Mike Lynch
Senior Director Of Operations & Deployment at Edison Interactive- Claim this Profile
Click to upgrade to our gold package
for the full feature experience.
Topline Score
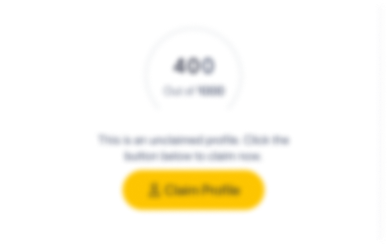
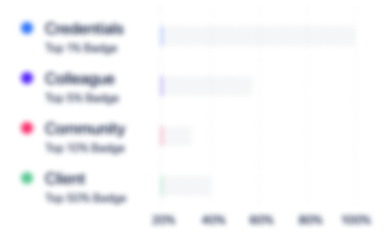
Bio

LinkedIn User
Michael has been a tremendous pleasure in working with and adding incredible value to our organization through his ideas and problem-solving.

LinkedIn User
Michael has been a tremendous pleasure in working with and adding incredible value to our organization through his ideas and problem-solving.

LinkedIn User
Michael has been a tremendous pleasure in working with and adding incredible value to our organization through his ideas and problem-solving.

LinkedIn User
Michael has been a tremendous pleasure in working with and adding incredible value to our organization through his ideas and problem-solving.

