Moana Baker
at United Steel- Claim this Profile
Click to upgrade to our gold package
for the full feature experience.
Topline Score
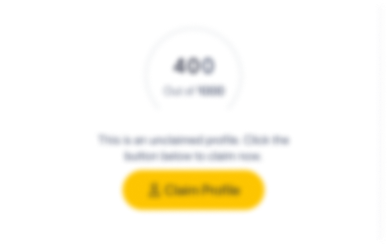
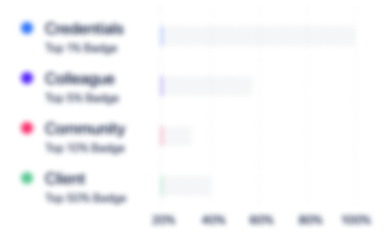
Bio


Experience
-
United Steel
-
United States
-
Construction
-
1 - 100 Employee
-
-
Dec 2022 - Present
-
-
-
Jun 2021 - Dec 2022
-
-
-
PlaceMakers
-
New Zealand
-
Wholesale Building Materials
-
700 & Above Employee
-
-
Feb 2020 - Jun 2021
-
-
-
Aug 2016 - Feb 2020
-
-
-
-
HR Assistant/Data Management temp for Carter Holt Harvey
-
Jun 2015 - Mar 2016
-
-
-
Hynds Limited
-
East Tamaki
-
Inventory Administrator
-
Mar 2013 - Apr 2015
Responsibilities: Implementation of planning policy project Data integrity Master Data management Demand planning review of min max levels Reduce SLOB stock inventory levels Reduce Excess stock inventory levels Part of the ERP project team / process Responsibilities: Implementation of planning policy project Data integrity Master Data management Demand planning review of min max levels Reduce SLOB stock inventory levels Reduce Excess stock inventory levels Part of the ERP project team / process
-
-
-
Danone
-
France
-
Food and Beverage Manufacturing
-
700 & Above Employee
-
Contract Administrator
-
Jan 2012 - Mar 2012
Responsibilities: Trained new SAP warehouse scripts Inwards goods receipt Bin to bin transfers Plant to Plant transfers Dispatch of raw materials to production Dispatch of finished goods to offsite storage RF Scanning QA sampling releases Wastage Scheduling bin transfers for next production run Stock take vs production schedule Responsibilities: Trained new SAP warehouse scripts Inwards goods receipt Bin to bin transfers Plant to Plant transfers Dispatch of raw materials to production Dispatch of finished goods to offsite storage RF Scanning QA sampling releases Wastage Scheduling bin transfers for next production run Stock take vs production schedule
-
-
-
Corporate Express New Zealand
-
Auckland, Business Parade, Highbrook
-
Inventory Planning Analyst
-
Jun 2009 - Jan 2012
Managing Problem Inventory re: Slow moving & Excess Stock. Analysis sales and demand for ongoing maintenance of optimal range and monitor warehouse selection. Managing Proprietary Stock process Managing Problem Inventory re: Slow moving & Excess Stock. Analysis sales and demand for ongoing maintenance of optimal range and monitor warehouse selection. Managing Proprietary Stock process
-
-
-
Staples Australia/New Zealand
-
Australia
-
Business Supplies & Equipment
-
700 & Above Employee
-
-
Jan 2010 - Apr 2011
Part of the implementation of SAUnderstand SAP implementation of Materials Master code creationCreate Purchasing Views in SAPDevelop various KPI (Key Performance Indicators) reportsMaintain buying model - Forecast vs. Non forecastReview data integrityResults & Achievements:Created over 10K purchasing views from Jun 10 to Dec 10Reviewed and maintained over 20K of warehouse combination materialsAble to produce the following reports in SAP / BW Reporting: ME2N Overdue purchase orders BW reporting - Consumption history ZQPURAUDIT Raw data ZPRICE Supplier contracts ZVA05 Open sales orders ME5A Overdue purchase requirements BW reporting - Total inventory stock holdings BW reporting - Back order detail report FBL1N & ZMRBR - Invoice variance reports by qty & priceHave a good understanding of the materials master, Sales & Purchasing viewsHave a good understanding of Purchasing functionsKnowledge in creating Info records & Supplier contract Show less
-
-
-
Mar 2008 - Jan 2010
