Mira Evrard
Senior Quality Assurance Consultant Life Sciences at Nalys- Claim this Profile
Click to upgrade to our gold package
for the full feature experience.
-
English Professional working proficiency
-
French Native or bilingual proficiency
-
Dutch Native or bilingual proficiency
Topline Score
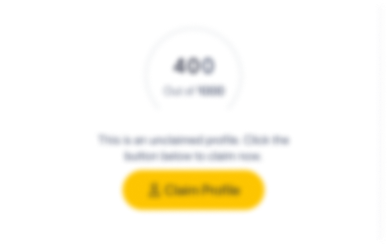
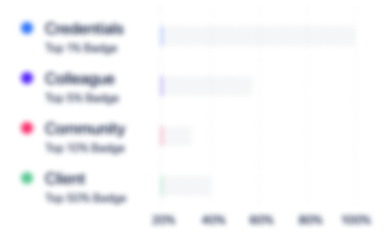
Bio


Experience
-
Nalys
-
Belgium
-
Business Consulting and Services
-
100 - 200 Employee
-
Senior Quality Assurance Consultant Life Sciences
-
Sep 2019 - Present
Current mission: GxP and GMP/GDP Quality Management System (QMS) Consultant - UCB Drive the development, implementation and maintenance of a Quality Management System framework Ensure lifecycle management of GMP/GDP Corporate Quality Management System and support these activities within the GxP QMS. Close strategic partnering with senior leaders and functional QMS Leads. Escalate any GMP/GDP QMS related issue to the QMS Governance and define appropriate actions in collaboration with the relevant stakeholders. Lead or participate to GxP and GMP/GDP QMS workstreams. Define and develop the training strategy for GMP/GDP QMS its deployment together with the training team. Second mission: Support Global Quality Lead GMP Auditing & Compliance on “Lack of Efficacy complaint case management” project - UCB • Revision of the complaint intake process to request relevant quality of medicine information (e.g. batch number) for lack of efficacy cases received by the Local Safety Officer, implementation of process to relay relevant information to the Quality unit and implementation of quality related investigation to elucidate the potential quality management background of the complaint. Assess and implement similar process for other adverse events or Safety information as deemed necessary. Implement new process on a global level. First mission: QA partner QMS master data - UCB • Establish a consolidation/harmonization of product defect coding/values for complaints between documentation and TrackWise (computerized system) Show less
-
-
-
Prothya Biosolutions
-
Belgium
-
Pharmaceutical Manufacturing
-
400 - 500 Employee
-
QA Engineer Operational
-
Sep 2015 - Aug 2019
• Complaint handling (SME) o Investigation, determine root cause and define CAPA plan to prevent re-current complaint o Set-up and follow-up of complaints to vendor • Audits o Internal audits: Auditee for complaint handling / Participate o External audits: Technical and administrative explanation towards the inspector/partner regarding questions to complaints and/or deviations • During shutdown period o Release of the clean room to start-up the shutdown activities o Daily check on the floor to observe the ongoing activities and report GMP shortcomings o Daily shutdown meeting: provide feedback on observed GMP shortcomings o Follow-up of the progress of the mandatory documentation to perform the release o Review of all GMP related documentation (e.g. sterilisation of the water systems; temperature trends of cold rooms, CoA reports QC results utilities, etc.) o Release of the cleanroom to start-up production activities • Deviation handling • QA-on-the-floor • Quality box • Collaboration Plasma Industries Belgium – Customer • Document and Batch Record Review • QA guard (24h availability) Show less
-
-
-
CAF-DCF
-
Belgium
-
Pharmaceutical Manufacturing
-
1 - 100 Employee
-
Preventive Maintenance Coordinator + Teamleader @interim (since 24th December 2014)
-
Sep 2014 - Sep 2015
During shutdown period: • Plan and coordinate all shutdown activities over several departments: maintenance, engineering, QA, production, QC, process validation, building, contractors • Focus on Safety – meeting with Safety department for revision of introduction booklet and work permit • Lead the shutdown meetings with all the concerned departments • Highlight the foreseen bottleneck(s) and discuss actions to be taken to solve the bottleneck(s) in order to keep the production start-up date • Daily follow-up of all activities to act fast if some unexpected problems occur • Check if all activities can be closed based on the PDCA circle • Final wrap-up meeting: provide the documention/data needed for QA to release the production Daily tasks: • Plan and coordinate all maintenance activities in accordance with production • Check if all work orders are completed GMP wise • Follow-up Maintenance Year Plan and evaluate with Maintenance Engineer(s) if adjustments are needed Teamleader @interim (24th December 2014-16th April 2015) • Manage / coach a team of 8 Maintenance Technicians • Encourage the team to bring up and participate to improvements • Follow-up of breakdown(s) and maintenance activities • Set up personnel planning Show less
-
-
-
Perfetti Van Melle
-
Netherlands
-
Food and Beverage Services
-
700 & Above Employee
-
QA/QC officer
-
May 2013 - Sep 2014
Set up an d follow up of Quality and Food Safety Standards. Management of the QMS by focusing on continuous approvement of the processes and methods to achieve and guarantee a high qualitative and safe product. Measure and interpret the product and/or process characteristics to assure that the Quality and Food Safety Standards are achieved. Management of the QMS documents according to the FSSC 22000, ISO 9001, ISO 14001 Standards. Organize and participate in internal and external audits to meet legal obligations and certification. Point of contact for external quality issues ( for example pest control, food safety (FAVV), ISO9001). Analyze and closure of consumer and supplier complaints. Validation of new products, processes and/or equipment to assure that Food Safety Standards are met. Participate, set up and follow up of improvement projects (Kaizen projects). Management of CAPA list: follow up of actions defined during internal audits and inspection of Food safety (FAVV). Participate to several meetings to inform about QA/QC matters to attain an alignment on these QA/QC matters on operational and tactical level. Training of employees regarding QA/QC matters. Show less
-
-
-
Sapa Building System BV
-
Landen
-
Production Planner
-
Nov 2012 - Apr 2013
Planning of output paint shop taking into account delivery times, inventory levels, capacity and efficiency. Follow-up of the planning and adjust if necessary. Detect bottlenecks in stockpile and lead times. Open communication with all concerned departments. Optimization and follow-up of lead times in the paint shop. Set up reports on frequent basis. Planning of output paint shop taking into account delivery times, inventory levels, capacity and efficiency. Follow-up of the planning and adjust if necessary. Detect bottlenecks in stockpile and lead times. Open communication with all concerned departments. Optimization and follow-up of lead times in the paint shop. Set up reports on frequent basis.
