Mike Lancaster
Operations Manager at Runamok Maple- Claim this Profile
Click to upgrade to our gold package
for the full feature experience.
Topline Score
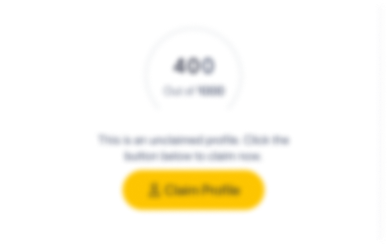
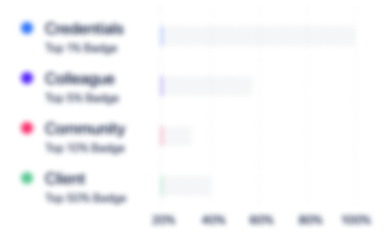
Bio


Experience
-
-
Operations Manager
-
Aug 2021 - Present
Runamok is a family-owned, Vermont based company that started with a foundation of premium, organic maple syrup and has expanded to an array of maple and honey-based products. Started by husband and wife, Eric and Laura Sorkin, we began tapping our woods in Cambridge, Vermont in 2009. For the first six years, we sold our maple crop on the bulk market but in 2016, with our eyes set on elevating maple in new and innovative ways, Curt Alpeter joined the team as a Partner and we started our own retail line.Our focus was on creating a truly unique maple syrup product and brand. With elegant packaging, innovative flavor profiles, and the highest quality ingredients, our infused, smoked and barrel-aged maple made waves in the food world from Oprah’s Favorite Things to Saveur and Food&Wine. In 2021 we expanded into nature’s other exquisite sweetener and started a line of raw varietal, infused, and hot honeys.
-
-
-
Bee's Wrap
-
United States
-
Manufacturing
-
1 - 100 Employee
-
Director of Production and Fulfillment
-
Nov 2019 - Aug 2021
Reuseable food storage, made with care in Vermont.Our Mission at BEE’S WRAP is to inspire planet positive habits every day. We are making considered choices for our daily lives by challenging single-use consumption. Bee's Wrap is a Certified B Corporation & we actively work with partners like 1% for the Planet & 5 Gyres to stem the tide of plastic pollution.Bee’s Wrap is available in more than 2400 stores across the US & found in the gift, grocery, housewares, &outdoor markets. Distribution extends internationally throughout the UK, Europe, Canada, South Africa, New Zealand, Australia, and parts of Asia.• Oversee & support day-to-day activities of the manufacturing process, from acquisition of raw material to delivery of finished goods• Increase throughput, quality, and efficiency in manufacturing processes in order to handle rapid growth• Meet efficiency, volume, cost, quality, safety, and profitability KPIs as established in partnership with management peers• Work with managers to develop job descriptions, paths for growth, and structured performance evaluations for production floor employees.• Continually improve the company's health and safety program to promote employee awareness of safety and minimize accidents and injuries• Develop and maintain an effective quality assurance system• Oversee order fulfillment process and ensure orders are fulfilled within company’s time frame and accuracy goals• Oversee implementation of new product development• Research and implement systems, equipment and tools to increase efficiencies, better utilize space, and/or reduce production costs• Oversee finished goods inventory levels and FIFO inventory management• Develop reports and metrics to track production floor efficiencies, identifies opportunities for improvements, and measures progress• Actively ensure an engaging, supportive and respectful workplace marked by high levels of collaboration, transparent communication and supportive policies
-
-
-
Pure Energy Apothecary
-
United States
-
Personal Care Product Manufacturing
-
1 - 100 Employee
-
Co-Founder/Manufacturing/Operations
-
Aug 2017 - Nov 2019
Pure Energy Apothecary is focused on creating all natural, plant-based body care and home fragrances focused on good health and balance for everyone. We are mission driven to bring quality, plant-based body care to all. Simple, readable ingredients offering luxury performance yet priced for all.CO-FOUNDER• Collaborate in brand development, mission, and product formulation.• Participate in launching and managing a second self-funded business while managing and growing original. MANUFACTURING MANAGER• Develop lean manufacturing policies, procedures and best practices to support small batch, fresh production mission.• Source and maintain manufacturing equipment.• Insure proper inventory levels and maintain quality control.OPERATIONS MANAGER• Project management, workflow and prioritize orders. • Purchasing (stock, supply and vendor relationships). R & D • Evaluate new product feasibility and formulations.
