Sep 2016 - Present
Key Accountabilities:• Prepare production plan (Daily, weekly and monthly) and delivery in line with internal & external expectations• Ensure product quality and control quality process • Prepare SOP and update agreed/required reports for management information and review.• Prepare budget and control the cost of PV plant as per agreement with line manager.• Ensure quality of work, cost control and continual improvement • Facilitate completive and effective sourcing of RM and other materials as per business requirement• Maintain & update records of all materials for management information.• Ensure assembly operations as per process instruction and maintain documents in line with ISO 9001 QMS requirements and company policy. • Ensure maintenance of plant and machinery to maximize machine up time by continual updating of policies and procedures• Coordinate with QA & other sections to ensure quality as per standard & company policy • Ensure continuous cost improvement for product competitiveness, maintaining targeted wastage percentage and productivity and cost ratios.• Assess and ensure the quality of incoming raw materials, intermediate and finished product as per standard.• Maintain and calibrate measuring instrument as per standard and schedule.• Oversee receiving, warehousing, delivery and maintenance operations of factory and trading warehouse• Plan, implement and utilize optimum use of warehouse space.• Reconcile inventory with ERP software• Attend & solve call from POs/Business partner regarding complains & warranty claims.• Check the faulty received goods whether it is falls under warranty claims or not.• Test and return defective materials found faulty after testing and send it to their factory.• Reduce warranty cost (by controlling wastage/rejections/implementation new innovation) to achieve continuous cost improvement.• Ensure safety and security of people and company assets• Imitate and plan for training and development of people Show less
-
-
Sr. Executive, Production
-
Sep 2012 - Aug 2016
-
-
Executive, DC Electronics Assembly
-
May 2007 - Aug 2012
-
-
Sr. Officer, Assembly and Store
-
Oct 2006 - Apr 2007
-
-
-
Navana Electronics Ltd.
-
1 - 100 Employee
-
Service In-Charge
-
Aug 2003 - Oct 2006
Key Accountabilities: • Maintenance and trouble shooting of IVS, UPS (Off-Line & On-Line), Substation equipments (Transformer, LT/HT/PFI panel), IPS, AVR, Battery Charger, ATS etc.• Oversee incoming emergency on call/ complaints via the phone, email and assures that a proper and timely responses are made. • Organize, control & improve the activity and productivity of service dept. in order to provide the best support activities.• Assure and control the balance between available capacity and support services planning/workloads.• Ensure promptly on call services, quality of work, cost control, continual improvement and timely bills submission including keeping of documents and records.• Manage and develop service personnel to facilitate an environment where employees are empowered and willing to initiate process improvements within the service department.• Make sure customer complaints are dealt within a structured time frame, logged and initiating appropriate corrective action as necessary.• Ensure standard procedures & processes are adhered to and only proper documents/tools/resources are used or employed.• Developing relations with new customers• Supporting the existing customer on regular basis Show less
-
-
UPS Section In-Charge
-
Sep 2001 - Jul 2003
Key Accountabilities: • Assisting Head of production in production planning to meet in time production based on sales forecasted by Marketing & Sales Department • Development, production, supervision & testing of UPS (Off-Line & On-Line)• Production process development plan for minimizing material wastage and reducing cost comparing competitors • Conducting time and motion study to determine gap/redundancy in production manpower • Preparing and submitting of monthly raw material requirement sheet, monthly material consumption report and monthly production report to the management • Monitoring and controlling day to day raw material requirement as per production target and accordingly manage the material by perusing related department • Attending Quality circle meeting with different section employees, problems identification, solving plan and submit to management Show less
-
-
-
Electro Mechanical Services
-
1 - 100 Employee
-
Service Engineer, Technical Department.
-
Nov 1998 - Aug 2001
Key Accountabilities: • Supervising installation, commissioning and maintenance of diesel & gas generator and On-line UPS. • Preparing maintenance schedule & ensure maintenance as per schedule. • Prepares reports, analyzes data, and makes recommendations for improving operations system and solving maintenance-related problems. • Ensure customer complaints are dealt within a structured time frame, logged and initiating appropriate corrective action as necessary. • Timely bills submission & collection including keeping of documents and records. • Ensure quality of work, cost control and continual improvement • Plan, manage and improve the productivity of service department. • Assure and control the balance between available capacity and support services planning/workloads. • Ensure standard procedures & processes are adhered to and only proper Documents/tools/resources are used or employed • Ensures that maintenance technicians are adequately training & Skill Development, equipped, and motivated so that the maintenance program can be accomplished in a safe, timely, and cost-effective manner. Show less
-
-
-
Micro Electronics Ltd
-
United Kingdom
-
1 - 100 Employee
-
Assistant Production & Service Engineer.
-
Mar 1996 - Oct 1998
Key Accountabilities: • Prepare production plan in line with sales demand and marketing plan. • Ensure operations as per process instruction and maintain documents in line with company policy. • Implement and achieve production planning. • Up to date modification of the diagram AVR & UPS. • Testing and quality checked of AVR & UPS. • Ensure servicing for the product which is given by our company or any other company to the customer. • Drawing the production plane of AVR & UPS. • Follow the production lines and checked regulation step by step. • Motivate work force and develop subordinates to enhance productivity • Implement Safety, Health & Environment regulations as per requirement & company policy • Build team spirit within the work force Show less
-
-
Education
-
University of Information Technology & Sciences (UITS)
Bachelor of Science (BSc), Electronics & Communication Engineering
Community
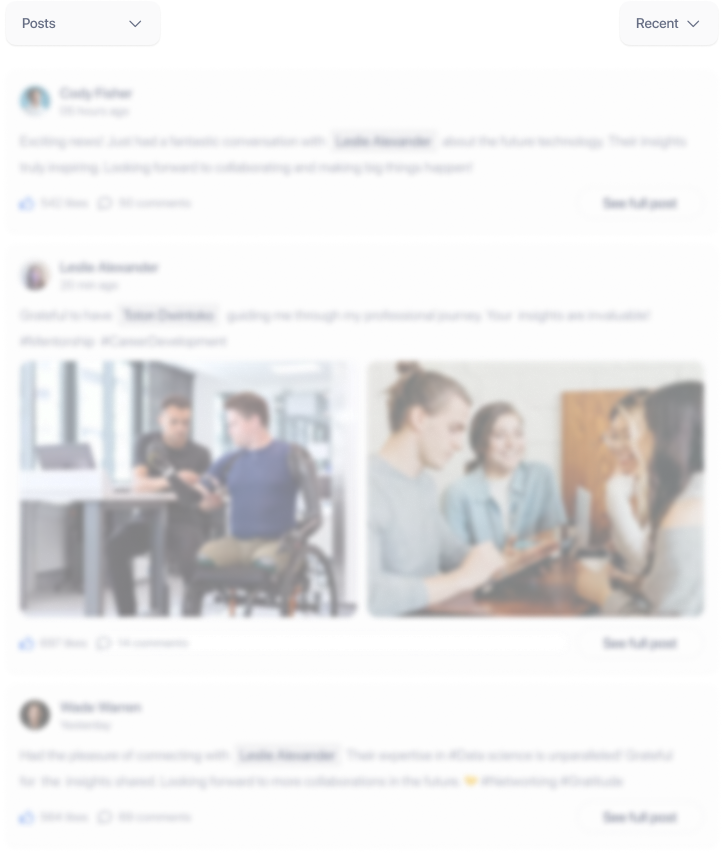