Mick Tucker
Transport Controller at Noble Foods Ltd- Claim this Profile
Click to upgrade to our gold package
for the full feature experience.
Topline Score
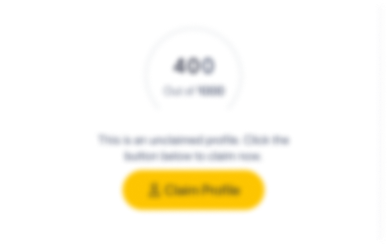
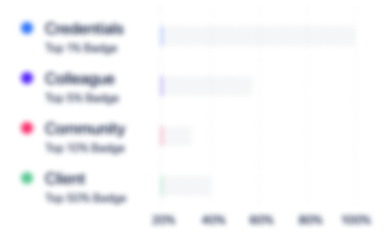
Bio


Experience
-
Noble Foods Ltd
-
Food Production
-
300 - 400 Employee
-
Transport Controller
-
Oct 2010 - Present
Control of the logistics operations at a fast paced high volume fresh FMCG company. Control of the logistics operations at a fast paced high volume fresh FMCG company.
-
-
-
-
Kids Manager
-
May 2009 - Jul 2009
Whilst I am looking for the next opportunity I've been promoted to look after my two kids. This is hard work!!! Whilst I am looking for the next opportunity I've been promoted to look after my two kids. This is hard work!!!
-
-
-
-
Group General Manager
-
Jan 2008 - Apr 2009
CPL are a £100 million turnover coal products manufacturer that also operates a Distribution Operation. Brought in to a new position to report into the Operations Director in a new role created to improve the operation. Instigated a key strategic review which ensured the company was able to cope with a 50% increase in demand due to the exceptionally cold winter. Initially given the responsibility to deliver a project that was six weeks behind a business critical time plan. Managed to deliver the project to my revised Gant chart which achieved business objectives and maintained customer base. Achieved this by a complete review of resources available and implemented a new plan which incorporated a 24 hour seven day working schedule to achieve the required production plan. Introduced a basic MRP system to allow the business to achieve the customer's requirement whilst controlling the lead times and stock levels of all SKU's. Introduced Performance appraisal and employee development programmes to define a people plan going forward to ensure the business could be developed to achieve customers expectations for tomorrow. Completed a formal review of the 34 depots within the organisation to develop a 5 year strategy to improve the ability of the business to achieve a 50% improvement in the key critical performance factors of deliver time, OTIF and cost per unit. Gained approval to a complete fleet renewal to facilitate the changes needed to take the business forward to achieve the strategic plan. Initially trialled the changes and implemented a new management approach to prove that the strategic plan could be achieved at a substantially reduced cost and much improved quality. Show less
-
-
-
Faccenda Foods Ltd
-
United Kingdom
-
Food and Beverage Manufacturing
-
100 - 200 Employee
-
Group General Manager
-
Oct 1999 - Jun 2008
-
-
-
-
Group General Manager
-
1999 - 2008
-
-
-
-
General Manager
-
Jan 1995 - Jan 1999
