
Mircea Tapalaga
Supply Chain Country Manager ( Production Control, Logistics and Demand Planning management ) at Yazaki Romania- Claim this Profile
Click to upgrade to our gold package
for the full feature experience.
Topline Score
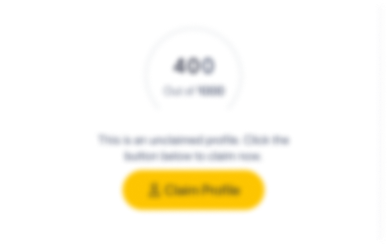
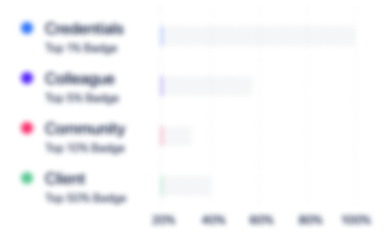
Bio

Mihaela Horecica
I worked with Mircea at my firts job in Honeywell and my first job in a multinational environment, for 8 months. I found in him a friendly and enjoyable person, always willing to take the time to support and explain no matter how fast the pace was. The customs activity required fast decision taking with little or no information, fast reactivity but also proactive when the situation would permit, and Mircea was doing a very good job in solving any issues fast and in a correct manner. His career evolution inside Honeywell (considerring the ever increasing responsibilities and complexity) and after leaving Honeywell only confirmed his qualities as a leader and manager. I would definetely recommend Mircea for any path he may choose, having in mind his ability to proper evaluate his strengths and weaknesses. I wish Mircea all the good luck and to never miss the best opportunities! Mihaela Horecica

Andreia Dimitriu
Mircea is an extrovert person, very dedicated to his work. He just loves to solve difficult problems. Always helpful and supporting, he was a key person in our team.

Mihaela Horecica
I worked with Mircea at my firts job in Honeywell and my first job in a multinational environment, for 8 months. I found in him a friendly and enjoyable person, always willing to take the time to support and explain no matter how fast the pace was. The customs activity required fast decision taking with little or no information, fast reactivity but also proactive when the situation would permit, and Mircea was doing a very good job in solving any issues fast and in a correct manner. His career evolution inside Honeywell (considerring the ever increasing responsibilities and complexity) and after leaving Honeywell only confirmed his qualities as a leader and manager. I would definetely recommend Mircea for any path he may choose, having in mind his ability to proper evaluate his strengths and weaknesses. I wish Mircea all the good luck and to never miss the best opportunities! Mihaela Horecica

Andreia Dimitriu
Mircea is an extrovert person, very dedicated to his work. He just loves to solve difficult problems. Always helpful and supporting, he was a key person in our team.

Mihaela Horecica
I worked with Mircea at my firts job in Honeywell and my first job in a multinational environment, for 8 months. I found in him a friendly and enjoyable person, always willing to take the time to support and explain no matter how fast the pace was. The customs activity required fast decision taking with little or no information, fast reactivity but also proactive when the situation would permit, and Mircea was doing a very good job in solving any issues fast and in a correct manner. His career evolution inside Honeywell (considerring the ever increasing responsibilities and complexity) and after leaving Honeywell only confirmed his qualities as a leader and manager. I would definetely recommend Mircea for any path he may choose, having in mind his ability to proper evaluate his strengths and weaknesses. I wish Mircea all the good luck and to never miss the best opportunities! Mihaela Horecica

Andreia Dimitriu
Mircea is an extrovert person, very dedicated to his work. He just loves to solve difficult problems. Always helpful and supporting, he was a key person in our team.

Mihaela Horecica
I worked with Mircea at my firts job in Honeywell and my first job in a multinational environment, for 8 months. I found in him a friendly and enjoyable person, always willing to take the time to support and explain no matter how fast the pace was. The customs activity required fast decision taking with little or no information, fast reactivity but also proactive when the situation would permit, and Mircea was doing a very good job in solving any issues fast and in a correct manner. His career evolution inside Honeywell (considerring the ever increasing responsibilities and complexity) and after leaving Honeywell only confirmed his qualities as a leader and manager. I would definetely recommend Mircea for any path he may choose, having in mind his ability to proper evaluate his strengths and weaknesses. I wish Mircea all the good luck and to never miss the best opportunities! Mihaela Horecica

Andreia Dimitriu
Mircea is an extrovert person, very dedicated to his work. He just loves to solve difficult problems. Always helpful and supporting, he was a key person in our team.

