Mitchell Sandre
Project Manager - Loop Refurbishment at Wisely Group- Claim this Profile
Click to upgrade to our gold package
for the full feature experience.
Topline Score
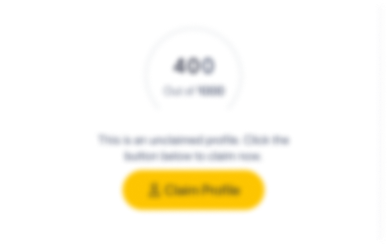
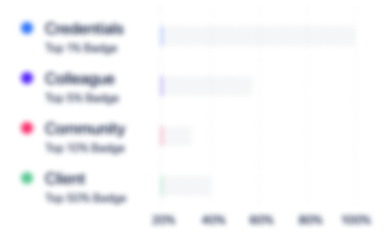
Bio


Credentials
-
▶ Certificate II in Business
. -
▶ Coal Board Medical 43/QLD Coal Board Medical
. -
▶ Fire & First Aid Training
. -
▶ New Century Resources, Mt Pleasant, Glencore & BMA Inductions
. -
▶ S123 & G2 (Apt Sup - GRM, SRM, BWM, CVM, MIM, NCR)
. -
▶ Standard 11 & BMA Core Coal Mining Inductions
. -
▶ WP (Elevating Work Platform), LF (Forklift) & Overhead/Gantry Crane
. -
▶ Working at Heights, Confined Space Entry & Gas Test Atmospheres
.
Experience
-
Wisely Group
-
Australia
-
Mining
-
1 - 100 Employee
-
Project Manager - Loop Refurbishment
-
Jan 2022 - Present
Wisely specialise in asset management for the resources, mining, industrial, ports, civil and transport sectors. Goonyella Riverside is Australia’s third-largest open-pit coal mine, and the Loop Refurbishment Project entails full replacement of 2 loops in the coal wash plant, each with 2 deslime screens, 2 float screens, 1 sink screen, pipework, cyclone, sump repair, structural assessments and repairs. Employed by Wisely but placed in the BMA Owner Team as Project Manager, core role deliverables include (but are not limited to):► Direct management of 2 planners, 1 scheduler, 1 cost controller and 2 execution coordinators, ensuring clarity of team and individual expectations, providing technical and procedural guidance, facilitating team meetings and training needs, making confident decisions, and modelling positive workplace behaviours through my daily actions and reactions► Tendering, estimating, budgeting, planning, scheduling, procurement, cost control, resourcing and forecasting, as well as contract management, writing technical specifications, answering TQ’s, and creating and implementing workflows► Project execution management, overseeing Management of Change (MoC) processes, managing QA/QC systems and documentation for compliance purposes, and ensuring overall good project governance► Changed project execution processes, which removed delays and resulted in both project being delivered ahead of schedule (2.5 days and 4.5 days), and completed both projects on-budget and with Zero incidents► Facilitating cross-functional relationships to ensure an integrated approach, enhanced workplace collaboration, and knowledge sharing (same for all leadership roles below)► Ensuring compliance for all vendors and equipment coming onto site, and building roster and training requirements.
-
-
Major Projects Works Coordinator (Owner Team)
-
Apr 2021 - Jan 2022
Placed in the Owner Team, role deliverables were similar to those in the Outage Works Coordinator below, with the addition of:► Scoping work and writing scope documents, as well as stepping out the schedule to ensure minimal interactions between works and other departments, and using SAP to plan the works, order parts, and engage vendors ► Engaging vendors to complete the works, and coordinating vendor supervisors (with up to 150 CMW’s under them)► Prioritising critical scope and tracking completions.
-
-
-
UGL
-
Australia
-
Engineering Services
-
700 & Above Employee
-
Outage Works Coordinator
-
Dec 2020 - Mar 2021
UGL provides engineering, asset management and maintenance services to the mining, refining, oil and gas, power generation, civil infrastructure, defence, transport and technology sectors. Employed by UGL but embedded into the BMA Owner Team as Outage Works Coordinator for BMA coal mining and processing sites, most specifically for Train Load Out (TLO) facilities, coal wash plant, stackers, surge bins and ROM’s, core role deliverables included (but were not limited to):► Planning scope of works for outages in-line with budgets and resourcing/personnel plans, as well as utilising SAP for works planning, coordinating Area Leaders to ensure minimise work group interactions and clear understanding of outage works, coordinating the actual works within the outages, and ensuring the full scope of works are completed ► Scheduling works within plant availability downtimes in correspondence with operational demand and supply, and adapting to break-in and emergent works within such plant downtimes► Ordering correct parts for the outages, and engaging vendors and on-hire companies to supply labour, cranes, lighting plants, crib hut facilities and EWP’s► Creating work packs, ITP’s, PRT’s, completion and close-out documents, and controlling management systems audits.
