Mike Saffarian
Plant and Manufacturing Manager at Northrop Grumman - Astro Aerospace- Claim this Profile
Click to upgrade to our gold package
for the full feature experience.
Topline Score
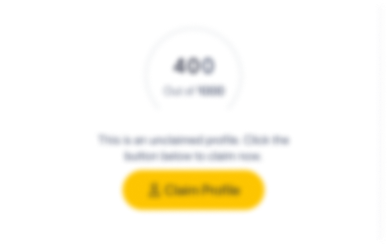
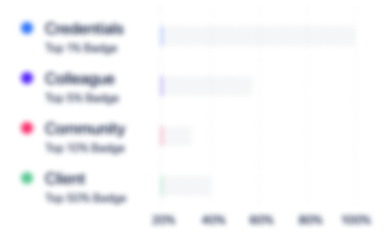
Bio
0
/5.0 / Based on 0 ratingsFilter reviews by:
Experience
-
Northrop Grumman - Astro Aerospace
-
United States
-
Aviation and Aerospace Component Manufacturing
-
1 - 100 Employee
-
Plant and Manufacturing Manager
-
Aug 2018 - Present
-
-
-
-
Director of Operations, Manufacturing Engineering and Continuous Improvement
-
Nov 2005 - Feb 2018
• Directed and facilitated operational excellence activities and converted operational goals into operational projects. Aligned resources to support these projects and insured projects were completed on-time and within budget. • Reduced scrap from 6% COGS to less than 1.5% COGS, which is a reduction equivalent to $500K annually from 2007 to the present. • Improved on-time delivery for 10 different production lines from 75% to above 97% on-time. Led teams that identified root causes of late deliveries and implemented corrective actions. • Completed and documented 189 continuous improvement projects from January 2009 to March 2012. These projects led to direct improvements in: safety, cost reduction, cycle time, customer satisfaction, scrap reduction, and on-time delivery. • Implemented lean philosophies throughout the facility (reduction of batch size, 5S, pull system, kanban, value stream mapping). • Championed creation of F-16 Canopy Actuator cell, which produced 1.6 million dollars of sale each month with only 4 employees at (peak) production. • Represented MSSI in manufacturing and quality audits with customers such as Airbus, Boeing, Rolls Royce and the U.S. Government. • Created automated manufacturing equipment to reduce process deviation, collect process data, reduce risk, and improve lead time in support of Meggitt’s strategic goals. • Trained 300 Meggitt employees in lean philosophy, manufacturing cell set up, point of use storage, kanban, and continuous flow for the manufacturing of the Boeing 737NG engine fire and over heat detectors; thus, achieving our goal to increase production rates and improve on-time delivery. Show less
-
-
-
-
Director of Operation and Quality
-
2002 - 2005
Responsible for the management of manufacturing operations, which also included purchasing of parts and planning for the manufacturing of custom designed laboratory equipment for medical and biomedical companies. Implemented lean manufacturing, cellular manufacturing, pull system and lead time reduction throughout the factory. • Achieved 100% on-time delivery to construction sites. • Reduced production hours to one shift by creating a one-piece flow cell that eliminated in process inventory and improved production lead time. • Eliminated stock room and setup point of use Kanbans and storage for the replenishment of parts. Show less
-
-
-
California Manufacturers & Technology Association (CMTA)
-
United States
-
Non-profit Organizations
-
1 - 100 Employee
-
Manufacturing and Lean Consultant
-
1998 - 2002
Provided clients with a wide range of manufacturing and management expertise including: process optimization, quality and operation system audits and assessments, facility layout, equipment modernization, and supply chain management. My focus was the implementation and training of lean manufacturing systems such as Kaizen, Cellular Manufacturing, Pull System, Value Stream Mapping, Workplace Organization (5S), Total Productive Maintenance (TPM), Visual Control, Set-up Reduction, and Quality at Source. Show less
-
-
-
Moog Inc.
