Mike Maldonado
Plant Manager at Luck Stone- Claim this Profile
Click to upgrade to our gold package
for the full feature experience.
Topline Score
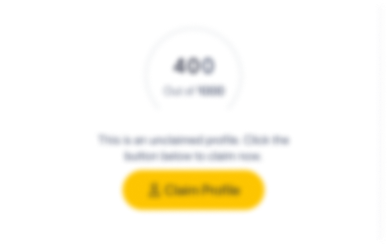
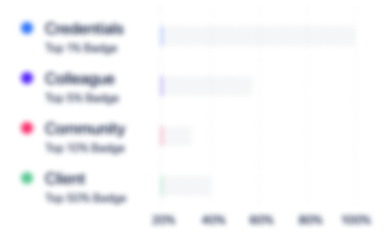
Bio


Experience
-
Luck Stone
-
United States
-
Mining
-
1 - 100 Employee
-
Plant Manager
-
Nov 2022 - Present
-
-
Assistant Plant Manager
-
Oct 2021 - Nov 2022
-
-
Pit Foreman
-
May 2021 - Oct 2021
-
-
Plant Foreman
-
Oct 2020 - May 2021
-
-
-
BrightView Landscapes
-
United States
-
Facilities Services
-
700 & Above Employee
-
Project Manager
-
Jul 2020 - Oct 2020
-
-
-
Hi-Crush
-
United States
-
Oil and Gas
-
100 - 200 Employee
-
Plant Manager
-
Jun 2018 - May 2020
• Directed 70 employees and related programs to maximize team productivity and facility output• Redesigned operational workflow processes to maximize efficiency• Maximized employee safety utilizing proactive strategies and well-structured training• Managed daily operations of two, 2.8 million ton Frac Sand Mines annually per plant• Planned and controlled plant budgets more than $32 million annually• Worked closely with mining planner to ensure maximization of mine assets • Coordinated well-organized maintenance program for predictive and preventive scheduling• Assessed logs and reports to identify inefficiencies, boost production levels and enhance safety• Worked directly with supply chain and sales to meet monthly sales quotas• Oversaw rail operations for shipped products consisting of 115 car unit trains daily• Worked closely with shipping manager to maximize rail yard utilization with a capacity 800 rail cars• Directed drilling and blasting operations in mine pit to ensure production schedules are met• Responsible for CapEx projects ranging between 2-4 million dollars annually Show less
-
-
Wet Plant Manager
-
Jan 2015 - Jun 2018
• Responsible for implementing key phases of initial start up including in excess of 4,000 feet of overland conveyor system, wash towers, plate and frame presses and crushing lines while focusing on reducing initial costs and maintaining zero lost time injuries • Recruited, hired and trained 20 employees for the wash plant start up• Created process to recruit key employees• Increased retention through key touch points, communication and team mentality• Implemented key processes to improve efficiencies, quality control and labor costs through design changes• Managed 900 ton/hour Frac sand wet plant including 1200 ton/hour crushing line• Key contributor with track record of meeting or exceeding production goals of 3 million tons• Responsible for reclamation of all effluent water used in the wash process to be chemically treated and reused in the system• Saved $300,000 by implementing cost-saving initiatives and led team in installation of overland conveyer system Show less
-
-
-
Preferred
