Mitchell Buchna
Interim Assembly Superintendent at IROCK Crushers, LLC- Claim this Profile
Click to upgrade to our gold package
for the full feature experience.
Topline Score
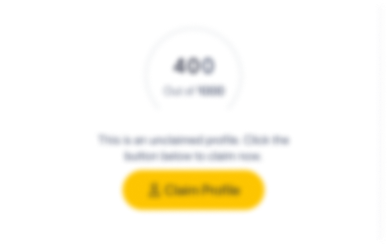
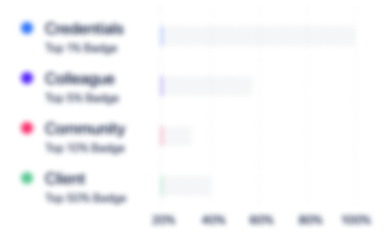
Bio


Experience
-
IROCK Crushers, LLC
-
United States
-
Industrial Machinery Manufacturing
-
1 - 100 Employee
-
Interim Assembly Superintendent
-
May 2023 - Present
-
-
Continuous Improvement Manager
-
Nov 2022 - Present
-
-
-
nVent
-
United States
-
Appliances, Electrical, and Electronics Manufacturing
-
700 & Above Employee
-
Manufacturing Supervisor
-
Nov 2021 - Nov 2022
-Improved CNC efficiencies from 70-115% through RCCM activities -Lead and managed over 40 direct reports across multiple MTO environments -Improved overall schedule attainment in various departments -Lead direct recruitment efforts for machining departments -Maintained departmental PNL -Assisted in onboarding and professional development of peer supervisors -Improved CNC efficiencies from 70-115% through RCCM activities -Lead and managed over 40 direct reports across multiple MTO environments -Improved overall schedule attainment in various departments -Lead direct recruitment efforts for machining departments -Maintained departmental PNL -Assisted in onboarding and professional development of peer supervisors
-
-
-
Swagelok
-
United States
-
Industrial Machinery Manufacturing
-
700 & Above Employee
-
Production Supervisor
-
Jun 2019 - Nov 2021
-Drive Lean Daily Management System Cadence to achieve operational excellence-Drive boundary team alignment between operations and all support functions-Demonstrate alignment of corporate mission, vision, values & strategies-Drive change through inspirational leadership-Coach & mentor associates to help them achieve their goals
-
-
Industrial Engineer
-
Aug 2018 - Jun 2019
-Completed product in-source assessment to save $200k annually & reduce LT up to 3 weeks-Identified & implemented improvement efforts to increase QC margins from 22-35%-Assessed, led & implemented Inbound supply chain improvement efforts to save $1M in DL costs-Completed torque supplier assessment & recommended VSG 5-year road map to improve asset health across the shop floor-Completed back end compression routing updates to improve lead time by 0.5 days
-
-
Assembly/Quality Engineer
-
May 2017 - Aug 2018
-Developed and designed assembly fixtures to improve productivity and efficiency-Solved internal and external corrective actions within 30 days-Implemented fan filters to two manual stake operations to operate class 10 cleanliness and reduce customer returns-Dispositioned day to day quality related issues
-
-
-
GE Transportation, a Wabtec company
-
United States
-
Truck Transportation
-
700 & Above Employee
-
Quality Engineering Co-op
-
May 2016 - May 2017
-Assessed and Implemented solutions for improving quality on various quantities of locomotive parts -Created & implemented inspection guides for Pakistan, Angola, India, and Rio Loco lines with 0% DPU -Conducted 6-Sigma project on loco oil shells and reduced scrap by $70K -Improved production time in finish area by 25% -Improved upon safety and ergonomics metrics in finish area by 25% -Created various standard work documents and manufacturing instructions -Assisted with the implementation of a lean 5S project on the Press Brake Station -Responsible for 3 non-conforming material areas -Conduct internal audits Show less
