Mihaly Kovacs
General Manager at Flow Dry Technology Inc.- Claim this Profile
Click to upgrade to our gold package
for the full feature experience.
Topline Score
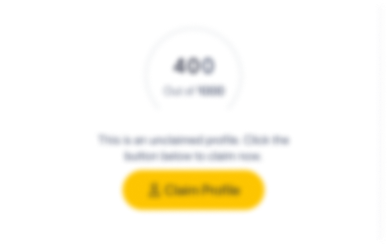
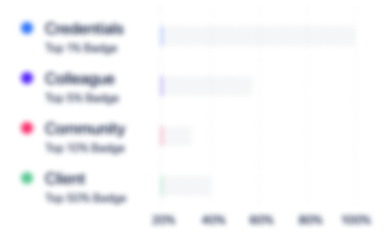
Bio


Experience
-
Flow Dry Technology Inc, Filtration Group Corporation
-
United States
-
Packaging and Containers
-
1 - 100 Employee
-
General Manager
-
Dec 2018 - Present
-
-
-
Hammel & Hochreiter Business & Management Consulting Kft.
-
Hungary
-
Human Resources Services
-
1 - 100 Employee
-
Interim Manager
-
Apr 2018 - Dec 2018
Working on crisis and change management projects at Tier1/Tier2 automotive supplier plants as operations/manufacturing/maintenance/quality manager, depending on the requirements of the partners Working on crisis and change management projects at Tier1/Tier2 automotive supplier plants as operations/manufacturing/maintenance/quality manager, depending on the requirements of the partners
-
-
-
ESSENTRA FILTER PRODUCTS LIMITED
-
Budapest
-
General Manager
-
Oct 2016 - Jan 2018
- The provision, maintenance and continuous improvement of a safe, healthy and constructive working environment for the site operations team. - Lead corrective actions and have customer facing contact where operational deviations make this appropriate - Review with commercial management the sales and volume opportunities impacting the site. - Regularly review all key performance indicators to develop and manage corrective or improvement actions. - Own the top level continuous improvement plan for the site operations focusing on the sustainable improvement of productivity, inventory reduction, health and safety, delivery performance, cost avoidance/reduction and the training and development of operations employees - Coach and mentor direct reports to be effective leaders of their function and to support the top level operations objectives. - Participate in site financial reviews. Develop and maintain budgets for direct, indirect and support function employees, operating expenses and capital projects. - Ensure that cost/margin objectives are met for all products and variances are identified and corrected in a timely manner. Participate in price discussions with commercial teams to ensure optimization of Gross Margin on existing and tendered business. - Ensure that all operations functions support all appropriate quality standards, ISO 9001, BRC and ISO 14001 processes and procedures so that certifications and systems are continually maintained. - Work constructively with the managers of all site functions and other Site Managers/General Managers across the Group to optimize operational performance and overall profitability - Take on the leadership and any special projects as developed by the European Leadership Team Show less
-
-
-
Thermo Fisher Scientific
-
United States
-
Biotechnology Research
-
700 & Above Employee
-
Managing Director/Site Leader
-
Jan 2013 - Oct 2016
-Represent Thermo Fisher Scientific Hungary as Managing Director of the Hungarian manufacturing site -Responsible for plant production, cost saving, productivity improvement, quality and reliability goals. -Responsible for maintaining appropriate production capacities and flexibility and store levels -Responsible for the implementation of lean principles in the plant. -Participate in the development of the annual operating plan of the Hungarian plant -Deploy annual goals and objectives from the AOP for the management lead team members -Participate in the development process of annual capital plan for the plant. Make sure that the projects are finished on time and on budget -Mentor members of the management lead team -Communicate with the sales, finance, engineering, and customer service staff regarding new business -Ensure customer requirements are met, customer satisfaction and delivery performance are maintained at the highest possible level -Review forecasted customer demand and make staff level adjustments as required -Report key performance indicators to Vice President/General Manager of SSG (Slides and Specialty Glasses) and to Vice President/Director of Operations monthly Show less
-
-
-
Pridgeon and Clay Kft.