Quality and Technical Development Robinson Healthcare was a £30million manufacture and distributor of medical products. Reporting to the Managing Director, and as part of the Executive business team, my brief was to develop the manufacturing facilities to comply with the relevant regulatory authorities requirements - BSI, MDA, VMD. All mandatory and customer audits were passed at the first attempt. With overall control of all the Quality and Technical departments, a total of some 125 staff including 3 Engineers, 6 Maintenance Supervisors, 3Project Managers, 2 Quality Managers and 2 Continuous Improvement Managers. Control a £5 million investment programme in new equipment and a relocation budget of £10 million. Development of a suitable contract for the purpose of major capital items and negotiation of the required contract to ensure projects are delivered on time and to cost. Development of a skin contact hot melt adhesive suitable for small skin areas and the suitable equipment to utilise this adhesive. Capital value of £500,000. Introduction of modern manufacturing machinery to remove excessively manual operations. Total capital spend of £2.5 million. Redesign of fibre processing lines for the manufacture of Cotton Wool products including introduction of new processing equipment to my design. Capital value of £1.25 million. Strategic development of the business, including divestment programmes and bringing the organisation back to its core competencies. Design and introduction of cellular manufacturing. This involved selection of cell leaders and a substantial restructuring of the organisation into teams based in Cells. Development of a suitable team building programme to build these teams. Strategic Development of joint ventures in France and Holland and ensuring these are maximised in the market place. Show less
-
-
-
-
Production Manager
-
Jan 1993 - Jan 1995
Developed a relayout program from first concept, subsequent design and planning and then final installation over a nine-month period at a cost of £1.25 million. Covered Unit Engineering Managers duties for three months during this period. Successfully managed to transform a loss making factory into a substantial contributor to the Group's financial performance whilst taking the factory to new standards of hygiene and achieving the American Institute of Baker's Excellent category this being the first time this was achieved at Show less
-
-
-
-
Underground Manager
-
Jan 1981 - Jan 1993
as an underground employee and subsequently worked at every supervisory level finishing as the Underground Manager of Silverwood Colliery, Rotherham, and South Yorkshire.Totally responsible for the effective supervision and control of upto 1000 men involved in all aspects of underground work. as an underground employee and subsequently worked at every supervisory level finishing as the Underground Manager of Silverwood Colliery, Rotherham, and South Yorkshire.Totally responsible for the effective supervision and control of upto 1000 men involved in all aspects of underground work.
-
-
Education
-
Leeds Metropolitan University
B Eng ( Hons), Mining Engineering -
Leeds University
Degree of Bachelor of Engineering (Honours), Mining Engineering -
Sheffield Business Schools
Master, Business Administration
Community
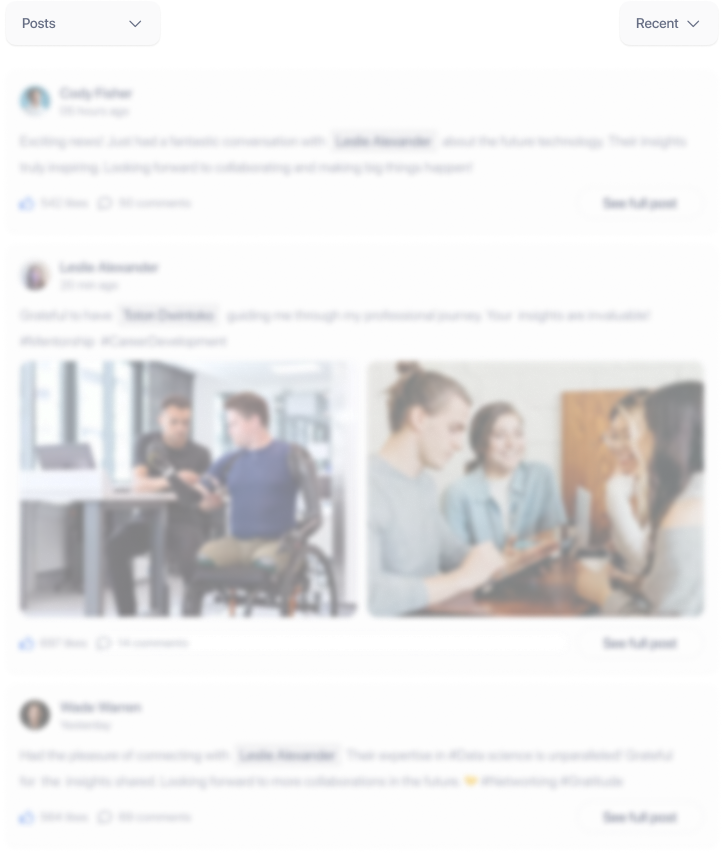