Experience
-
Edison Interactive
-
United States
-
Technology, Information and Internet
-
1 - 100 Employee
-
Senior Director Of Operations & Deployment
-
Oct 2021 - Present
-
-
Director Of Operations & Deployment
-
Jun 2021 - Dec 2021
-
-
Director Of Operations
-
Oct 2019 - Dec 2021
Edison Interactive is a leading software provider that builds customized interactive customer experience solutions for complex environments. Edison has built unparalleled customer experience solutions for industry-leading Fortune 500 companies. Shark Experience presented by Verizon is now available in 23,000+ golf cars in the U.S., and the Avis Budget Group (ABG) Travel Assistant is available to car rental customers at top airport and local-market locations throughout the U.S. and Canada with plans to expand globally. With robust analytics and ancillary revenue opportunities, Edison has enabled brands to connect with customers in more relevant and meaningful ways. The company was founded in 2016, and is headquartered in Denver, Colorado.
-
-
-
B&B Pharmaceuticals, Inc.
-
United States
-
Pharmaceutical Manufacturing
-
1 - 100 Employee
-
Quality Assurance Manager
-
Jun 2016 - Oct 2018
•Reviewed lab data, validation and stability protocols/documents, batch records, specifications, and manufacturing orders for compliance.•Supported manufacturing through timely process of deviations, change controls, CAPA complaint handling, and investigations to ensure quality products.•Conducted facility and/or supplier assessments, raw material release, and line clearances.•Authorized and updated SOPs as needed.•Followed GMP guidelines to adhere to SOPs and GMP requirements.•Communicated QA issues to employees and managers in a tactful manner.•Executed multiple projects at once with changing deadlines and priorities.
-
-
Production Manager
-
Sep 2015 - Oct 2018
Directed a multifunctional team responsible for safely producing API's (active pharmaceutical ingredients) in compliance with regulatory requirements (cGMPs, FDA/DEA regulations, etc.), within company policies and goals. •Created planned and executed, all production orders while maintaining all cGMP and Federal and State guidelines.•Managed the overall activities of a functional area within the manufacturing facility, while implementing policies/procedures and assuring employees understood/complied with all cGMPs, SOP's, procedures, FDA, DEA, and OSHA regulations.•Responsible for assuring maximized utilization of resources (including highlighting opportunities for improvement).•Developed functional processes for area managed and executed periodic reviews.•Drove, monitored and assured delivery of product, within the department •Continuously improved data integrity, knowledge base and understanding within the department.
-
-
Warehouse Manager
-
Aug 2015 - Oct 2018
•Compared prices amongst various vendors in order to make sound purchasing decisions which benefited the overall operation of the company.•Worked within a given budget to purchase goods and services for an organization.•Ensured that products were delivered in a timely manner, and that the quality of the goods received was satisfactory.•Negotiated with contractors on price, mode of shipping, and delivery time.•Checked invoices for accuracy, and authorized the accounts payable department to issue payment.•Evaluated the performance of certain vendors in order to decide whether or not to continue purchasing from them.•Managed all inventory of items in order to determine which ones need to be purchased.•Entered data concerning inventory and order amounts into a computer database (ERP).
-
-
Sales and Account Manager
-
Aug 2008 - Oct 2018
Maintained and increased market share with assigned accounts and territory, keeping over 70% profit margin on all sales, while developing and maintaining sound customer relations. Maintained and drove new business from all top accounts, which generated over 4 million in sales. •Identified new business opportunities, generated leads, closed new business and converted accounts from competitor products. While professionally driving a sense of urgency in accounts to speed up purchasing decision.•Maintained knowledge of the current industry and competitive landscape. Interacted with Marketing, Customer Service, Production and other internal departments to ensure product quality guidelines were in compliance.
-
-
Procurement Specialist
-
Aug 2015 - Nov 2017
•Compared prices amongst various vendors in order to make sound purchasing decisions which benefited the overall operation of the company.•Worked within a given budget to purchase goods and services for an organization.•Ensured that products were delivered in a timely manner, and that the quality of the goods received was satisfactory.•Negotiated with contractors on price, mode of shipping, and delivery time.•Checked invoices for accuracy, and authorized the accounts payable department to issue payment.•Evaluated the performance of certain vendors in order to decide whether or not to continue purchasing from them.•Managed all inventory of items in order to determine which ones need to be purchased.•Entered data concerning inventory and order amounts into a computer database (ERP).
-
-
Senior Production Technician
-
Oct 2006 - Oct 2013
•Worked all areas of production operation: weighing, blending, filling, packaging, and cleaning of products. •Accurately weighed product.•Blended product according to batch record and SOP. •Accurately filled and packages materials.•Cleaned equipment and rooms to specifications.•Regularly inspected equipment for proper functioning.•Meet productivity and production schedules and deadlines.•Troubleshot process/production problems.•Assisted with inventory duties such as receiving, product retrieval and shipping.•Safely operated forklift.•Assured production was in compliance with established standard operating procedures, cGMP quality standards and regulatory procedures•Accurately and consistently completed and documented batch records and other required paperwork for compliance
-
-
Customer Service Specialist
-
Oct 2006 - Aug 2008
•Served as a first point of contact and responded to customer inquiries via telephone or email.•Increased revenue on all inbound orders. •Processed orders in our ERP system. •Ensured proper order handling and follow-up with accounts to maintain ongoing business.•Liaise with Sales and Operations on issues, customer requests, etc.•Received and processed complaints and/or issues and provided feedback and resolution to the customers.•Verified and updated customer data in our ERP systems- Microsoft Navision, ACT and Sales Force.
-
-
Education
-
Metro State University
Business Administration and Management, General
Community
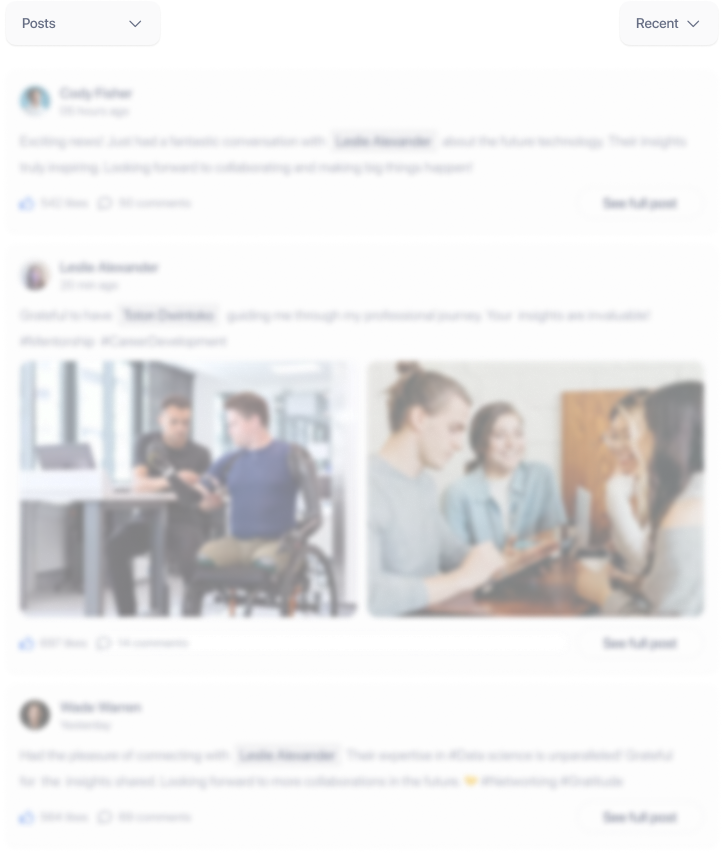