-
Apostag, Hungary
-
Plant manager
-
Nov 2011 - Jan 2013
-Direct and coordinate operations in the P&C stamping plant -Improves the operational systems, processes and policies -Responsible for plant production, cost saving, productivity improvement and reliability goals. -Responsible for maintaining appropriate production capacities and flexibility, store levels and delivery performance -Responsible for the product quality control for the plant. -Define and prioritize annual goals and objectives for the management -Participate in the creation and drive the execution of annual capital plan for the plant -Mentor members of the management team -Delegate contract work depending on best value, service, or availability of contractors/vendors, work with outside contractors to set internal standards and ensure they are met -Communicate with the sales, finance, APQP, engineering, and customer service staff regarding new business, relevant business unit finance data, new business unit launches, product engineering changes, and customer visits -Ensure new product launches meet safety, capacity, manpower, and efficiency goals -Review future customer demand and make manpower level adjustments on a monthly basis -Review equipment capacity on a monthly basis, create contingency plans for key equipment -Report key measurable activity to vice president of global operations and executive staff monthly Show less
-
-
-
BDW technologies Hungary Kft
-
Székesfehérvár, Hungary
-
General Manager
-
May 2010 - Nov 2011
- Same as Plant manager / ATS Köfém, with additional responsibilities for managing the sales activities on Automotive and Truck Body area - Same as Plant manager / ATS Köfém, with additional responsibilities for managing the sales activities on Automotive and Truck Body area
-
-
-
Alcoa
-
United States
-
Mining
-
700 & Above Employee
-
-
Dec 2008 - May 2010
-Direct and coordinate operations in the Automotive plant and Truck Body plant-Improve the operational systems, processes and policies-Oversee monthly and quarterly assessments and forecasts of organization's financial performance against budget, financial and operational goals. Oversee short and long-term financial and managerial reporting.-Responsible for plant production, cost saving, productivity improvement and reliability goals. -Responsible for maintaining appropriate production capacities and flexibility, store levels and delivery performance-Responsible for the product quality control for the plant. -Play significant role in long-term planning, including initiatives geared toward operational excellence (implementation of Alcoa Business System).-Direct annual budgeting and planning process for the organization's annual budget and capital expenditure plan-Drive initiatives in the management team and organizationally that contribute to long-term operational excellence.-Comply with all internal and external rules and regulations-Contribute to short and long-term organizational planning and strategy -Foster a well-trained and motivated staff-Select and train plant supervisory and administrative staff. -Conduct employee performance reviews Show less
-
-
-
Oct 2007 - Dec 2008