-
-
-
-
Production Planner
-
May 2010 - Sep 2012
Optimization of the production lines by using the good raw materials to achieve the highest efficiency of the finished product.Placing orders and follow-up of raw materials.Put new codes – products in the ERP system.Weekly meeting with production, maintenance and R&D to discuss the planned maintenance activities and the R&D tests.Monthly meeting with Sales, Quality and Finance to discuss the customer complaints (possible return of goods), the sales and the consignments.Monthly inventory of raw materials, BOM materials and finished products. Show less
-
-
Quality Engineer
-
Aug 2007 - May 2010
Set up procedures, instructions, forms and quality manual to achieve the ISO 9001-2000 certificate (achieved 2009).Set up and follow-up of action plans due to internal deviations, customer and supplier complaints to aim a continuous improvement of processes and KPI’s.Perform internal and supplier audits.Point of contact for quality issues.
-
-
-
Danone
-
France
-
Food and Beverage Manufacturing
-
700 & Above Employee
-
Production Planner
-
1998 - 2007
Plan forecasts and orders through SAP into the GMP planning (planning system).Plan 14 production lines and 4 preparations.Optimization of the amount of switches (x4, x6, x8…product and fruit switches) to aim the best efficiency / throughput without losing the quality of the product.Order and follow-up of primary raw materials based on the production schedule.Daily communication with production, technical department and distribution centre regarding status of the time scheme of the production (backlogs, stoppages,…). Show less
-
-
Quality Technician
-
1998 - 2007
Perform quality controls according to the quality plan.Daily follow-up of internal deviations and customer complaints.Startup and follow-up of projects: HACCP, LAF production lines, procedure glass breakage.Perform internal and supplier audits.Validation of new equipment and processes.
-
-
Education
-
Groep T - Internationale Hogeschool Leuven
Bachelor's degree, Chemical Engineering
Community
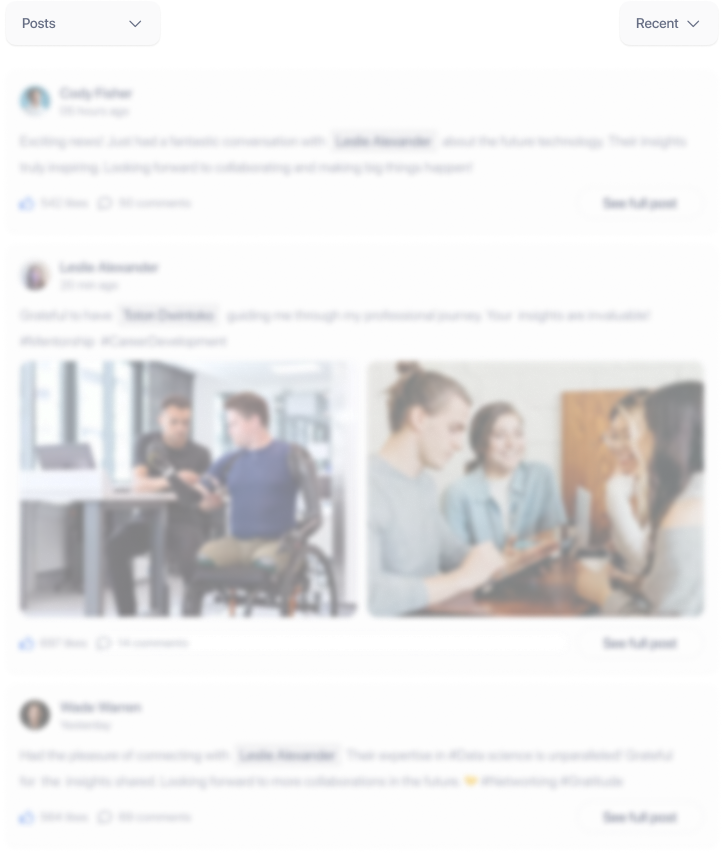