Experience
-
Yazaki Romania
-
Romania
-
Motor Vehicle Manufacturing
-
200 - 300 Employee
-
Supply Chain Country Manager ( Production Control, Logistics and Demand Planning management )
-
Feb 2019 - Present
-
-
Supply Chain Manager
-
Apr 2015 - Feb 2019
To design, implement, and supervise organizational strategies via coordinating and monitoring the purchasing, storage, transportation, material handling, and planning activities based on Lean Manufacturing Principles, in order to achieve the established objectives of the company To determine the Logistics department targets according to the company’s overall targets and monitor the action plansEnsuring middle and long term planning in order to establish the needed production capacity and its maintenance in case of needBased on various inputs from the customer as well as from other departments within the company like Manufacturing Engineering (standard work times) and Production (efficiency and productivity figures), preparation of the Plant Load Strategy.Creation, coordination, and implementation of the policies and procedures to improve the purchasing storage, transport, material handling as well as production planning and controlTo monitor cost reduction action plans related to LogisticsCoordination of the supply chain activities from production planning till FG delivery to the customerTo ensure the availability of the material for production, responsible for the procurement of all raw material and supplier contactsManagement of in-bound and out-bound material flowManagement of warehouse, material storage and handling, inventory control, and stock in transitEnsuring the optimal level of FG’s inventory in close cooperation with CSC Logistics, and any potential WH providerLogistics budget preparation and monitoringPreparation of statistical information on in-plant Logistics status at monthly meetings or any other meeting, if requestedMonitoring the quality, cost and efficiency of the supply chain and Logistics functionsSupport to the BU for coordination and monitoring of overall Production Planning and Control activity in order to cover the customer’s orders fully and on time.To establish and continuously improve the logistics flow
-
-
Supply Chain Deputy Manager
-
Feb 2013 - Apr 2015
•responsibility to design, implement and supervise organizational strategies through coordinating and controlling the purchasing, storage, transportation, planning activities in order to achieve the company’s established objectives.•Ensuring middle and long term planning – establishes the needed production capacity and pursues its adjustment when necessary •Based on various inputs, preparing the plant load strategy•Establishing, developing, managing and leading the Supply Chain & Logistics Department along with the Supply Chain Manager•Developing, implementing and coordinating policies and procedures in order to improve the activities of purchasing, storage, transport, planning and control of production•Responsibility for coordinating the supply chain activities from planning production till delivering the product to the client•Offering support for the Business Units in coordinating and checking the Planning activity and Production control in order to cover the customers’ orders and the production capacity; also support in ensuring the deliveries in time and according with the customers’ needs •Monitoring the quality, cost and efficiency of supply chain and logistics•Responsibility for all raw materials issues and keeping the contact with the suppliers •Control and management of in-bound and out-bound material flow•Responsibility for warehousing, materials storage, inventory control and stock in transit•Supporting an optimized level of finished goods inventory in balance with CSC logistics and warehouse provider•Preparation of statistical information on in-plant logistical status at monthly meetings •Management and control of shipping schedules, transportation, customs and other freight related activities
-
-
-
Hewlett Packard Enterprise
-
United States
-
IT Services and IT Consulting
-
700 & Above Employee
-
Logistics Improvement Manager
-
Aug 2009 - Feb 2013
• Set up and manage complex, cross organizational Logistics projects and Governance teams in close cooperation with other organizations (logistics platform, Route to Markets, other Bus, logistic and mfg partners).• Support decision making process on cross-organizational Logistics topics based on detailed investigations and simulations• In coordination with the PSG transportation account mgrs, identify & drive improvement opportunities to improve speed of the delivery process (end to end transportation TAT), predictability (Logistics OTD), and quality of shipments and /or to reduce costs.• Continuously assess customer new requirements in collaboration with the GTMs and proactively identify the required transportation capabilities & Services to Optimize and develop the end to end performance of the transportation network • Act as a lead in logistic process improvements and demonstrate strong expertise in process improvement techniques and Supply chain modeling.• Support and/or drive process improvement skills and mindset at forwarder level.