-
United States
-
Oil and Gas
-
1 - 100 Employee
-
Production Supervisor
-
Sep 2012 - Jan 2015
• Oversaw all process of both wet and dry plant operations to ensure production goals are met• Maintained quality control measures, environmental and safety requirements and scheduling• Created a team atmosphere through a hands-on approach focusing on leading by example• Plant production averaged 450 ton/hour wet plant, 180/ton hour dry plant daily operations• Managed 10 employees while reporting directly to the production manager
-
-
Rail Load Out Operator
-
Apr 2011 - Sep 2012
• Inspected and loaded rail cars, tested sand profiles for correct gradation• Assisted with logistics to ensure tonnage and products were correct before shipping• Managed quality assurance program including on -site evaluations, internal audits and customer surveys
-
-
-
Berg & Maldonado Construction
-
Blair, WI
-
Co-Owner
-
Jan 2003 - Apr 2011
• Self-employed owner designing and constructing residential homes • Planned, directed and coordinated budgeted all activities with construction • Prepared budget estimates and progress cost tracking reports • Delivered positive customer experience through day-to-day supervision and management • Self-employed owner designing and constructing residential homes • Planned, directed and coordinated budgeted all activities with construction • Prepared budget estimates and progress cost tracking reports • Delivered positive customer experience through day-to-day supervision and management
-
-
-
Independence Lumber
-
Independence, WI
-
Contractor Sales
-
Aug 1996 - Jan 2003
• Contractor sales for residential building materials • Material estimates, home design and construction coordinator • Resolved construction related problems, improved operations and provided exceptional customer support • Contractor sales for residential building materials • Material estimates, home design and construction coordinator • Resolved construction related problems, improved operations and provided exceptional customer support
-
-
-
United States Marine Corps
-
United States
-
Armed Forces
-
700 & Above Employee
-
Infantry Squad Leader
-
Jan 1986 - May 1990
• Combat Infantry Squad during first Gulf War-Operation Desert Storm • Refined skills as Squad leader to transition into mining • Developed teamwork, motivation and leadership skills • Resolved conflicts and negotiated mutually beneficial agreements between parties • Combat Infantry Squad during first Gulf War-Operation Desert Storm • Refined skills as Squad leader to transition into mining • Developed teamwork, motivation and leadership skills • Resolved conflicts and negotiated mutually beneficial agreements between parties
-
-
Education
-
Western Wisconsin Technical College
Technical Degree, Building Trades
Community
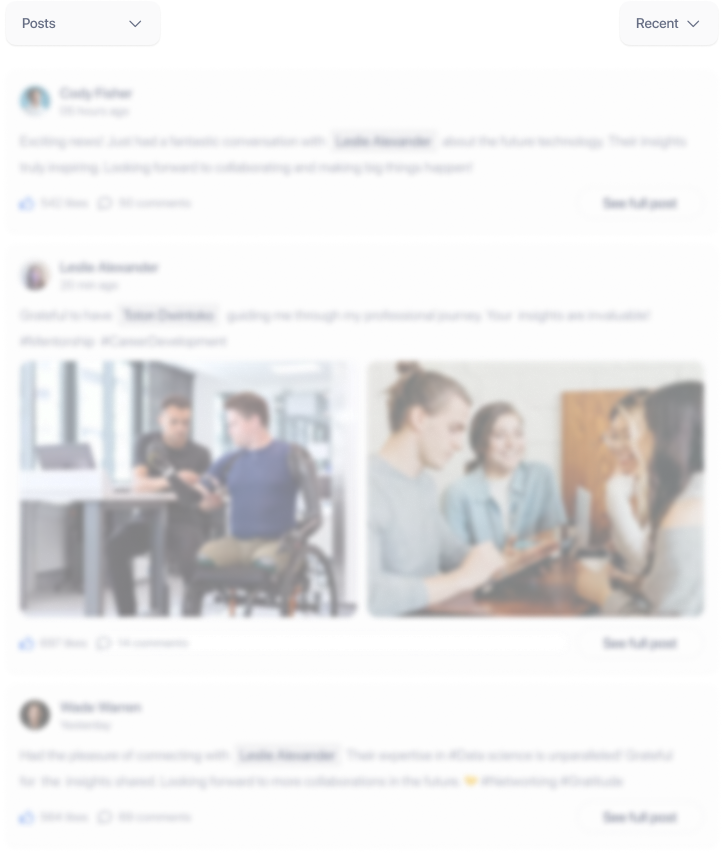