-
-
Mechanical Supervisor - Shutdowns
-
Jun 2020 - Dec 2020
Employed as a Mechanical Supervisor, most specifically for TLO's, coal wash plant, stackers, surge bins and ROM’s, associated core role deliverables included (but were not limited to):► Coordination & supervision of 15 to 22 workers including Fitters, Boilermakers, Riggers, Crane Operators, Electricians, Painters, Blasters, T/A’s & Peggys for the installation, removal, re-installation, testing, inspection, commissioning, preventative maintenance, breakdown maintenance, overhaul &/or refurbishment of the following plant & equipment:► Crushers, conveyors, vessels, tanks, stackers, reclaimers, chutes, apron feeders, thickeners, malco feeders, sytron feeders & slingers, & associated process piping, pumps, valves, steel structures, hydraulic & pneumatic rams, cylinders, engines, seals, spacers, gearboxes, bearings, spools & blinds► Delegating duties & monitoring workflows, measuring performance, appropriately confronting any under-performance, providing technical & procedural guidance & training, facilitating pre-starts, managing timesheets & mobilisations, & ensuring the overall delivery of high-quality workmanship (same for all supervisor & team leader roles below)► Working collaboratively with management, peers, team members & client representatives, & facilitating cross-functional relationships to ensure an integrated approach & enhanced workplace collaboration & knowledge sharing (same for all supervisor & team leader roles below)► Reading & interpreting P&ID’s, isometrics, specifications, plans, schedules, ASME & API Standards to ensure site tasks are completed on-time, to required QA/QC Standards, & with correct materials (same for all roles below)► Design, verification, approval & installation of safe isolations, as well as de-isolations for effective returns to service, & ensuring overall compliance with site PTW & LOTO systems ► Flange management for joint integrity, hi-torqueing & tensioning, precision laser alignments, & tightness testing.
-
-
-
Glencore
-
Switzerland
-
Mining
-
700 & Above Employee
-
Mechanical Supervisor - Shutdowns
-
Feb 2020 - Jun 2020
Employed as a Mechanical Fitter for shutdowns on concentrators, smelters and filter plants, core role deliverables included (but were not limited to): ► Coordination and supervision of 12 to 15 workers for the installation, removal, re-installation, testing, inspection, commissioning, preventative maintenance, breakdown maintenance, overhaul and refurbishment of the following plant: ► Vessels, tanks, chutes, filters, strainers, burners, furnaces, gantry cranes, charge cart (little train), pan conveyors, mixers, crushers, bag house and dust systems and associated process piping, vacuumed pumps, valves, steel structures, cylinders, engines, seals, spacers, gearboxes, bearings, spools, spades and blinds ► Scoping jobs and planning associated works, ordering parts, ensuring on-time deliveries, preparing work packs and QA sheets, maintaining schedules, and using CMMS for work order tracking, task scheduling and maintenance recording ► Design, verification, approval and installation of safe isolations, as well as de-isolations for effective returns to service, and ensuring overall compliance with site PTW and LOTO systems for standard and high-risk works ► Flange management, hi-torqueing/tensioning, precision alignments, and hydrostatic/pneumatic leak and tightness testing ► Ensured the overall safe, on-time, on-budget and high-quality delivery of scoped work packages to required specifications ► Conducted safety audits and job hazard analysis, and provided on-the-job training for tool-setting and maintenance tasks ► Completed QA/QC documentation including FIC’s (Field Installation Checklists) and ITP's (Inspection and Test Plans).
-
-
-
Monadelphous
-
Australia
-
Construction
-
700 & Above Employee
-
Leading Hand Mechanical Fitter & Flange Technician
-
Jan 2020 - Feb 2020
Employed as a Leading Hand Mechanical Fitter, I worked in a multi-discipline trades team to deliver high-quality preventative and scheduled maintenance services. Associated core role deliverables included (but were not limited to): ► Inspection of pressurised equipment including boilers, pressure vessels and process piping, as well as tray change-outs, and extensive removals and installations of Pressure Safety Valves (PSV’s) and Pressure Relief Valves (PRV’s) ► Controlled flange management (including flange face and mating surface inspections) as per maintenance and pre-commissioning schedules ► Completing all required QA/QC documentation, and providing detailed project progress reports ► Writing plant locations and permits for high-risk work entries.
-
-
-
UGL
-
Australia
-
Engineering Services
-
700 & Above Employee
-
Leading Hand Mechanical Fitter - Construction & Commissioning
-
Apr 2019 - Dec 2019
The Mount Pleasant Operation is approved to produce up to 10.5 million tonnes of ROM thermal coal. Construction began in November 2016, with the scope including a new CHPP, rail loop, mine infrastructure area, water management system and supporting facilities. It was due for completion late 2018, however UGL took the contract over in 2019 (G&S was the original constructor) to complete an ailing project. Employed as a Leading Hand Mechanical Fitter, role deliverables included (but were not limited to): ► Removal, modification, re-installation and precision alignment of process piping, pumps, vibrators, shaker screens, motors and gearboxes, as well as modifying brackets to eliminate soft foot issues ► Flange management of bolted flange connections for joint integrity, and writing PTW.
