Mitesh Patel PEng,CQE
Engineer-Process at Integran Technologies Inc.- Claim this Profile
Click to upgrade to our gold package
for the full feature experience.
-
Hindi, Gujarati -
Topline Score
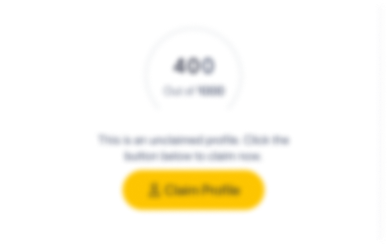
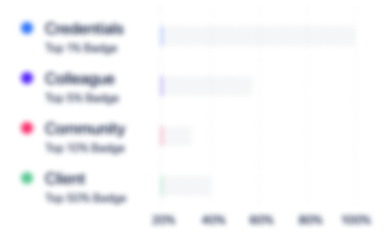
Bio

Khairul Islam
I had the pleasure of working with Mitesh for couple of years at Hastech Manufacturing. I found his ability to handle any situation calmly and patiently even with in toughest time. His work ethicks are pristine, he is detail oriented and very much of a team player. He played a key role for launching 6 speed transmission for Ford while he was at Hastech Manufacturing by using his mettalurgical and process control talents. He is one of the most dedicated professionals I have worked with. Mitesh will be a valuable asset to any company.

Chahat Kansal Awasthi
I have closely worked with Mitesh at Integran Technologies for over a period of 2 years. He is a very hard-working and driven individual with advanced knowledge and hands-on experience in metallurgical principles. He has successfully worked as a part of a bigger team, executed projects with tight deadlines and has always been available to support the task at hand. His strong work-ethic and skill-set will an asset to any organization.

Khairul Islam
I had the pleasure of working with Mitesh for couple of years at Hastech Manufacturing. I found his ability to handle any situation calmly and patiently even with in toughest time. His work ethicks are pristine, he is detail oriented and very much of a team player. He played a key role for launching 6 speed transmission for Ford while he was at Hastech Manufacturing by using his mettalurgical and process control talents. He is one of the most dedicated professionals I have worked with. Mitesh will be a valuable asset to any company.

Chahat Kansal Awasthi
I have closely worked with Mitesh at Integran Technologies for over a period of 2 years. He is a very hard-working and driven individual with advanced knowledge and hands-on experience in metallurgical principles. He has successfully worked as a part of a bigger team, executed projects with tight deadlines and has always been available to support the task at hand. His strong work-ethic and skill-set will an asset to any organization.

Khairul Islam
I had the pleasure of working with Mitesh for couple of years at Hastech Manufacturing. I found his ability to handle any situation calmly and patiently even with in toughest time. His work ethicks are pristine, he is detail oriented and very much of a team player. He played a key role for launching 6 speed transmission for Ford while he was at Hastech Manufacturing by using his mettalurgical and process control talents. He is one of the most dedicated professionals I have worked with. Mitesh will be a valuable asset to any company.

Chahat Kansal Awasthi
I have closely worked with Mitesh at Integran Technologies for over a period of 2 years. He is a very hard-working and driven individual with advanced knowledge and hands-on experience in metallurgical principles. He has successfully worked as a part of a bigger team, executed projects with tight deadlines and has always been available to support the task at hand. His strong work-ethic and skill-set will an asset to any organization.

Khairul Islam
I had the pleasure of working with Mitesh for couple of years at Hastech Manufacturing. I found his ability to handle any situation calmly and patiently even with in toughest time. His work ethicks are pristine, he is detail oriented and very much of a team player. He played a key role for launching 6 speed transmission for Ford while he was at Hastech Manufacturing by using his mettalurgical and process control talents. He is one of the most dedicated professionals I have worked with. Mitesh will be a valuable asset to any company.

Chahat Kansal Awasthi
I have closely worked with Mitesh at Integran Technologies for over a period of 2 years. He is a very hard-working and driven individual with advanced knowledge and hands-on experience in metallurgical principles. He has successfully worked as a part of a bigger team, executed projects with tight deadlines and has always been available to support the task at hand. His strong work-ethic and skill-set will an asset to any organization.