-
United States
-
Aviation and Aerospace Component Manufacturing
-
700 & Above Employee
-
Director of operation
-
1996 - 1998
Responsible for the overall management of vertically-integrated manufacturing operations with a focus on planning the production and delivery of high quality space qualified solar array drive assemblies (SADA). Managed the production, material management, machine shop, and manufacturing engineering teams. Responsible for the overall management of vertically-integrated manufacturing operations with a focus on planning the production and delivery of high quality space qualified solar array drive assemblies (SADA). Managed the production, material management, machine shop, and manufacturing engineering teams.
-
-
-
Honeywell
-
Software Development
-
1 - 100 Employee
-
Director Of Operations
-
1995 - 1996
Managed manufacturing, production, quality, and manufacturing engineering teams for the production of temperature sensors for commercial and military use. Responsible for operational metrics such as on-time delivery, quality, safety, costs of goods sold and scrap reduction. Managed manufacturing, production, quality, and manufacturing engineering teams for the production of temperature sensors for commercial and military use. Responsible for operational metrics such as on-time delivery, quality, safety, costs of goods sold and scrap reduction.
-
-
-
Kavlico Pressure Sensors
-
Appliances, Electrical, and Electronics Manufacturing
-
100 - 200 Employee
-
Manufacturing Engineering Manager
-
1987 - 1995
Managed a team of manufacturing engineers, process engineers, toolmakers, and machine builders. Designed, built, and qualified new production lines using internal resources and external suppliers in a fast pace rapidly growing automotive pressure sensor manufacturing factory. Responsible for transfer of new product designs from R&D to production, as well as prototype and pre-production builds. Managed a team of manufacturing engineers, process engineers, toolmakers, and machine builders. Designed, built, and qualified new production lines using internal resources and external suppliers in a fast pace rapidly growing automotive pressure sensor manufacturing factory. Responsible for transfer of new product designs from R&D to production, as well as prototype and pre-production builds.
-
-
Education
-
University of Southern California
Masters of Science in Manufacturing Engineering, Manufacturing Engineering -
University of Southern California
Bachelor of Science in Industrial and Systems Engineering, Industrial and Systems Engineering
Community
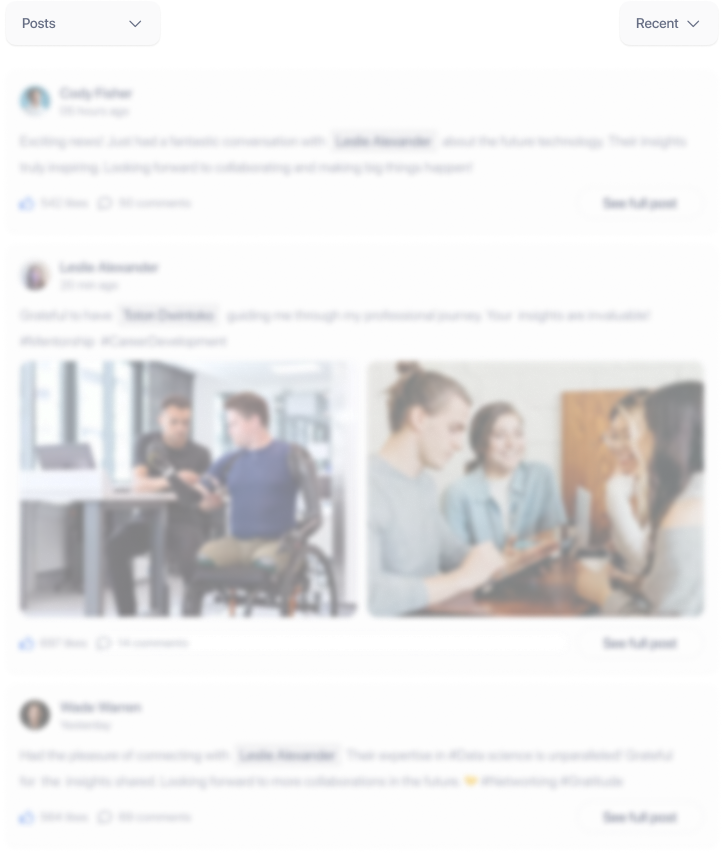