Miriam Chew
Quality System Engineer at Criotec, S.A. de C.V.- Claim this Profile
Click to upgrade to our gold package
for the full feature experience.
Topline Score
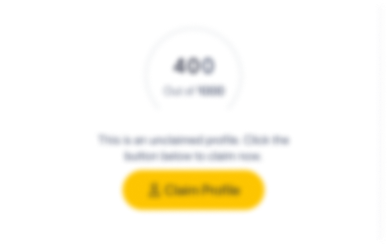
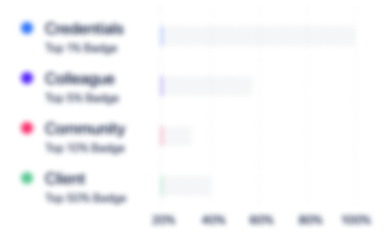
Bio

Mauricio V.
I had the chance to work with Miriam during a very challenging time in the company, without her input it surely would’ve been much difficult, she drives herself as a very responsible team worker, a keen attitude to solve problems and comply with the company’s expectation will make her a great partner, charismatic and energetic., I highly recommend Miriam, she will make a great fit for any position she applies for.

Rafael Salazar
Miriam is a very responsible person, also has a great attitude for new developments, team work and/or lead groups for problem solving, statistic tools and 5 S teams excelent partner and friend

Mauricio V.
I had the chance to work with Miriam during a very challenging time in the company, without her input it surely would’ve been much difficult, she drives herself as a very responsible team worker, a keen attitude to solve problems and comply with the company’s expectation will make her a great partner, charismatic and energetic., I highly recommend Miriam, she will make a great fit for any position she applies for.

Rafael Salazar
Miriam is a very responsible person, also has a great attitude for new developments, team work and/or lead groups for problem solving, statistic tools and 5 S teams excelent partner and friend

Mauricio V.
I had the chance to work with Miriam during a very challenging time in the company, without her input it surely would’ve been much difficult, she drives herself as a very responsible team worker, a keen attitude to solve problems and comply with the company’s expectation will make her a great partner, charismatic and energetic., I highly recommend Miriam, she will make a great fit for any position she applies for.

Rafael Salazar
Miriam is a very responsible person, also has a great attitude for new developments, team work and/or lead groups for problem solving, statistic tools and 5 S teams excelent partner and friend

Mauricio V.
I had the chance to work with Miriam during a very challenging time in the company, without her input it surely would’ve been much difficult, she drives herself as a very responsible team worker, a keen attitude to solve problems and comply with the company’s expectation will make her a great partner, charismatic and energetic., I highly recommend Miriam, she will make a great fit for any position she applies for.

Rafael Salazar
Miriam is a very responsible person, also has a great attitude for new developments, team work and/or lead groups for problem solving, statistic tools and 5 S teams excelent partner and friend