-
-
-
-
Supply Chain Manager
-
May 2007 - Jul 2009
Major Responsibilities:• Coordinating Procurement Department (in charge with acquisition of all kind of products and services as: raw materials, spare parts, investments, marketing, auxiliary materials, oil & energy, office and administrative, packaging etc.): suppliers selection, negotiation, budgets, and development of internal procedures, stock level• Intercompany purchase of finished goods , transfer prices negotiation • Planning production based on the production capacities , market trend and stocks • Coordinating Logistic Dept.: warehouses , transportation (inbound and outbound), stock management , inventory accuracy • Operational and strategically management , KPI for Supply Chain team• Responsible for supply chain budget Key Accomplishments:• Defining and managing the implementation of purchasing strategies which have realized significant process and cost reduction• Reviewed internal supply chain processes, defined and implemented ERP Purchasing Module for the use of the Purchasing Department• Redesigned warehouse layouts, increasing productivity by 20% • Reduce distribution costs • Re-codification of all products in our internal ERP system and implementation of EAN 13 bar code for all finished goods • Improvement of packaging systems generated very good result: reclamation 0,1 % of total sales (2% in the past)• Inventory management: safety stocks of raw materials and finished goods acc. to the sales and production needs , decrease the level of stocks;• Synergy (logistic and procurement) with subsidiaries from region in order to increase the power of negotiation based on bigger volumes. • Internal and external benchmarking with very good results
-
-
-
Tornado Technology
-
Romania
-
IT Services and IT Consulting
-
1 - 100 Employee
-
Logistic Manager
-
2006 - 2007
Major Responsibilities:• Coordinating Import-Export Dept. • Coordinating logistic team of 26 people • Transportation flows between Tornado's logistics platforms Bucharest and Giurgiu• Transportation flows from the logistics platforms and customers• Expedition of goods to final customers or to distributors• Ensure that the temporary imports process is followed up until the goods is exported• Internal procedures• Budgets of warehouse and import export activitiesKey Accomplishments:• Layout of a new warehouse of 2500 square meters • Improve the internal procedures referring to logistics flows and storage locations • No logistics reclamation from customers as Metro, Selgros • Key Performance Indicators (KPI) for my team as : Inventory accuracy, In Time Delivery, Safe Delivery
-
-
-
Honeywell
-
United States
-
Appliances, Electrical, and Electronics Manufacturing
-
700 & Above Employee
-
Customs Leader
-
Mar 2003 - Apr 2006
Major Responsibilities/ Key Accomplishments:• Issue all documents required for export/import of goods• Ensure that the temporary imports process is followed up until the goods is exported• In charge with physical and document flows for returned goods• Logistics support for transferred of the production line from Honeywell sites to Romania• Interface with Romanian Customs Authorities• Inventory and safety stocks• Customs agent evaluations Major Responsibilities/ Key Accomplishments:• Issue all documents required for export/import of goods• Ensure that the temporary imports process is followed up until the goods is exported• In charge with physical and document flows for returned goods• Logistics support for transferred of the production line from Honeywell sites to Romania• Interface with Romanian Customs Authorities• Inventory and safety stocks• Customs agent evaluations
-
-
-
-
Buyer
-
2000 - 2003
Major Responsibilities / Key Accomplishments:• Purchasing of goods (raw materials , spare parts for the production lines )• Increase of the suppliers portfolio• Preparing of the technical specifications for company inquiries• Technical drawings for purchased goods• Negotiation of the contracts/agreements• Transportation for the goods with ExWorks INCOTERMS delivery condition• Customs formalities Major Responsibilities / Key Accomplishments:• Purchasing of goods (raw materials , spare parts for the production lines )• Increase of the suppliers portfolio• Preparing of the technical specifications for company inquiries• Technical drawings for purchased goods• Negotiation of the contracts/agreements• Transportation for the goods with ExWorks INCOTERMS delivery condition• Customs formalities
-
-
Education
-
University POLITEHNICA of Bucharest
-
iulia hasdeu
-
scoala generala
Community
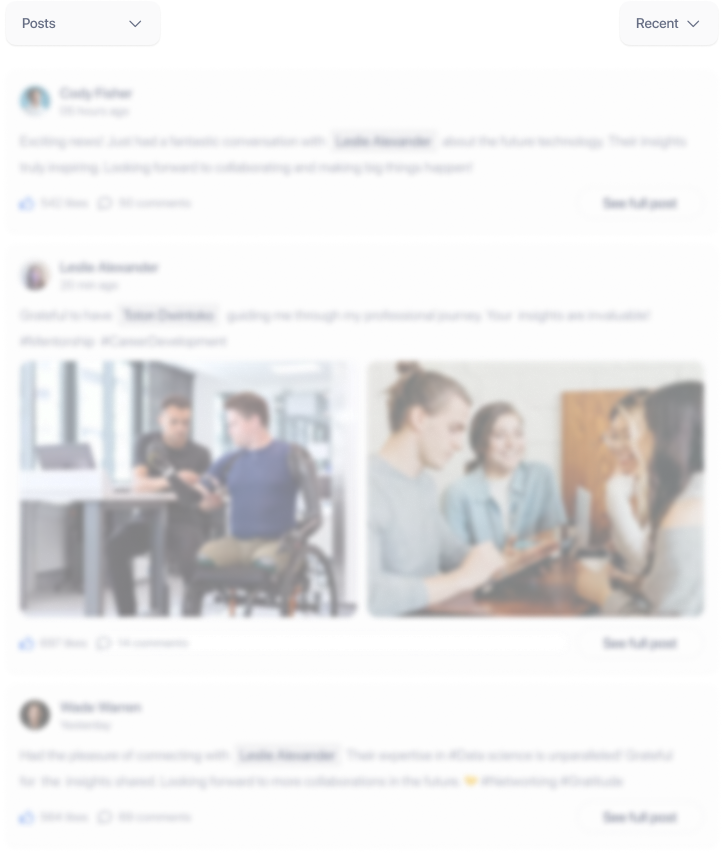