-
-
-
Penn State University
-
United States
-
Higher Education
-
700 & Above Employee
-
Resident Assistant
-
Aug 2014 - Aug 2016
-Served as a role model by providing guidance and direction to residents -Promoted and aid residents in their growth and development -Served as an academic connection, emergency response, individual help and referral liaison -Created a safe space for residents to learn and grow -Served as a role model by providing guidance and direction to residents -Promoted and aid residents in their growth and development -Served as an academic connection, emergency response, individual help and referral liaison -Created a safe space for residents to learn and grow
-
-
-
Mason Farms LLC
-
Lake City, Pennsylvania
-
Wholesale Sales and Distribution
-
Jun 2008 - Jul 2016
-Processed orders for a large range of customers including distributors and the general public -Handled customer billing and inventory needs worth $1MM -Communicated with satellite locations and outside companies on supply and produce orders -Delivered orders throughout Western Pennsylvania and Western New York -Trained new employees within the warehouse -Processed orders for a large range of customers including distributors and the general public -Handled customer billing and inventory needs worth $1MM -Communicated with satellite locations and outside companies on supply and produce orders -Delivered orders throughout Western Pennsylvania and Western New York -Trained new employees within the warehouse
-
-
-
Swagelok
-
United States
-
Industrial Machinery Manufacturing
-
700 & Above Employee
-
Engineering Intern
-
Mar 2015 - Aug 2015
-Developed routing targets for 5 auxiliary and assembly operations -Created 3 in-cell standard work documents -Implemented solutions for achieving 10% increase in production targets -Improved communication channels among employees -Developed routing targets for 5 auxiliary and assembly operations -Created 3 in-cell standard work documents -Implemented solutions for achieving 10% increase in production targets -Improved communication channels among employees
-
-
-
FMC Technologies
-
Oil and Gas
-
700 & Above Employee
-
Product Support Intern
-
May 2014 - May 2015
-Created transfer orders and purchase requisitions -Communicated between purchasing and production -Offered support to production managers -Ran various, daily inventory reports for direct sites -Conducted a cost analysis on a product line -Created transfer orders and purchase requisitions -Communicated between purchasing and production -Offered support to production managers -Ran various, daily inventory reports for direct sites -Conducted a cost analysis on a product line
-
-
Education
-
Penn State Erie, The Behrend College
Interdisciplinary Business w/ Engineering Studies, B.S, Project and Supply Chain Management, B.S
Community
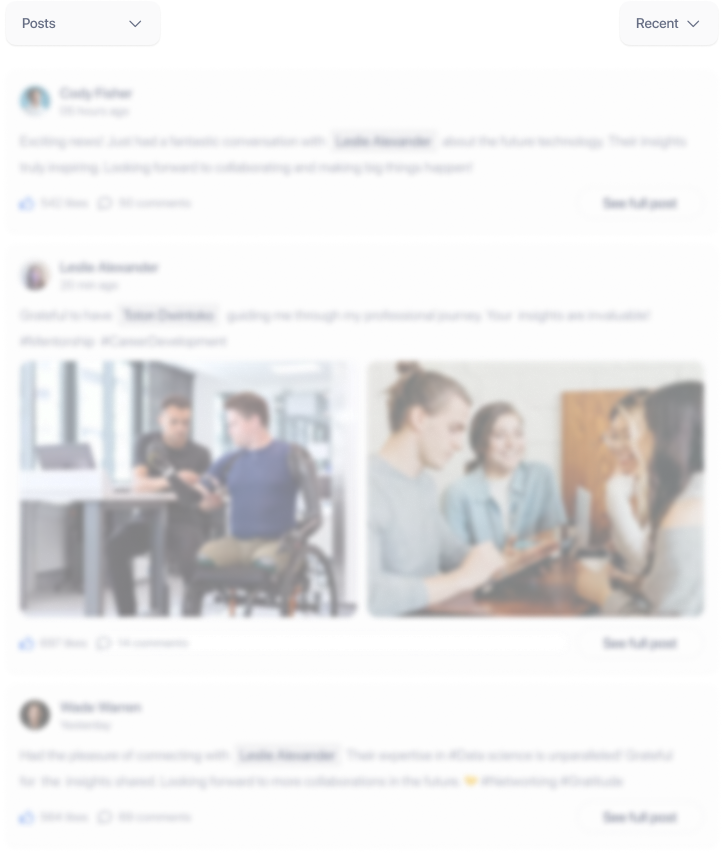