Experience
-
Criotec, S.A. de C.V.
-
Manufacturing
-
1 - 100 Employee
-
Quality System Engineer
-
Sep 2016 - Present
-
-
-
Nemak
-
García, Nuevo León.
-
Quality System Engineer
-
May 2016 - Aug 2016
- Lead Auditor for QMS based on ISO/TS16949:2009. - Nemak Quality System (NQS) management, including internal audits plan to ensure procedures are being followed. - Specific customer requirements accomplishments supported by NQS and Internal Audits. - Support and preparation for external Audits performed by customers from the automotive industry and ABS (Quality Evaluation). - Skilled facilitator in QRQC (Quick Response Quality Control) problem solving global methodology including solutions and lessons learnt (read across), resulting from QRQC management for Nemak Business Units. Show less
-
-
-
Criotec, S.A. de C.V.
-
Manufacturing
-
1 - 100 Employee
-
Quality Systems Engineer
-
Apr 2013 - May 2016
- Lead Auditor for the Quality Management System based on ISO 9001:2018 & 2015 – Lead the cycle audits assuring the ISO 9001 Standard Requirements are being met. - Update and Maintain the Quality Management System- Document control, process audits, and System improvements, QMS induction, Problem Solving tools Training (Ishikawa, C&E Matrix, 5 Why, 8D), Report System KPIs - Maintain the Laboratory Management System (ISO17025:2005)- Coordinate process audits, Document control and Lead External audits. - Corrective Action Follow up- (8D based process). - Coordinate 3rd party audits such as Customer and Certifying agencies. - Perform Supplier Audits on their Quality Management System. - Manage the MRB and Material Reject/Disposition Process. - Lead/Perform System Monitor Audits: Measurement Equipment audits, Operator Certification, 5S & Customer Requirements. - Customer Audits (Coca-Cola, PEPSI & Sigma). - Implement ISO13485:2016 STD, Lead Auditor. Show less
-
-
-
Kaydon Corporation
-
United States
-
Machinery Manufacturing
-
100 - 200 Employee
-
Quality Engineer.
-
2010 - 2013
- Process and finished goods Quality Assurancem, (3 quality inspectors). - Internal ISO auditor (9001:2008&14001:2004), member of the Environment Health & Safety Committee and Safety methodologies coordinator. - Quality metrics (Process PPM, Scrap, FPY, Reprocess/Rework) and statistics analysis of the production line. - Corrective actions definition and follow up. - Customer complaints and follow up (Root Cause Analysis). - Supplier claims and return of non conforming material. - Responsible for new product process implementations. - Continuous Improvement Projects Leader based on PDCA. - Purchase of quality measurement equipment (digital/analogue calipers, process gage, dial indicators, micrometers, thickness gage(Elcometer), surface finish, paint thickness, etc) . Show less
-
-
-
Wolverine Tube, Inc.
-
United States
-
Mining
-
100 - 200 Employee
-
ISO Coordinator & Quality Engineer
-
Jun 2008 - May 2009
- Quality system management (document control, corrective action process, system metrics, lead auditor), in order to comply with ISO 9001 and other certifications entities (AD2000). - Coordination of all required audits in the plant (internal audits, external audits, procedures, processes, customer audits). - Quality Management System Improvement (Corrective and Preventive Actions, Continuous Improvement process definition, Management Review). - Quality system management (document control, corrective action process, system metrics, lead auditor), in order to comply with ISO 9001 and other certifications entities (AD2000). - Coordination of all required audits in the plant (internal audits, external audits, procedures, processes, customer audits). - Quality Management System Improvement (Corrective and Preventive Actions, Continuous Improvement process definition, Management Review).
-
-
Education
-
Universidad Autónoma de Nuevo León
Licentiate degree, Industrial Engineering and Management specialty -
Universidad Tecmilenio
Master of Business Administration (MBA), Calidad y Productividad
Community
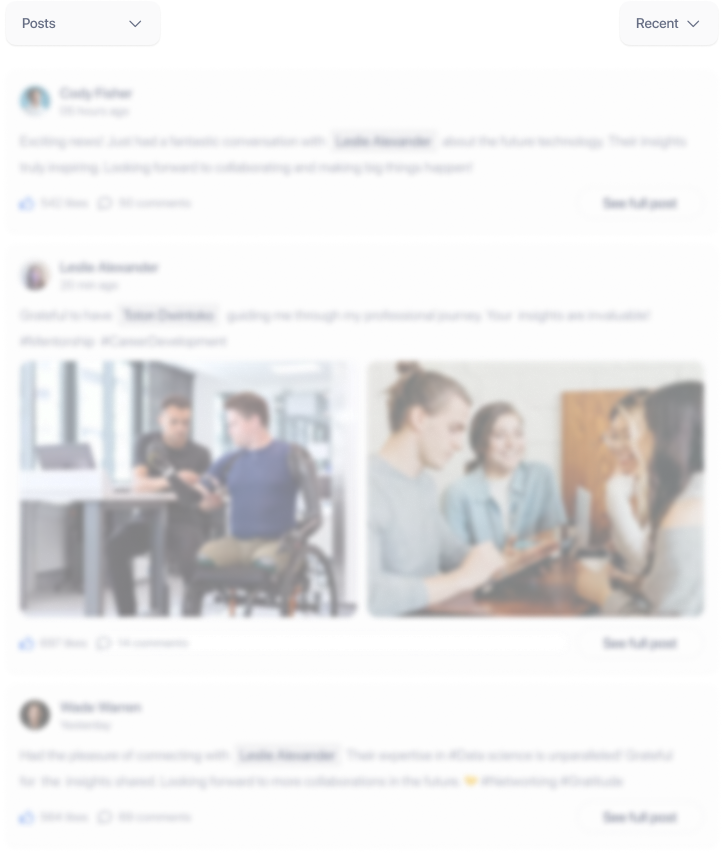