Reducing Slow Moving & Excess Stock levelsProvide senior sales managers with KPI (Key Performance Indicators) reportsMonthly Problem Inventory ReportingManaging Proprietary StockArrange Promotion Sales with the Marketing team Results & Achievements:Rules applied to inventory groups to identify slow moving items and flag for deletionProvided monthly reports to the National Sales Managers Developed a good relationship with suppliers to return excess & slow moving stockReduced Problem Inventory down from 5.06% June 08 to 3.79% June 09 and achieved as of Jan 10 - 3%Improved the code creation process - Created a generic electronic form Revised rules around Proprietary Stock procedure & reviewed proprietary stock register clean upExcess stock reduced by $300K (1 year period)Managed staff sales of slow moving stock. A total of $3K+ credited back into stock provisionWorked closely with marketing for promotional campaign offers of slow moving product Show less
-
-
-
Coca-Cola Europacific Partners
-
United Kingdom
-
Manufacturing
-
700 & Above Employee
-
Inventory Controller
-
Apr 2003 - Jun 2008
Reconciling discrepancies after each production IRA results to reach 100% Daily cycle counting - variance hits under 5% Receipting of packing lists Responsible for offsite storage of raw packaging Dispatching of raw materials to third party for production Production planning cover for production schedulers Invoicing reconciliation for overdue payments Cover for the Concentrates beverage base area Responsible for inwards goods hoist drivers Results & Achievements: Reached 99.9% accuracy in IRA (Inventory Record Accuracy) results from 40% Managed inwards goods staff for availability - both day shift & night shift. Improved structure of Daily Cycle Counting Supported in production scheduling Developed a good relationship with third party suppliers, managing & maintaining inventory accuracy of raw materials. Peer support to inwards goods staff Reason for leaving: Unfortunately there was no room for movement, and had lost the motivation in my current role. Needed to widen and gain more experience in Inventory Management. Show less
-
-
-
-
Purchasing/Planner
-
Jan 1994 - Jan 2002
Process MRP (Material Requirements Planning) reports to plan and raise purchase orders Process DRP (Distribution Requirements Planning) reports to replenish and top up warehousing minimums / safety stock levels Order to forecasts and sales by budget Maintaining data integrity Results & Achievements: Good understanding of BPCS (Business Planning and Control System) AS400 hardware - ERP (Environmental Resource Planning) system Understanding of MRP (Material Requirements Planning) reports for demand planning Understanding of DRP (Distribution Requirements Planning) reports to replenish ROP / ROQ (Reorder Point / Reorder Qty) within the SSL (Safety Stock Levels) Purchased daily orders to forecast and keep within the minimum order volume to achieve KPI results Maintaining data integrity as part of code maintenance, reviewing safety stock levels and minimum quantities DIFOT & DIFOTIS Provided competitive quotes to sales to win contracts. Maintain a close relationship with the suppliers locally & internationally Show less
-
-
-
-
-
Jan 1997 - Jan 2000
Processed shipping documents and distributed to customs freight forwarders, inwards goods, inter-branch destinations and accounts department.
-
-
-
Jan 1994 - Jan 1997
Recorded and filed original copies. On request a copy of the test certificate was delivered with the product to the customer. Reason for leaving:
-
-
Education
-
Manukau Instititute of Technology (Auckland)
NZIM Diploma Certificate in Business Management -
2011 - Manukau Institute of Technology (Auckland)
NZIM Diploma Certificate in Business Management -
2010 - Manukau Institute of Technology (Auckland)
NZIM Diploma Certificate in Business Management -
Tamaki College
-
Tamaki College
Community
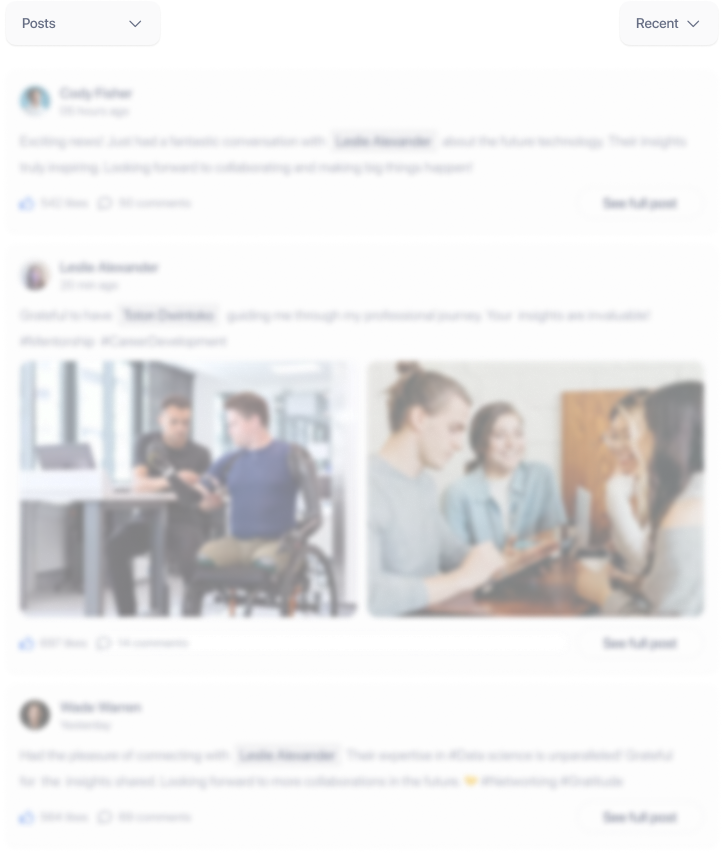