-Manage the manufacturing and production aspects of the machining (machining, Ultra Bright machining) and finishing (polishing, high luster polishing, brush finish, DuraBright, Clear Coat, paint) supply base in Cleveland-Barberton flow path for Truck and Auto wheels-Responsible for managing the production of product at the sources, movement of product among the sources, inventory planning and control, scrap & rework and timely launch of new products-Enforcing contract compliance with all the suppliers-Contract management and pricing-Maximizing production capacities and flexiblity, minimizing store levels-Minimize inventory inaccuracies-Drive cost saving and productivity improvement activities-Improve delivery performance Show less
-
-
-
Dec 2005 - Oct 2007
-Manage the manufacturing and production aspects of the machining (machining, Ultra Bright machining) and finishing (polishing, high luster polishing, brush finish, DuraBright, Clear Coat, paint) supply base in Cleveland-Barberton flow path for Truck wheels-Responsible for managing the production of product at the sources, movement of product among the sources, inventory planning and control, scrap & rework and timely launch of new products-Enforcing contract compliance with all the suppliers-Contract management and pricing-Maximizing production capacities and flexiblity, minimizing store levels-Minimize inventory inaccuracies-Drive cost saving and productivity improvement activities-Improve delivery performance-Implement direct shipment to Alcoa sub-assembly plants-Consolidate truck wheel flowpath-Motivating, training, developing production, ABS, finance and quality assurance personnel Show less
-
-
-
Jun 2003 - Dec 2005
-Managing warehousing, production scheduling, production, logistics, maintenance and ABS activities-Maximizing production capacities and flexiblity, minimizing store levels-Maintain/improve cost effectiveness and productivity-Maintain required delivery performance-Implement direct shipments to customers-Maintain/improve reliabilty of production equipments-Motivating, training, developing production, maintenance and logistics personnel
-
-
-
Mar 2002 - Jun 2003
-Managing and directing AWPE EHS department-Assuring the compliance with Alcoa and Hungarian standards and regulations-Operate the Environmental Management System according to ISO14001-Co-ordinate internal, external and Alcoa self audits-Assuring and certifying the quality of products-Managing and directing the AWPE quality assurance staff-Developing and implementing new and improved procedures-Assist manufacturing units in statistical process control-Co-ordinate customer audits, internal and external audits-Prepare self assessments according to EFQM Business Excellence Model Show less
-
-
-
Aug 2000 - Mar 2002
-Assuring and certifying the quality of products-Managing and directing the AWPE quality assurance staff-Developing and implementing new and improved procedures-Assist manufacturing units in statistical process control-Co-ordinate customer audits, internal and external audits-Prepare self assessments according to EFQM Business Excellence Model
-
-
-
-
-
Mar 1999 - Aug 2000
-
-
-
Mar 1998 - Mar 1999
-
-
-
AFL Hungary
-
Mór, Hungary
-
Manufacturing Quality Manager
-
Jun 1997 - Mar 1998
-
-
-
University of Miskolc, Faculty of Economics
-
Miskolc, Hungary
-
Assistant Lecturer
-
Jun 1995 - Jun 1997
-
-
Education
-
University of Miskolc
Environmental Manager, Environment management -
University of Miskolc
M.Sc. Engineer-Economist, Economics -
University of Miskolc
Mechanical Engineer (M. Sc.), Mechanical Engineering
Community
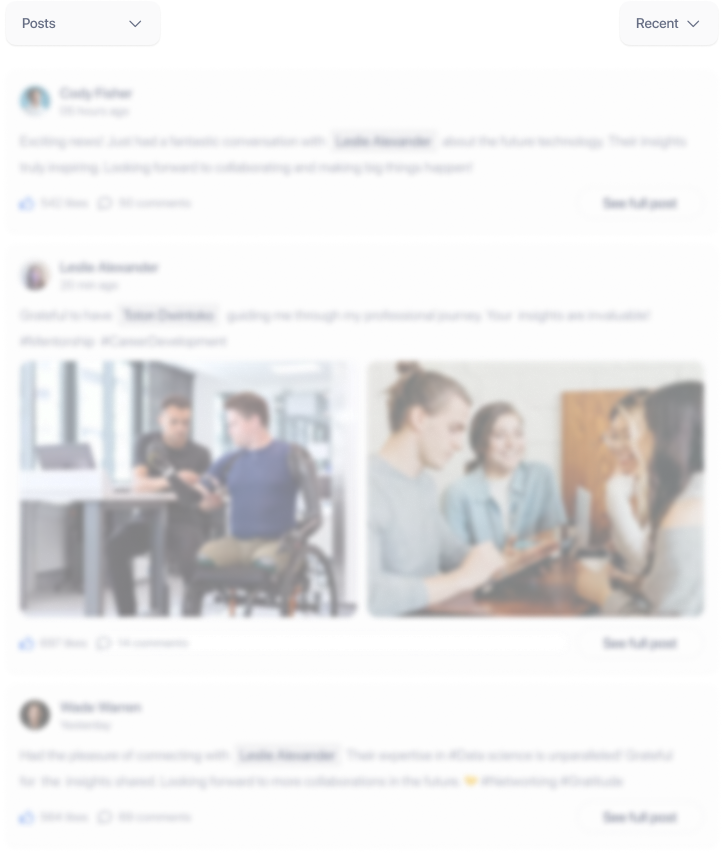