-
-
-
Carved Solutions
-
Manufacturing
-
1 - 100 Employee
-
Founder/COO
-
Feb 2006 - Oct 2018
CO-FOUNDER• Determine demand for high quality personalized gifts with a made in USA focus • Design & create custom carving equipment for personalization of soap & candles creating the base of a brand that would grow to set the bar for quality in the personalized gift industry.• Develop lean manufacturing policies, procedures and best practices to establish a tight 24-48 hour turnaround time with one-off, drop ship gifts in a high-volume manufacturing environment. - - This dependable production time established the standard for fulfillment in today’s gift industry. • Start and grow a self-funded, luxury product business at the height of the recession. MANUFACTURING MANAGER• Create and/or source custom manufacturing equipment and software for all manufacturing departments • Laser Engraving, CNC Carving, Metal Casting, Candle Pouring, Hot Stamping, Sublimation, Embroidery, Wood Product Manufacturing, Large Format Printing• Create, maintain and improve all manufacturing procedures, policies and best practices.• Oversee, train, support and schedule all coding, production and fulfillment staff members. • Quality Control: Establish and supervise “5 Star Client Care”. This best practice creates trust in our reputation as our nationwide retailers know they can depend on promoting Carved Solutions in their stores as the products will be received timely and correct every time.OPERATIONS MANAGER• Project management, workflow and prioritize orders across 9 different departments• Purchasing (stock, supply and vendor relationships) • Troubleshoot and resolve any equipment, software and IT issues.R & D • Create and/or source new products and technologies
-
-
-
SUSS MicroTec
-
Germany
-
Semiconductor Manufacturing
-
400 - 500 Employee
-
Senior Product Manager
-
1999 - 2008
• Product manager is a key role in producing new product designs and development with all departments. From idea conception, client presentation, design overview, management, new design build, new design customer installation, and final acceptance at customer’s site.• Oversaw and managed all daily activities for US facility including, manufacturing department, assembly department , QA, final test.• Managed service department for North America.• Main technical contact for sales and technical sales support.• Served as primary contact between within Germany and North America for all technical related issues.
-
-
Product Specialist
-
1993 - 1999
• Provided technical assistance to North America sales, service department, manufacturing & R&D • Main primary contact within North America for all technical related issues.
-
-
Manufacturing Production Technician
-
1990 - 1993
• Performed assembly, QA, and test machine function.• Repaired semiconductor manufacturing machinery lithography aligners, scribers, & test equipment.
-
-
Apprentice Program
-
1988 - 1990
Trained in all aspects of:• Metal working machine shop.• Electronics troubleshooting and repair.• Pneumatics design.• Optical design and repair.• Mechanical machine design with emphasis on hands on training.
-
-
Education
-
Champlain College
Electronics Technologies, Electrical and Electronics Engineering -
Suss Microtec Apprentice Program
Mechanical, Electrical, Pneumatics, Optical
Community
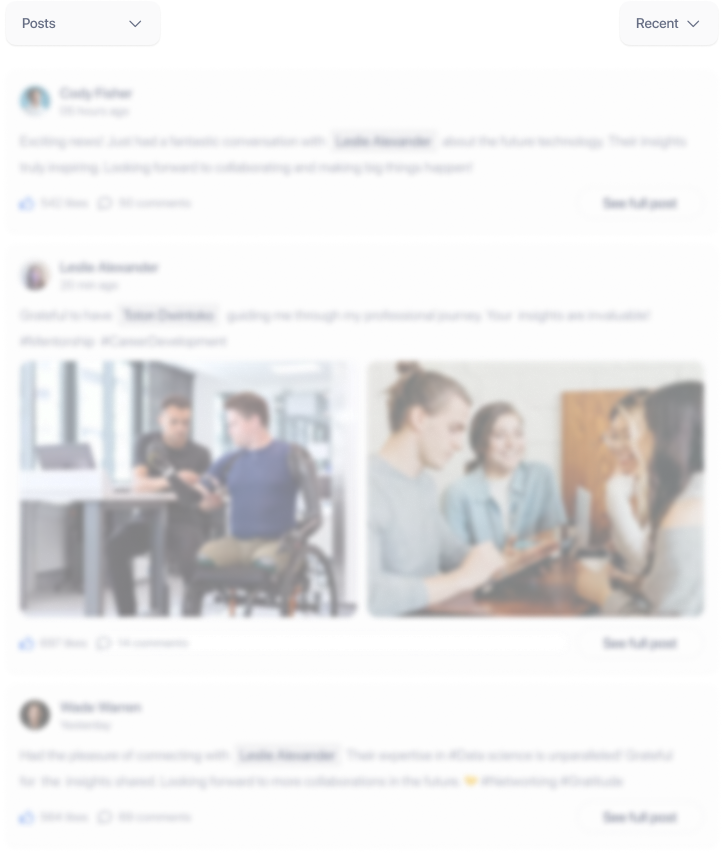