Experience
-
Integran Technologies Inc.
-
Canada
-
Nanotechnology Research
-
1 - 100 Employee
-
Engineer-Process
-
Mar 2008 - Present
Responsible for process control of various electroplating process ( Nickel, Nickel-Iron, Copper, Nickel-Cobalt electro plating process) and plating of plastic process Performs Laboratory scale trials to develop product/processes Instrumental in developing plating on plastic process from laboratory scale to production scale Responsible for material and chemical testing and analysis activities of the plant Involved in development of revolutionary nanometal/polymer hybrid product Developed and maintained control plans, FMEA, work instructions, flowcharts, quality control/inspection plans, engineering changes as per AS 9100 guidelines Assist in planning, execution and interpretation of designed experiments to identify and characterize critical factors affecting manufacturing process Initiate and participate in continual improvement projects and waste reduction initiative Conducted root causes analysis for non confirming products. Recommended preventive and corrective actions to resolve product quality issues/problems Liaison with suppliers regarding incoming raw material quality issues and provided feedback Support the development of new product/process specifications and procedures and manufacturing of prototype parts Involved in process optimization, scale-up and process validation efforts .Validated new products according to control plan Conducted Process capability study for the newly developed process (Cp and Cpk ) Work and communicate with engineering on product performance, functionality issues and procedure updates Provide technical support to troubleshoot chemical and metallurgical issues on shop floor Achieved operational targets with optimum operating cost, excellent recoveries and efficiencies Perform regular product/process verification audits to assess quality process effectiveness Solved quality problems using 5 why, 8D Analysis, Fishbone and Pareto analysis Assist the project team with customer needs and technical support Show less
-
-
-
-
Metallurgist/Quality Specialist
-
Mar 2005 - Mar 2008
Supervised various heat-treatment processes and monitored all quality control functions to ensure Product integrity and contractual compliance with vendors and suppliers Managed for all the activities of Metallurgical laboratory to support plant operations Optimized Induction hardening process for 6R-80 Transmission shaft of Ford motor company Provide technical support to customers as well as other internal departments to resolve heat –treat related quality issues Investigate causes of non-confirming products and wrote reports regarding findings, conclusions and made recommendations Developed Process control and quality control documents as per TS 16949 guidelines Actively involved in Lean manufacturing activities for product and process improvement as well as waste reduction initiatives Verify product quality through audit and support the manufacturing operation set up and First Off Analyzed induction and temper products for metallurgical quality characteristics like hardness, case depth and microstructure Adjust Induction hardening machines by modifying program to meet hardness and case depth specifications of the final product Conduct Hardness(Rockwell) testing, Micro-hardness testing, Magnetic particle inspection Participated in failure analysis and corrective action investigations Calibrate measuring instruments & maintain calibration records as per requirement. Maintains document control including quality checklists, inspection checklists, SPC data and quality reports and associated quality documentation as per quality systems guidelines Responsible for process control of Induction hardening and tempering operations Prepare daily and monthly quality test reports v Show less
-
-
-
-
Process Improvement Engineer
-
Aug 1997 - Sep 2002
Responsible for process control and quality control of all the operations involved in refining of copper such as electrolysis, leaching, purification and filtration Monitored and analyzed various process parameters of copper refinery to find out deviations from standards and made recommendations as a part of process improvement activities Gained hands on experience in operations like leaching, filtration, purification, electro refining and also every aspect of plant operations Responsible for production planning & achieving targets with optimum operating costs and excellent recoveries Maintained Copper cathode quality as LME grade-A by maintaining impurity level in anode (especially As, Bi, Sb) and in electrolyte below desire limit Continuous efforts have been made to achieve consistent current efficiency > 95% by adopting some regular practices Improved quality of Electro- win copper in electrolyte purification area by additional practices Monitored plant operations and liaised between plant & laboratory. Maintained plant and machinery in excellent condition, with timely updating the technology Budgeted & procured raw material, stores consumables and ensured inventory controls Audited hazardous waste management facilities & waste accumulation areas for compliance with Pollution Control Boards regulations and government policies Conducted test runs/trials in liaising with plant operations personnel for improvement /optimization of process Generated daily and monthly quality assurance and production reports Show less
-
-
Education
-
ASQ
-
The Maharaja Sayajirao University of Baroda
Bachelor of Engineering (B.E.), Metallurgical Engineering -
The Maharaja Sayajirao University of Baroda
Bachelor of Engineering ( Metallurgical)
Community
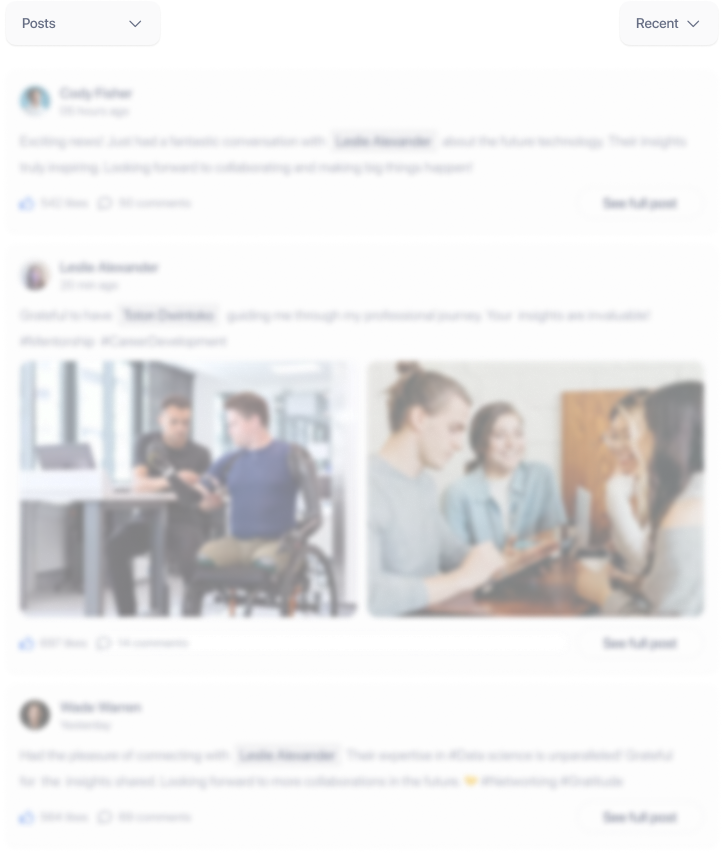