-
-
-
New Century Resources
-
Australia
-
Mining
-
1 - 100 Employee
-
Mechanical Supervisor - Commissioning (Owner Team)
-
Jun 2018 - Apr 2019
Employed as a Mechanical Supervisor in the Owner’s team, role deliverables included (but were not limited to): ► Re-building Warman and Bredel pumps, as well as re-alignment of motors, pumps and gearboxes, marking out and installing brackets, flange management for joint integrity, pipe fitting, and associated re-commissioning works ► Scoping jobs and planning associated works, ordering parts, ensuring on-time deliveries, preparing work packs and QA sheets, maintaining schedules, and ensuring the overall safe and efficient continuity of works ► Conduct safety audits and wrote PTW.
-
-
-
Glencore
-
Switzerland
-
Mining
-
700 & Above Employee
-
Mechanical Fitter (through to) Leading Hand Mechanical Fitter
-
Jan 2017 - Jun 2018
Initially employed as Mechanical Fitter and promoted to Leading Hand Mechanical Fitter, with a focus on the coordination and hands-on delivery of high-quality preventative and reactive maintenance services at the George Fisher Underground Lead-Zinc Mine and associated concentrators, smelters and filter plants, other role deliverables included (but were not limited to): ► Preventative and breakdown maintenance works including the inspection, stripping, overhaul, refurbishment and re-installation of mechanical components on conveyors, pans, overhead cranes, vibrating feeders, drum filters and crushers ► Delegated work priorities, monitored workflows, provided technical and procedural training guidance ► Flange management, pipe fitting, and the diagnosis and rectification of mechanical breakdowns.
-
-
-
NUTEK ENG LTD
-
United Kingdom
-
Apprentice Mechanical Fitter & Turner & Foreman
-
Mar 2013 - Jan 2017
Nu-Tek specialises in the manufacturing of hydraulic fittings for the mining sector, as well as the fabrication, maintenance repair of old and new machinery for the agricultural and horticultural industries. They also manufacture and test prototypes, reverse engineer and design new solutions for existing processes and operations, and manufacture single, multiple and odd shaped components. Employed as an Apprentice Fitter and Turner, and appointed as Foreman for 3.5 of my apprenticeship, role deliverables included: ► Trained in the areas of quality manufacturing and engineering, as well as the fabrication and maintenance of hydraulic fittings, agricultural and horticultural machinery, Stick and Tig welding, zinc electroplating, CNC machining and oxy cutting ► General repairs and component change outs for mobile equipment including road trains, dewatering pumps, harvesters, haul outs, tractors, dozers and excavators ► Flange management, pipe fitting, grinding, buffing and the set-up, operation and maintenance of CNC cutting machines.
-
-
Education
-
✔ Certificate III in Engineering - Mechanical (Fitter & Turner)
Full Term Apprenticeship Mechanical Apprenticeship -
✔ Burdekin Catholic High School
Community
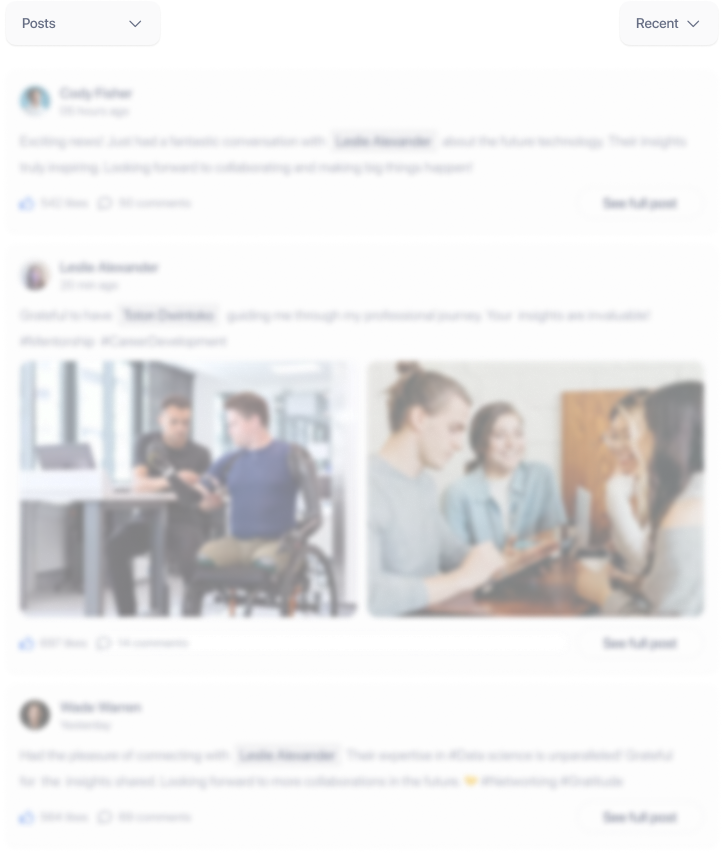